Le dépôt physique en phase vapeur (PVD) est une technique largement utilisée pour déposer des films minces, en particulier dans les secteurs de la fabrication de pointe et de l'électronique. Le processus implique le transfert de matériau d'une source (cible) vers un substrat dans un environnement sous vide, où le matériau est vaporisé puis condensé sur le substrat pour former un film mince. Le PVD est très apprécié pour sa capacité à produire des films précis, uniformes et de haute qualité aux propriétés contrôlées. Les principes du PVD s'articulent autour de trois composants principaux : la source, le processus de transport et le substrat. Chacun de ces composants joue un rôle essentiel dans la détermination de la qualité, de la structure et de la fonctionnalité du film déposé. De plus, les interactions entre le matériau et le substrat, ainsi que les paramètres de dépôt, influencent le mode de croissance et les propriétés finales du film mince.
Points clés expliqués :
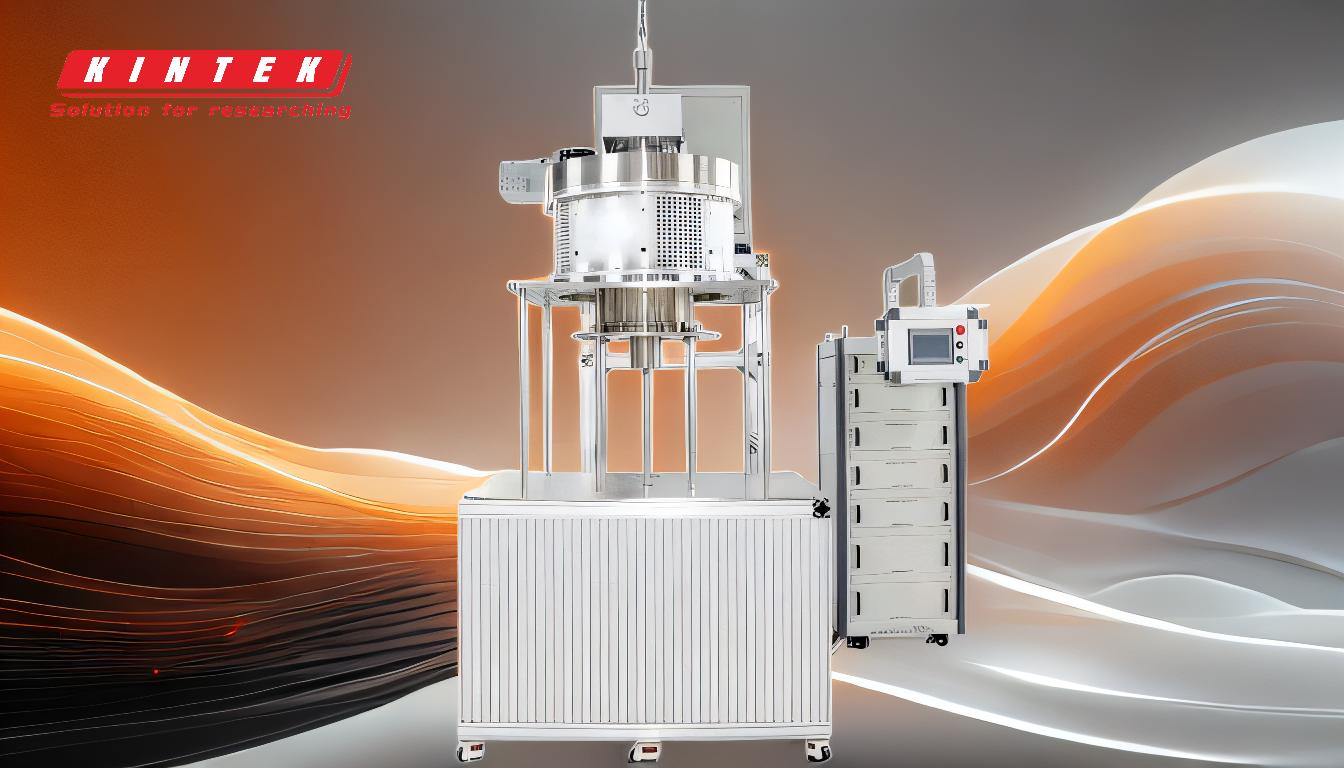
-
Composants du PVD:
- Source (Cible): Le matériau à déposer est typiquement sous forme solide, comme une cible métallique ou céramique. La source est vaporisée à l'aide de techniques telles que la pulvérisation cathodique, l'évaporation ou la décharge en arc.
- Processus de transport: Le matériau vaporisé est transporté dans un environnement sous vide ou basse pression jusqu'au substrat. Cette étape garantit une contamination minimale et un contrôle précis du processus de dépôt.
- Substrat: La surface sur laquelle le film mince est déposé. Les propriétés du substrat, telles que la température, la rugosité de la surface et la composition chimique, influencent l'adhérence, la structure et les performances du film.
-
Techniques de vaporisation:
- Pulvérisation: Une méthode PVD courante dans laquelle des ions à haute énergie bombardent la cible, éjectant des atomes ou des molécules qui se déposent ensuite sur le substrat. Cette technique est connue pour produire des films très uniformes et denses.
- Évaporation: Le matériau cible est chauffé jusqu'à son point de vaporisation, souvent à l'aide d'un faisceau d'électrons ou d'un chauffage résistif. La matière vaporisée se condense alors sur le substrat. Cette méthode convient aux matériaux à bas points de fusion.
- Arc-PVD: Un arc électrique est utilisé pour vaporiser le matériau cible. Cette méthode est particulièrement efficace pour déposer des revêtements durs et est largement utilisée dans les applications industrielles.
-
Modes de croissance des couches minces:
- Adsorption: L'étape initiale où le matériau vaporisé adhère à la surface du substrat.
- Diffusion superficielle: Les atomes ou molécules adsorbés migrent à travers la surface du substrat pour trouver des positions stables.
- Nucléation: De petits amas d'atomes ou de molécules se forment, qui se transforment ensuite en îlots plus grands et finissent par fusionner en un film continu.
-
Influence des paramètres de dépôt:
- Température du substrat: Des températures plus élevées peuvent améliorer la diffusion en surface et la qualité du film, mais une chaleur excessive peut entraîner des réactions ou des défauts indésirables.
- Taux de dépôt: Des taux de dépôt contrôlés garantissent une épaisseur de film uniforme et minimisent les défauts tels que les trous d'épingle ou les vides.
- Pression et environnement: L'environnement sous vide ou basse pression réduit la contamination et permet un contrôle précis du processus de dépôt.
-
Traitements post-dépôt:
- Recuit: Le traitement thermique peut améliorer la cristallinité, l'adhérence et les propriétés mécaniques du film.
- Analyse et optimisation: Le film déposé est analysé pour des propriétés telles que l'épaisseur, l'uniformité et la composition. Ces commentaires sont utilisés pour affiner le processus de dépôt pour les analyses futures.
-
Applications du PVD:
- Le PVD est utilisé dans un large éventail d'industries, notamment l'électronique (par exemple, les dispositifs semi-conducteurs, les revêtements optiques), l'aérospatiale (par exemple, les revêtements protecteurs) et les dispositifs médicaux (par exemple, les revêtements biocompatibles).
- La capacité de déposer des films précis et uniformes rend le PVD idéal pour les dispositifs avancés à couches minces, tels que les cellules solaires, les capteurs et les systèmes microélectromécaniques (MEMS).
En comprenant ces principes, les acheteurs d'équipements et de consommables peuvent prendre des décisions éclairées sur les matériaux, les processus et les paramètres requis pour des applications spécifiques. Ces connaissances garantissent la sélection des équipements et consommables PVD appropriés pour obtenir les propriétés et les performances souhaitées du film.
Tableau récapitulatif :
Aspect | Détails |
---|---|
Composants du PVD | Source (cible), processus de transport, substrat |
Techniques de vaporisation | Pulvérisation, évaporation, Arc-PVD |
Modes de croissance des couches minces | Adsorption, diffusion en surface, nucléation |
Paramètres de dépôt | Température du substrat, taux de dépôt, pression et environnement |
Traitements post-dépôt | Recuit, analyse et optimisation |
Applications | Electronique, aérospatiale, dispositifs médicaux, cellules solaires, MEMS |
Découvrez comment le PVD peut améliorer vos applications de couches minces : contactez nos experts dès aujourd'hui pour des solutions sur mesure !