Le moulage du caoutchouc est un procédé de fabrication polyvalent utilisé pour façonner le caoutchouc non vulcanisé en produits fonctionnels en le chauffant et en le remodelant dans une cavité métallique.Les trois principaux types de moulage du caoutchouc sont le moulage par injection, le moulage par compression et le moulage par transfert, chacun ayant sa propre approche et ses propres applications.Ces procédés font partie d'un processus plus large de fabrication du caoutchouc qui comprend le compoundage, l'extrusion, le calandrage, la vulcanisation, le traitement du latex et la production de polyuréthane.Il est essentiel de comprendre les étapes et les techniques spécifiques du moulage du caoutchouc pour fabriquer des produits en caoutchouc de haute qualité adaptés à diverses industries.
Explication des points clés :
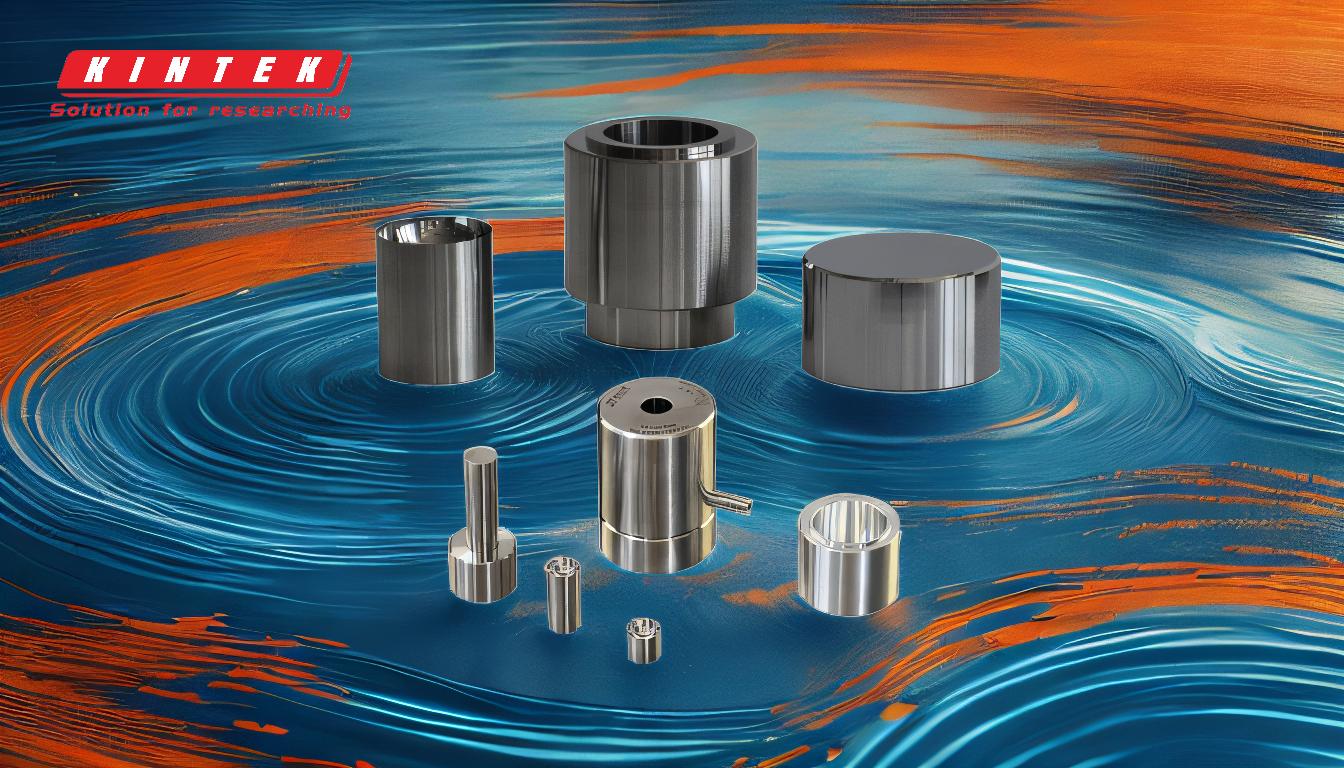
-
Vue d'ensemble du moulage du caoutchouc
- Le moulage du caoutchouc est un processus qui transforme le caoutchouc non vulcanisé en produits utilisables en le chauffant et en le façonnant dans un moule métallique.
- Il s'agit de l'une des nombreuses méthodes de fabrication de produits en caoutchouc, avec l'extrusion, le laminage de feuilles découpées, la vulcanisation ouverte et la vulcanisation continue.
- Ce procédé est largement utilisé dans des secteurs tels que l'automobile, l'aérospatiale, le médical et les biens de consommation, en raison de sa capacité à produire des composants durables, flexibles et précis.
-
Types de procédés de moulage du caoutchouc
-
Moulage par injection:
- Le caoutchouc non vulcanisé est injecté sous haute pression dans une cavité de moule chauffée.
- Idéal pour la production en grande quantité de formes complexes avec des tolérances serrées.
- Couramment utilisé pour les joints, les garnitures et les joints toriques.
-
Moulage par compression:
- Le caoutchouc pré-dosé est placé dans une cavité de moule ouverte, qui est ensuite fermée et chauffée sous pression.
- Convient aux grandes pièces simples et aux volumes de production faibles à moyens.
- Souvent utilisé pour les composants automobiles tels que les bagues et les supports.
-
Moulage par transfert:
- Le caoutchouc est transféré d'une chambre dans une cavité de moule fermée à l'aide d'un piston.
- Combine des éléments du moulage par injection et du moulage par compression, offrant un équilibre entre précision et simplicité.
- Il est souvent utilisé pour des pièces complexes nécessitant une répartition homogène des matériaux.
-
Moulage par injection:
-
Principales étapes du processus de moulage du caoutchouc
-
Préparation du matériau:
- Les composés de caoutchouc sont préparés en mélangeant du caoutchouc brut avec des additifs tels que des charges, des plastifiants et des agents de vulcanisation.
- Cette étape permet de s'assurer que le matériau possède les propriétés souhaitées, telles que l'élasticité, la solidité et la résistance à la chaleur ou aux produits chimiques.
-
Conception et préparation du moule:
- Les moules sont conçus sur mesure en fonction des spécifications du produit.
- Ils sont généralement fabriqués dans des matériaux durables tels que l'acier ou l'aluminium pour résister à des températures et des pressions élevées.
-
Processus de moulage:
- La méthode de moulage choisie (injection, compression ou transfert) est utilisée pour façonner le caoutchouc.
- La chaleur et la pression sont appliquées pour durcir le caoutchouc et le solidifier dans la forme souhaitée.
-
Post-traitement:
- Après le moulage, le produit en caoutchouc peut subir des étapes supplémentaires telles que le rognage, la finition de surface ou l'inspection de la qualité.
- Ces étapes permettent de s'assurer que le produit répond aux spécifications et aux normes de performance requises.
-
Préparation du matériau:
-
Avantages du moulage en caoutchouc
- Polyvalence:Peut produire une large gamme de formes, de tailles et de complexités.
- Durabilité:Les produits en caoutchouc sont résistants à l'usure et aux facteurs environnementaux.
- Rapport coût-efficacité:Convient aussi bien à la production de gros volumes qu'à celle de faibles volumes, selon la méthode utilisée.
- Précision:Garantit une qualité constante et des tolérances serrées, en particulier dans le cas du moulage par injection.
-
Applications du moulage en caoutchouc
- Automobile:Joints, garnitures, amortisseurs de vibrations et tuyaux.
- Médical:Bouchons de seringues, joints et composants de dispositifs médicaux.
- Biens de consommation:Chaussures, poignées et housses de protection.
- Industriel:Joints, garnitures et composants d'isolation des vibrations.
En comprenant le processus de fabrication du moulage du caoutchouc, y compris ses types, ses étapes et ses applications, les acheteurs d'équipements et de consommables peuvent prendre des décisions éclairées sur les méthodes et les matériaux les mieux adaptés à leurs besoins spécifiques.Ces connaissances garantissent la production de produits en caoutchouc de haute qualité qui répondent aux normes industrielles et aux exigences de performance.
Tableau récapitulatif :
Aspect | Détails |
---|---|
Types de moulage | Injection, compression, transfert |
Étapes clés | Préparation des matériaux, conception du moule, processus de moulage, post-traitement |
Avantages | Polyvalence, durabilité, rentabilité, précision |
Applications | Automobile, médical, biens de consommation, industriel |
Découvrez comment le moulage en caoutchouc peut répondre à vos besoins de production. contactez nos experts dès aujourd'hui !