Le dépôt physique en phase vapeur (PVD) est une technologie polyvalente et largement utilisée dans divers secteurs, notamment la fabrication, les produits décoratifs et l'amélioration des outils.Le dépôt physique en phase vapeur consiste à déposer des couches minces sur des substrats par la vaporisation de matériaux sources dans un environnement sous vide.Ce procédé permet d'améliorer les caractéristiques des produits telles que la durabilité, la résistance à l'usure et l'attrait esthétique, souvent à moindre coût et avec un impact minimal sur l'environnement.Le dépôt en phase vapeur est particulièrement utile dans des applications telles que les revêtements décoratifs durables, les revêtements performants et les alternatives au chromage traditionnel.Le processus peut être réalisé par des méthodes telles que l'évaporation thermique, où les matériaux sont chauffés pour former une vapeur qui se condense sur le substrat, créant ainsi un revêtement de haute qualité.
Explication des points clés :
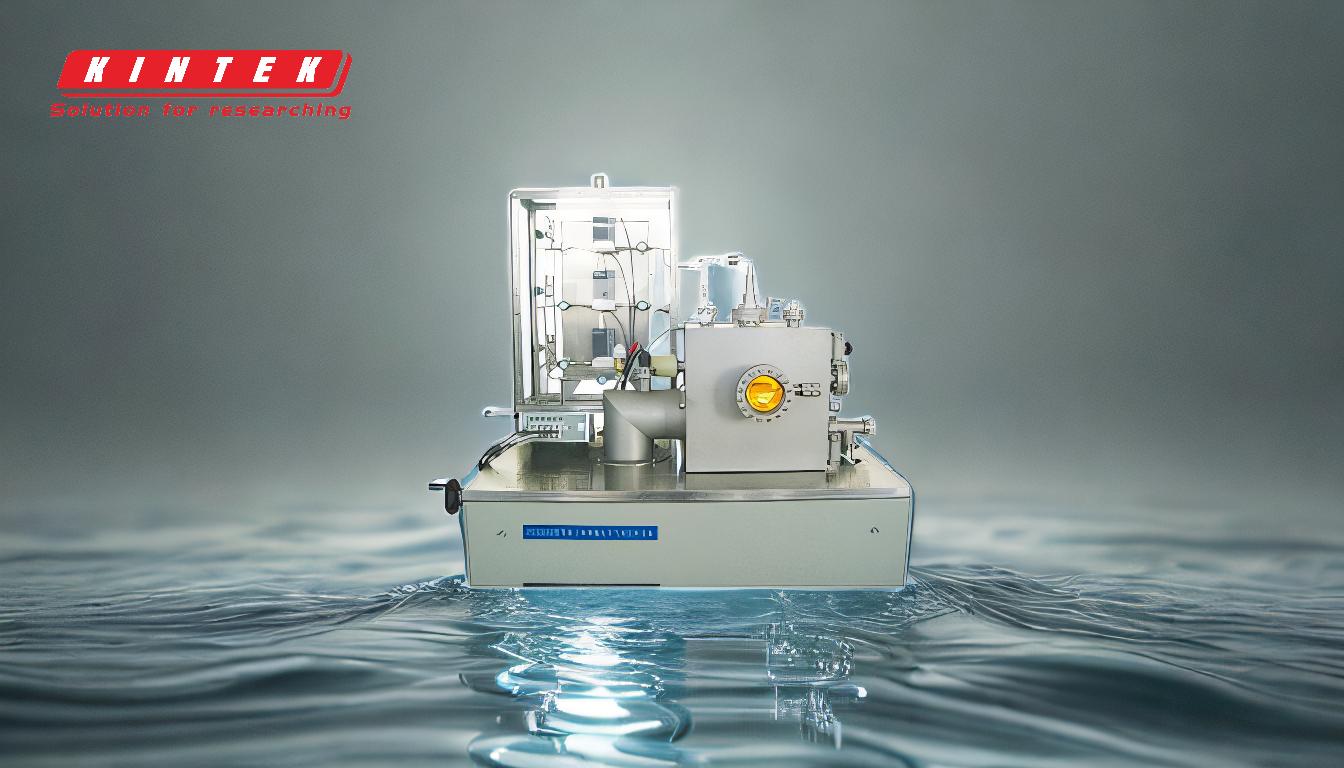
-
Qu'est-ce que le PVD ?
- Le dépôt physique en phase vapeur (PVD) est un procédé de revêtement par lequel des matériaux sont vaporisés sous vide, puis déposés sur un substrat pour former un film mince.Cette technologie est largement utilisée pour améliorer les propriétés des produits, telles que la résistance à l'usure, la durabilité et l'attrait esthétique.
-
Applications du PVD :
-
Le dépôt en phase vapeur (PVD) est utilisé dans une variété d'industries, y compris :
- Bijoux et produits décoratifs : Améliore l'apparence et la durabilité d'articles tels que les bijoux, la quincaillerie de porte et les accessoires de cuisine.
- Outils industriels : Améliore la résistance à l'usure des outils de coupe et réduit l'adhérence entre les outils et les pièces à usiner, en particulier dans le travail des métaux et le moulage par injection de plastique.
- Revêtements de performance : Comprend les revêtements de carbone de type diamant et les alternatives au chrome PVD, qui sont utilisés pour leur durabilité et leurs avantages environnementaux.
-
Le dépôt en phase vapeur (PVD) est utilisé dans une variété d'industries, y compris :
-
Avantages des revêtements PVD :
- Rentabilité : Les revêtements PVD sont souvent plus abordables que les méthodes de placage traditionnelles comme le chrome.
- Impact sur l'environnement : Les procédés PVD sont généralement plus respectueux de l'environnement, car ils produisent moins de sous-produits nocifs.
- Propriétés améliorées : Les revêtements améliorent la dureté, la résistance à l'usure et à la corrosion, prolongeant ainsi la durée de vie des produits.
-
Techniques PVD :
-
Évaporation thermique :
L'une des méthodes PVD les plus courantes, dans laquelle le matériau source est chauffé sous vide jusqu'à ce qu'il se vaporise.La vapeur se condense ensuite sur le substrat pour former un revêtement.Les méthodes de chauffage comprennent
- le filament chaud
- Résistance électrique
- Faisceau d'électrons ou faisceau laser
- Arc électrique
- Environnement sous vide poussé : Le processus se déroule sous vide afin de minimiser les interférences des atomes ou molécules de gaz, ce qui garantit un revêtement de haute qualité.
-
Évaporation thermique :
L'une des méthodes PVD les plus courantes, dans laquelle le matériau source est chauffé sous vide jusqu'à ce qu'il se vaporise.La vapeur se condense ensuite sur le substrat pour former un revêtement.Les méthodes de chauffage comprennent
-
Industries et produits utilisant le PVD :
-
Le PVD est utilisé dans la fabrication de :
- Bijoux : Pour les revêtements décoratifs et protecteurs.
- Quincaillerie : Les accessoires de portes et de fenêtres, la quincaillerie de cuisine et de salle de bains, par exemple.
- Lampes et fournitures marines : Pour une durabilité et un aspect accrus.
- Artisanat et articles décoratifs : Améliorer l'attrait esthétique et la longévité.
-
Le PVD est utilisé dans la fabrication de :
-
Avantages par rapport aux méthodes traditionnelles :
- Le dépôt en phase vapeur (PVD) offre une alternative plus durable et plus efficace aux méthodes de revêtement traditionnelles telles que le chromage.Il offre des caractéristiques de performance similaires ou supérieures tout en réduisant l'impact sur l'environnement et les coûts.
En résumé, le dépôt en phase vapeur (PVD) est une technologie très efficace et polyvalente utilisée dans de nombreuses industries pour améliorer les performances et l'apparence des produits.Ses applications vont des revêtements décoratifs à l'amélioration des outils industriels, offrant des solutions rentables, durables et respectueuses de l'environnement.
Tableau récapitulatif :
Aspect | Détails |
---|---|
Qu'est-ce que le PVD ? | Procédé de revêtement utilisant des matériaux vaporisés sous vide pour former des films minces. |
Applications | Bijouterie, outils industriels, revêtements performants et produits décoratifs. |
Avantages | Rentabilité, respect de l'environnement, amélioration de la durabilité et de la résistance à l'usure. |
Techniques | Évaporation thermique, environnement sous vide poussé et diverses méthodes de chauffage. |
Industries | Bijouterie, quincaillerie, fournitures marines, artisanat et articles de décoration. |
Avantages | Durable, efficace et supérieur au chromage traditionnel. |
Transformez vos produits avec la technologie PVD. contactez nos experts dès aujourd'hui pour des solutions sur mesure !