Le dépôt physique en phase vapeur (PVD) est un procédé sophistiqué utilisé pour déposer de fines couches de matériaux sur un substrat.Il s'agit de créer une vapeur à partir d'un matériau solide, qui se condense ensuite sur le substrat pour former un film mince.Ce processus est réalisé dans un environnement sous vide afin de garantir la pureté et la précision.Le procédé PVD est largement utilisé dans diverses industries en raison de sa capacité à produire des revêtements durables et de haute qualité, dotés d'excellentes propriétés mécaniques, chimiques et optiques.
Explication des points clés :
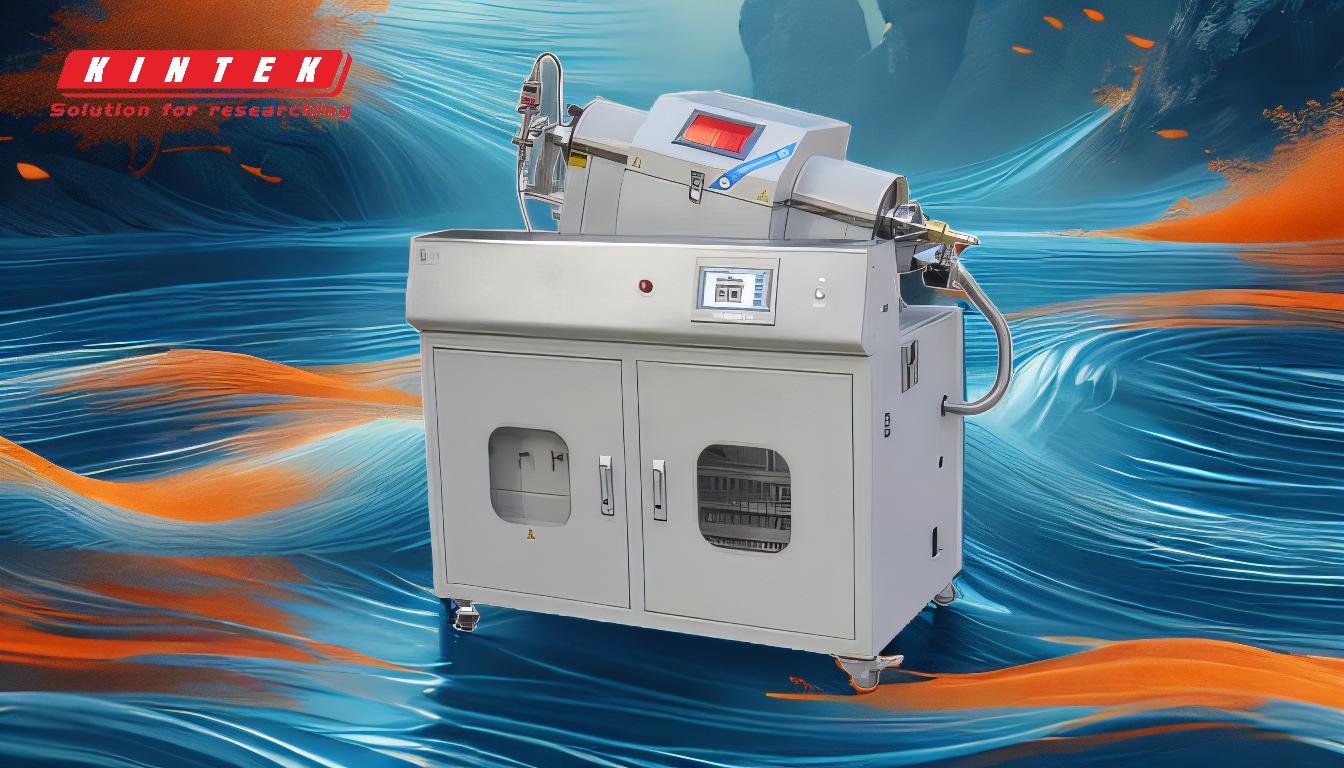
-
Nettoyage du support:
- Avant le début du processus PVD, le substrat doit être soigneusement nettoyé afin d'éliminer tout contaminant.Cette étape est cruciale car toute impureté sur la surface peut affecter l'adhérence et la qualité du revêtement.Les méthodes de nettoyage peuvent inclure le nettoyage par ultrasons, le nettoyage chimique ou le nettoyage au plasma.
-
Création d'un environnement sous vide:
- Le processus PVD se déroule dans une chambre à vide afin d'éliminer tout gaz atmosphérique susceptible d'interférer avec le dépôt.Un vide poussé est essentiel pour que le matériau vaporisé puisse se déplacer sans entrave jusqu'au substrat.
-
Vaporisation du matériau cible:
- Le matériau à déposer, appelé cible, est vaporisé à l'aide de diverses techniques telles que la pulvérisation cathodique, l'évaporation à l'arc ou l'évaporation par faisceau d'électrons.Dans le cas de la pulvérisation cathodique, des ions à haute énergie bombardent la cible, provoquant l'éjection d'atomes de sa surface.Dans l'évaporation à l'arc, un arc électrique est utilisé pour vaporiser le matériau cible.
-
Formation du plasma:
- Un plasma est créé en ionisant un gaz, généralement de l'argon ou de l'azote, dans la chambre à vide.Le plasma est constitué d'ions et d'électrons très énergétiques qui peuvent interagir avec le matériau cible vaporisé.Cette étape est cruciale pour l'ionisation et l'activation des atomes vaporisés.
-
Réaction avec des gaz réactifs:
- Des gaz réactifs tels que l'azote ou l'oxygène sont introduits dans la chambre.Ces gaz réagissent avec le matériau cible vaporisé pour former des composés.Par exemple, si le matériau cible est le titane et que le gaz réactif est l'azote, le composé résultant sera le nitrure de titane (TiN), connu pour sa dureté et sa résistance à l'usure.
-
Dépôt sur le substrat:
- Le matériau vaporisé et ionisé, maintenant sous la forme d'un composé, est déposé sur le substrat.Le dépôt s'effectue atome par atome, ce qui permet d'obtenir une couche fine et uniforme.Le substrat est généralement maintenu à une température contrôlée pour garantir une bonne adhérence et une bonne qualité du film.
-
Essais et contrôle de la qualité:
- Après le processus de dépôt, les composants revêtus sont testés pour garantir leur cohérence et leur qualité.Des techniques telles que la fluorescence X (XRF) et la spectrophotométrie sont utilisées pour mesurer la composition, l'épaisseur et la couleur du revêtement.Cette étape est essentielle pour vérifier que le revêtement répond aux spécifications requises.
-
Avantages du revêtement PVD:
- Les revêtements PVD offrent plusieurs avantages, notamment une grande dureté, une excellente résistance à l'usure et une bonne adhérence au substrat.Ils présentent également une excellente stabilité chimique et thermique, ce qui les rend adaptés à un large éventail d'applications.En outre, le PVD est un procédé respectueux de l'environnement, car il ne produit pas de sous-produits nocifs.
-
Applications du revêtement PVD:
- Les revêtements PVD sont utilisés dans diverses industries, notamment l'automobile, l'aérospatiale, la médecine et l'électronique.Les applications courantes comprennent le revêtement d'outils de coupe, de moules et de composants qui nécessitent une résistance à l'usure et une durabilité élevées.Les revêtements PVD sont également utilisés dans des applications décoratives en raison de leur capacité à produire une large gamme de couleurs et de finitions.
En résumé, le procédé de revêtement PVD est une méthode très contrôlée et précise de dépôt de films minces sur des substrats.Il comporte plusieurs étapes critiques, depuis le nettoyage du substrat jusqu'à l'essai du revêtement final, garantissant que le produit obtenu répond aux normes de qualité et de performance les plus élevées.La polyvalence et les avantages environnementaux du procédé PVD en font un choix privilégié pour de nombreuses applications industrielles.
Tableau récapitulatif :
Étape | Description de l'étape |
---|---|
1.Nettoyage du support | Éliminer les contaminants à l'aide d'un nettoyage par ultrasons, chimique ou au plasma. |
2.Création d'un vide | Créer un environnement de vide poussé pour garantir la pureté et la précision. |
3.Vaporisation | Vaporiser le matériau cible par pulvérisation cathodique, évaporation à l'arc ou faisceau d'électrons. |
4.Formation du plasma | Ioniser le gaz (par exemple, l'argon ou l'azote) afin de créer un plasma pour l'activation. |
5.Réaction avec des gaz | Introduire des gaz réactifs pour former des composés tels que le nitrure de titane (TiN). |
6.Dépôt | Déposer le matériau vaporisé sur le substrat, atome par atome. |
7.Essais et qualité | Utiliser le XRF et la spectrophotométrie pour vérifier l'épaisseur et la qualité du revêtement. |
8.Avantages | Dureté élevée, résistance à l'usure, stabilité chimique et respect de l'environnement. |
9.Applications | Utilisé dans les secteurs de l'automobile, de l'aérospatiale, de la médecine et de l'électronique. |
Découvrez comment la métallisation PVD peut améliorer vos produits. contactez nos experts dès aujourd'hui pour une consultation !