Le procédé de revêtement PVD (Physical Vapor Deposition) est une méthode sophistiquée utilisée pour créer des revêtements minces, durables et fonctionnels sur divers substrats. Il consiste à vaporiser un matériau solide dans un environnement sous vide, à transporter les atomes vaporisés vers le substrat et à les déposer pour former un film mince. Ce procédé permet d'améliorer les propriétés du substrat, telles que la dureté, la résistance à l'usure et à la corrosion, tout en améliorant son aspect esthétique. Le mécanisme du revêtement PVD peut être décomposé en plusieurs étapes clés, notamment le nettoyage, la vaporisation, le transport, la réaction et le dépôt. Chaque étape est essentielle pour garantir la qualité et les performances du revêtement final.
Explication des points clés :
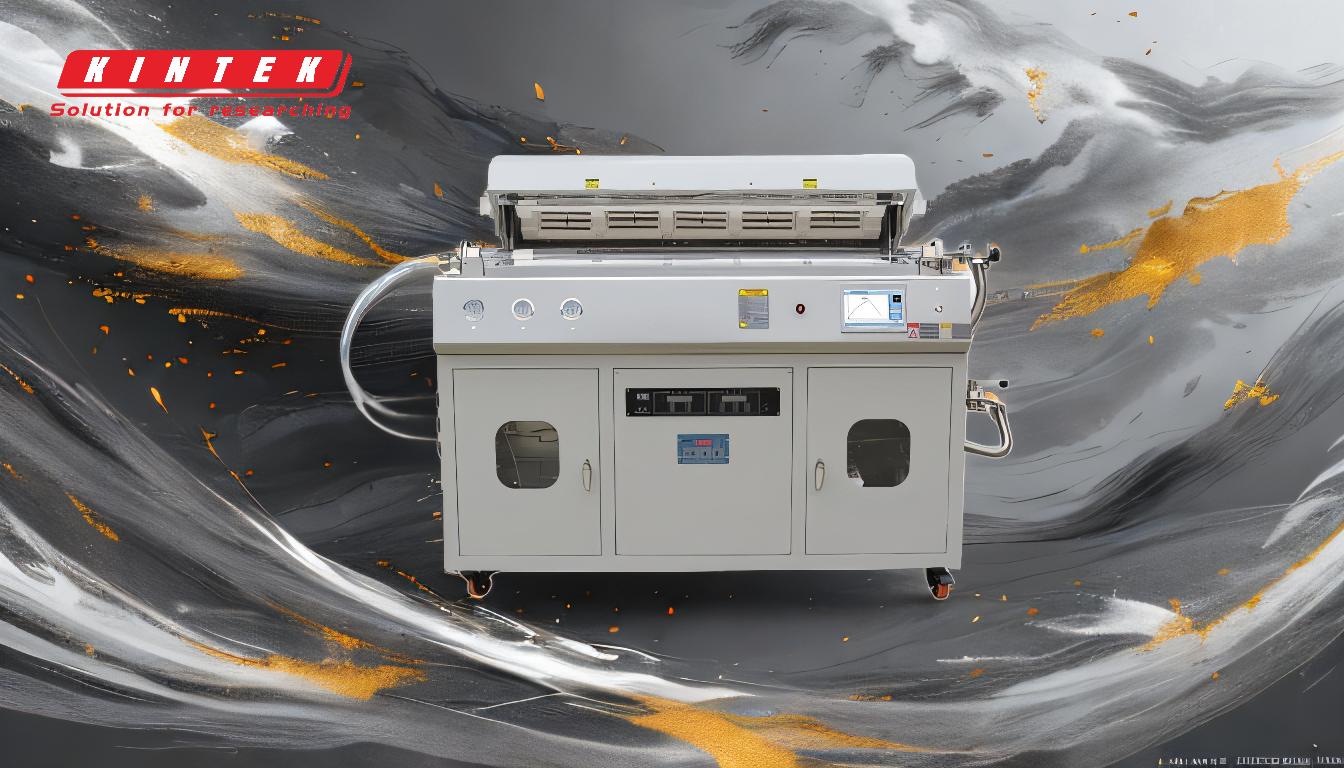
-
Nettoyage et prétraitement du substrat:
- Avant le début du processus de revêtement PVD, le substrat doit être soigneusement nettoyé afin d'éliminer tous les contaminants tels que les huiles, les poussières ou les oxydes. Cette étape est cruciale car toute impureté sur la surface peut avoir un impact négatif sur l'adhérence et la qualité du revêtement.
- Des processus de prétraitement, tels que le nettoyage au plasma ou la gravure, peuvent également être utilisés pour améliorer l'énergie de surface et l'adhérence du revêtement. Cette étape garantit que le revêtement adhérera efficacement au substrat.
-
Création d'un environnement sous vide poussé:
- Le processus de revêtement PVD se déroule dans une chambre à vide, qui est évacuée à une pression extrêmement basse, généralement comprise entre 10^-3 et 10^-9 Torr. Cet environnement sous vide poussé est essentiel pour éviter la contamination par les gaz atmosphériques et pour permettre au matériau vaporisé de se déplacer sans entrave jusqu'au substrat.
- Le vide garantit également que le matériau vaporisé reste propre et pur, ce qui est essentiel pour obtenir des revêtements de haute qualité.
-
Vaporisation du matériau cible:
- Le matériau cible, qui est la source du revêtement, est vaporisé à l'aide de plusieurs techniques, telles que la pulvérisation cathodique, l'évaporation à l'arc ou l'évaporation par faisceau d'électrons. Dans le cas de la pulvérisation, des ions à haute énergie bombardent la cible, délogeant les atomes de sa surface. Dans l'évaporation à l'arc, un arc électrique vaporise le matériau cible, tandis que dans l'évaporation par faisceau d'électrons, un faisceau d'électrons focalisé chauffe et vaporise la cible.
- Le choix de la technique de vaporisation dépend du matériau à revêtir et des propriétés souhaitées du revêtement.
-
Transport des atomes vaporisés:
- Une fois que le matériau cible est vaporisé, les atomes ou les molécules sont transportés à travers la chambre à vide jusqu'au substrat. Ce transport se fait en ligne droite en raison de l'absence de molécules d'air dans l'environnement sous vide.
- La distance entre la cible et le substrat, ainsi que l'énergie des atomes vaporisés, influencent l'uniformité et l'épaisseur du revêtement.
-
Réaction avec des gaz réactifs (en option):
- Pendant la phase de transport, des gaz réactifs tels que l'azote, l'oxygène ou l'acétylène peuvent être introduits dans la chambre à vide. Ces gaz réagissent avec les atomes de métal vaporisés pour former des composés tels que des nitrures, des oxydes ou des carbures métalliques.
- Cette étape de réaction est cruciale pour modifier les propriétés du revêtement. Par exemple, l'ajout d'azote peut entraîner la formation d'un revêtement de nitrure métallique dur et résistant à l'usure.
-
Dépôt et condensation sur le substrat:
- Les atomes ou molécules vaporisés atteignent finalement le substrat, où ils se condensent et forment un film mince et uniforme. Ce dépôt s'effectue atome par atome, ce qui permet d'obtenir un revêtement très contrôlé et précis.
- Le processus de dépôt est influencé par des facteurs tels que la température du substrat, l'énergie des atomes vaporisés et l'angle d'incidence des atomes sur le substrat.
-
Contrôle de la qualité et finition:
- Après le dépôt du revêtement, des mesures de contrôle de la qualité sont prises pour s'assurer que le revêtement répond aux spécifications requises. Il peut s'agir de tester l'épaisseur, l'adhérence, la dureté et d'autres propriétés du revêtement.
- Des procédés de finition, tels que le polissage ou des traitements de surface supplémentaires, peuvent également être appliqués pour améliorer l'aspect ou les performances du revêtement.
-
Avantages environnementaux et opérationnels:
- Le revêtement PVD est considéré comme un procédé respectueux de l'environnement car il n'utilise pas de produits chimiques nocifs et ne produit pas de déchets importants. Le processus est également très efficace, avec une perte minimale de matériau.
- Les revêtements obtenus sont durables, résistants à l'usure et à la corrosion, et peuvent être adaptés pour répondre à des exigences fonctionnelles ou esthétiques spécifiques.
En résumé, le mécanisme du revêtement PVD implique une série d'étapes soigneusement contrôlées qui transforment un matériau cible solide en un revêtement mince et performant sur un substrat. Chaque étape, du nettoyage et de la vaporisation au dépôt et à la finition, joue un rôle essentiel pour garantir la qualité et la fonctionnalité du produit final. Le procédé est très polyvalent et permet de créer des revêtements aux propriétés très variées, ce qui en fait une technique précieuse dans des secteurs tels que l'automobile, l'aérospatiale, les appareils médicaux et l'électronique grand public.
Tableau récapitulatif :
Étape | Description de l'étape |
---|---|
Nettoyage et prétraitement | Éliminer les contaminants et améliorer l'adhérence grâce au nettoyage et au traitement de la surface. |
Environnement à vide poussé | Créer un vide pour éviter la contamination et assurer la propreté du matériau vaporisé. |
Vaporisation de la cible | Utiliser la pulvérisation cathodique, l'évaporation à l'arc ou le faisceau d'électrons pour vaporiser le matériau cible. |
Transport des atomes | Transporter les atomes vaporisés vers le substrat en ligne droite. |
Réaction avec des gaz (facultatif) | Introduire des gaz réactifs pour modifier les propriétés du revêtement (par exemple, la dureté). |
Dépôt et condensation | Déposer des atomes sur le substrat pour former un film mince et uniforme. |
Contrôle de la qualité et finition | Tester et améliorer les propriétés du revêtement en termes de performance et d'apparence. |
Avantages pour l'environnement | Respectueux de l'environnement, efficace et produisant des revêtements durables et sur mesure. |
Exploitez le potentiel des revêtements PVD pour vos applications. contactez nos experts dès aujourd'hui !