Dans le processus de revêtement par dépôt physique en phase vapeur (PVD), différents gaz sont utilisés en fonction des propriétés souhaitées du revêtement et de la technique PVD employée.L'argon est le gaz inerte le plus couramment utilisé en raison de sa nature non réactive, qui garantit la pureté du matériau de revêtement pendant la vaporisation.Les gaz réactifs tels que l'oxygène, l'azote, le méthane et l'acétylène sont également utilisés pour former des revêtements composés tels que les oxydes, les nitrures et les carbures.Le choix du gaz dépend du matériau de revêtement, du substrat et de l'application prévue du produit revêtu.
Explication des points clés :
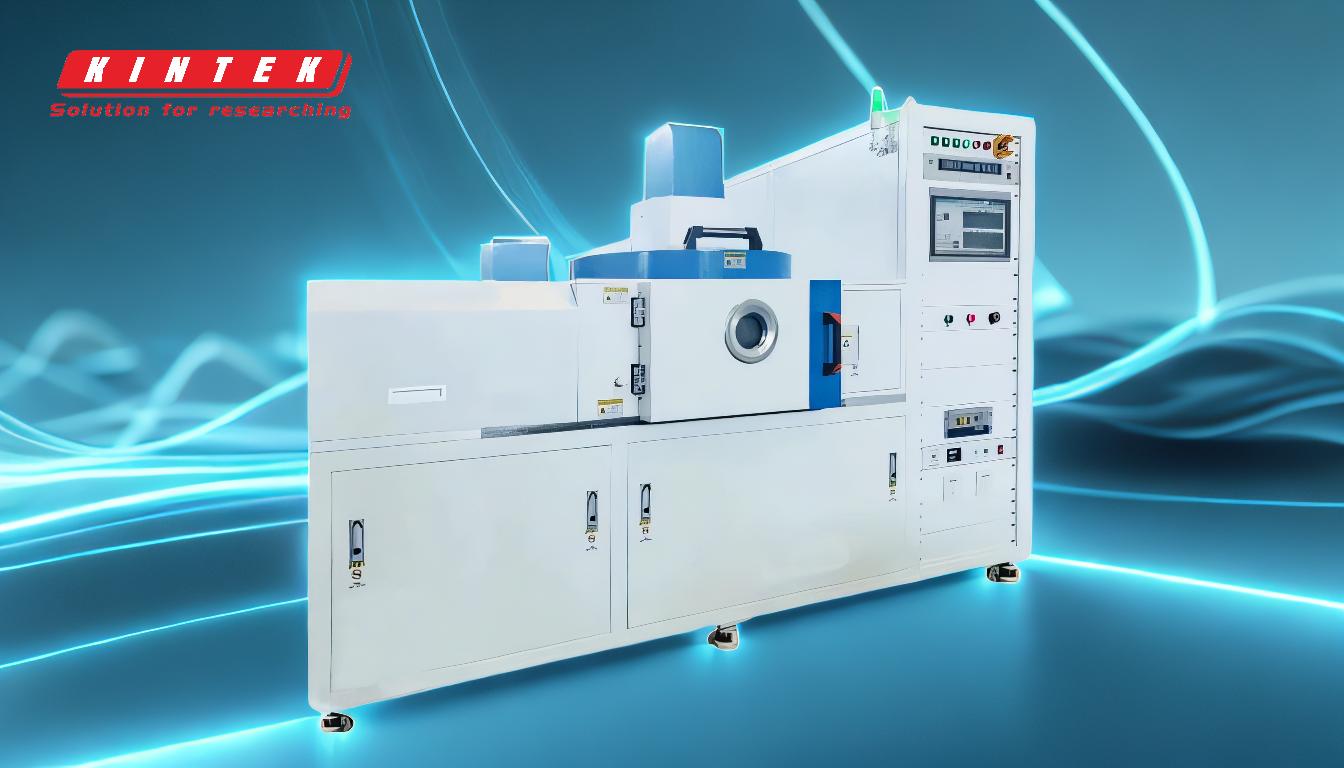
-
L'argon, principal gaz inerte:
- Rôle:L'argon est largement utilisé en PVD car il est inerte, c'est-à-dire qu'il ne réagit pas chimiquement avec le matériau de revêtement ou le substrat.Cela garantit que le matériau de revêtement reste pur pendant les étapes de vaporisation et de dépôt.
- Le procédé:Lors de la pulvérisation magnétron ou de l'évaporation par arc cathodique, des ions d'argon sont utilisés pour bombarder le matériau cible, provoquant sa vaporisation et la formation d'un plasma.Le matériau vaporisé se dépose alors sur le substrat.
- Les avantages:La nature inerte de l'argon le rend idéal pour créer des revêtements métalliques purs sans introduire d'impuretés.
-
Gaz réactifs pour les revêtements composés:
- Oxygène (O2):Utilisé pour former des revêtements d'oxyde métallique (par exemple, dioxyde de titane, oxyde d'aluminium).Ces revêtements sont souvent utilisés pour leur dureté, leur résistance à l'usure et leurs propriétés optiques.
- Azote (N2):Réagit avec les atomes de métal pour former des nitrures (par exemple, le nitrure de titane, le nitrure de chrome), connus pour leur dureté, leur résistance à la corrosion et leur aspect décoratif semblable à l'or.
- Méthane (CH4) et acétylène (C2H2):Utilisé pour créer des revêtements en carbure (par exemple, carbure de titane, carbure de silicium), qui sont extrêmement durs et résistants à l'usure.L'acétylène est particulièrement utilisé pour les revêtements de carbone de type diamant (DLC).
- Hexa-Méthyl-Disiloxane (HMDSO):Utilisé dans le dépôt chimique en phase vapeur assisté par plasma (PACVD) pour créer des revêtements contenant du silicium, souvent utilisés pour leurs propriétés optiques et de barrière.
-
Sélection des gaz en fonction de la technique de dépôt en phase vapeur (PVD):
- Pulvérisation magnétron:L'argon est le principal gaz de pulvérisation, mais des gaz réactifs comme l'azote ou l'oxygène peuvent être introduits pour former des revêtements composés.
- Évaporation par arc cathodique:L'argon est utilisé comme gaz primaire, mais des gaz réactifs peuvent être ajoutés pour modifier les propriétés du revêtement.
- Évaporation thermique ou par faisceau d'électrons:L'argon est généralement utilisé, mais des gaz réactifs peuvent être introduits pour former des revêtements composés.
-
Système d'alimentation en gaz de procédé:
- Alimentation en gaz:Les gaz sont fournis par des bouteilles et contrôlés par des vannes et des compteurs afin de garantir des débits précis.
- Chambre à vide:Les gaz sont introduits dans la chambre à vide, où ils interagissent avec le matériau de revêtement vaporisé pour former le revêtement souhaité.
-
Applications des différents gaz:
- Revêtements décoratifs:L'azote est souvent utilisé pour créer des revêtements dorés à des fins décoratives.
- Revêtements fonctionnels:L'oxygène et le méthane sont utilisés pour créer des revêtements durs et résistants à l'usure pour des applications industrielles.
- Revêtements optiques:L'HMDSO est utilisé pour créer des revêtements aux propriétés optiques spécifiques.
-
Importance de la pureté des gaz:
- Les gaz de haute pureté sont essentiels pour éviter la contamination et garantir une qualité constante du revêtement.Les impuretés présentes dans le gaz peuvent entraîner des défauts dans le revêtement, réduisant ainsi ses performances et sa durabilité.
En choisissant soigneusement le gaz ou le mélange de gaz approprié, les fabricants peuvent adapter les propriétés du revêtement PVD aux exigences spécifiques de l'application, que ce soit à des fins décoratives, fonctionnelles ou optiques.
Tableau récapitulatif :
Type de gaz | Rôle dans le revêtement PVD | Applications courantes |
---|---|---|
Argon (Ar) | Gaz inerte pour les revêtements métalliques purs, utilisé dans les processus de pulvérisation et d'évaporation. | Revêtements métalliques purs, garantissant l'absence d'impuretés. |
Oxygène (O2) | Forme des revêtements d'oxyde métallique (par exemple, TiO2, Al2O3) pour la dureté et la résistance à l'usure. | Revêtements durs et résistants à l'usure pour les applications industrielles. |
Azote (N2) | Crée des nitrures (par exemple, TiN, CrN) pour la dureté, la résistance à la corrosion et la décoration. | Revêtements décoratifs de type or et couches fonctionnelles résistantes à l'usure. |
Méthane (CH4) | Forme des revêtements de carbure (par exemple TiC, SiC) pour une dureté et une résistance à l'usure extrêmes. | Applications industrielles nécessitant une grande durabilité. |
Acétylène (C2H2) | Utilisé pour les revêtements de carbone de type diamant (DLC). | Revêtements haute performance pour les outils et les machines. |
HMDSO | Crée des revêtements contenant du silicium pour des propriétés optiques et de barrière. | Revêtements optiques et couches protectrices. |
Vous avez besoin d'aide pour sélectionner les gaz appropriés pour votre processus de revêtement PVD ? Contactez nos experts dès aujourd'hui pour des solutions sur mesure !