Les fours rotatifs sont des équipements industriels complexes utilisés pour le traitement à haute température des matériaux.Leur conception et leur fonctionnement sont régis par une série de paramètres qui garantissent des performances efficaces.Ces paramètres peuvent être classés en trois grandes catégories : les facteurs de conception, les facteurs structurels et les facteurs opérationnels.Les paramètres de conception comprennent les caractéristiques des matériaux telles que la taille des particules, la densité apparente et les propriétés thermiques, qui influencent la construction du four.Les paramètres structurels impliquent des composants tels que la coque du four, le revêtement réfractaire et l'ensemble de l'entraînement.Les paramètres opérationnels, tels que l'angle d'inclinaison, la vitesse de rotation et les profils de température, déterminent les performances du four pendant son utilisation.Il est essentiel de comprendre ces paramètres pour optimiser l'efficacité du four et obtenir les résultats souhaités.
Explication des points clés :
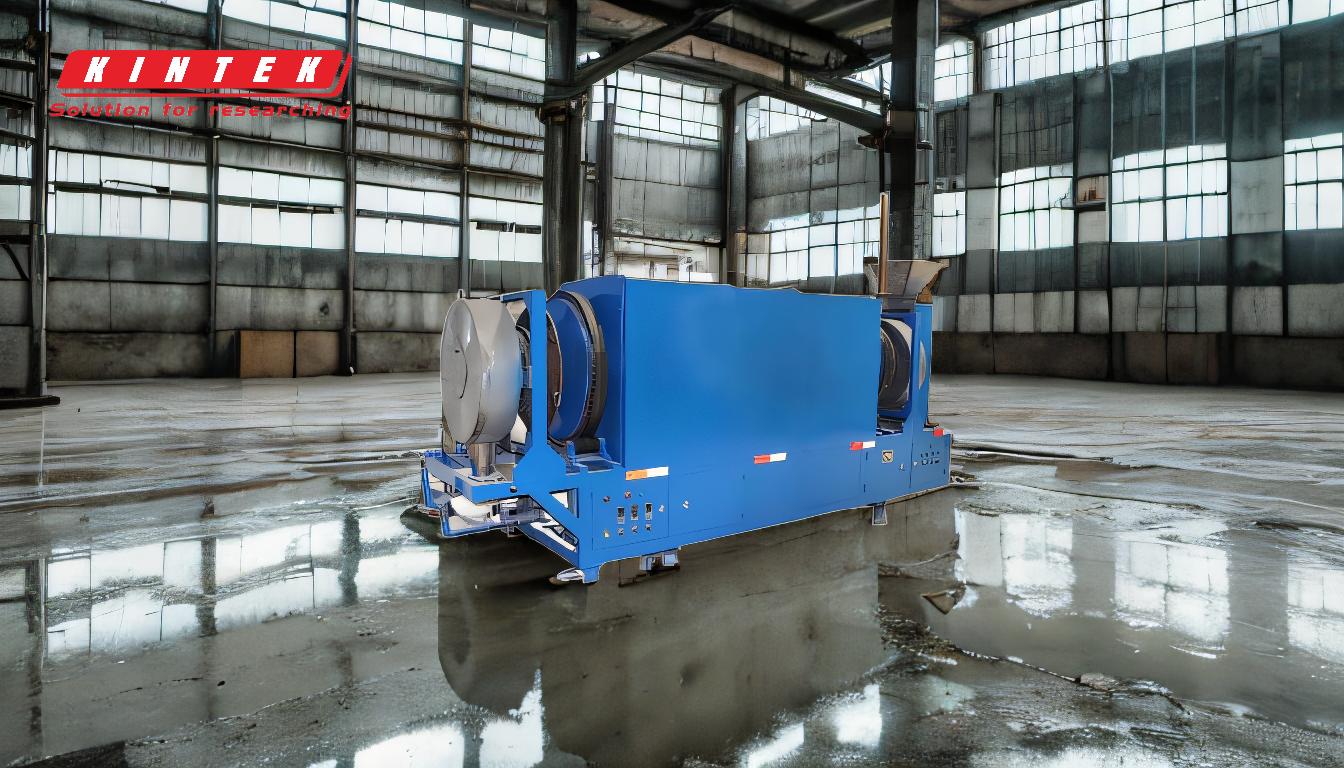
-
Paramètres de conception:
-
Caractéristiques des matériaux:La conception d'un four rotatif est fortement influencée par les propriétés du matériau traité.Ces propriétés sont les suivantes
- la distribution de la taille des particules:Détermine la façon dont le matériau s'écoule et réagit dans le four.
- Densité apparente:Affecte le volume de matériau qui peut être traité à un moment donné.
- Abrasivité et corrosivité:Influence le choix des matériaux pour la construction du four afin d'en assurer la durabilité.
- Chaleur spécifique et chaleur de réaction:Détermine les besoins en énergie pour la transformation.
- Conductivité thermique:Affecte l'efficacité du transfert de chaleur à l'intérieur du four.
- Composition chimique:Détermine la résistance du four aux réactions chimiques et à la corrosion.
-
Caractéristiques des matériaux:La conception d'un four rotatif est fortement influencée par les propriétés du matériau traité.Ces propriétés sont les suivantes
-
Paramètres structurels:
- Coquille de four:Le corps principal du four, souvent conique aux extrémités, conçu pour résister à la torsion et à la flexion.
- Revêtement réfractaire:Protège l'enveloppe des températures élevées et des réactions chimiques, garantissant ainsi sa longévité.
- Pneus et rouleaux de support:Ils fournissent un support structurel et permettent au four de tourner sans à-coups.
- Assemblage de l'entraînement:Comprend les mécanismes tels que les entraînements par chaîne et pignon, les entraînements par engrenage, les entraînements par friction ou les entraînements directs, qui entraînent la rotation du four.
- Échangeurs de chaleur internes:Améliorer l'efficacité du transfert de chaleur dans le four.
-
Paramètres de fonctionnement:
- Angle d'inclinaison:L'inclinaison du four affecte le débit du matériau à travers le four.
- Vitesse de rotation:Détermine la vitesse à laquelle le matériau est mélangé et exposé à la chaleur.
- Temps de rétention:La durée pendant laquelle les particules solides restent dans le four, influençant l'ampleur de la réaction ou du traitement.
- Profils de température:Le four fonctionne avec plusieurs zones de chauffage (séchage, chauffage, réaction et trempage) pour obtenir le traitement thermique souhaité.
- Débit de matière et débit de décharge:Contrôlez le débit et assurez un traitement cohérent.
- Profondeur du lit:Contrôlé à l'aide d'un barrage circulaire, il affecte l'exposition du matériau à la chaleur et les conditions de réaction.
-
Zones de chauffage:
- Zone de séchage:Élimine l'humidité du matériau.
- Zone de chauffage:Porte le matériau à la température requise pour le traitement.
- Zone de réaction:Lieu où se produisent les premières transformations chimiques ou physiques.
- Zone de trempage:Assure une distribution uniforme de la température et achève les réactions restantes.
-
Mécanismes de contrôle:
- Barrage annulaire:Utilisé pour contrôler la profondeur du lit, assurant une exposition optimale du matériau à la chaleur et aux conditions de réaction.
- Systèmes d'entraînement:Différents mécanismes d'entraînement (chaîne et pignon, engrenage, friction ou direct) sont choisis en fonction de la taille du four et des exigences opérationnelles.
En prenant soigneusement en compte ces paramètres, les fours rotatifs peuvent être conçus et exploités de manière à maximiser l'efficacité, la durabilité et l'efficience du processus.Chaque paramètre joue un rôle essentiel pour garantir que le four répond aux besoins spécifiques du matériau traité, qu'il s'agisse de séchage, de chauffage ou de réactions chimiques.
Tableau récapitulatif :
Type de paramètre | Facteurs clés |
---|---|
Paramètres de conception | Taille des particules, densité apparente, propriétés thermiques, composition chimique |
Paramètres structurels | Coquille du four, revêtement réfractaire, pneus de support, ensemble d'entraînement, échangeurs de chaleur |
Paramètres opérationnels | Angle d'inclinaison, vitesse de rotation, profils de température, temps de rétention |
Zones de chauffage | Séchage, chauffage, réaction, trempage |
Mécanismes de contrôle | Barrage annulaire, systèmes d'entraînement |
Prêt à optimiser les performances de votre four rotatif ? Contactez nos experts dès aujourd'hui pour des solutions sur mesure !