Une atmosphère inerte est utilisée dans la fabrication d'alliages pour éviter les réactions chimiques indésirables, telles que l'oxydation ou la contamination, au cours de processus tels que le traitement thermique, le frittage ou le pressage isostatique à chaud.En créant un environnement contrôlé avec des gaz comme l'argon ou l'azote, les fabricants peuvent s'assurer que l'alliage conserve les propriétés souhaitées, telles que la résistance, la durabilité et la qualité de la surface.Cet aspect est particulièrement important dans des secteurs tels que l'aérospatiale, l'automobile et la pétrochimie, où l'intégrité des matériaux est primordiale.L'atmosphère inerte réduit également les risques d'incendie, d'explosion et de contamination, garantissant ainsi des processus de production plus sûrs et plus efficaces.
Explication des points clés :
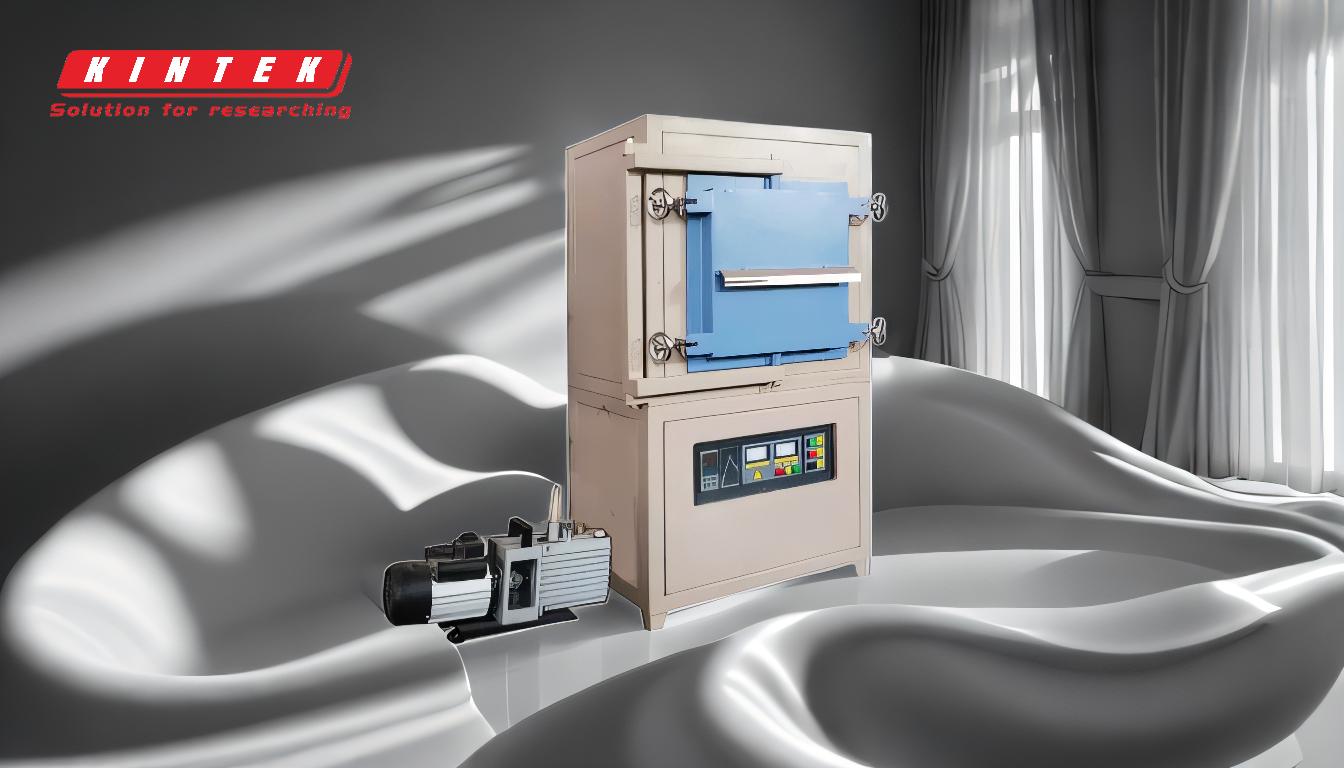
-
Prévention de l'oxydation et de la contamination
- L'oxydation se produit lorsque les métaux réagissent avec l'oxygène de l'air, formant des oxydes qui peuvent dégrader la surface et les propriétés mécaniques de l'alliage.
- Une atmosphère inerte, généralement créée à l'aide de gaz comme l'argon ou l'azote, déplace l'oxygène et les autres gaz réactifs, empêchant ainsi l'oxydation et la contamination.
- L'alliage conserve ainsi la composition chimique et la qualité de surface souhaitées, ce qui est essentiel pour les applications exigeant une grande précision et une grande durabilité.
-
Maintien des propriétés du matériau
- Au cours des processus de traitement thermique tels que le frittage, le recuit brillant ou la carbonitruration, la microstructure et les propriétés mécaniques de l'alliage sont soigneusement contrôlées.
- Une atmosphère inerte garantit que ces processus se déroulent sans interférence de facteurs externes, préservant ainsi la résistance, la dureté et d'autres propriétés critiques de l'alliage.
- Par exemple, dans les secteurs de l'aérospatiale ou de l'automobile, des écarts même mineurs dans les propriétés des matériaux peuvent entraîner des défaillances catastrophiques.
-
Amélioration du contrôle des processus
- Une atmosphère inerte fournit un environnement hautement contrôlé, réduisant la variabilité du processus de fabrication.
- Ceci est particulièrement important dans des procédés tels que le pressage isostatique à chaud (HIP) ou les opérations sous vide, où un contrôle précis de la température, de la pression et de la composition des gaz est nécessaire.
- En minimisant les réactions indésirables, les fabricants peuvent obtenir des résultats cohérents et réduire les déchets.
-
Sécurité et atténuation des risques
- Les atmosphères inertes réduisent le risque d'incendie et d'explosion, en particulier lorsque l'on travaille avec des métaux réactifs ou des procédés à haute température.
- En déplaçant l'oxygène, la probabilité de combustion est considérablement réduite, ce qui crée un environnement de travail plus sûr.
- Ceci est particulièrement important dans des industries telles que la pétrochimie, où la sécurité est une priorité absolue.
-
Applications dans les industries critiques
- Les industries telles que l'aérospatiale, l'automobile et la pétrochimie dépendent des atmosphères inertes pour produire des alliages de haute qualité répondant à des spécifications précises.
- Par exemple, dans l'aérospatiale, les alliages doivent résister à des conditions extrêmes, et toute contamination ou oxydation pourrait compromettre leurs performances.
- De même, dans la construction automobile, les composants tels que les pièces de moteur ou les systèmes de transmission nécessitent des matériaux aux propriétés constantes pour garantir leur fiabilité et leur longévité.
-
Avantages en termes de coûts et d'efficacité
- Si la création d'une atmosphère inerte peut entraîner des coûts supplémentaires, les avantages à long terme l'emportent souvent sur l'investissement initial.
- En réduisant l'oxydation et la contamination, les fabricants peuvent minimiser les déchets de matériaux et les retouches, ce qui permet de réaliser des économies.
- En outre, l'amélioration de la cohérence et de la qualité des alliages peut renforcer l'efficacité globale du processus de fabrication.
En résumé, une atmosphère inerte est essentielle dans la fabrication d'alliages pour prévenir l'oxydation, maintenir les propriétés des matériaux, assurer le contrôle des processus, renforcer la sécurité et répondre aux exigences rigoureuses des industries critiques.En utilisant des gaz inertes comme l'argon ou l'azote, les fabricants peuvent produire des alliages de haute qualité avec des performances constantes, ce qui en fait un élément essentiel des processus industriels modernes.
Tableau récapitulatif :
Principaux avantages de l'atmosphère inerte | Détails |
---|---|
Prévient l'oxydation et la contamination | Utilise des gaz tels que l'argon ou l'azote pour déplacer l'oxygène, garantissant ainsi l'intégrité de l'alliage. |
Maintien des propriétés des matériaux | Préserve la résistance, la dureté et la durabilité au cours des processus de traitement thermique. |
Améliore le contrôle des processus | Réduit la variabilité, garantissant des résultats cohérents dans des processus tels que le HIP ou le frittage. |
Amélioration de la sécurité | Réduit les risques d'incendie et d'explosion en déplaçant l'oxygène dans les processus à haute température. |
Applications industrielles critiques | Essentiel pour l'aérospatiale, l'automobile et la pétrochimie. |
Avantages en termes de coûts et d'efficacité | Réduit les déchets et les retouches, améliorant ainsi l'efficacité de la fabrication à long terme. |
Découvrez comment une atmosphère inerte peut optimiser votre processus de fabrication d'alliages. contactez nos experts dès aujourd'hui !