La pulvérisation magnétron est une technique largement utilisée pour le dépôt de couches minces, offrant des avantages tels que des taux de dépôt élevés, un contrôle précis et une grande polyvalence.Cependant, elle est également confrontée à plusieurs défis, notamment les limites de la surface de revêtement effective, la faible force d'adhérence, les coûts élevés du système et les problèmes liés à l'uniformité du dépôt et au chauffage du substrat.Ces problèmes peuvent affecter la qualité et l'applicabilité des films produits, en particulier pour les applications à grande échelle ou sensibles à la température.Malgré ces difficultés, les recherches et les progrès en cours continuent d'améliorer la technique, ce qui la rend adaptée à une large gamme d'applications dans les domaines de la microélectronique, des semi-conducteurs et des revêtements décoratifs.
Explication des points clés :
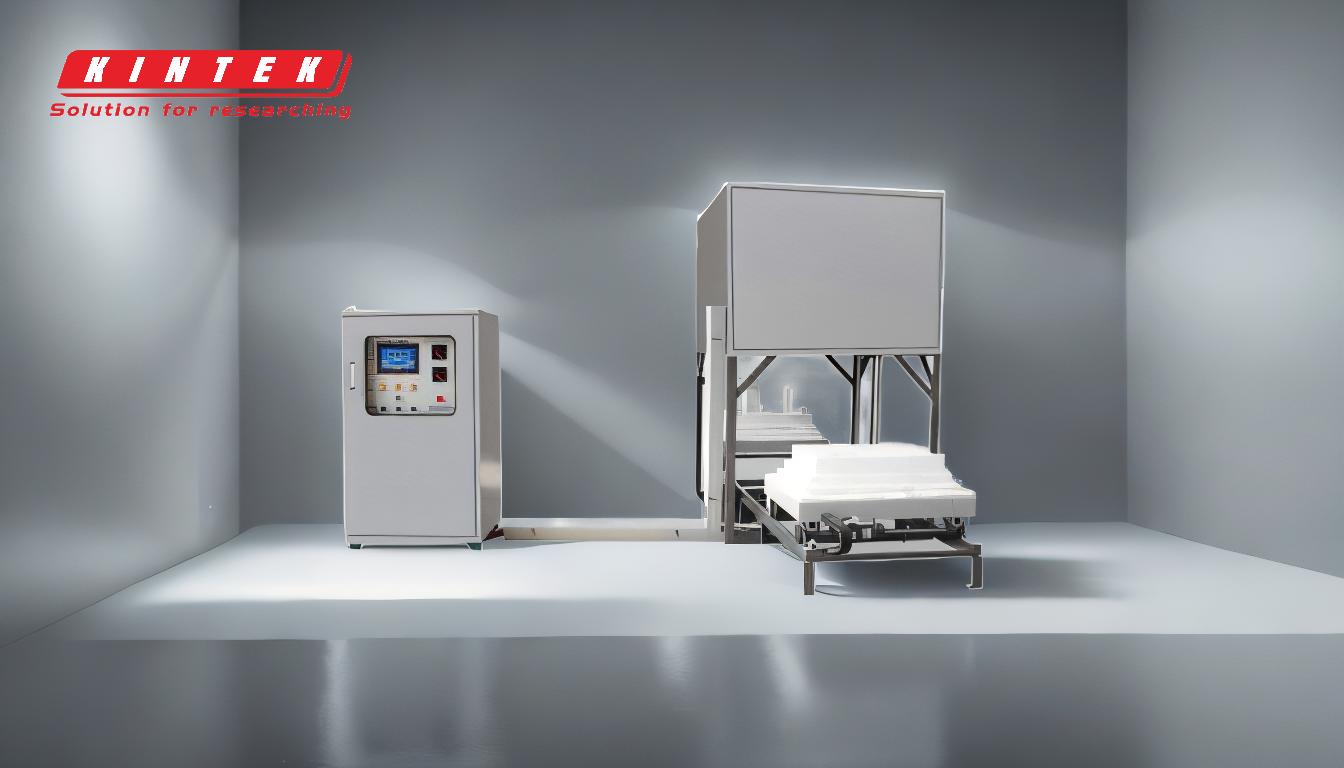
-
Une surface de revêtement efficace limitée:
- La zone de revêtement effective dans la pulvérisation magnétron équilibrée est relativement courte, ce qui limite la taille géométrique des pièces qui peuvent être revêtues.La concentration du plasma diminue rapidement au-delà de 60 mm de la surface de la cible, ce qui limite le placement des pièces.Cela peut constituer un inconvénient important pour les applications à grande échelle ou pour le revêtement de géométries complexes.
-
Force d'adhérence et qualité du film médiocres:
- L'énergie des particules cibles volantes lors de la pulvérisation magnétron est souvent faible, ce qui entraîne une faible force d'adhérence entre le film et le substrat.Il peut en résulter la formation de structures colonnaires poreuses et rugueuses, susceptibles de compromettre les propriétés mécaniques et fonctionnelles du film.L'augmentation de la température de la pièce peut améliorer les propriétés du film, mais cette approche n'est pas réalisable pour les matériaux qui ne supportent pas les températures élevées.
-
Coût et complexité élevés du système:
- Les systèmes de pulvérisation magnétron sont généralement coûteux et complexes à utiliser.L'investissement initial élevé et les coûts de maintenance peuvent constituer un obstacle pour les opérations à petite échelle ou les installations de recherche.En outre, la complexité du système exige un personnel qualifié pour le fonctionnement et le dépannage.
-
Questions relatives au chauffage du substrat:
- Le procédé peut provoquer un échauffement important du substrat en raison de l'énergie du matériau cible.Cela peut être problématique pour les matériaux sensibles à la température ou pour les applications nécessitant un contrôle précis de la température.L'échauffement du substrat peut également entraîner des contraintes et des déformations thermiques, ce qui affecte la qualité du film déposé.
-
Vitesse de dépôt et directionnalité:
- Alors que la pulvérisation magnétron offre des taux de dépôt élevés pour de nombreux matériaux, elle peut être moins efficace pour les diélectriques, qui peuvent avoir des taux de dépôt plus faibles.En outre, la technique souffre souvent d'une faible directionnalité, qui peut être améliorée par la géométrie du système, mais qui reste un défi pour obtenir des revêtements uniformes sur des substrats complexes ou tridimensionnels.
-
Homogénéité et applicabilité sur de grandes surfaces:
- L'obtention d'une homogénéité dans le film déposé peut s'avérer difficile, en particulier pour les grandes surfaces.La technique peut avoir du mal à fournir une épaisseur et une composition uniformes sur l'ensemble du substrat, ce qui est essentiel pour les applications exigeant des propriétés de film constantes.Cette limitation rend la pulvérisation magnétron moins adaptée à certaines applications à grande échelle ou de haute précision.
-
Procédés de post-revêtement à haute température:
- Certaines applications nécessitent des procédés à haute température après le revêtement afin d'améliorer les propriétés du film, telles que l'adhérence et la densité.Cependant, ces traitements à haute température peuvent être désavantageux pour les matériaux sensibles à la chaleur ou pour les applications où le budget thermique est un problème.
-
Avantages et améliorations continues:
- Malgré ces défis, la pulvérisation magnétron reste une technique très efficace et polyvalente.Elle offre des taux de dépôt élevés, une couverture complète des matériaux, une grande pureté des films et la possibilité d'opérer à basse température.Les recherches en cours et les avancées technologiques continuent de remédier à de nombreuses limitations, ce qui en fait un outil précieux pour la préparation de couches minces dans diverses industries.
En résumé, si la pulvérisation magnétron est une technique puissante et polyvalente pour le dépôt de couches minces, elle n'est pas sans poser de problèmes.Il est essentiel de comprendre ces limites pour optimiser le processus et étendre son applicabilité à une gamme plus large de matériaux et d'applications.
Tableau récapitulatif :
Défi | Description |
---|---|
Zone de revêtement efficace limitée | La concentration de plasma diminue au-delà de 60 mm, ce qui limite les applications à grande échelle. |
Faible force d'adhérence | La faible énergie des particules cibles conduit à des films poreux et rugueux avec une faible adhérence. |
Coût et complexité élevés du système | Investissement initial et maintenance coûteux ; nécessite un personnel qualifié. |
Problèmes de chauffage du substrat | Le matériau cible énergétique provoque un échauffement, ce qui est problématique pour les matériaux sensibles à la température. |
Vitesse de dépôt et directionnalité | Faible directionnalité et taux plus lent pour les diélectriques ; défis pour les substrats complexes. |
Homogénéité et applicabilité sur de grandes surfaces | Difficulté à obtenir une épaisseur et une composition uniformes sur de grandes surfaces. |
Procédés de post-revêtement à haute température | Les traitements thermiques peuvent endommager les matériaux sensibles à la température. |
Améliorations en cours | La recherche continue de s'attaquer aux limites, en améliorant la polyvalence et l'efficacité. |
Découvrez comment surmonter les défis de la pulvérisation magnétron et optimiser vos processus de couches minces. contactez nos experts dès aujourd'hui !