Le revêtement par dépôt physique en phase vapeur (PVD) est une technique polyvalente et largement utilisée pour appliquer des couches minces sur divers substrats.Le processus consiste à vaporiser un matériau solide dans un environnement sous vide et à le déposer sur un substrat pour former un revêtement mince et durable.Il existe plusieurs types de revêtements et de procédés PVD, chacun présentant des caractéristiques et des avantages uniques, ce qui les rend adaptés à différentes applications et à différents matériaux.
Explication des points clés :
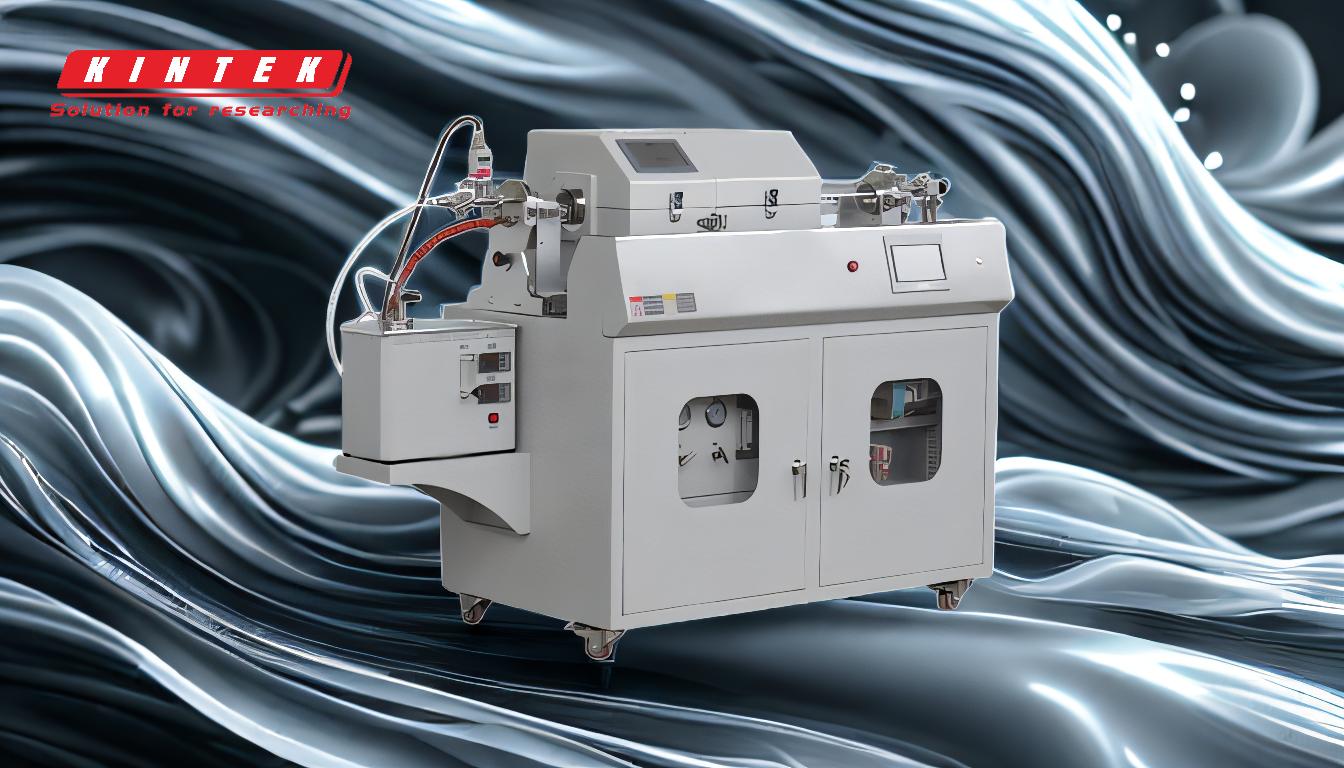
-
Types de revêtements PVD :
- Nitrure de titane (TiN) : Connu pour sa couleur dorée, le TiN est largement utilisé pour sa dureté, sa résistance à l'usure et ses propriétés de faible friction.Il est couramment utilisé pour les outils de coupe, les moules et les dispositifs médicaux.
- Nitrure de chrome (CrN) : Les revêtements CrN offrent une excellente résistance à la corrosion, une stabilité à haute température et un faible frottement.Ils sont souvent utilisés dans des applications nécessitant une résistance élevée à l'usure et une protection contre la corrosion, notamment dans les secteurs de l'automobile et de l'aérospatiale.
- Nitrure de titane et d'aluminium (TiAlN) : Ce revêtement est connu pour sa grande résistance à l'oxydation et sa dureté, ce qui le rend idéal pour l'usinage à grande vitesse et les outils de coupe.
- Nitrure de titane et de bore (TiBN) : Les revêtements TiBN combinent les propriétés du TiN et du nitrure de bore, offrant une grande dureté, un faible frottement et une excellente résistance à l'usure.Ils sont utilisés dans des applications nécessitant une durabilité et des performances extrêmes.
-
Procédés de revêtement PVD :
- Dépôt par arc cathodique : Ce procédé consiste à créer un arc entre une cathode (matériau cible) et une anode, ce qui vaporise le matériau cible.Le matériau vaporisé se condense ensuite sur le substrat.Cette méthode est connue pour produire des revêtements denses et de haute qualité avec une excellente adhérence.
- Dépôt physique en phase vapeur par faisceau d'électrons (EB-PVD) : Dans ce procédé, un faisceau d'électrons est utilisé pour vaporiser le matériau cible.Le matériau vaporisé est ensuite déposé sur le substrat.Le procédé EB-PVD est connu pour sa capacité à produire des revêtements de haute pureté et est souvent utilisé dans l'industrie aérospatiale pour les revêtements à barrière thermique.
- Dépôt par évaporation : Cette méthode consiste à chauffer le matériau cible jusqu'à ce qu'il s'évapore.Le matériau vaporisé se condense ensuite sur le substrat.Le dépôt par évaporation est couramment utilisé pour le revêtement des composants optiques et des appareils électroniques.
- Dépôt par laser pulsé (PLD) : Le PLD utilise un laser de forte puissance pour vaporiser le matériau cible.Le matériau vaporisé est ensuite déposé sur le substrat.Cette méthode est connue pour sa capacité à produire des revêtements complexes, multicouches, avec un contrôle précis de l'épaisseur et de la composition.
- Dépôt par pulvérisation cathodique : Dans ce processus, des ions sont utilisés pour bombarder le matériau cible, ce qui provoque l'éjection d'atomes et leur dépôt sur le substrat.Le dépôt par pulvérisation cathodique est largement utilisé pour produire des couches minces présentant une excellente uniformité et une bonne adhérence.Il est couramment utilisé dans les industries des semi-conducteurs et de l'optique.
-
Techniques courantes de revêtement PVD :
- Évaporation thermique : Cette technique consiste à chauffer le matériau cible jusqu'à ce qu'il s'évapore.Le matériau vaporisé est ensuite déposé sur le substrat.L'évaporation thermique est couramment utilisée pour le revêtement des métaux et des alliages.
- Revêtement par pulvérisation cathodique : Le revêtement par pulvérisation cathodique consiste à bombarder le matériau cible avec des ions, ce qui provoque l'éjection d'atomes et leur dépôt sur le substrat.Cette technique est connue pour produire des revêtements uniformes de haute qualité et est largement utilisée dans les secteurs de l'électronique et de l'optique.
- Placage ionique : Le placage ionique combine les techniques d'évaporation et de pulvérisation.Le matériau cible est vaporisé et des ions sont utilisés pour améliorer le processus de dépôt, ce qui permet d'obtenir des revêtements denses et adhérents.Cette technique est souvent utilisée pour le revêtement d'outils et de composants nécessitant une grande résistance à l'usure.
- Ablation au laser : Dans cette technique, un laser de forte puissance est utilisé pour vaporiser le matériau cible.Le matériau vaporisé est ensuite déposé sur le substrat.L'ablation laser est connue pour sa capacité à produire des revêtements complexes de haute qualité avec un contrôle précis de l'épaisseur et de la composition.
-
Applications des revêtements PVD :
- Outils de coupe : Les revêtements PVD sont largement utilisés pour améliorer les performances et la durée de vie des outils de coupe en offrant une résistance à l'usure, une faible friction et une grande dureté.
- Dispositifs médicaux : Les revêtements PVD sont appliqués aux appareils médicaux pour améliorer la biocompatibilité, la résistance à la corrosion et la résistance à l'usure.
- Composants automobiles : Les revêtements PVD sont utilisés dans l'industrie automobile pour améliorer les performances et la durabilité des composants du moteur, des pièces de la transmission et d'autres composants critiques.
- Composants aérospatiaux : Les revêtements PVD sont utilisés dans l'industrie aérospatiale pour les revêtements de barrière thermique, les revêtements résistants à l'usure et les revêtements résistants à la corrosion sur les pales de turbines, les composants de moteurs et d'autres pièces critiques.
- Composants optiques : Les revêtements PVD sont utilisés pour améliorer les performances des composants optiques en fournissant des revêtements antireflets, anti-rayures et protecteurs.
En résumé, le revêtement PVD offre un large éventail d'options en termes de types de revêtements et de procédés utilisés pour les appliquer.Chaque type de revêtement et de procédé présente des caractéristiques et des avantages uniques, ce qui les rend adaptés à des applications et à des matériaux différents.Comprendre les exigences spécifiques de votre application vous aidera à choisir l'option de revêtement PVD la plus appropriée.
Tableau récapitulatif :
Aspect | Détails |
---|---|
Types de revêtements PVD | - Nitrure de titane (TiN) : dureté, résistance à l'usure, faible friction. |
- Nitrure de chrome (CrN) :Résistance à la corrosion, stabilité à haute température. | |
- Nitrure de titane et d'aluminium (TiAlN) : résistance élevée à l'oxydation, dureté. | |
- Nitrure de titane et de bore (TiBN) : dureté élevée, faible frottement, résistance à l'usure. | |
Procédés de revêtement PVD | - Dépôt par arc cathodique :Revêtements denses et de haute qualité. |
- PVD par faisceau d'électrons (EB-PVD) :Revêtements de haute pureté, applications aérospatiales. | |
- Dépôt par évaporation :Revêtements optiques et électroniques. | |
- Dépôt par laser pulsé (PLD) :Revêtements complexes et multicouches. | |
- Dépôt par pulvérisation cathodique :Couches minces uniformes et adhérentes. | |
Applications | - Outils de coupe :Amélioration de la résistance à l'usure et de la durée de vie. |
- Dispositifs médicaux :Amélioration de la biocompatibilité et de la résistance à la corrosion. | |
- Automobile :Composants durables de moteurs et de transmissions. | |
- Aérospatiale :Barrière thermique et revêtements résistants à l'usure. | |
- Composants optiques :Revêtements antireflets et protecteurs. |
Découvrez comment les revêtements PVD peuvent optimiser vos applications. contactez-nous dès aujourd'hui pour obtenir des conseils d'experts !