Le frittage à l'hydrogène est un procédé spécialisé dans lequel des matériaux, généralement sous forme de poudre, sont chauffés dans une atmosphère riche en hydrogène pour former une masse solide sans atteindre le point de fusion du matériau.Ce procédé est particulièrement avantageux pour produire des matériaux denses et de haute qualité, dotés de propriétés mécaniques supérieures.Le frittage à l'hydrogène empêche l'oxydation, réduit les impuretés et améliore la qualité globale du produit final.Il est largement utilisé dans les industries nécessitant des matériaux de haute performance, telles que l'aérospatiale, l'automobile et l'électronique, en raison de sa capacité à produire des pièces présentant d'excellents états de surface et d'excellentes propriétés mécaniques.
Explication des points clés :
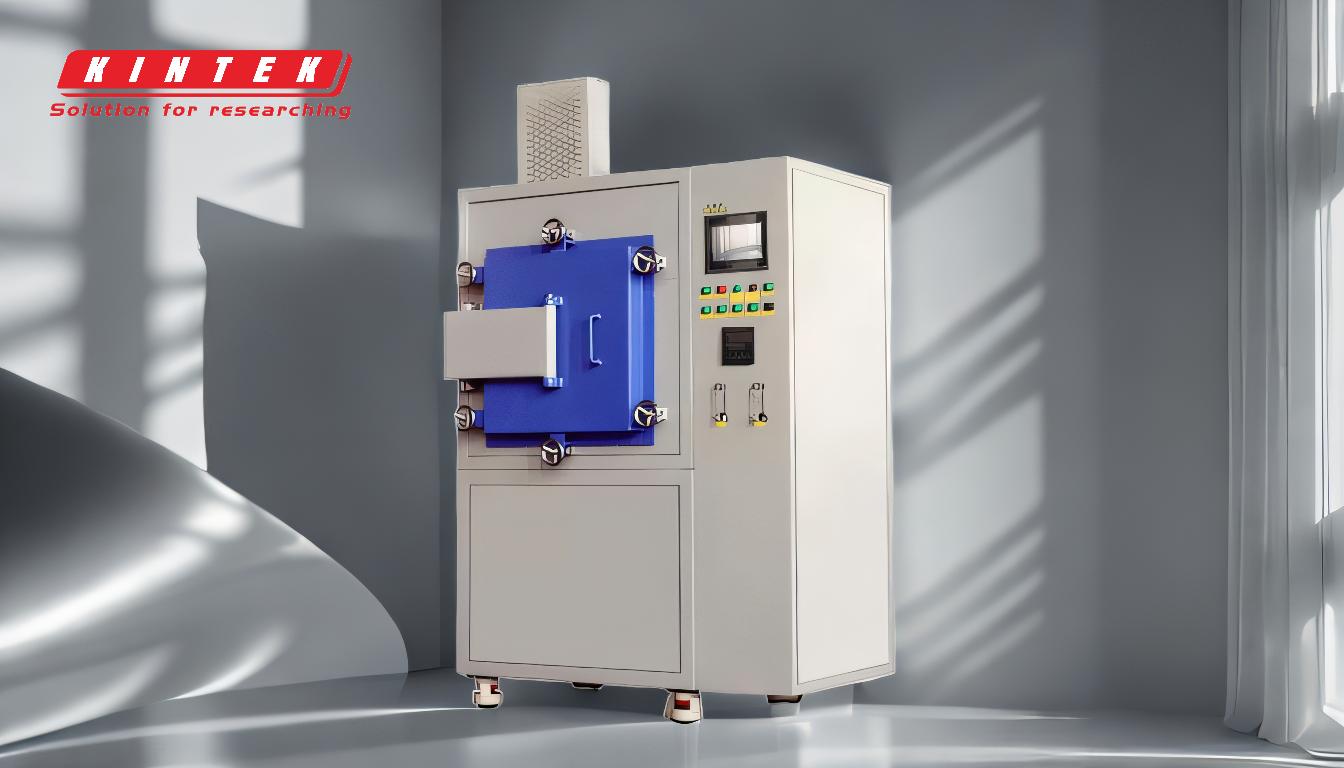
-
Définition du frittage à l'hydrogène:
- Le frittage à l'hydrogène consiste à chauffer des matériaux en poudre dans une atmosphère riche en hydrogène (hydrogène pur, mélange hydrogène/azote ou ammoniac dissocié) pour former une masse solide.
- Ce procédé est particulièrement efficace pour les matériaux tels que le tungstène, le molybdène et l'acier inoxydable, pour lesquels une pureté et une densité élevées sont essentielles.
-
Rôle de l'hydrogène dans le processus de frittage:
- Prévention de l'oxydation:L'hydrogène agit comme un agent réducteur, empêchant l'oxydation des poudres métalliques, ce qui peut conduire à de mauvais résultats de frittage.
- Réduction des impuretés:L'hydrogène réagit avec les oxydes de surface et les impuretés telles que la silice, les éliminant efficacement de l'alliage.Ce phénomène est crucial pour obtenir des matériaux de haute densité dotés de propriétés mécaniques supérieures.
- Amélioration des réactions d'oxydoréduction:L'atmosphère d'hydrogène facilite les réactions d'oxydoréduction, ce qui permet d'éliminer les impuretés et d'améliorer la qualité globale du produit fritté.
-
Avantages de l'utilisation de l'hydrogène pour le frittage:
- Haute pureté:L'hydrogène utilisé pour le frittage est généralement d'une très grande pureté (>99,9995%), ce qui le rend adapté à une large gamme de matériaux, y compris ceux utilisés dans des applications critiques.
- Propriétés mécaniques améliorées:La réduction des impuretés et la prévention de l'oxydation permettent d'obtenir des pièces frittées présentant des qualités mécaniques supérieures, telles qu'une résistance et une durabilité accrues.
- Finition de surface:L'utilisation de l'hydrogène permet d'obtenir une finition de surface brillante et propre, ce qui est souvent souhaitable pour les produits finis.
- Avantages pour l'environnement et la sécurité:Le frittage à l'hydrogène réduit la pollution de l'air et minimise les risques pour le personnel, ce qui en fait une option plus sûre et plus respectueuse de l'environnement que les autres méthodes de frittage.
-
Four de frittage à l'hydrogène:
- Conception et composants:Un four de frittage à l'hydrogène utilise généralement du molybdène ou du fil de tungstène comme élément chauffant et du molybdène comme bouclier thermique.Le corps du four est généralement en acier inoxydable ou en acier au carbone.
- Fonctionnement:Le four fonctionne sous atmosphère d'hydrogène, ce qui est essentiel pour le frittage à haute température de matériaux tels que le tungstène et le molybdène.L'atmosphère d'hydrogène garantit que les matériaux sont protégés de l'oxydation et d'autres contaminants pendant le processus de frittage.
-
Applications du frittage à l'hydrogène:
- Industries aérospatiale et automobile:Le frittage à l'hydrogène est utilisé pour produire des composants de haute performance qui requièrent des propriétés mécaniques et une durabilité exceptionnelles.
- L'électronique:Le procédé est également utilisé dans l'industrie électronique pour fabriquer des composants d'une grande précision et d'une grande fiabilité.
- Dispositifs médicaux:Le frittage à l'hydrogène est utilisé dans la production de dispositifs médicaux où la pureté et la biocompatibilité sont essentielles.
-
Comparaison avec d'autres méthodes de frittage:
- Avantages par rapport au frittage à l'air:Contrairement au frittage à l'air, qui peut entraîner une oxydation et une contamination, le frittage à l'hydrogène fournit une atmosphère propre et réductrice qui améliore la qualité du produit final.
- Efficacité en termes de coûts:Bien que le frittage à l'hydrogène nécessite un équipement spécialisé, le processus peut permettre de réaliser des économies substantielles à long terme grâce à la réduction des déchets de matériaux et à l'amélioration de la qualité des produits.
En résumé, le frittage à l'hydrogène est un processus très efficace pour produire des matériaux denses et de haute qualité, dotés de propriétés mécaniques supérieures.L'utilisation de l'hydrogène empêche l'oxydation, réduit les impuretés et améliore la qualité globale du produit fritté, ce qui en fait un choix idéal pour les industries qui exigent des matériaux de haute performance.
Tableau récapitulatif :
Aspect | Détails |
---|---|
Procédé | Chauffage de matériaux en poudre dans une atmosphère riche en hydrogène pour former une masse solide. |
Principaux avantages | Prévient l'oxydation, réduit les impuretés, améliore les propriétés mécaniques. |
Matériaux | Tungstène, molybdène, acier inoxydable et autres alliages de haute pureté. |
Applications | Aérospatiale, automobile, électronique et dispositifs médicaux. |
Avantages par rapport à l'air | Processus plus propre, qualité supérieure et rentabilité à long terme. |
Découvrez comment le frittage à l'hydrogène peut améliorer la qualité de vos matériaux. contactez nos experts dès aujourd'hui !