Le revêtement PVD (Physical Vapor Deposition) est une technologie moderne de dépôt en phase vapeur utilisée pour appliquer des revêtements extrêmement fins et performants sur des matériaux.Ces revêtements se caractérisent par leur grande pureté, leur uniformité et leur excellente adhérence au substrat.Les revêtements PVD ont généralement une épaisseur de 0,5 à 5 μm et offrent des améliorations significatives en termes de dureté de surface, de stabilité chimique, de résistance à l'usure et d'ajustabilité de l'apparence du produit.Le procédé consiste à convertir un matériau solide en sa phase vapeur sous vide, qui se condense ensuite pour revêtir la pièce.Les facteurs clés influençant la qualité du revêtement PVD sont le transfert en ligne droite, le prétraitement de la surface, la propreté et l'absence d'air piégé dans les trous hermétiquement fermés.Les revêtements PVD sont connus pour leur durabilité, leur résistance à la corrosion et leur capacité à éliminer le besoin de couches de finition protectrices supplémentaires.
Explication des points clés :
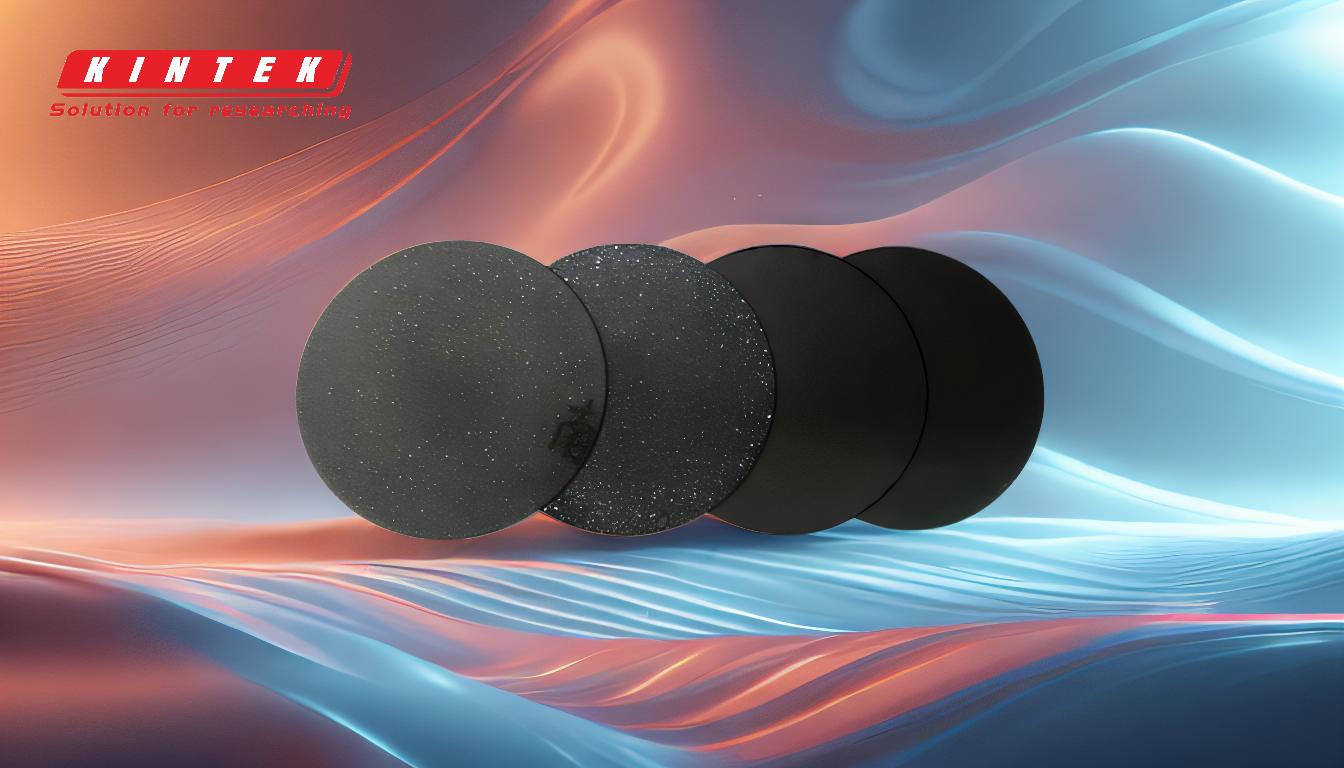
-
Épaisseur et uniformité du revêtement:
- Les revêtements PVD sont extrêmement fins, allant généralement de 0,5 à 5 μm.Cette finesse permet un contrôle précis des propriétés du revêtement tout en conservant les dimensions d'origine du substrat.
- L'uniformité du revêtement est cruciale pour garantir des performances constantes sur toute la surface de la pièce.Une grande uniformité est obtenue grâce à des processus de dépôt contrôlés dans un environnement sous vide.
-
Adhésion et durabilité:
- Les revêtements PVD présentent une excellente adhérence au substrat, ce qui est essentiel pour leur durabilité et leurs performances.Cette forte adhérence garantit que le revêtement reste intact en cas de contraintes mécaniques, de températures élevées et d'environnements corrosifs.
- La durabilité des revêtements PVD élimine souvent le besoin de couches de finition protectrices supplémentaires, ce qui en fait une solution rentable pour de nombreuses applications.
-
Dureté de la surface et résistance à l'usure:
- Les revêtements PVD sont connus pour leur grande dureté de surface, qui améliore considérablement la résistance à l'usure du matériau revêtu.Ils sont donc idéaux pour les applications où le matériau est soumis à des forces abrasives ou à un frottement élevé.
- L'amélioration de la résistance à l'usure prolonge la durée de vie des outils et des composants, réduisant ainsi les coûts de maintenance et les temps d'arrêt.
-
Stabilité chimique et résistance à la corrosion:
- Les revêtements PVD offrent une excellente stabilité chimique, ce qui les rend résistants à la corrosion et à la dégradation dans les environnements difficiles.Ceci est particulièrement important pour les applications dans des industries telles que l'aérospatiale, l'automobile et les appareils médicaux.
- La résistance à la corrosion des revêtements PVD garantit que les matériaux revêtus conservent leur intégrité et leurs performances dans le temps, même lorsqu'ils sont exposés à des substances corrosives.
-
Transfert en ligne de mire et prétraitement de la surface:
- Le revêtement PVD est un procédé à visibilité directe, ce qui signifie que seules les surfaces directement exposées au matériau vaporisé seront revêtues.Cette limitation nécessite une attention particulière à la géométrie de la pièce et à la nécessité d'un prétraitement de la surface.
- Le prétraitement de la surface est essentiel pour garantir une bonne adhérence et l'uniformité du revêtement.Il peut s'agir d'un nettoyage, d'un polissage ou d'autres techniques de préparation de la surface afin d'éliminer les contaminants et de créer une surface optimale pour le revêtement.
-
Propreté de la surface et air piégé:
- La propreté de la surface est essentielle pour le revêtement PVD, car même de petites particules ou des contaminants peuvent nuire à la qualité et à l'adhérence du revêtement.Des processus de nettoyage minutieux sont nécessaires pour obtenir les résultats souhaités.
- L'air emprisonné dans des trous ou des cavités hermétiquement fermés peut interférer avec le processus de revêtement, entraînant une couverture inégale ou incomplète.Ces caractéristiques doivent être évitées lors de la conception afin de garantir une qualité de revêtement constante.
-
Considérations relatives à la température et à l'environnement:
- Les revêtements PVD sont appliqués à des températures relativement basses par rapport à d'autres méthodes de revêtement, ce qui réduit le risque de distorsion thermique ou d'endommagement du substrat.Le dépôt en phase vapeur convient donc au revêtement de matériaux sensibles à la température.
- L'environnement sous vide utilisé pour le revêtement PVD minimise la contamination et garantit un revêtement d'une grande pureté, ce qui améliore encore les performances et la longévité du matériau.
-
Propriétés esthétiques et fonctionnelles:
- Les revêtements PVD peuvent être adaptés pour obtenir divers effets esthétiques, y compris un éclat métallique et des variations de couleur.Ces revêtements ne nécessitent pas de polissage supplémentaire pour obtenir une finition de haute qualité.
- La possibilité d'ajuster l'aspect du revêtement permet de le personnaliser pour répondre à des exigences de conception spécifiques, améliorant ainsi l'attrait fonctionnel et visuel du matériau revêtu.
En résumé, les normes de revêtement PVD mettent l'accent sur des revêtements minces, uniformes et durables présentant une excellente adhérence, une grande dureté et une bonne résistance à la corrosion.Le processus exige une attention particulière à la préparation de la surface, à la propreté et aux considérations de conception afin d'obtenir des résultats optimaux.Les revêtements PVD offrent une solution polyvalente et rentable pour améliorer les performances et l'aspect des matériaux dans diverses industries.
Tableau récapitulatif :
Caractéristique principale | Description |
---|---|
Épaisseur du revêtement | De 0,5 à 5 μm, garantissant une précision et un impact minimal sur les dimensions du substrat. |
Adhésion et durabilité | Excellente force d'adhérence, éliminant le besoin de couches de finition protectrices supplémentaires. |
Dureté de la surface | Améliore considérablement la résistance à l'usure, idéal pour les applications à frottement élevé. |
Résistance à la corrosion | La stabilité chimique élevée protège contre les environnements difficiles. |
Transfert en visibilité directe | Nécessite un prétraitement soigneux de la surface et des considérations de conception. |
Propriétés esthétiques | Éclat métallique personnalisable et variations de couleurs pour un attrait fonctionnel et visuel. |
Améliorez vos matériaux avec le revêtement PVD. contactez-nous dès aujourd'hui pour des solutions expertes !