Les revêtements PVD (Physical Vapor Deposition) sont appliqués à une large gamme de métaux, d'alliages et de substrats, en fonction des propriétés et des applications souhaitées.Les métaux couramment soumis à un revêtement PVD sont l'acier inoxydable, le titane, le zirconium, l'aluminium et le cuivre, ainsi que des alliages spécialisés tels que les aciers à outils et les alliages de titane.Ces revêtements sont utilisés pour améliorer des propriétés telles que la dureté, la résistance à l'usure, la stabilité chimique et l'aspect esthétique.Les revêtements PVD sont généralement appliqués sur des matériaux qui peuvent résister à des températures élevées (jusqu'à 800°F) et qui sont compatibles avec les procédés de dépôt sous vide.Cette technique est polyvalente et peut être utilisée sur les métaux, les céramiques et même certains polymères, ce qui la rend adaptée à des secteurs allant de l'aérospatiale et de l'automobile au médical et à l'électronique.
Explication des points clés :
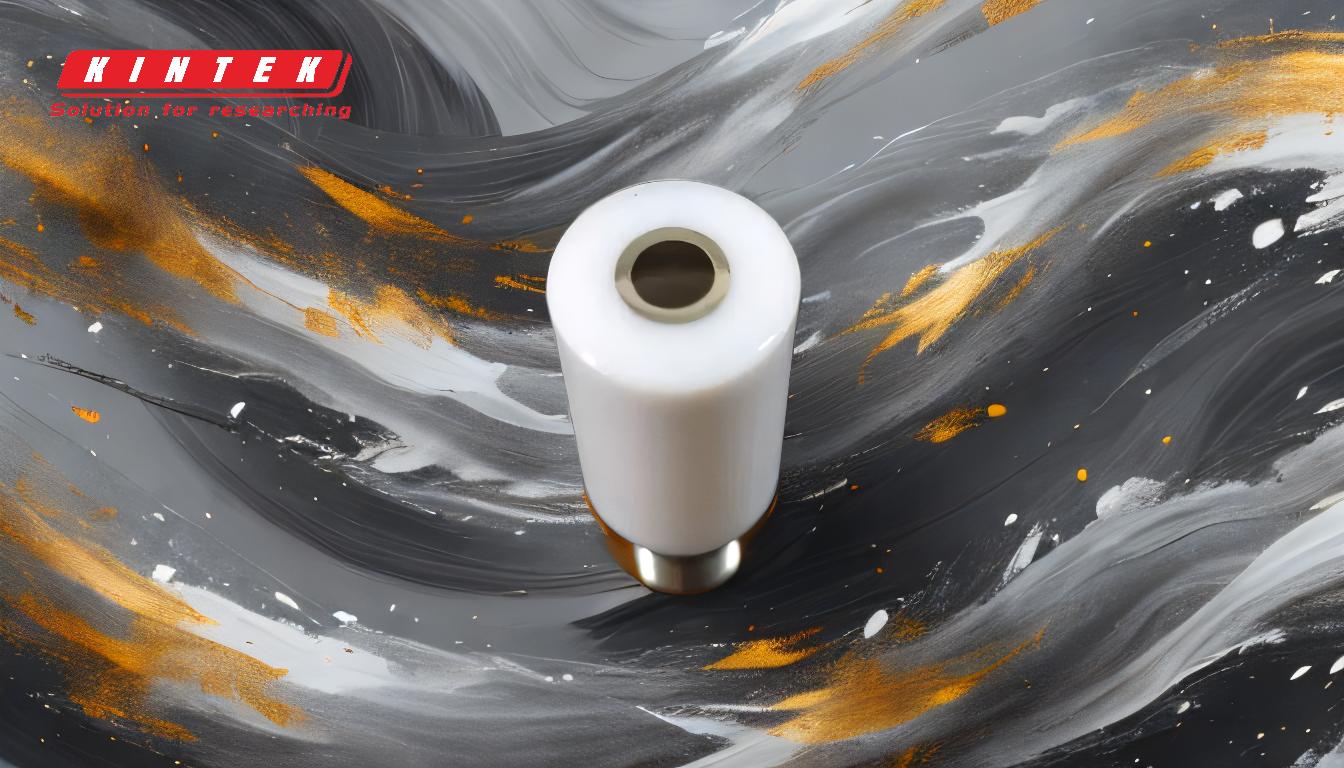
-
Métaux courants pour le revêtement PVD:
- Acier inoxydable:Les nuances les plus couramment utilisées sont les aciers inoxydables 303, 440C et 17-4.Ils sont souvent choisis pour leur durabilité et leur résistance à la corrosion, ce qui les rend idéaux pour les applications médicales et industrielles.
- Titane et alliages de titane:Le titane est léger, solide et biocompatible, ce qui en fait un choix populaire pour l'aérospatiale, les implants médicaux et les applications de haute performance.
- L'aluminium:Bien que moins courant en raison de son faible point de fusion, l'aluminium peut encore être revêtu par PVD pour des applications spécifiques où la réduction du poids est essentielle.
- Le cuivre:Utilisé dans l'électronique et l'aérospatiale pour son excellente conductivité électrique et ses propriétés thermiques.
- Zirconium:Souvent utilisé dans les revêtements spécialisés pour sa haute résistance à la corrosion et sa biocompatibilité.
-
Compatibilité avec les substrats:
- Les revêtements PVD peuvent être appliqués sur une variété de substrats, y compris les métaux, les céramiques et certains polymères.Le substrat doit pouvoir résister aux températures élevées (généralement jusqu'à 800°F) et aux conditions de vide du procédé PVD.
-
Revêtements spécialisés:
- Carbures, nitrures et borures:Ces revêtements sont utilisés pour répondre à des exigences de performance spécifiques, telles qu'une dureté accrue, une résistance à l'usure ou une stabilité thermique.Le nitrure de titane (TiN) et le nitrure de zirconium (ZrN), couramment utilisés dans les outils de coupe et les composants automobiles, en sont des exemples.
- Or et autres métaux précieux:L'or est fréquemment demandé pour l'électronique aérospatiale en raison de son excellente conductivité et de sa résistance à la corrosion.
-
Conditions du procédé:
- Le revêtement PVD est réalisé dans une chambre à vide à des températures comprises entre 50 et 600 degrés Celsius.Le processus consiste à vaporiser le matériau de revêtement (cible) et à le déposer sur le substrat (pièce) dans un environnement contrôlé.Des gaz réactifs tels que l'azote, l'acétylène ou l'oxygène peuvent être introduits pour créer des revêtements composés aux propriétés adaptées.
-
Applications des revêtements PVD:
- Aérospatiale:Utilisé pour les composants nécessitant une grande solidité, une résistance à l'usure et une stabilité thermique.
- Médical:Appliqué aux implants et aux instruments chirurgicaux pour leur biocompatibilité et leur résistance à la corrosion.
- Automobile:Améliore la durabilité et les performances des pièces de moteur, des outils de coupe et des éléments décoratifs.
- L'électronique:Il s'agit de revêtements conducteurs et protecteurs pour des composants tels que les connecteurs et les cartes de circuits imprimés.
-
Avantages des revêtements PVD:
- Mince et durable:Les revêtements PVD sont extrêmement fins (0,5 - 5 μm) mais offrent des améliorations significatives en termes de dureté de surface, de résistance à l'usure et de stabilité chimique.
- Polyvalence esthétique:Le procédé permet une large gamme de couleurs et de finitions, ce qui le rend adapté aux applications décoratives.
- Forte adhérence:Les revêtements forment une liaison solide avec le substrat, ce qui garantit des performances durables.
En connaissant les métaux et les substrats adaptés au revêtement PVD, ainsi que les conditions du procédé et les applications, les acheteurs peuvent prendre des décisions éclairées lorsqu'ils sélectionnent des matériaux et des revêtements pour leurs besoins spécifiques.
Tableau récapitulatif :
Catégorie | Détails |
---|---|
Métaux courants | Acier inoxydable, titane, zirconium, aluminium, cuivre, aciers à outils, alliages de titane |
Compatibilité des substrats | Métaux, céramiques et certains polymères qui résistent à des températures élevées et au vide |
Revêtements spécialisés | Carbures, nitrures, borures, or et autres métaux précieux |
Conditions du procédé | Chambre à vide, 50-600°C, gaz réactifs (azote, acétylène, oxygène) |
Applications | Aérospatiale, médecine, automobile, électronique |
Avantages | Finesse, durabilité, résistance à l'usure, stabilité chimique, polyvalence esthétique |
Prêt à améliorer vos matériaux avec des revêtements PVD ? Contactez nos experts dès aujourd'hui pour des solutions sur mesure !