La longueur d'un four rotatif à ciment peut varier considérablement en fonction de sa conception, de son application et de sa capacité de production.Les fours rotatifs à ciment sont généralement de longs cylindres horizontaux en acier revêtus de matériaux réfractaires, conçus pour faciliter les réactions chimiques nécessaires à la production de ciment.La longueur de ces fours peut varier d'environ 50 mètres à 230 mètres, la limite supérieure étant limitée par des considérations structurelles telles que la capacité de la coque à résister à la déformation sous son propre poids.Le rapport longueur/diamètre (L/D) est un paramètre de conception essentiel, qui influe sur l'efficacité du four, la distribution de la chaleur et le temps de séjour des matériaux.Les fours de grande taille sont souvent utilisés dans les cimenteries de grande capacité, tandis que les fours plus petits peuvent être employés dans des applications spécialisées ou des opérations à plus petite échelle.
Explication des points clés :
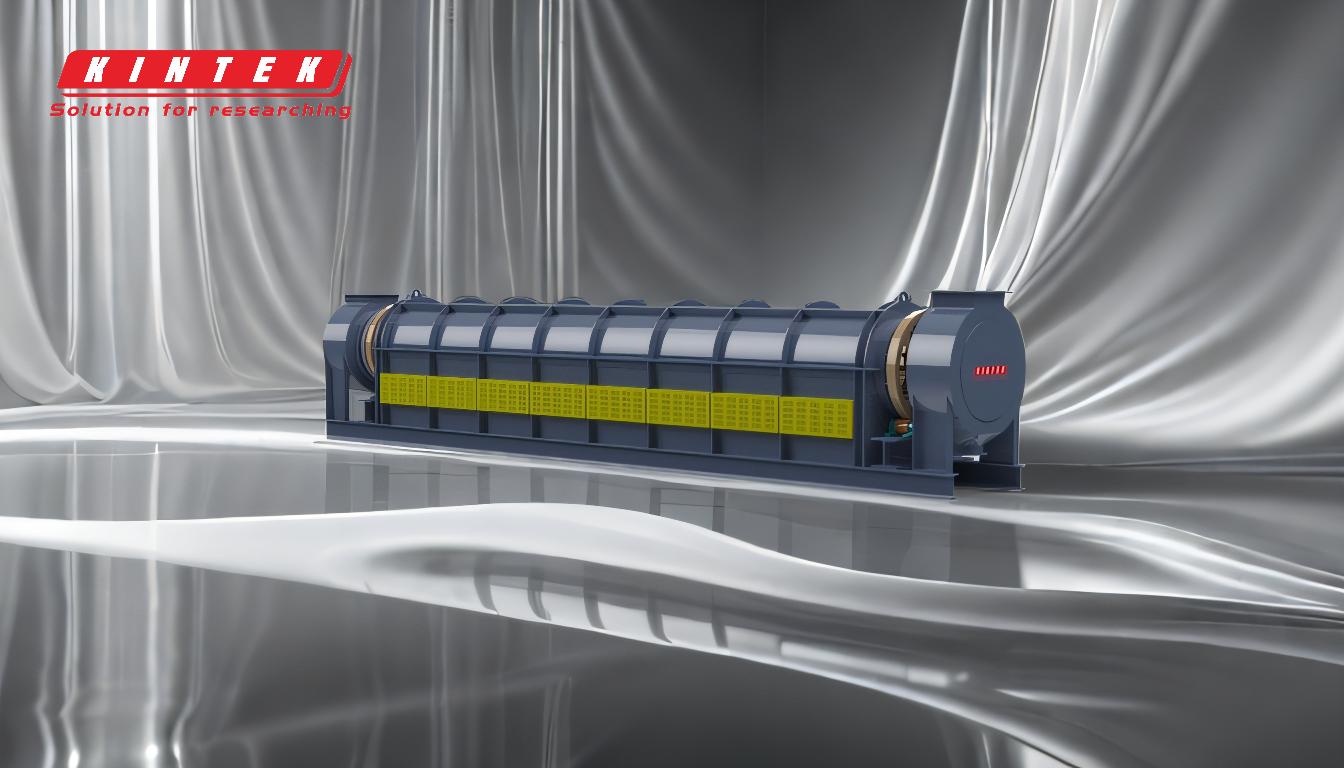
-
Gamme de longueurs typiques des fours rotatifs à ciment:
- Les fours rotatifs à ciment sont généralement de longues structures, dont la longueur varie de 50 mètres à 230 mètres .
- La longueur est déterminée par la capacité de production, le type de ciment produit et les réactions chimiques spécifiques requises.
- Les fours de grande taille sont utilisés dans les cimenteries de grande capacité, tandis que les fours de petite taille conviennent aux applications spécialisées ou à faible volume.
-
Contraintes structurelles sur la longueur du four:
- La coque du four est généralement constituée de plaques d'acier doux laminées, d'une épaisseur comprise entre 15 à 30 mm .
- La limite supérieure de la longueur (environ 230 mètres) est fixée par l'intégrité structurelle du navire. l'intégrité structurelle Les fours plus longs sont plus susceptibles de se déformer sous l'effet de leur propre poids.
- Le diamètre du four joue également un rôle dans la détermination de la longueur maximale réalisable, les diamètres plus importants nécessitant des longueurs plus courtes pour maintenir la stabilité.
-
Rapport longueur/diamètre (L/D):
- Le rapport L/D est un paramètre de conception essentiel pour les fours rotatifs, car il influence la distribution de la chaleur, le temps de séjour des matières et l'efficacité globale.
- Un rapport L/D plus élevé permet généralement un meilleur transfert de chaleur et des réactions chimiques mieux contrôlées, mais il augmente également la complexité et le coût du four.
- Les rapports L/D typiques pour les fours rotatifs à ciment sont compris entre 15:1 à 40:1 en fonction de l'application spécifique et des objectifs de conception.
-
Impact de la longueur du four sur les performances:
- Des fours plus longs permettent un temps de séjour plus long pour les matériaux, ce qui est essentiel pour mener à bien les réactions chimiques nécessaires à la production de ciment.
- Cependant, les fours plus longs nécessitent également plus d'énergie pour fonctionner et sont plus difficiles à entretenir et à gérer.
- Le choix de la longueur du four est un équilibre entre la capacité de production , l'efficacité énergétique et la faisabilité opérationnelle .
-
Comparaison avec d'autres types de fours rotatifs:
- Si les fours rotatifs à ciment sont parmi les plus longs, d'autres types de fours rotatifs (par exemple ceux utilisés pour la pyrolyse ou le traitement de la biomasse) peuvent être plus courts.
- Par exemple, les fours rotatifs à pyrolyse sont souvent conçus pour les opérations suivantes opérations de pyrolyse lente et peuvent avoir des longueurs optimisées pour des matières premières spécifiques et des exigences de distribution de la chaleur.
-
Considérations relatives à la conception des fours rotatifs à ciment:
- L'angle d'inclinaison l'angle d'inclinaison et vitesse de rotation du four sont réglés pour optimiser le flux de matière et la distribution de la chaleur.
- Les dispositifs internes tels que les barrages d'étranglement et élévateurs sont utilisés pour contrôler le temps de séjour et le mélange des matériaux.
- Les surface libre (espace ouvert au-dessus du lit de matériau) et la forme de la surface libre sont influencées par les exigences opérationnelles telles que le débit d'alimentation et les propriétés du matériau.
En comprenant ces points clés, les acheteurs d'équipement peuvent prendre des décisions éclairées quant à la longueur et à la conception du four qui conviennent à leurs besoins spécifiques en matière de production de ciment.Le choix de la longueur du four doit s'aligner sur les objectifs de production, les objectifs d'efficacité énergétique et les contraintes opérationnelles.
Tableau récapitulatif :
Aspect clé | Détails |
---|---|
Longueur typique | 50 à 230 mètres |
Contraintes structurelles | Épaisseur de la coque : 15-30 mm ; longueur maximale limitée par l'intégrité structurelle |
Rapport L/D | 15:1 à 40:1, influençant la distribution de la chaleur et l'efficacité |
Impact sur les performances | Des fours plus longs = un temps de séjour plus long, une consommation d'énergie plus élevée et des frais d'entretien plus importants. |
Considérations relatives à la conception | Angle d'inclinaison, vitesse de rotation, fixations internes et panneau libre |
Vous avez besoin d'aide pour sélectionner le four rotatif à ciment adapté à vos besoins de production ? Contactez nos experts dès aujourd'hui !