Les réacteurs à lit fluidisé (FBR) sont largement utilisés dans des industries telles que le pétrole, la chimie et le traitement de la biomasse en raison de leurs avantages tels que le mélange uniforme des particules, les gradients de température et le fonctionnement en continu.Cependant, ils présentent également des limites importantes qui peuvent avoir un impact sur leur efficacité, leur évolutivité et leurs coûts d'exploitation.Les principales limitations sont l'augmentation de la taille de la cuve du réacteur, les exigences de pompage plus élevées et la chute de pression, l'entraînement de particules, l'érosion des composants internes et les défis liés à l'augmentation de l'échelle de transfert de chaleur.En outre, le comportement des matériaux dans les FBR n'est pas suffisamment bien compris, ce qui peut entraîner des problèmes opérationnels imprévisibles.Ces limites doivent être soigneusement prises en compte lors de la conception et de l'exploitation des BRF afin de garantir des performances et une longévité optimales.
Explication des principaux points :
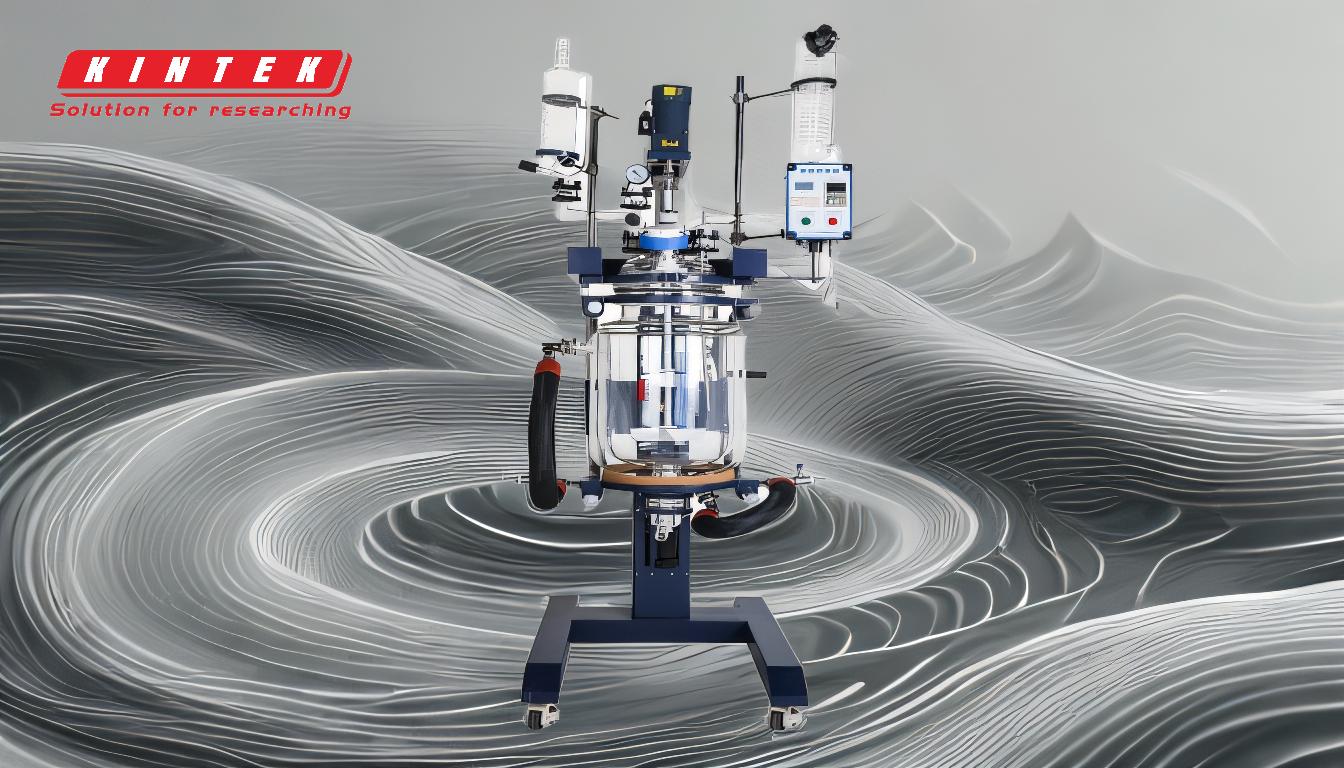
-
Augmentation de la taille de la cuve du réacteur:
- Les réacteurs à lit fluidisé nécessitent des cuves plus grandes que les autres types de réacteurs.En effet, le processus de fluidisation nécessite un espace suffisant pour que les particules solides se comportent comme un fluide.La taille plus importante augmente les coûts d'investissement et les besoins en espace, ce qui rend les RBF moins adaptés aux applications avec des contraintes d'espace ou de budget limitées.
-
Exigences de pompage et pertes de charge plus élevées:
- Les FBR nécessitent un apport d'énergie important pour maintenir l'état de fluidisation, ce qui entraîne des besoins de pompage plus élevés.La chute de pression à travers le lit peut également être importante, ce qui augmente les coûts d'exploitation.Ceci est particulièrement difficile dans les opérations à grande échelle où l'efficacité énergétique est cruciale.
-
Entraînement des particules:
- Dans les FBR, les particules fines peuvent être entraînées hors du réacteur par le gaz de fluidisation, un phénomène connu sous le nom d'entraînement de particules.Ce phénomène peut entraîner la perte de catalyseurs ou de réactifs précieux et peut nécessiter des équipements supplémentaires tels que des cyclones ou des filtres pour capturer et recycler les particules entraînées, ce qui accroît la complexité et le coût du système.
-
Érosion des composants internes:
- Le mouvement constant des particules solides dans un lit fluidisé peut provoquer l'érosion des composants internes tels que les parois du réacteur, les échangeurs de chaleur et les plaques de distribution.Cette érosion peut entraîner une maintenance et un remplacement fréquents des pièces, ce qui augmente les temps d'arrêt et les coûts d'exploitation.
-
Scénarios de perte de pression:
- Les surgénérateurs sont susceptibles de subir des pertes de pression qui peuvent perturber le processus de fluidisation et réduire l'efficacité du réacteur.Les pertes de pression peuvent être dues à des blocages, à une distribution inégale du gaz de fluidisation ou à des changements dans la taille et la densité des particules.La gestion de ces pertes de pression est cruciale pour maintenir un fonctionnement stable.
-
Les défis de l'extension du transfert de chaleur:
- Alors que les FBR offrent d'excellentes caractéristiques de transfert de chaleur à petite échelle, l'augmentation du transfert de chaleur dans les grands réacteurs est un défi.La conception doit tenir compte de la méthode de transfert de chaleur, qu'il s'agisse d'un cycle caloporteur ou d'un échange de chaleur direct.Un transfert de chaleur inadéquat peut entraîner l'apparition de points chauds ou froids, ce qui réduit l'efficacité de la réaction et peut poser des problèmes de sécurité.
-
Manque de compréhension du comportement des matériaux:
- Le comportement des matériaux dans un lit fluidisé est complexe et n'est pas entièrement compris, en particulier à grande échelle.Ce manque de compréhension peut conduire à des problèmes opérationnels imprévisibles, tels que des changements dans la qualité de la fluidisation, l'agglomération des particules ou des réactions chimiques inattendues.Des recherches continues sont nécessaires pour améliorer la prévisibilité et le contrôle des opérations des surgénérateurs.
-
Complexité opérationnelle:
- Le fonctionnement continu des FBR, bien qu'avantageux pour l'efficacité de la production, introduit également une complexité opérationnelle.Le maintien de conditions stables nécessite un contrôle précis de paramètres tels que le débit de gaz, la température et la distribution de la taille des particules.Tout écart peut entraîner une instabilité du processus, ce qui nécessite des opérateurs qualifiés et des systèmes de contrôle avancés.
-
Préoccupations en matière d'environnement et de sécurité:
- La manipulation de particules fines et de gaz à haute vitesse dans les FBR peut présenter des risques pour l'environnement et la sécurité.Les émissions de poussières, les risques d'explosion et la libération de gaz dangereux sont des problèmes qui doivent être résolus par une conception, un fonctionnement et des mesures de sécurité appropriés.
En résumé, si les réacteurs à lit fluidisé offrent des avantages significatifs en termes de mélange, de contrôle de la température et de fonctionnement continu, leurs limites - telles que l'augmentation de la taille de la cuve, les besoins énergétiques plus élevés, l'entraînement de particules, l'érosion et les défis liés à l'augmentation du transfert de chaleur - doivent être gérées avec soin.Il est essentiel de comprendre ces limites pour optimiser la conception et le fonctionnement des surgénérateurs dans diverses applications industrielles.
Tableau récapitulatif :
Limitation | Description |
---|---|
Augmentation de la taille de la cuve du réacteur | Des cuves plus grandes sont nécessaires, ce qui augmente les coûts d'investissement et les besoins en espace. |
Besoins de pompage plus élevés | Un apport d'énergie important est nécessaire, ce qui entraîne des coûts d'exploitation plus élevés. |
Entraînement des particules | Les particules fines sont entraînées, ce qui nécessite un équipement supplémentaire pour la récupération. |
Érosion des composants internes | Le mouvement constant des particules provoque l'usure, ce qui augmente les coûts de maintenance. |
Scénarios de perte de pression | Perturbe la fluidisation, ce qui nécessite une gestion attentive pour maintenir l'efficacité. |
Défis liés à la mise à l'échelle du transfert de chaleur | Difficile de passer à l'échelle supérieure, ce qui entraîne des points chauds ou froids potentiels. |
Manque de compréhension du comportement des matériaux | Problèmes opérationnels imprévisibles dus à la complexité du comportement des matériaux. |
Complexité opérationnelle | Nécessite un contrôle précis des paramètres, ce qui accroît les exigences opérationnelles. |
Préoccupations en matière d'environnement et de sécurité | Les risques comprennent les émissions de poussières, les explosions et les rejets de gaz dangereux. |
Vous avez besoin d'aide pour optimiser votre réacteur à lit fluidisé ? Contactez nos experts dès aujourd'hui pour des solutions sur mesure !