Un moule est un outil essentiel dans les processus de fabrication tels que le moulage par injection, et sa conception a une incidence directe sur la qualité et la fonctionnalité du produit final.À la base, un moule se compose de deux moitiés principales : la cavité et le noyau.La cavité forme la forme extérieure du produit, tandis que le noyau en forme l'intérieur ou l'arrière.Ces deux moitiés travaillent ensemble pour créer la pièce souhaitée.Outre ces composants primaires, les moules peuvent comporter des caractéristiques supplémentaires telles que des glissières, des portes et des broches d'éjection pour faciliter le flux de matériau et l'enlèvement des pièces.Il est essentiel de comprendre les principales parties d'un moule pour garantir une production efficace et des résultats de haute qualité.
Explication des points clés :
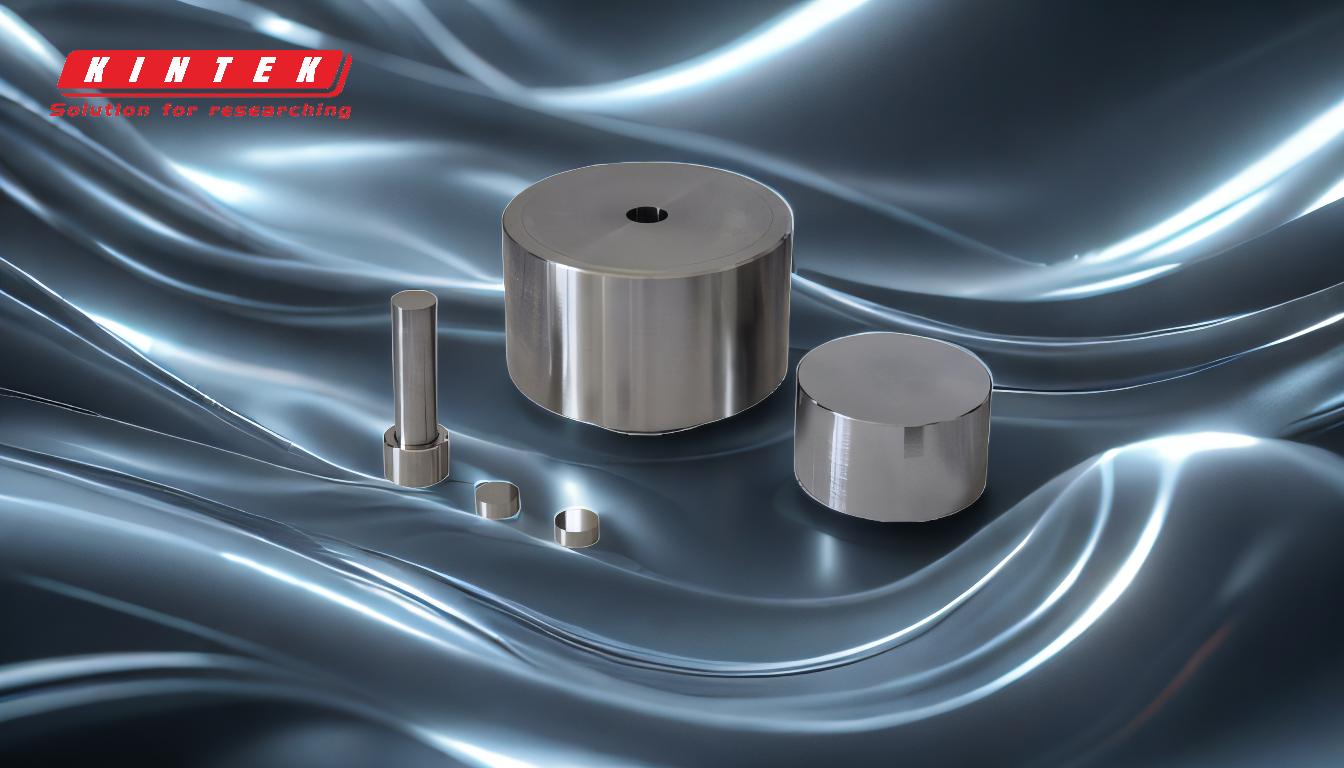
-
Cavité et cœur:
- La cavité est la partie du moule qui forme la surface extérieure du produit.Il s'agit généralement de la face A, qui est la face cosmétique présentant un meilleur aspect extérieur.
- L'âme est la partie qui forme l'intérieur ou l'arrière du produit, connue sous le nom de "face B".Elle comporte souvent des caractéristiques fonctionnelles telles que des nervures ou des bossages.
-
Plaques métalliques:
- Les moules sont constitués de deux plaques métalliques qui abritent la cavité et le noyau.Ces plaques sont usinées avec précision pour correspondre à la forme souhaitée de la pièce finie.
- Les plaques doivent résister à une pression et à une température élevées pendant le processus de moulage, c'est pourquoi elles sont généralement fabriquées dans des matériaux durables comme l'acier ou l'aluminium.
-
Cavités:
- Les cavités sont les espaces creux à l'intérieur des plaques du moule où le matériau (par exemple, le plastique ou le caoutchouc) est injecté pour former le produit.
- La conception des cavités influence directement les dimensions, l'état de surface et l'intégrité structurelle du produit final.
-
Rails et portes:
- Les glissières sont des canaux qui guident la matière en fusion depuis la buse de la machine de moulage par injection jusqu'aux cavités.
- Les portes sont les points d'entrée où la matière s'écoule dans les cavités.Leur conception influe sur le débit, le refroidissement et l'aspect final du produit.
-
Système d'éjection:
- Après la solidification du matériau, le système d'éjection permet de retirer la pièce finie du moule.Ce système comprend généralement des broches d'éjection qui poussent la pièce hors de la cavité.
- Une éjection correcte est essentielle pour éviter d'endommager la pièce ou le moule.
-
Système de refroidissement:
- Les moules comportent souvent des canaux de refroidissement pour réguler la température et assurer un refroidissement uniforme du matériau.Cela permet d'éviter les défauts tels que le gauchissement ou les marques d'enfoncement.
- Un refroidissement efficace est essentiel pour maintenir les temps de cycle et la qualité du produit.
-
Caractéristiques d'alignement et de soutien:
- Les moules peuvent comporter des goupilles de guidage et des bagues pour assurer un alignement précis des moitiés de la cavité et du noyau.
- Les caractéristiques de soutien, telles que les bases de moule et les plaques de serrage, assurent la stabilité structurelle pendant le processus de moulage.
En comprenant ces principales parties d'un moule, les fabricants peuvent optimiser leurs conceptions pour améliorer les performances, la durabilité et la qualité des produits.Chaque composant joue un rôle essentiel dans la fonctionnalité globale du moule, et leur bonne intégration est la clé d'une production réussie.
Tableau récapitulatif :
Composant | Fonction |
---|---|
Cavité | Forme la surface extérieure (côté A) du produit. |
Noyau | Forme l'intérieur ou la face arrière (face B) du produit. |
Plaques métalliques | Elles abritent la cavité et le noyau ; elles sont fabriquées dans des matériaux durables tels que l'acier ou l'aluminium. |
Glissières et portes | Canaux et points d'entrée pour l'écoulement des matières en fusion. |
Système d'éjection | Retire la pièce finie du moule à l'aide de broches d'éjection. |
Système de refroidissement | Régule la température pour assurer un refroidissement uniforme et éviter les défauts. |
Caractéristiques d'alignement | Garantit un alignement précis des moitiés de la cavité et du noyau. |
Optimisez la conception de vos moules pour une meilleure efficacité de production. contactez nos experts dès aujourd'hui !