Le dépôt physique en phase vapeur (PVD) et le dépôt chimique en phase vapeur (CVD) sont deux techniques largement utilisées pour déposer des couches minces sur des substrats.Le dépôt physique en phase vapeur repose sur des processus physiques, tels que l'évaporation ou la pulvérisation, pour transformer un matériau solide en une vapeur qui se condense ensuite sur le substrat.En revanche, le dépôt en phase vapeur utilise des réactions chimiques impliquant des précurseurs gazeux pour former un film solide sur le substrat.Alors que le PVD fonctionne à des températures plus basses et évite les sous-produits corrosifs, le CVD permet un revêtement uniforme de géométries complexes et des taux de dépôt plus élevés.Les deux méthodes sont essentielles dans des secteurs tels que les semi-conducteurs, l'optique et les revêtements, et offrent des avantages uniques en fonction de l'application.
Explication des points clés :
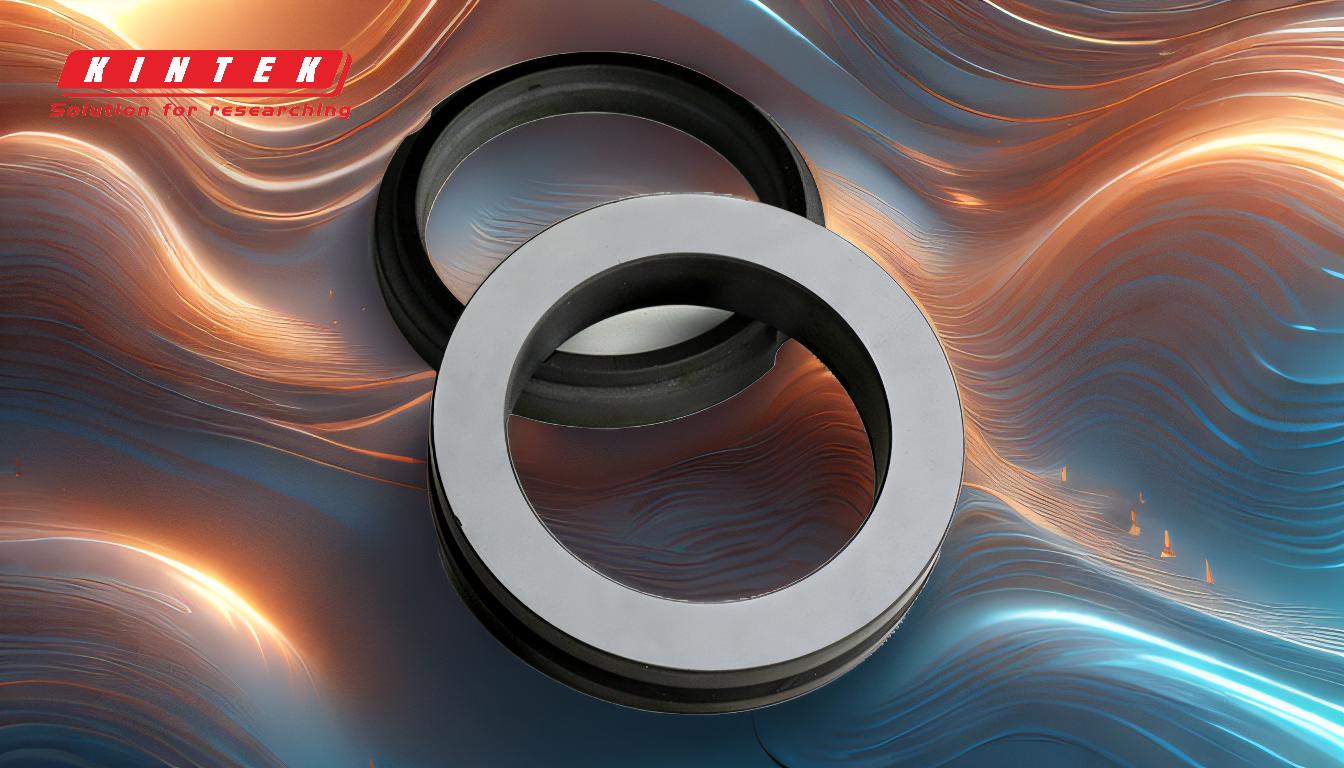
-
Définition et principes de base:
- PVD:Le dépôt physique en phase vapeur consiste à transformer un matériau solide en vapeur par des moyens physiques (chauffage, pulvérisation).La vapeur se condense ensuite sur le substrat pour former un film mince.
- CVD:Le dépôt chimique en phase vapeur fait appel à des précurseurs gazeux qui réagissent chimiquement ou se décomposent à la surface du substrat pour former un film solide.Ce procédé repose sur des réactions chimiques plutôt que sur des transformations physiques.
-
Mécanismes du processus:
-
PVD:
- Le matériau solide est chauffé au-dessus de son point de fusion ou bombardé d'ions (pulvérisation) pour générer de la vapeur.
- Les atomes ou molécules vaporisés se déplacent vers le substrat et se déposent sous la forme d'un film mince.
- Les méthodes courantes de dépôt en phase vapeur comprennent l'évaporation, la pulvérisation, le faisceau d'électrons et l'explosion d'un fil.
-
CVD:
- Des précurseurs gazeux sont introduits dans une chambre de réaction.
- Les gaz réagissent chimiquement ou se décomposent à la surface du substrat chauffé, formant un film solide.
- Le dépôt en phase vapeur peut être activé thermiquement ou renforcé par un plasma pour améliorer l'efficacité de la réaction.
-
PVD:
-
Principales différences:
-
État des matériaux:
- Le PVD utilise des matériaux solides qui sont vaporisés physiquement.
- Le CVD utilise des précurseurs gazeux qui se transforment chimiquement en un film solide.
-
Ligne de mire:
- Le dépôt en phase vapeur (PVD) nécessite une ligne de visée directe entre le matériau cible et le substrat, ce qui limite sa capacité à revêtir uniformément des géométries complexes.
- Le dépôt en phase vapeur ne nécessite pas de ligne de visée, ce qui permet de revêtir uniformément des formes complexes et plusieurs pièces simultanément.
-
Température et sous-produits:
- Le PVD fonctionne à des températures plus basses et ne produit pas de sous-produits corrosifs.
- La CVD nécessite souvent des températures élevées, ce qui peut entraîner des sous-produits gazeux corrosifs et des impuretés potentielles dans le film.
-
État des matériaux:
-
Avantages et limites:
-
PVD:
- Avantages :Températures de dépôt plus basses, pas de sous-produits corrosifs, efficacité élevée de l'utilisation des matériaux (par exemple, l'EBPVD offre des taux de dépôt élevés).
- Limites :Limité au dépôt en visibilité directe, taux de dépôt inférieurs à ceux du CVD.
-
CVD:
- Avantages :Revêtement uniforme de géométries complexes, taux de dépôt plus élevés, possibilité de revêtir plusieurs pièces en une seule réaction.
- Limites :Températures élevées et sous-produits corrosifs, risque d'impuretés dans le film.
-
PVD:
-
Applications:
-
PVD:
- Couramment utilisé pour les revêtements décoratifs, les revêtements résistants à l'usure et les dispositifs semi-conducteurs.
- Les exemples incluent les revêtements de nitrure de titane sur les outils de coupe et les revêtements d'aluminium sur les matériaux d'emballage.
-
CVD:
- Largement utilisé dans la fabrication de semi-conducteurs, les revêtements optiques et les revêtements de protection.
- Les exemples incluent les films de dioxyde de silicium et de nitrure de silicium en microélectronique et les revêtements de carbone de type diamant.
-
PVD:
-
Utilisation des matériaux et efficacité:
- PVD:Efficacité élevée de l'utilisation des matériaux, en particulier dans des méthodes telles que l'EBPVD, où les vitesses de dépôt vont de 0,1 à 100 μm/min.
- CVD:Efficace pour le revêtement de formes complexes et de pièces multiples simultanément, mais peut impliquer des coûts de matériaux plus élevés en raison de l'utilisation de précurseurs gazeux.
-
Considérations relatives à l'environnement et à la sécurité:
- PVD:Généralement plus sûr et plus respectueux de l'environnement en raison des températures plus basses et de l'absence de sous-produits corrosifs.
- CVD:Il faut manipuler avec précaution les gaz réactifs et gérer les sous-produits corrosifs, ce qui peut poser des problèmes de sécurité et d'environnement.
En comprenant ces points clés, un acheteur d'équipement ou de consommables peut décider en toute connaissance de cause si le dépôt en phase vapeur par procédé physique (PVD) ou le dépôt en phase vapeur par procédé chimique (CVD) convient mieux à son application spécifique, en tenant compte de facteurs tels que la géométrie du substrat, la vitesse de dépôt, la sensibilité à la température et l'impact environnemental.
Tableau récapitulatif :
Aspect | PVD | CVD |
---|---|---|
État des matériaux | Matériaux solides vaporisés physiquement | Précurseurs gazeux transformés chimiquement en un film solide |
Ligne de visée | Nécessite une ligne de vue directe ; limité pour les géométries complexes | Pas de ligne de visée requise ; revêtement uniforme de formes complexes |
Température | Températures basses ; pas de sous-produits corrosifs | Températures élevées ; sous-produits corrosifs potentiels |
Taux de dépôt | Plus faible que pour les MCV | Taux de dépôt plus élevés |
Applications | Revêtements décoratifs, revêtements résistants à l'usure, semi-conducteurs | Semi-conducteurs, revêtements optiques, revêtements de protection |
Impact sur l'environnement | Plus sûr et plus respectueux de l'environnement | Nécessite une manipulation prudente des gaz réactifs et des sous-produits |
Vous avez besoin d'aide pour choisir entre le dépôt en phase vapeur (PVD) et le dépôt en phase vapeur (CVD) pour votre application ? Contactez nos experts dès aujourd'hui pour des conseils personnalisés !