L'épaisseur des couches minces produites par dépôt physique en phase vapeur (PVD) varie généralement de 0,00004 à 0,0002 pouces (environ 1 à 5 micromètres). Cette épaisseur est influencée par divers facteurs, notamment la méthode de dépôt (par exemple, la pulvérisation cathodique ou l'évaporation), les paramètres du processus tels que la durée du cycle, la puissance appliquée et les propriétés du matériau. Le dépôt en phase vapeur (PVD) est une technique polyvalente de dépôt sous vide utilisée pour créer des couches minces sur des substrats tels que les métaux, les céramiques, le verre et les polymères. Le processus consiste à faire passer les matériaux d'une phase condensée à une phase vapeur, puis de nouveau à une phase condensée de film mince. Pour obtenir l'épaisseur et la qualité souhaitées, il faut contrôler avec précision des facteurs tels que la température de dépôt, la préparation du substrat et les conditions de vide.
Explication des points clés :
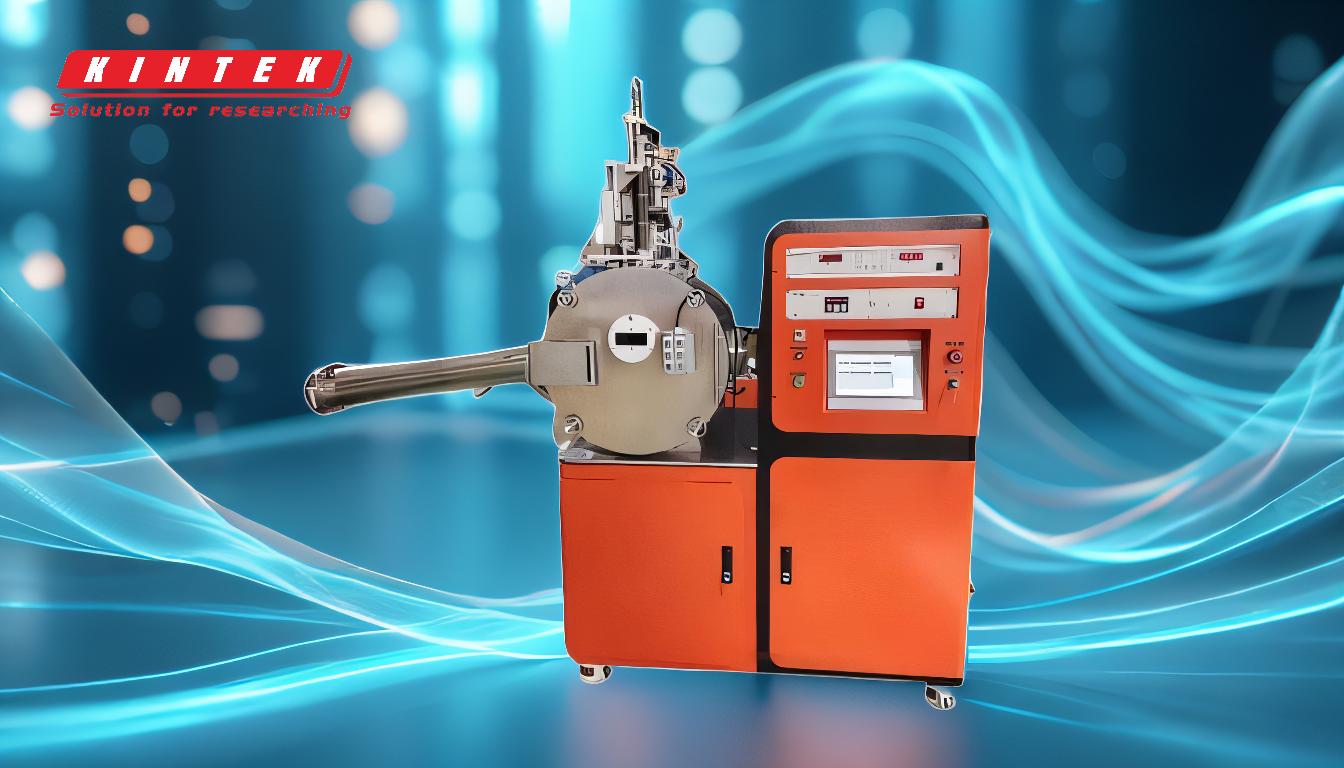
-
Gamme d'épaisseurs typiques des revêtements PVD:
- L'épaisseur des revêtements PVD varie généralement de 0.00004 à 0.0002 pouces (environ 1 à 5 micromètres ).
- Cette gamme convient aux applications nécessitant tolérances serrées et une accumulation minimale de matériaux.
- La faible épaisseur des revêtements PVD garantit que les finition de la surface du substrat est reproduit avec précision.
-
Facteurs influençant l'épaisseur:
- Méthode de dépôt: Les deux méthodes de dépôt en phase vapeur les plus courantes, pulvérisation et évaporation peuvent produire des épaisseurs différentes en fonction de leurs paramètres de traitement spécifiques.
- Durée du cycle: Des cycles de pulvérisation ou d'évaporation plus longs permettent d'obtenir des revêtements plus épais.
- Puissance appliquée: Des niveaux de puissance plus élevés pendant la pulvérisation augmentent l'énergie des particules de revêtement, ce qui permet un dépôt plus rapide et des films potentiellement plus épais.
- Propriétés des matériaux: La masse et le niveau d'énergie des particules du revêtement (allant de dizaines à des milliers d'électronvolts) affectent la vitesse de dépôt et l'épaisseur finale.
- Préparation du substrat: Un nettoyage et un traitement de surface adéquats du substrat garantissent un dépôt uniforme et une épaisseur constante.
-
Paramètres du processus et leur impact:
- Température: Les procédés de dépôt en phase vapeur (PVD) fonctionnent généralement dans une plage de température de 320 à 900 degrés Fahrenheit . Des températures plus élevées peuvent améliorer l'adhérence et l'uniformité, mais peuvent également affecter l'épaisseur finale.
- Conditions de vide: La composition du gaz résiduel et la pression dans la chambre à vide influencent la vitesse de dépôt et la qualité du film.
- Ligne de mire: PVD est un ligne de mire le procédé de vernissage est un procédé de type "à la volée", c'est-à-dire que le matériau de revêtement se déplace en ligne droite de la source au substrat. Cette caractéristique nécessite un positionnement minutieux du substrat afin d'obtenir une épaisseur uniforme.
-
Avantages du dépôt en phase vapeur par procédé physique (PVD) pour le dépôt de couches minces:
- Respect de l'environnement: Les procédés PVD n'impliquent pas de produits chimiques nocifs, ce qui en fait un choix durable pour la production de couches minces.
- Haute pureté: L'environnement sous vide garantit que les revêtements sont exempts de contaminants, ce qui permet d'obtenir des films minces d'une grande pureté.
- Amélioration de la qualité de la surface: Les revêtements PVD améliorent les propriétés de surface des substrats, notamment la dureté, la résistance à l'usure et la résistance à la corrosion.
-
Applications des films minces PVD:
- Revêtements industriels: Le procédé PVD est largement utilisé pour revêtir les outils, les moules et les composants afin d'en améliorer la durabilité et les performances.
- Finitions décoratives: La capacité de reproduire les finitions de surface fait du PVD un procédé idéal pour les applications décoratives sur les bijoux, les montres et les éléments architecturaux.
- Électronique: Les couches minces produites par PVD sont utilisées dans les semi-conducteurs, les cellules solaires et les dispositifs optiques en raison de leur contrôle précis de l'épaisseur et de leur haute qualité.
-
Comparaison avec d'autres techniques de dépôt:
- PVD offre un meilleur contrôle de l'épaisseur par rapport à d'autres méthodes de dépôt, comme le dépôt chimique en phase vapeur (CVD), qui peuvent donner des revêtements plus épais et moins uniformes.
- Contrairement à la MCV, la PVD ne nécessite pas traitement thermique après le dépôt, ce qui simplifie le processus et réduit le temps de production.
En comprenant ces points clés, un acheteur ou un ingénieur peut prendre des décisions éclairées quant à l'utilisation du dépôt en phase vapeur pour des applications spécifiques, en garantissant des performances optimales et un bon rapport coût-efficacité.
Tableau récapitulatif :
Aspect | Détails |
---|---|
Gamme d'épaisseur | 0.00004 à 0,0002 pouces (1 à 5 micromètres) |
Méthodes de dépôt | Pulvérisation, évaporation |
Principaux facteurs d'influence | Durée du cycle, puissance appliquée, propriétés des matériaux, préparation du substrat |
Plage de température | 320 à 900 degrés Fahrenheit |
Applications | Revêtements industriels, finitions décoratives, électronique |
Avantages | Respectueux de l'environnement, grande pureté, meilleure qualité de surface |
Réaliser des revêtements en couches minces avec précision grâce à la technologie PVD- contactez nos experts dès aujourd'hui pour des solutions sur mesure !