Un four à induction fait fondre le métal en utilisant l'induction électromagnétique pour générer de la chaleur dans le métal lui-même.Ce processus consiste à faire passer un courant alternatif dans une bobine, ce qui crée un champ magnétique qui change rapidement.Lorsqu'un métal conducteur est placé dans ce champ, des courants de Foucault sont induits dans le métal, qui s'échauffe et finit par fondre.L'efficacité et la rapidité de la fusion dépendent de facteurs tels que la puissance absorbée, le type de métal et la conception du four.Les fours à induction modernes, en particulier ceux qui utilisent des four à induction IGBT offrent un contrôle précis du processus de fusion, ce qui les rend très efficaces pour les applications industrielles.
Explication des points clés :
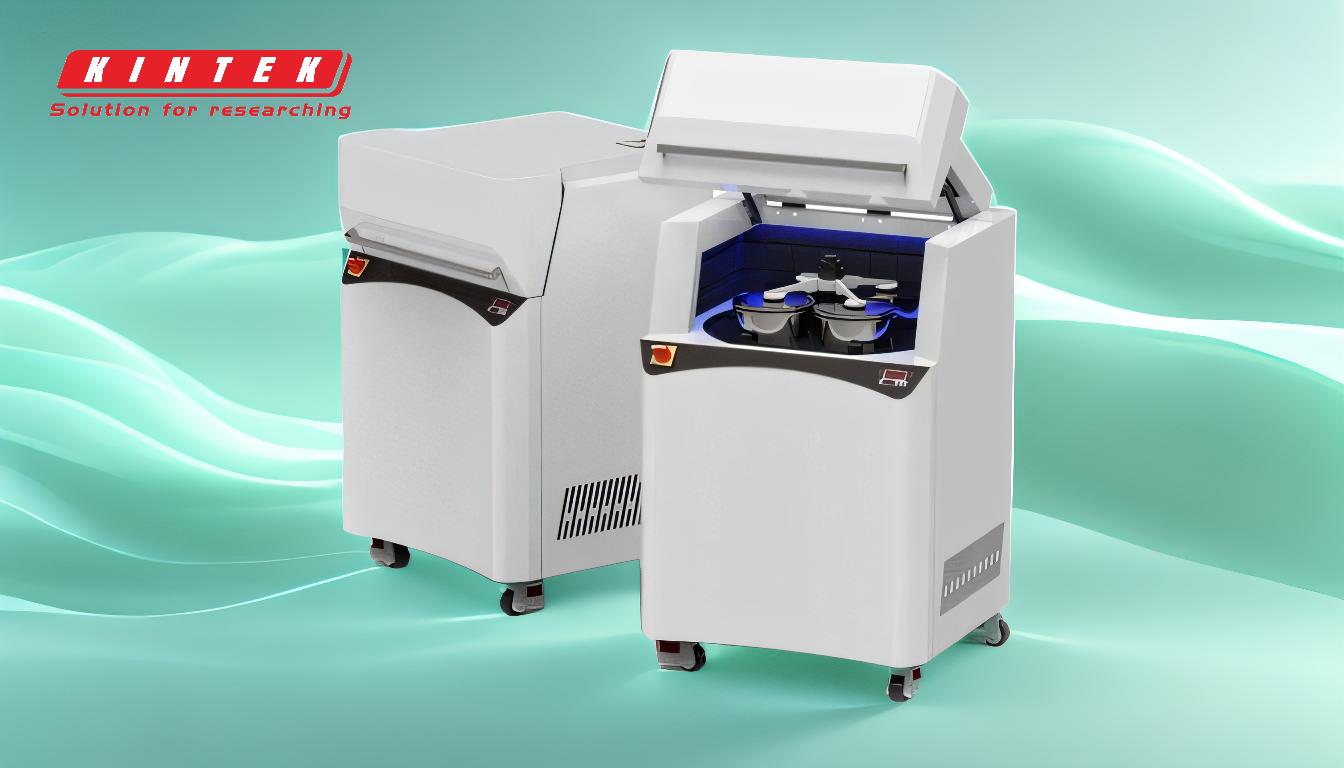
-
Principe de l'induction électromagnétique:
- Les fours à induction fonctionnent selon le principe de l'induction électromagnétique.Un courant alternatif (CA) passe dans une bobine, créant un champ magnétique.Lorsqu'un métal conducteur est placé dans ce champ, des courants de Foucault sont induits dans le métal, générant une chaleur due à la résistance électrique.Cette chaleur est suffisante pour faire fondre le métal.
-
Rôle de la bobine et du champ magnétique:
- La bobine, souvent en cuivre, est un élément essentiel du four à induction.Le courant alternatif dans la bobine produit un champ magnétique qui change rapidement.Ce champ pénètre le métal, induisant des courants de Foucault qui chauffent le métal de l'intérieur.L'efficacité de ce processus dépend de la fréquence du courant alternatif et de la conception de la bobine.
-
Facteurs influençant le processus de fusion:
- Température:Le point de fusion du métal détermine la température requise.Les fours à induction peuvent atteindre des températures très élevées, ce qui leur permet de fondre une large gamme de métaux.
- Pression:Alors que la pression n'est pas un facteur important dans la fusion par induction, l'absence de contaminants atmosphériques est cruciale pour maintenir la pureté du métal.
- Impuretés et scories:La présence d'impuretés peut affecter le processus de fusion.Les fours à induction comportent souvent des mécanismes d'élimination des scories et des impuretés, ce qui permet d'obtenir une fonte plus propre.
- Oxydants:L'absence d'oxydants est essentielle pour éviter l'oxydation du métal pendant le processus de fusion.Les fours à induction fonctionnent généralement dans une atmosphère contrôlée afin de minimiser l'oxydation.
-
Calcul de la vitesse de fusion:
- La vitesse de fusion dans un four à induction peut être calculée à l'aide de la formule :
- [
- \text{Taux de fusion (kg/heure)} = \frac{\text{Puissance (kW)}{\text{Consommation électrique standard (kWh/tonne)}}
-
] Par exemple, si le four fonctionne à 325 kW et que la consommation électrique standard est de 0,625 kWh/kg, la vitesse de fusion sera la suivante :
- [ \frac{325 \text{ kW}}{0,625 \text{ kWh/kg}} = 520 \text{ kg/h} ] Cette formule permet de déterminer l'efficacité et la capacité du four pour des métaux spécifiques.
- Avantages des fours à induction IGBT:
- Contrôle de précision:
- Le four à induction IGBT permet un contrôle précis de la puissance absorbée, ce qui se traduit par une meilleure régulation de la température et une plus grande efficacité énergétique.
-
Efficacité énergétique:Les fours à IGBT sont plus économes en énergie que les fours à induction traditionnels, ce qui permet de réduire les coûts d'exploitation.
- Conception compacte
:Ces fours sont souvent plus compacts, ce qui leur permet de s'adapter à de nombreux environnements industriels. Maintenance réduite :La technologie avancée des fours à induction IGBT permet de réduire les besoins de maintenance et d'allonger la durée de vie.
Applications des fours à induction
: | Les fours à induction sont largement utilisés dans l'industrie pour fondre des métaux tels que l'acier, le fer, l'aluminium et le cuivre.Ils sont particulièrement appréciés pour leur capacité à produire des fusions de haute qualité avec une contamination minimale, ce qui les rend idéaux pour le moulage de précision et la production d'alliages. |
---|---|
En résumé, les fours à induction, en particulier ceux qui utilisent des | four à induction IGBT |
offrent une méthode de fusion des métaux très efficace et contrôlée.Le processus repose sur l'induction électromagnétique pour générer de la chaleur dans le métal, ce qui garantit une fusion propre et précise.Des facteurs tels que la température, les impuretés et la puissance absorbée jouent un rôle crucial dans la détermination de l'efficacité et de la qualité du processus de fusion. | Tableau récapitulatif : |
Aspect clé | Détails |
Principe | L'induction électromagnétique génère de la chaleur dans le métal par le biais de courants de Foucault. |
Rôle de la bobine | La bobine de cuivre crée un champ magnétique, ce qui induit de la chaleur dans le métal. |
Facteurs de fusion | La température, les impuretés, les oxydants et la puissance absorbée influent sur l'efficacité de la fusion. |
Formule du taux de fusion Taux de fusion (kg/heure) = Puissance (kW) / Consommation électrique standard (kWh/kg). Avantages du four IGBT