Les revêtements PVD (Physical Vapor Deposition) sont réputés pour leur dureté, leur durabilité et leur polyvalence exceptionnelles. Ces revêtements sont largement utilisés dans les industries nécessitant des matériaux hautes performances, telles que la microélectronique, l'optique et les dispositifs médicaux. La dureté d'un revêtement PVD dépend du matériau spécifique utilisé, certains revêtements atteignant des niveaux de dureté extrêmes en raison de leurs propriétés uniques et de leurs processus de dépôt. Parmi les revêtements PVD les plus durs figurent ceux à base de carbone de type diamant (DLC) et de nitrure de titane (TiN), connus pour leur résistance supérieure à l'usure, leur stabilité à haute température et leur excellente adhérence aux substrats. Cela les rend idéaux pour les applications nécessitant une durabilité et des performances extrêmes.
Points clés expliqués :
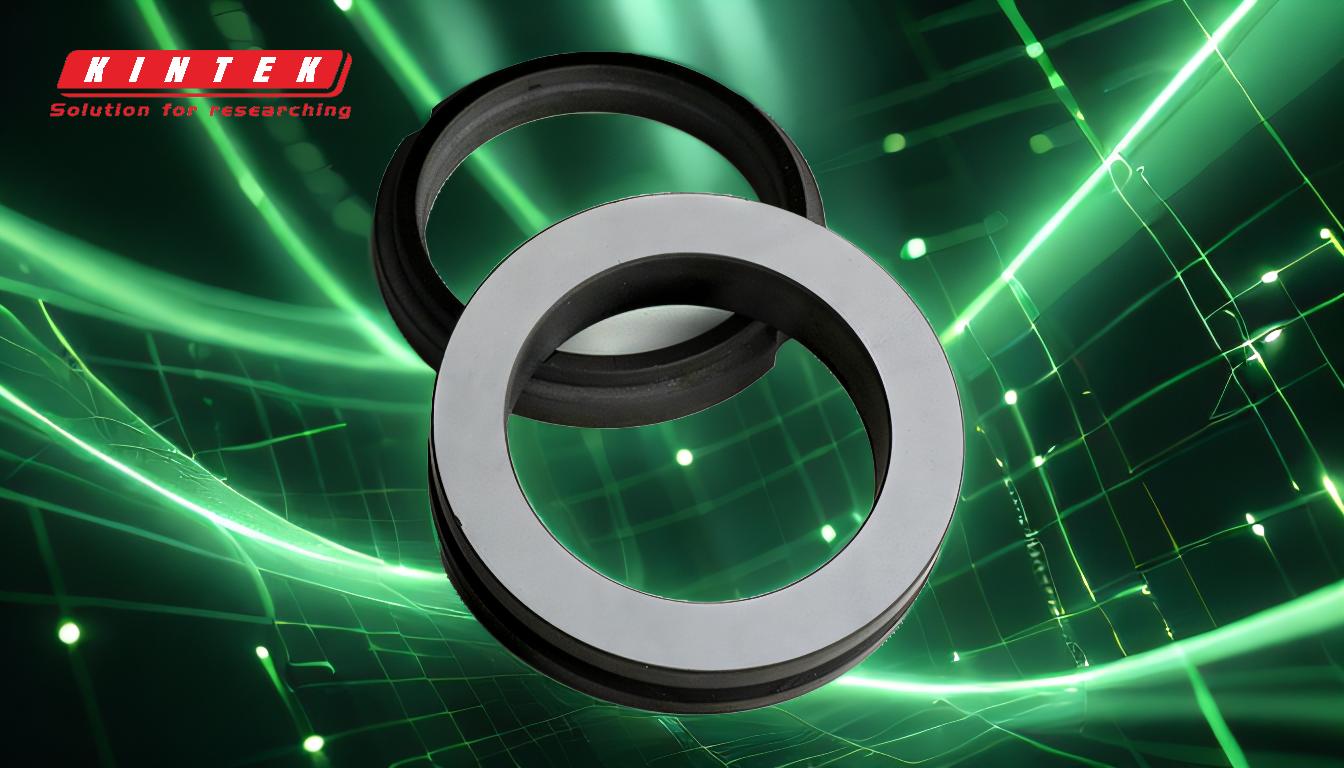
-
Qu'est-ce qui rend les revêtements PVD durs ?
- Les revêtements PVD sont créés grâce à un processus dans lequel un matériau solide est vaporisé sous vide puis déposé sur un substrat. Ce processus permet un contrôle précis des propriétés du revêtement, notamment de sa dureté.
- La dureté des revêtements PVD est influencée par le matériau utilisé, le processus de dépôt et la microstructure qui en résulte. Des matériaux comme le carbone de type diamant (DLC) et le nitrure de titane (TiN) sont particulièrement durs en raison de leurs liaisons atomiques fortes et de leurs structures denses.
-
Revêtements en carbone de type diamant (DLC)
- Les revêtements DLC font partie des revêtements PVD les plus durs disponibles. Ils sont constitués d'un mélange de liaisons carbone sp2 (de type graphite) et sp3 (de type diamant), qui leur confèrent une dureté et une résistance à l'usure exceptionnelles.
- Ces revêtements sont utilisés dans des applications nécessitant une durabilité extrême, telles que les outils de coupe, les composants automobiles et les dispositifs médicaux. Ils présentent également un faible frottement et une grande inertie chimique.
-
Revêtements en nitrure de titane (TiN)
- Les revêtements TiN sont un autre exemple de revêtements PVD extrêmement durs. Ils sont connus pour leur couleur dorée et sont largement utilisés dans les applications industrielles, notamment les outils de coupe et les composants de machines.
- Les revêtements TiN offrent une excellente dureté, résistance à l'usure et stabilité thermique, ce qui les rend adaptés aux environnements à fortes contraintes.
-
Autres revêtements PVD durs
- D'autres revêtements PVD durs comprennent le nitrure de titane et d'aluminium (TiAlN), le nitrure de chrome (CrN) et le nitrure de zirconium (ZrN). Ces revêtements offrent un équilibre entre dureté, résistance à la corrosion et stabilité thermique, ce qui les rend adaptés à des applications spécialisées.
- Le choix du revêtement dépend des exigences spécifiques de l'application, telles que l'environnement d'exploitation, le matériau du substrat et les performances souhaitées.
-
Avantages des revêtements PVD durs
- Durabilité: Les revêtements PVD durs sont très résistants à l'usure, à l'abrasion et aux chocs, prolongeant ainsi la durée de vie des composants revêtus.
- Stabilité à haute température : Ces revêtements peuvent résister à des températures extrêmes, ce qui les rend adaptés aux applications à haute température.
- Versatilité: Les revêtements PVD peuvent être appliqués sur une large gamme de substrats, notamment les métaux, les céramiques et les polymères.
- Précision et contrôle : Le processus PVD permet un contrôle précis de l'épaisseur, de la composition et des propriétés du revêtement, garantissant ainsi des performances optimales.
-
Applications des revêtements PVD durs
- Outils industriels : Les outils de coupe, les forets et les moules bénéficient de la dureté et de la résistance à l'usure des revêtements PVD.
- Aérospatiale et automobile : Les composants exposés à des contraintes et à des températures élevées, tels que les pièces de moteur et les aubes de turbine, sont souvent recouverts de matériaux PVD durs.
- Dispositifs médicaux : Les instruments chirurgicaux et les implants utilisent des revêtements PVD pour leur biocompatibilité et leur durabilité.
- Electronique et Optique : Les revêtements PVD sont utilisés dans les micropuces, les lentilles optiques et les panneaux solaires en raison de leur pureté et de leurs performances.
En résumé, les revêtements PVD les plus durs, tels que le DLC et le TiN, sont très appréciés pour leur dureté, leur durabilité et leur polyvalence exceptionnelles. Ces revêtements sont essentiels dans les industries nécessitant des matériaux capables de résister à des conditions extrêmes et d'offrir des performances durables. Le contrôle précis offert par le processus PVD garantit que ces revêtements répondent aux besoins spécifiques de diverses applications, ce qui en fait un élément essentiel de la fabrication et de la technologie modernes.
Tableau récapitulatif :
Type de revêtement | Propriétés clés | Applications |
---|---|---|
Carbone de type diamant (DLC) | Dureté extrême, faible frottement, haute inertie chimique | Outils de coupe, composants automobiles, dispositifs médicaux |
Nitrure de titane (TiN) | Excellente dureté, résistance à l'usure, stabilité thermique | Outils industriels, composants de machines |
Nitrure de titane et d'aluminium (TiAlN) | Dureté équilibrée, résistance à la corrosion, stabilité thermique | Applications industrielles spécialisées |
Nitrure de chrome (CrN) | Haute dureté, résistance à la corrosion | Industries aérospatiale, automobile et médicale |
Nitrure de Zirconium (ZrN) | Dureté supérieure, stabilité thermique | Electronique, optique et environnements très sollicités |
Trouvez le revêtement PVD parfait pour votre application— contactez nos experts dès aujourd'hui pour commencer !