La taille des particules obtenue dans un broyeur à billes dépend de plusieurs facteurs, notamment la taille initiale des particules du matériau, la taille et le type de support de broyage (billes), la durée du broyage et les paramètres opérationnels tels que la vitesse de rotation et le taux de remplissage. En règle générale, les broyeurs à billes sont utilisés pour réduire la taille des particules à une fourchette de 1 à 20 μm, des billes plus petites et des durées de broyage plus longues permettant d'obtenir des particules plus fines. La taille finale des particules est influencée par les cycles de broyage, le temps de séjour et les conditions opérationnelles spécifiques du broyeur.
Explication des points clés :
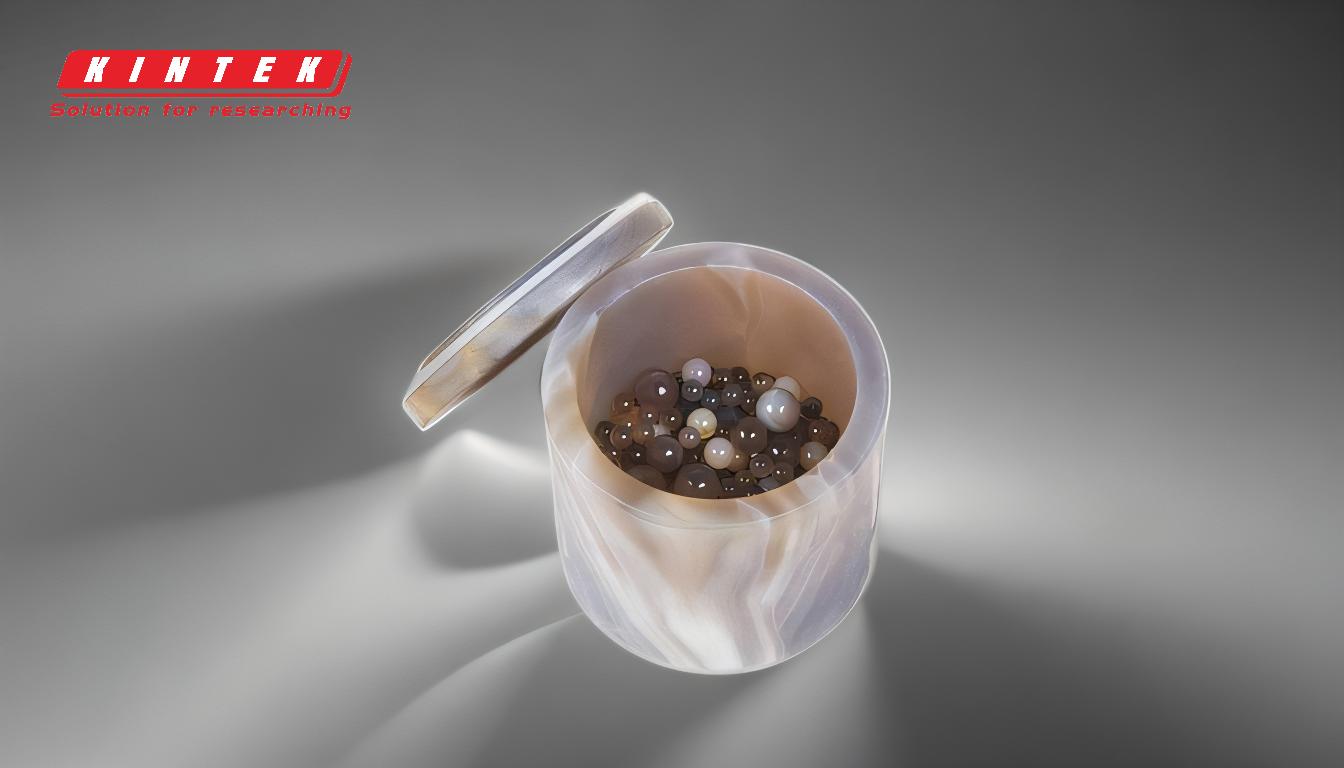
-
Gamme de tailles de particules typique dans les broyeurs à boulets :
- Les broyeurs à billes sont généralement utilisés pour obtenir des particules de taille comprise entre 1-20 μm notamment dans les laboratoires de céramique et dans les processus de broyage des minerais.
- La taille moyenne initiale des particules (d50) du matériau broyé joue un rôle important dans la détermination de la taille finale des particules.
-
Facteurs influençant la taille des particules :
- Moyen de broyage (boulets) : Des billes plus petites sont plus efficaces pour produire des particules plus fines. La taille, la densité et le nombre de billes ont un impact direct sur l'efficacité du broyage.
- Durée du broyage : Des durées de broyage plus longues permettent généralement d'obtenir des particules de plus petite taille, car le matériau est soumis à davantage de collisions et d'abrasion.
- Temps de séjour : Le temps passé par le matériau dans la chambre du broyeur influe sur le degré de réduction de la taille. Des temps de séjour plus longs permettent un broyage plus complet.
- Vitesse de rotation : La vitesse de rotation du broyeur influe sur l'énergie transmise à l'agent de broyage et au matériau. Des vitesses plus élevées peuvent améliorer l'efficacité du broyage, mais doivent être optimisées pour éviter une usure excessive ou une surchauffe.
- Taux de remplissage : Le pourcentage du volume du broyeur rempli d'agent de mouture (billes) influe sur les performances du broyage. Un taux de remplissage optimal garantit un broyage efficace sans surcharger le broyeur.
-
Paramètres opérationnels :
- Dimensions du tambour : Le diamètre et la longueur du tambour, ainsi que le rapport entre le diamètre et la longueur du tambour (le rapport optimal L:D est de 1,56-1,64), influencent l'efficacité du broyage.
- Vitesse d'alimentation et niveau : La vitesse à laquelle le matériau est introduit dans le broyeur et le niveau du matériau dans la cuve peuvent affecter le processus de broyage. Une vitesse d'alimentation constante permet de maintenir des conditions de broyage optimales.
- Propriétés du matériau : La dureté et les propriétés physico-chimiques du matériau à broyer jouent un rôle dans la détermination de l'efficacité du broyage et de la taille finale des particules.
-
Optimisation pour des applications spécifiques :
- Dans les applications industrielles, l'optimisation des paramètres du broyeur à boulets est cruciale pour obtenir la distribution granulométrique souhaitée. Il s'agit notamment de sélectionner la taille de bille appropriée, d'ajuster la vitesse de rotation et de contrôler le taux de remplissage.
- Pour les applications céramiques, l'objectif est souvent d'obtenir un mélange homogène de poudres de départ avec une granulométrie spécifique.
-
Considérations pratiques :
- Cycles de broyage : Le nombre de cycles de broyage et le temps de séjour dans le broyeur déterminent le degré de réduction de la taille. Plusieurs cycles peuvent être nécessaires pour obtenir la finesse souhaitée.
- Élimination rapide du produit broyé : L'extraction efficace du produit broyé du broyeur permet d'éviter le surbroyage et d'assurer une distribution granulométrique cohérente.
En contrôlant soigneusement ces facteurs, les opérateurs peuvent obtenir la taille de particule souhaitée dans les processus de broyage à boulets, que ce soit pour le broyage de minerais industriels ou la préparation de poudres céramiques.
Tableau récapitulatif :
Facteur | Impact sur la taille des particules |
---|---|
Moyen de broyage (billes) | Des billes plus petites produisent des particules plus fines ; la taille, la densité et le nombre de billes affectent l'efficacité du broyage. |
Durée du broyage | Des durées de broyage plus longues produisent des particules plus petites en raison de l'augmentation des collisions et de l'abrasion. |
Vitesse de rotation | Des vitesses plus élevées augmentent l'efficacité du broyage mais doivent être optimisées pour éviter l'usure ou la surchauffe. |
Taux de remplissage | Un taux de remplissage optimal garantit un broyage efficace sans surcharger le broyeur. |
Dimensions du tambour | Le diamètre, la longueur et le rapport L:D influencent l'efficacité du broyage. |
Propriétés du matériau | La dureté et les propriétés physico-chimiques influencent l'efficacité du broyage et la taille finale des particules. |
Optimisez votre processus de broyage à boulets pour obtenir des particules de taille précise. contactez nos experts dès aujourd'hui !