Le dépôt physique en phase vapeur (PVD) est un procédé de revêtement en couche mince polyvalent et largement utilisé qui implique le transfert physique d'un matériau d'une source à un substrat dans un environnement sous vide. L'objectif principal du PVD est de déposer des revêtements fins, uniformes et de haute qualité sur des surfaces afin d'améliorer leurs propriétés, telles que la résistance à l'usure, la résistance à la corrosion, la conductivité électrique, les performances optiques et l'attrait esthétique. Ce processus est essentiel dans des secteurs tels que l’électronique, l’aérospatiale, l’automobile et les dispositifs médicaux, où des revêtements précis et durables sont nécessaires. Les techniques PVD, telles que la pulvérisation cathodique et l'évaporation, permettent le dépôt d'une large gamme de matériaux, notamment les métaux, les céramiques et les composites, avec une excellente adhérence et un excellent contrôle de l'épaisseur et de la composition du film.
Points clés expliqués :
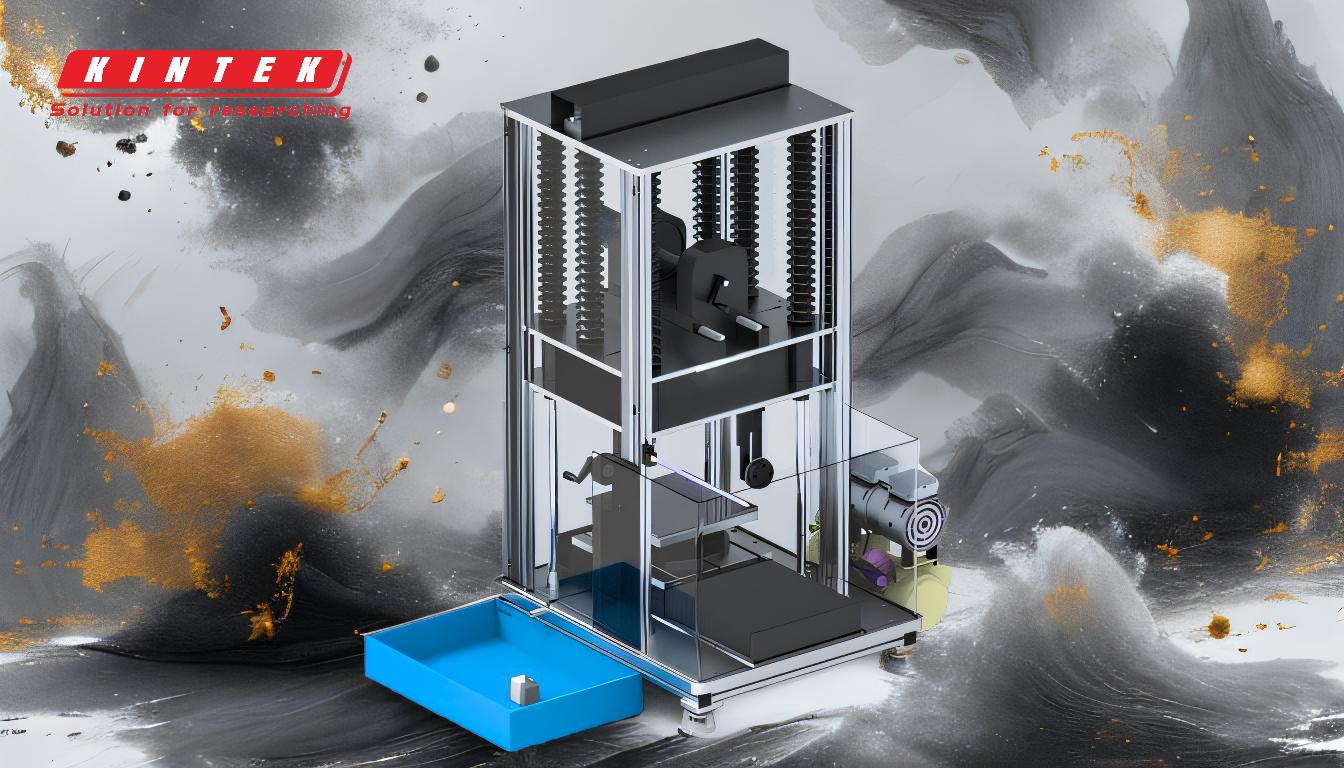
-
Dépôt de couches minces:
- Le PVD est principalement utilisé pour déposer des films minces, allant généralement de quelques nanomètres à plusieurs micromètres d'épaisseur. Ces films sont appliqués pour améliorer les propriétés de surface des substrats, par exemple en améliorant la dureté, en réduisant la friction ou en fournissant des finitions décoratives.
- Le processus garantit un revêtement uniforme et précis, ce qui est essentiel pour les applications nécessitant des performances et une fiabilité élevées.
-
Propriétés de surface améliorées:
- Résistance à l'usure: Les revêtements PVD, tels que le nitrure de titane (TiN) ou le carbone de type diamant (DLC), améliorent considérablement la résistance à l'usure des outils, moules et composants, prolongeant ainsi leur durée de vie.
- Résistance à la corrosion: Les revêtements comme le nitrure de chrome (CrN) ou l'oxyde d'aluminium (Al2O3) protègent les surfaces de la dégradation environnementale, les rendant adaptées aux conditions difficiles.
- Conductivité électrique: Le PVD est utilisé pour déposer des matériaux conducteurs comme l'or, l'argent ou le cuivre dans l'électronique pour les interconnexions, les contacts et les circuits.
- Performances optiques: Les revêtements PVD sont appliqués sur les lentilles, les miroirs et les écrans pour améliorer les propriétés de réflectivité, d'antireflet ou de filtrage.
-
Polyvalence dans la sélection des matériaux:
- Le PVD peut déposer une large gamme de matériaux, notamment des métaux (par exemple, l'aluminium, le titane), des céramiques (par exemple, des oxydes, des nitrures) et des composites. Cette polyvalence le rend adapté à diverses applications dans tous les secteurs.
- Le procédé permet la création de revêtements multicouches ou alliés aux propriétés personnalisées en combinant différents matériaux.
-
Revêtements de haute qualité et durables:
- Les revêtements PVD présentent une excellente adhérence aux substrats, garantissant des performances durables même dans des conditions extrêmes.
- L'environnement sous vide minimise la contamination, ce qui donne lieu à des revêtements de haute pureté et de qualité constante.
-
Applications dans tous les secteurs:
- Électronique: Le PVD est utilisé pour déposer des films minces pour les semi-conducteurs, les cellules solaires et les écrans.
- Aérospatial: Des revêtements sont appliqués sur les aubes de turbine et d'autres composants pour résister aux températures élevées et à l'usure.
- Automobile: Le PVD améliore la durabilité et l'apparence des pièces de moteur, des garnitures décoratives et des outils de coupe.
- Dispositifs médicaux: Des revêtements biocompatibles sont déposés sur les implants et les instruments chirurgicaux pour améliorer les performances et la sécurité.
-
Avantages environnementaux et économiques:
- Le PVD est un processus propre et respectueux de l’environnement, car il n’implique pas de produits chimiques dangereux ni ne produit de sous-produits nocifs.
- La durabilité des revêtements PVD réduit le besoin de remplacements fréquents, ce qui entraîne des économies et une réduction des déchets de matériaux.
-
Techniques de traitement:
- Pulvérisation: Méthode PVD courante dans laquelle des ions à haute énergie bombardent un matériau cible, éjectant des atomes qui se déposent sur le substrat.
- Évaporation: Consiste à chauffer un matériau sous vide jusqu'à ce qu'il se vaporise et se condense sur le substrat.
- Les deux techniques permettent un contrôle précis de l’épaisseur, de la composition et de la microstructure du revêtement.
En résumé, le dépôt physique en phase vapeur constitue une technologie essentielle pour créer des revêtements hautes performances qui améliorent la fonctionnalité, la durabilité et l’apparence des matériaux dans diverses industries. Sa capacité à déposer une large gamme de matériaux avec une précision et une qualité exceptionnelles le rend indispensable dans la fabrication et l'ingénierie modernes.
Tableau récapitulatif :
Aspect clé | Détails |
---|---|
But | Dépose des revêtements fins et uniformes pour améliorer les propriétés de surface. |
Avantages clés | Résistance à l'usure, résistance à la corrosion, conductivité électrique, performances optiques. |
Matériaux utilisés | Métaux (par exemple aluminium, titane), céramiques (par exemple oxydes, nitrures), composites. |
Applications | Electronique, aérospatiale, automobile, dispositifs médicaux. |
Techniques | Pulvérisation, évaporation. |
Avantages environnementaux | Processus propre, sans produits chimiques dangereux, réduit les déchets de matériaux. |
Découvrez comment le PVD peut transformer vos matériaux : contactez nos experts dès aujourd'hui !