Les revêtements par dépôt physique en phase vapeur (PVD) sont appliqués grâce à un processus hautement contrôlé qui consiste à vaporiser un matériau solide dans un environnement sous vide et à le déposer sur un substrat pour former un film mince et durable.Ce procédé est largement utilisé dans des industries telles que l'aérospatiale, l'automobile et la fabrication d'outils pour améliorer les propriétés de surface telles que la dureté, la résistance à l'usure et la résistance à la corrosion.Les principales étapes consistent à préparer le substrat, à créer un vide, à vaporiser le matériau cible et à déposer le matériau vaporisé sur le substrat.Des gaz réactifs peuvent être introduits pour modifier les propriétés du revêtement, et le processus est réalisé dans une chambre à vide pour garantir la propreté et la précision.
Explication des points clés :
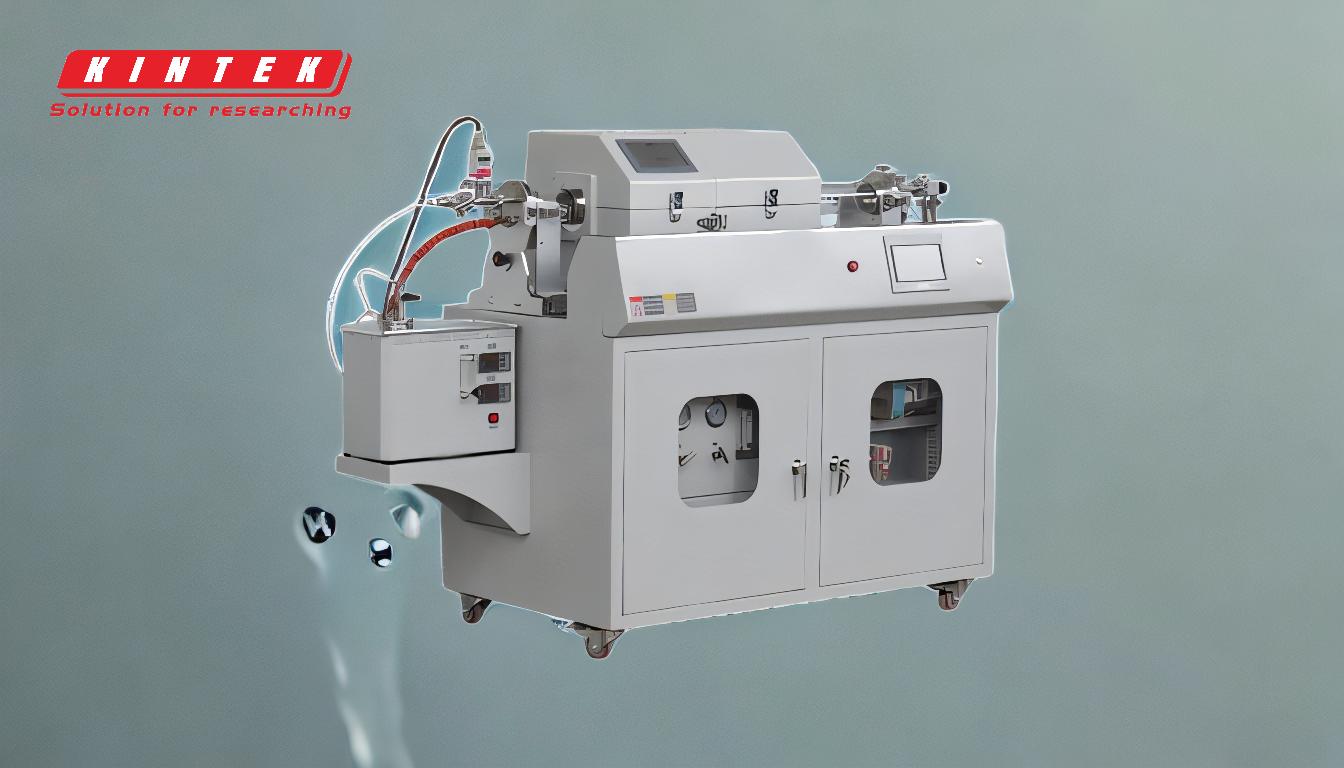
-
Préparation du substrat:
- Nettoyage:Le substrat est soigneusement nettoyé pour éliminer les contaminants tels que les huiles, la poussière ou les oxydes.Cette étape est cruciale pour garantir une bonne adhérence du revêtement.
- Prétraitement:Le substrat peut subir des traitements supplémentaires, tels que la gravure ou le bombardement ionique, afin d'améliorer la rugosité de la surface et l'adhérence du revêtement.
-
Création d'un environnement sous vide:
- Le substrat et le matériau cible sont placés dans une chambre à vide, qui est ensuite évacuée pour créer un environnement sous vide poussé (généralement de 10-³ à 10-⁹ Torr).Cette étape permet de s'assurer que le matériau vaporisé ne sera pas contaminé et qu'il pourra être contrôlé avec précision.
-
Vaporisation du matériau cible:
-
Techniques de vaporisation:Différentes méthodes sont utilisées pour vaporiser le matériau cible, notamment :
- l'évaporation par faisceau d'électrons:Un faisceau d'électrons à haute énergie chauffe le matériau cible jusqu'à ce qu'il se vaporise.
- Pulvérisation:Le bombardement ionique déloge les atomes du matériau cible.
- Évaporation par arc cathodique:Un arc électrique à haute intensité vaporise le matériau cible.
- Évaporation thermique:Le matériau cible est chauffé dans un creuset jusqu'à ce qu'il se vaporise.
- Gaz réactifs:Des gaz réactifs comme l'azote ou l'oxygène peuvent être introduits pour modifier la composition de la matière vaporisée, formant des composés tels que des nitrures ou des oxydes métalliques.
-
Techniques de vaporisation:Différentes méthodes sont utilisées pour vaporiser le matériau cible, notamment :
-
Transport de la matière vaporisée:
- Les atomes ou molécules vaporisés sont transportés à travers la chambre à vide jusqu'au substrat.Cette étape est influencée par la pression du vide et la distance entre la cible et le substrat.
-
Dépôt sur le substrat:
-
Le matériau vaporisé se condense sur le substrat, formant un film mince et uniforme.Le processus de dépôt peut être amélioré par
- Bombardement ionique:Les ions sont utilisés pour améliorer la densité et l'adhérence du revêtement.
- Assistance plasma:Un environnement plasma peut améliorer la réactivité et l'uniformité du revêtement.
-
Le matériau vaporisé se condense sur le substrat, formant un film mince et uniforme.Le processus de dépôt peut être amélioré par
-
Procédés de post-dépôt:
- Contrôle de la qualité:Le revêtement est inspecté pour s'assurer qu'il répond aux spécifications en matière d'épaisseur, d'adhérence et de performance.
- Finition:Des traitements supplémentaires, tels que le polissage ou la modification de la surface, peuvent être appliqués pour améliorer l'aspect ou la fonctionnalité du revêtement.
-
Avantages des revêtements PVD:
- Durabilité:Les revêtements PVD sont très résistants à l'usure, à la corrosion et à l'oxydation.
- Précision:Le procédé permet un contrôle précis de l'épaisseur et de la composition du revêtement.
- La polyvalence:Une large gamme de matériaux peut être utilisée comme cibles, et les propriétés du revêtement peuvent être adaptées en ajustant les paramètres du processus.
En suivant ces étapes, les revêtements PVD offrent une surface performante et durable qui répond aux exigences des applications industrielles modernes.
Tableau récapitulatif :
Étape | Détails clés |
---|---|
Préparation du substrat | Nettoyage et prétraitement (gravure, bombardement ionique) pour une forte adhérence. |
Environnement sous vide | La chambre à vide poussé (10-³ à 10-⁹ Torr) garantit une vaporisation sans contamination. |
Techniques de vaporisation | Faisceau d'électrons, pulvérisation, arc cathodique ou méthodes d'évaporation thermique. |
Gaz réactifs | L'azote ou l'oxygène modifie les propriétés du revêtement (par exemple, les nitrures/oxydes métalliques). |
Transport et dépôt | Le matériau vaporisé se condense sur le substrat pour former un film fin et uniforme. |
Procédés de post-dépôt | Contrôle de la qualité et finition (polissage, modification de la surface) pour la performance. |
Découvrez comment les revêtements PVD peuvent améliorer vos applications industrielles. contactez nos experts dès aujourd'hui !