Introduction à la technologie CVD
Définition et importance
Le dépôt chimique en phase vapeur (CVD) est une technologie essentielle de dépôt de couches minces, qui joue un rôle crucial dans la fabrication des semi-conducteurs et dans une myriade d'autres industries. Cette technologie permet le dépôt précis et contrôlé de couches minces sur divers substrats, ce qui est essentiel pour la fabrication de composants électroniques, de revêtements optiques et de couches protectrices.
Dans la fabrication des semi-conducteurs, le dépôt en phase vapeur est indispensable pour créer des films uniformes de haute qualité qui améliorent les performances et la fiabilité des circuits intégrés. La capacité de déposer des matériaux aux propriétés spécifiques, telles que la conductivité, l'isolation et la transparence optique, fait du dépôt en phase vapeur un outil essentiel dans la production de dispositifs microélectroniques avancés.
Au-delà des semi-conducteurs, la CVD trouve de nombreuses applications dans la technologie des écrans, où elle est utilisée pour déposer des films d'oxyde d'indium et d'étain (ITO) et des films de cuivre, améliorant ainsi la fonctionnalité et la durabilité des dispositifs d'affichage. En outre, le dépôt en phase vapeur est utilisé dans la production de revêtements optiques pour les lentilles et les miroirs, ainsi que dans les revêtements anticorrosion pour les surfaces métalliques, ce qui démontre sa polyvalence dans divers domaines.
L'importance du dépôt en phase vapeur réside non seulement dans l'étendue de ses applications, mais aussi dans sa capacité à produire des films d'une uniformité, d'une adhérence et d'une contrôlabilité exceptionnelles. Ces attributs font du dépôt en phase vapeur une technologie indispensable pour faire progresser diverses industries et stimuler l'innovation dans la science des matériaux.
Principe de fonctionnement du dépôt en phase vapeur (CVD)
Processus de réaction chimique
Au cours du processus de dépôt chimique en phase vapeur (CVD), la formation de couches minces repose sur une réaction chimique contrôlée. Dans un premier temps, des précurseurs gazeux, qui sont les matières premières du film souhaité, sont introduits dans la chambre de réaction. Ces précurseurs sont généralement des composés volatils qui peuvent être facilement vaporisés. Une fois dans la chambre, ces gaz sont soumis à la chaleur, souvent entre plusieurs centaines et milliers de degrés Celsius, en fonction du précurseur spécifique et des propriétés du film souhaitées.
Le processus de chauffage est crucial car il fournit l'énergie nécessaire pour que les molécules de gaz surmontent leurs barrières d'énergie d'activation, ce qui leur permet de réagir. À mesure que la température augmente, les précurseurs gazeux se décomposent et réagissent entre eux ou avec la surface du substrat. Cette réaction se produit généralement à la surface du substrat, où les précurseurs s'adsorbent et subissent ensuite une décomposition ou une combinaison supplémentaire. Les produits résultant de ces réactions comprennent le matériau du film souhaité, qui se dépose sur le substrat, et les sous-produits, qui sont généralement gazeux et sont évacués du système.
Par exemple, dans le dépôt de films de silicium, un précurseur courant est le silane (SiH4). Lorsqu'il est chauffé, le silane se décompose en silicium et en hydrogène gazeux. Les atomes de silicium se déposent alors sur le substrat, formant un film continu, tandis que l'hydrogène gazeux est évacué de la chambre de réaction. Cet exemple illustre la nature dynamique du procédé CVD, où un contrôle précis de la température et des débits des précurseurs est essentiel pour obtenir la qualité et l'uniformité souhaitées du film.
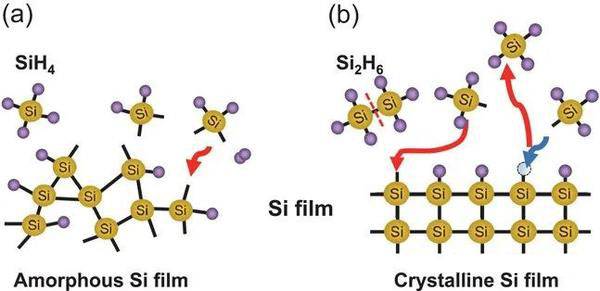
Le processus de réaction chimique dans le dépôt en phase vapeur n'est pas limité à de simples décompositions ; il peut également impliquer des réactions complexes telles que l'oxydation, la nitruration ou la formation de matériaux composés. Ces réactions sont souvent facilitées par la présence de gaz réactifs supplémentaires, tels que l'oxygène ou l'azote, qui sont introduits dans la chambre pour modifier les propriétés du film. Par exemple, lors du dépôt de films de dioxyde de silicium (SiO2), le silane réagit avec l'oxygène pour former la couche d'oxyde.
Exemple de réaction
Dans le contexte du dépôt chimique en phase vapeur (CVD), l'une des principales réactions implique la décomposition du trichlorosilane (SiHCl₃). Ce processus est fondamental pour la formation de couches minces, en particulier dans la fabrication de semi-conducteurs. Lorsque le SiHCl₃ est chauffé, il subit une transformation chimique complexe. Le matériau d'origine du silicium, SiHCl₃, se décompose en silicium élémentaire, qui se dépose ensuite sur le substrat. Simultanément, des gaz de chlore (Cl₂) et d'acide chlorhydrique (HCl) sont libérés en tant que sous-produits. Ces gaz sont généralement évacués de la chambre de réaction, de sorte qu'ils n'interfèrent pas avec le processus de dépôt.
Cette réaction illustre le principe fondamental du dépôt chimique en phase vapeur, où les gaz précurseurs sont convertis en films solides par le biais de réactions chimiques contrôlées. La décomposition du SiHCl₃ fournit non seulement le silicium nécessaire à la formation du film, mais illustre également l'importance de la gestion des gaz dans le maintien d'un environnement de dépôt propre et efficace. Les gaz sous-produits, Cl₂ et HCl, doivent absolument être surveillés et contrôlés, car leur présence peut affecter la qualité et l'uniformité du film déposé.
Classification du dépôt en phase vapeur (CVD)
Dépôt chimique en phase vapeur (CVD) thermique
Le dépôt chimique en phase vapeur (CVD) thermique consiste à chauffer les gaz précurseurs à une température élevée, généralement supérieure à 700°C, dans une chambre de réaction. Cette température élevée est essentielle pour favoriser la décomposition des gaz précurseurs, qui se déposent ensuite sur le substrat pour former un film mince. Le processus s'appuie sur l'énergie thermique pour entraîner les réactions chimiques nécessaires à la formation du film, ce qui garantit que le film déposé présente des propriétés améliorées telles qu'une meilleure cristallinité, une plus grande densité et des taux de dépôt plus rapides.
Dans le procédé CVD thermique, les réactifs gazeux sont souvent transportés dans la chambre du réacteur par un gaz inerte comme l'azote, ce qui permet de maintenir un environnement contrôlé. Les températures élevées facilitent non seulement la décomposition des précurseurs, mais permettent également des réactions qui seraient autrement impossibles à des températures plus basses. Toutefois, ces températures élevées peuvent entraîner des inconvénients tels que la formation de contraintes dans le film, des taux de diffusion plus élevés des éléments du substrat dans le film et une dégradation potentielle du substrat lui-même.
Avantages | Inconvénients |
---|---|
Vitesse de dépôt accrue | Formation de contraintes |
Amélioration de la cristallinité | Taux de diffusion plus élevés |
Plus grande densité du film | Dégradation du substrat |
La CVD thermique est particulièrement avantageuse dans la fabrication des semi-conducteurs, où elle est utilisée pour déposer des films minces tels que le dioxyde de silicium, le nitrure de silicium et le polysilicium sur des plaquettes de silicium. Ces films sont essentiels pour la fabrication de circuits intégrés et d'autres dispositifs électroniques. Malgré ses avantages, la CVD thermique nécessite une gestion minutieuse de la température et des débits de livraison des précurseurs afin d'optimiser le processus de dépôt et d'atténuer les inconvénients potentiels.
Dépôt en phase vapeur assisté par plasma (PECVD)
Le dépôt chimique en phase vapeur assisté par plasma (PECVD) est une variante spécialisée du dépôt chimique en phase vapeur (CVD) qui utilise le plasma pour augmenter la vitesse de réaction et contrôler méticuleusement le processus de dépôt. Contrairement aux méthodes traditionnelles de dépôt en phase vapeur, qui reposent uniquement sur l'énergie thermique pour décomposer les gaz précurseurs, le PECVD utilise le plasma pour activer les gaz réactifs, facilitant ainsi le dépôt à des températures nettement plus basses, généralement comprises entre 100 et 600 °C.
Dans la PECVD, le plasma agit comme un catalyseur, décomposant les précurseurs réactifs en leurs atomes ou molécules constitutifs, qui réagissent ensuite et se déposent sur la surface du substrat. Cette décomposition assistée par plasma permet le dépôt de divers films, notamment de silicium (Si), de dioxyde de silicium (SiO2), de nitrure de silicium, d'oxynitrure de silicium et de carbure de silicium, à des températures aussi basses que 200-350 °C. Cette plage de températures plus basses est particulièrement avantageuse pour les applications impliquant des matériaux sensibles à la température, tels que l'aluminium, où des températures plus élevées pourraient compromettre l'intégrité du substrat.
Le processus PECVD est souvent réalisé dans un système plasma à plaques parallèles et à couplage capacitif. Dans cette configuration, le substrat est placé sur une électrode mise à la terre, tandis que le plasma est généré entre deux électrodes. Les gaz utilisés dans le procédé PECVD peuvent varier en fonction des propriétés souhaitées du film, les gaz les plus courants étant le silane (SiH4), l'oxyde nitreux (N2O), l'ammoniac (NH3), l'hélium (He), l'argon (Ar), le trifluorure d'azote (NF3) et la phosphine (PH3). Chaque gaz joue un rôle spécifique dans le processus de dépôt, contribuant à la formation du film souhaité.
L'une des principales caractéristiques techniques de la PECVD est sa capacité à fonctionner à des températures inférieures à 540 °C, ce qui la rend adaptée à une large gamme de substrats. La chambre de traitement est généralement équipée de plusieurs chambres à gaz, telles que des chambres à silane (A + C) et une chambre à TEOS (orthosilicate de tétraéthyle) (B), chacune étant conçue pour traiter différents mélanges de gaz et répondre à différentes exigences en matière de dépôt. Cette conception modulaire permet une plus grande flexibilité et un meilleur contrôle du processus de dépôt, garantissant la production de films de haute qualité aux propriétés précises.
Dépôt en phase vapeur par procédé chimique métal-organique (MOCVD)
Le dépôt en phase vapeur par procédé chimique métal-organique (MOCVD) est une technique avancée de croissance épitaxiale qui utilise des composés métal-organiques comme gaz précurseurs pour le dépôt de films métalliques et semi-conducteurs. Cette méthode est particulièrement remarquable pour sa capacité à faire croître une large gamme de semi-conducteurs composés, y compris les matériaux Ⅲ-V et Ⅱ-VI, ainsi que leurs solutions solides multicouches.
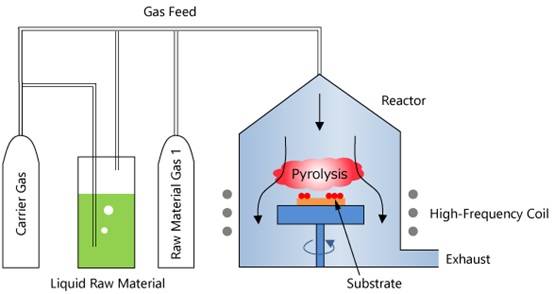
Caractéristiques principales de la MOCVD
-
Matériaux sources: La MOCVD utilise des composés organiques des éléments des groupes III et II, ainsi que des hydrures des éléments des groupes V et VI, comme sources principales pour la croissance des cristaux. Ces matériaux sont introduits dans la chambre de réaction sous forme gazeuse, où ils subissent une décomposition thermique pour former de fines couches monocristallines sur le substrat.
-
Contrôle de précision: L'un des principaux avantages de la MOCVD est le contrôle précis de la composition et de la concentration en dopants des films déposés. Cette précision est obtenue en régulant le débit et le temps d'activation/désactivation des précurseurs gazeux, ce qui permet la croissance de matériaux en couches minces et ultraminces avec une grande précision.
-
Commutation rapide: Le débit relativement rapide du gaz dans la chambre de réaction permet de modifier rapidement la composition et la concentration en dopants des multiples composés. Cette capacité de commutation rapide réduit la probabilité d'effets de mémoire, facilitant la création d'interfaces abruptes et rendant la MOCVD idéale pour la croissance d'hétérostructures, de super-réseaux et de matériaux à puits quantiques.
Avantages par rapport aux autres techniques d'épitaxie
Par rapport aux autres méthodes de croissance épitaxiale, la technique MOCVD offre plusieurs avantages distincts :
Avantage | Description |
---|---|
Contrôle des composants | L'état gazeux des précurseurs permet un contrôle précis des composants, de la concentration des dopants et de l'épaisseur de la couche épitaxiale. |
Ajustements rapides | Des changements rapides dans les débits de gaz permettent des ajustements rapides dans la composition des composés, réduisant les effets de mémoire et améliorant la qualité de l'interface. |
Polyvalence | Convient à une large gamme de semi-conducteurs composés, y compris les matériaux Ⅲ-V et Ⅱ-VI, ce qui le rend très polyvalent pour diverses applications. |
Applications de la CVD
Fabrication de semi-conducteurs
Dans la fabrication des semi-conducteurs, le dépôt chimique en phase vapeur (CVD) joue un rôle essentiel dans la création de matériaux avancés qui améliorent les performances et la fiabilité des dispositifs. Le processus implique le dépôt de divers films, notamment des siliciures, des films de nitrure et des films métalliques, chacun étant conçu pour des applications spécifiques au sein de l'industrie des semi-conducteurs.
Siliciures
Les siliciures, formées par la réaction du silicium avec des métaux, sont essentielles pour réduire la résistance de contact et améliorer l'efficacité des dispositifs à semi-conducteurs. Ils sont couramment utilisés dans les électrodes de grille, les interconnexions et les plaquettes de contact. Par exemple, le siliciure de tungstène (WSi₂) est souvent utilisé dans la technologie CMOS en raison de sa faible résistivité et de sa stabilité thermique.
Films de nitrure
Les films de nitrure, tels que le nitrure de silicium (Si₃N₄), ont de multiples fonctions dans la fabrication des semi-conducteurs. Ils agissent comme des barrières de diffusion, empêchant la migration des dopants et des impuretés, et comme des couches de passivation, protégeant le dispositif des facteurs environnementaux. En outre, les films de nitrure font partie intégrante de la formation des condensateurs dans les dispositifs DRAM, garantissant une capacité élevée et de faibles courants de fuite.
Films métalliques
Les films métalliques, y compris l'aluminium (Al) et le cuivre (Cu), sont essentiels pour créer des interconnexions qui facilitent le flux des signaux électriques dans les circuits intégrés. Le cuivre, en particulier, est apprécié pour sa faible résistivité et sa capacité à réduire la consommation d'énergie et la production de chaleur. L'utilisation de la technique CVD pour le dépôt de ces films métalliques garantit une couverture uniforme et une excellente adhérence, essentielles au maintien de l'intégrité et des performances des dispositifs semi-conducteurs.
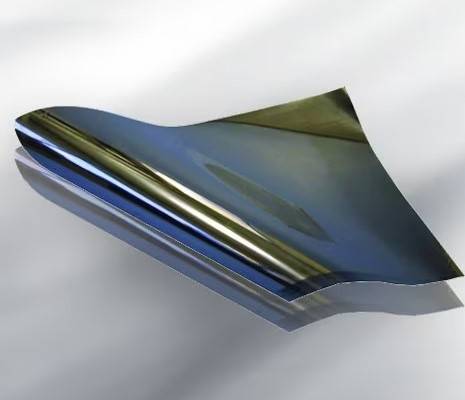
Grâce à la technologie CVD, les fabricants de semi-conducteurs peuvent contrôler avec précision le processus de dépôt, ce qui permet d'obtenir des films de haute qualité qui répondent aux exigences rigoureuses des appareils électroniques modernes.
Technologie d'affichage
Dans le domaine de la technologie d'affichage,les films d'oxyde d'indium et d'étain (ITO) etfilms de cuivre jouent un rôle essentiel. Ces matériaux font partie intégrante de la fabrication de divers dispositifs d'affichage, dont ils améliorent les performances et la fonctionnalité.
Films d'oxyde d'indium et d'étain (ITO)
Les films d'ITO sont réputés pour leur conductivité électrique et leur transparence optique exceptionnelles. Cette combinaison unique les rend idéaux pour des applications telles que :
- les écrans tactiles: Fournir la couche conductrice nécessaire aux écrans tactiles.
- Panneaux électroluminescents: Faciliter l'émission de lumière dans les écrans.
- Cellules solaires: Améliorer l'efficacité des dispositifs photovoltaïques en permettant le passage de la lumière tout en conduisant l'électricité.
Films de cuivre
Les films de cuivre, quant à eux, sont réputés pour leur conductivité électrique et leur résistance mécanique élevées. Ces propriétés sont exploitées dans :
- les écrans flexibles: Ils offrent une durabilité et une transmission efficace des signaux.
- Écrans à haute résolution: Garantissent une perte de signal minimale et un traitement des données à grande vitesse.
- Emballage avancé: Prise en charge de l'interconnectivité dans les systèmes électroniques complexes.
Les films d'ITO et de cuivre sont généralement déposés pardépôt chimique en phase vapeur (CVD) qui permettent un contrôle précis de l'épaisseur et de l'uniformité du film, garantissant ainsi des performances optimales dans les dispositifs d'affichage.
Autres domaines
La technologie de dépôt chimique en phase vapeur (CVD) étend ses applications au-delà de la fabrication de semi-conducteurs et de la technologie d'affichage, pénétrant dans diverses industries qui nécessitent des revêtements précis et durables. L'une des principales applications est lerevêtements optiquesoù le dépôt en phase vapeur est utilisé pour déposer des films minces sur des lentilles, des miroirs et d'autres composants optiques. Ces revêtements améliorent la transmission de la lumière, réduisent la réflexion et améliorent les performances optiques globales, ce qui les rend indispensables dans des domaines tels que les télécommunications, l'aérospatiale et l'imagerie médicale.
Une autre application importante est celle desles revêtements anticorrosion. Les techniques de dépôt en phase vapeur sont utilisées pour créer des couches protectrices sur les métaux et les alliages, les protégeant ainsi des conditions environnementales difficiles et prolongeant leur durée de vie. Cela est particulièrement important dans des secteurs comme l'automobile, l'aérospatiale et l'ingénierie marine, où les matériaux sont exposés à des éléments corrosifs.
Application | Impact sur l'industrie |
---|---|
Revêtements optiques | Améliorent les dispositifs optiques, essentiels pour les télécommunications et l'imagerie médicale. |
Revêtements anticorrosion | Protègent les métaux dans les secteurs de l'automobile, de l'aérospatiale et de la marine, prolongeant ainsi leur durée de vie. |
Ces applications soulignent la polyvalence et la robustesse de la technologie CVD, qui en fait une pierre angulaire des processus industriels modernes.
Caractéristiques du procédé CVD
Exigences en matière de températures élevées
La température élevée exigée par le procédé de dépôt chimique en phase vapeur (CVD) est essentielle pour plusieurs raisons. Tout d'abord, les températures élevées sont essentielles pourfavoriser la vitesse de réaction des gaz précurseurs. Lorsqu'ils sont chauffés, ces gaz subissent une décomposition et des réactions chimiques ultérieures à la surface du substrat, ce qui conduit à la formation de la couche mince souhaitée. L'énergie cinétique fournie par la chaleur garantit que les molécules ont suffisamment d'énergie pour réagir et former des liaisons stables.
En outre, les températures élevées contribuent àaméliorer la vitesse de diffusion des réactifs sur le substrat. Cette diffusion est cruciale pour obtenir un dépôt de film uniforme sur la surface. Sans chaleur adéquate, le processus de diffusion serait lent, ce qui donnerait des films non uniformes et potentiellement défectueux.
En outre, les températures élevées jouent un rôle danséliminer les impuretés de l'environnement de réaction. Les impuretés telles que l'humidité ou les gaz résiduels peuvent être éliminées à des températures élevées, ce qui garantit un processus de dépôt plus propre. Cet aspect de la purification est particulièrement important dans la fabrication de matériaux de haute pureté utilisés dans les dispositifs semi-conducteurs.
Plage de température | Effet |
---|---|
Faible (<400°C) | Vitesse de réaction lente, diffusion limitée, risque de films non uniformes. |
Moyenne (400-800°C) | Optimisée pour de nombreux procédés CVD, taux de réaction et de diffusion équilibrés. |
Haute (>800°C) | Réactions rapides, taux de diffusion élevés, mais risque de dépasser les limites thermiques du substrat. |
Environnement sous vide
Le processus de dépôt en phase vapeur (CVD) se déroule généralement sous vide. Cette atmosphère contrôlée est cruciale pour plusieurs raisons. Tout d'abord, le vide minimise la présence de contaminants, tels que l'oxygène et la vapeur d'eau, qui pourraient autrement interférer avec les réactions chimiques et dégrader la qualité du film déposé. Deuxièmement, le maintien du vide permet de gérer la pression à l'intérieur de la chambre de dépôt, ce qui garantit que les précurseurs gazeux s'écoulent à des vitesses optimales et réagissent efficacement à la surface du substrat.
Dans le vide, le libre parcours moyen des molécules de gaz augmente, ce qui réduit les collisions entre les molécules. Cette réduction des collisions permet un mouvement plus dirigé des précurseurs gazeux vers le substrat, améliorant ainsi le processus de dépôt. En outre, l'environnement sous vide permet de mieux contrôler les conditions de température et de pression, qui sont des paramètres critiques dans le processus de dépôt chimique en phase vapeur (CVD).
Avantages | Description de l'avantage |
---|---|
Réduction des contaminants | Minimise l'interférence de l'oxygène et de la vapeur d'eau. |
Gestion de la pression | Assure un flux et une réaction optimaux des précurseurs gazeux. |
Augmentation du libre parcours moyen | Réduit les collisions moléculaires, améliorant ainsi le dépôt. |
Contrôle de la température | Facilite un meilleur contrôle des paramètres critiques. |
L'environnement sous vide n'est pas seulement une exigence technique, mais un aspect fondamental qui sous-tend l'efficacité et la précision du procédé CVD. En maintenant le vide, les fabricants peuvent obtenir des films uniformes de haute qualité présentant les propriétés souhaitées, ce qui en fait un élément indispensable de la technologie CVD.
Préparation de la surface
Avant tout processus de revêtement, en particulier dans le cadre du dépôt chimique en phase vapeur (CVD), la surface du substrat doit faire l'objet d'une préparation rigoureuse afin de garantir une adhérence et une qualité de film optimales. Cette étape est cruciale car elle a un impact direct sur les performances et la longévité des couches minces déposées.
Les contaminants tels que les résidus organiques, les oxydes et l'humidité doivent être méticuleusement éliminés. Ces impuretés peuvent entraver les réactions chimiques nécessaires à la formation du film et entraîner des défauts tels que des trous d'épingle ou des revêtements non uniformes. Les techniques de préparation des surfaces varient, mais les méthodes les plus courantes sont les suivantesle nettoyage chimique,gravureettraitement au plasma.
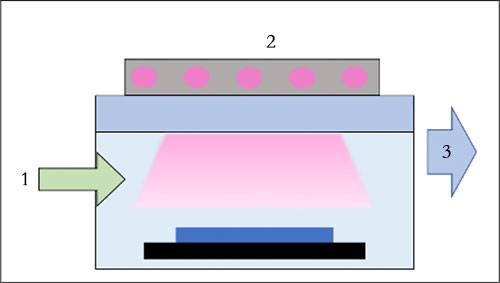
-
Nettoyage chimique: Il s'agit d'utiliser des solvants ou des acides pour dissoudre et éliminer les contaminants organiques et inorganiques. Par exemple, le nettoyage RCA est une méthode standard qui utilise un mélange de peroxyde d'hydrogène et d'acide sulfurique pour nettoyer les plaquettes de silicium.
-
Gravure: Cette méthode permet d'éliminer sélectivement les couches superficielles à l'aide de réactions chimiques. Par exemple, l'acide fluorhydrique est souvent utilisé pour enlever le dioxyde de silicium natif des substrats de silicium.
-
Traitement au plasma: Cette technique utilise le plasma pour activer la surface, améliorer sa réactivité et la débarrasser de tout contaminant résiduel. Elle est particulièrement efficace pour éliminer les résidus organiques et améliorer l'énergie de surface.
Chacune de ces méthodes joue un rôle essentiel en garantissant que le substrat est exempt de contaminants, ce qui facilite le dépôt de films minces de haute qualité. Une bonne préparation de la surface permet non seulement d'améliorer l'adhérence du film déposé, mais aussi de s'assurer que les propriétés du film, telles que l'uniformité et la densité, répondent aux spécifications requises.
Limites du substrat
Les limites de température et de réactivité sont des facteurs critiques qui peuvent considérablement restreindre la gamme des substrats applicables dans les procédés de dépôt chimique en phase vapeur (CVD). Les températures élevées requises pour que les réactions chimiques se produisent peuvent imposer des contraintes thermiques au matériau du substrat, ce qui limite le choix à ceux qui peuvent résister à ces conditions extrêmes sans dégradation ni déformation. Par exemple, certains matériaux organiques ou métaux à bas point de fusion peuvent ne pas convenir en raison de leur incapacité à maintenir leur intégrité structurelle à des températures élevées.
En outre, la réactivité des gaz précurseurs et les interactions chimiques qui en résultent avec la surface du substrat peuvent encore réduire la sélection des matériaux appropriés. Certains substrats peuvent réagir de manière défavorable avec les gaz de dépôt, entraînant des réactions secondaires indésirables ou la formation de films non uniformes. Cette limitation de la réactivité nécessite une sélection minutieuse et un prétraitement des substrats afin de garantir leur compatibilité avec le procédé CVD.
Couverture et masquage
Dans le contexte du dépôt chimique en phase vapeur (CVD), le processus de couverture et de masquage joue un rôle crucial dans la détermination de la qualité finale et de la fonctionnalité des couches minces déposées. Alors que le dépôt chimique en phase vapeur garantit que toutes les zones du substrat sont uniformément recouvertes du matériau souhaité, la capacité à masquer sélectivement des zones spécifiques devient un facteur critique pour obtenir des motifs et des structures précis.
L'aspect couverture du dépôt chimique en phase vapeur est très efficace, car il se traduit généralement par un dépôt uniforme de matériau sur toute la surface du substrat. Cette uniformité est essentielle pour les applications où une épaisseur de film uniforme est nécessaire, comme dans la fabrication de semi-conducteurs et la technologie d'affichage. Toutefois, le problème se pose lorsque des zones spécifiques du substrat doivent être protégées du processus de dépôt. C'est là que les techniques de masquage entrent en jeu.
Le masquage en dépôt chimique en phase vapeur implique l'utilisation de barrières physiques ou de couches de résine photosensible pour empêcher le dépôt de matériaux dans certaines zones. Bien que cette technique soit généralement efficace, elle présente des limites. Par exemple, la précision du processus de masquage peut être affectée par des facteurs tels que le type de substrat, la complexité du motif et les paramètres spécifiques du dépôt en phase vapeur utilisés. En outre, les matériaux de masquage eux-mêmes doivent être choisis avec soin pour s'assurer qu'ils ne réagissent pas avec les gaz de dépôt ou qu'ils ne se dégradent pas sous l'effet des températures élevées généralement associées aux procédés CVD.
Limitation de l'épaisseur du film
L'épaisseur des films minces déposés par dépôt chimique en phase vapeur (CVD) est intrinsèquement limitée par plusieurs facteurs, principalement les paramètres du procédé et l'état physique des matériaux concernés. Ces limitations sont essentielles pour comprendre les applications pratiques et les limites de la technologie CVD.
Paramètres du procédé
Le processus de dépôt lui-même impose plusieurs contraintes sur l'épaisseur du film. Les facteurs clés sont les suivants
- la température et la pression: Les températures élevées requises pour les réactions CVD peuvent limiter l'épaisseur du film déposé. Les températures extrêmes peuvent entraîner une dégradation thermique ou une non-uniformité du film. De même, la pression sous laquelle le processus est mené peut affecter la vitesse de croissance et l'uniformité du film.
- Cinétique des réactions: La vitesse à laquelle les gaz précurseurs réagissent et forment le film souhaité est un autre facteur limitant. Des réactions plus rapides peuvent conduire à des films plus fins si le processus n'est pas soigneusement contrôlé.
État du matériau
Les propriétés physiques et chimiques des matériaux précurseurs jouent également un rôle important :
- Stabilité du précurseur: La stabilité des gaz précurseurs à haute température peut limiter l'épaisseur du film. Les précurseurs instables peuvent se décomposer prématurément, ce qui entraîne des films incomplets ou non uniformes.
- Compatibilité du substrat: La capacité du matériau du substrat à supporter les conditions de dépôt est cruciale. Certains substrats peuvent ne pas être en mesure de supporter les températures élevées ou la réactivité requises pour le dépôt de films plus épais.
Ces contraintes ne sont pas de simples limitations mais font partie intégrante du processus, garantissant que les films déposés sont de haute qualité et adaptés aux applications prévues.
Adhésion
La technologie de dépôt chimique en phase vapeur (CVD) se caractérise par d'excellentes propriétés d'adhésion, qui sont cruciales pour la durabilité et la fonctionnalité des films minces qu'elle produit. L'adhérence de ces films est influencée par plusieurs facteurs, notamment la préparation de la surface du substrat, la réactivité chimique des gaz précurseurs et les conditions du processus telles que la température et la pression.
Par exemple, une bonne préparation de la surface permet d'éliminer les contaminants et de créer une surface propre et réactive qui améliore l'adhérence entre le film et le substrat. Cette étape est particulièrement importante dans la fabrication des semi-conducteurs, où même des impuretés mineures peuvent entraîner des problèmes de performance importants.
La nature chimique des gaz précurseurs joue également un rôle essentiel. La réaction entre les gaz précurseurs et la surface du substrat forme une liaison chimique forte, qui est à la base de l'excellente adhérence observée dans les films CVD. Ce mécanisme de liaison chimique garantit que les films déposés restent fermement attachés au substrat, même dans des conditions opérationnelles difficiles.
Les conditions du processus, telles que les températures élevées requises pour le dépôt chimique en phase vapeur, contribuent également à la forte adhérence. Ces températures élevées favorisent non seulement les réactions chimiques nécessaires à la formation du film, mais permettent également une meilleure diffusion des matériaux du film dans le substrat, créant ainsi une interface plus robuste.
Avantages de la technologie CVD
Uniformité
L'uniformité du dépôt chimique en phase vapeur (CVD) est un attribut essentiel qui garantit une qualité de film constante sur des substrats de grande surface. Cette uniformité est obtenue grâce à un contrôle méticuleux des paramètres du processus, notamment la température, la pression et les débits des précurseurs. La capacité à maintenir l'uniformité est particulièrement cruciale dans la fabrication des semi-conducteurs, où des variations même mineures peuvent entraîner des problèmes de performance importants dans le produit final.
Pour illustrer ce point, prenons l'exemple d'une installation CVD typique où le substrat est exposé à un flux uniforme de gaz précurseurs. Les molécules de gaz se diffusent et réagissent à la surface du substrat, formant un film mince. En gérant avec précision la distribution de ces gaz, les fabricants peuvent s'assurer que le dépôt se produit uniformément sur l'ensemble du substrat, quelle que soit sa taille. Cette opération est souvent facilitée par la conception de réacteurs avancés qui favorisent une distribution uniforme des gaz et minimisent les variations localisées.
Paramètre | Impact sur l'uniformité |
---|---|
Température | Assure une décomposition et un dépôt uniformes des précurseurs. |
Pression | Permet de maintenir un débit de gaz et un taux de réaction cohérents. |
Flux de précurseurs | Contrôle la concentration et la distribution des espèces réactives. |
En résumé, l'uniformité des procédés CVD n'est pas seulement une caractéristique souhaitable, mais une exigence fondamentale pour produire des couches minces de haute qualité. Elle souligne l'importance d'un contrôle précis du processus et d'une technologie de réacteur avancée pour obtenir des résultats cohérents sur de grands substrats.
Contrôlabilité
L'une des principales caractéristiques de la technologie de dépôt chimique en phase vapeur (CVD) est son haut degré de contrôle du processus de dépôt. Ce contrôle est essentiel pour obtenir des propriétés de film et des taux de dépôt précis, qui sont essentiels pour diverses applications dans la fabrication de semi-conducteurs, la technologie d'affichage et autres.
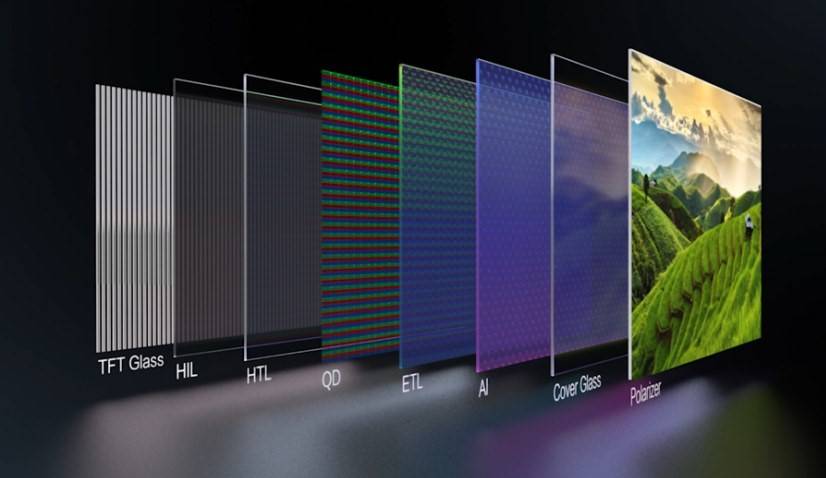
Contrôle de la vitesse de dépôt
La vitesse de dépôt dans le procédé CVD peut être minutieusement contrôlée en ajustant plusieurs paramètres. Ces paramètres sont les suivants
- la température: En faisant varier la température du substrat et des gaz précurseurs, la vitesse à laquelle les réactions chimiques se produisent peut être ajustée avec précision. Des températures plus élevées accélèrent généralement la vitesse de réaction, ce qui conduit à un dépôt plus rapide.
- La pression: Le fait d'opérer sous différentes pressions peut influencer la dynamique du flux des gaz précurseurs et la vitesse à laquelle ils atteignent la surface du substrat.
- Débits de gaz: Le contrôle des débits des gaz précurseurs permet des ajustements précis de la concentration des réactifs sur le substrat, affectant ainsi la vitesse de dépôt.
Personnalisation des propriétés du film
Au-delà de la vitesse de dépôt, le dépôt chimique en phase vapeur permet un contrôle étendu des propriétés du film obtenu. Les principales propriétés qui peuvent être personnalisées sont les suivantes
- Epaisseur du film: En gérant soigneusement les paramètres du procédé, l'épaisseur du film déposé peut être contrôlée dans une fourchette étroite, ce qui garantit l'uniformité sur des substrats de grande taille.
- Composition chimique: L'utilisation de différents gaz ou mélanges de précurseurs permet de déposer des films de compositions chimiques variées, adaptées aux exigences d'applications spécifiques.
- Structure cristalline: Les conditions de température et de pression peuvent influencer la cristallinité du film déposé, permettant la création de structures amorphes ou cristallines selon les besoins.
- Contrainte: La tension interne du film peut être contrôlée pour éviter les défauts et garantir l'intégrité et l'adhérence du film au substrat.
Flexibilité du procédé
La contrôlabilité du dépôt en phase vapeur s'étend à la flexibilité du procédé lui-même. Les différents types de dépôt en phase vapeur, tels que le dépôt en phase vapeur thermique, le dépôt en phase vapeur assisté par plasma (PECVD) et le dépôt en phase vapeur métal-organique (MOCVD), offrent des avantages et des mécanismes de contrôle uniques. Par exemple, la PECVD utilise le plasma pour augmenter la vitesse de réaction et fournir un contrôle supplémentaire sur le processus de dépôt, tandis que la MOCVD permet d'utiliser des composés métallo-organiques pour déposer des matériaux complexes.
Polyvalence
La technologie de dépôt chimique en phase vapeur (CVD) se distingue par sa polyvalence exceptionnelle, ce qui en fait une pierre angulaire dans diverses industries. Cette polyvalence est principalement attribuée à sa capacité à déposer une large gamme de matériaux, chacun adapté à des applications spécifiques. Qu'il s'agisse de créer des films semi-conducteurs de haute qualité, d'améliorer les technologies d'affichage ou de mettre au point des revêtements protecteurs, le dépôt en phase vapeur prouve son adaptabilité à différents types de matériaux et d'exigences fonctionnelles.
Diversité des matériaux
La capacité du dépôt en phase vapeur à traiter divers matériaux est un avantage significatif. Des films de silicium et de métal aux composés complexes tels que les nitrures et les oxydes, la gamme des matériaux pouvant être traités est très étendue. Ce large éventail permet au procédé CVD de répondre aux exigences rigoureuses des applications technologiques modernes, de la microélectronique à l'optique avancée.
Flexibilité des applications
Au-delà de la diversité des matériaux, la flexibilité du dépôt en phase vapeur s'étend à ses applications dans de multiples domaines. Dans la fabrication des semi-conducteurs, elle est indispensable pour créer des siliciures, des films de nitrure et des couches métalliques, qui jouent tous un rôle crucial dans les performances des appareils. Dans la technologie des écrans, la CVD est utilisée pour déposer des films d'oxyde d'indium et d'étain (ITO) et de cuivre, ce qui améliore la fonctionnalité et la durabilité des écrans. En outre, le dépôt en phase vapeur trouve son utilité dans des domaines moins conventionnels tels que les revêtements optiques et les traitements anticorrosion, ce qui illustre encore sa polyvalence.
Adaptabilité des procédés
L'adaptabilité des procédés de dépôt en phase vapeur est une autre facette de sa polyvalence. Les techniques telles que la CVD thermique, la CVD assistée par plasma (PECVD) et la CVD métal-organique (MOCVD) offrent chacune des avantages uniques, permettant un contrôle précis du processus de dépôt. Cette adaptabilité garantit que la CVD peut être optimisée pour différents substrats et conditions environnementales, ce qui en fait un outil polyvalent entre les mains des chercheurs et des ingénieurs.
CONTACTEZ-NOUS POUR UNE CONSULTATION GRATUITE
Les produits et services de KINTEK LAB SOLUTION ont été reconnus par des clients du monde entier. Notre personnel se fera un plaisir de répondre à toute demande que vous pourriez avoir. Contactez-nous pour une consultation gratuite et parlez à un spécialiste produit pour trouver la solution la plus adaptée aux besoins de votre application !