Le recuit à l'hydrogène est un processus de traitement thermique spécialisé réalisé dans une atmosphère d'hydrogène contrôlée, généralement à des températures élevées (200-300°C). Il a de multiples fonctions, notamment la prévention de l'oxydation, la réduction des oxydes de surface, le relâchement des contraintes internes et la lutte contre la fragilisation par l'hydrogène. Le processus est souvent appelé "recuit brillant" en raison de sa capacité à produire une surface propre et exempte d'oxydation. Il nécessite toutefois une manipulation prudente, car l'hydrogène peut décarburer l'acier et il est plus coûteux que d'autres atmosphères de recuit. Les mélanges d'azote et d'hydrogène sont parfois utilisés comme alternative rentable. En outre, le recuit à faible teneur en hydrogène (ou "cuisson") est utilisé pour réduire la teneur en hydrogène des matériaux, ce qui permet d'éviter la fragilisation par l'hydrogène et d'améliorer les propriétés mécaniques.
Explication des points clés :
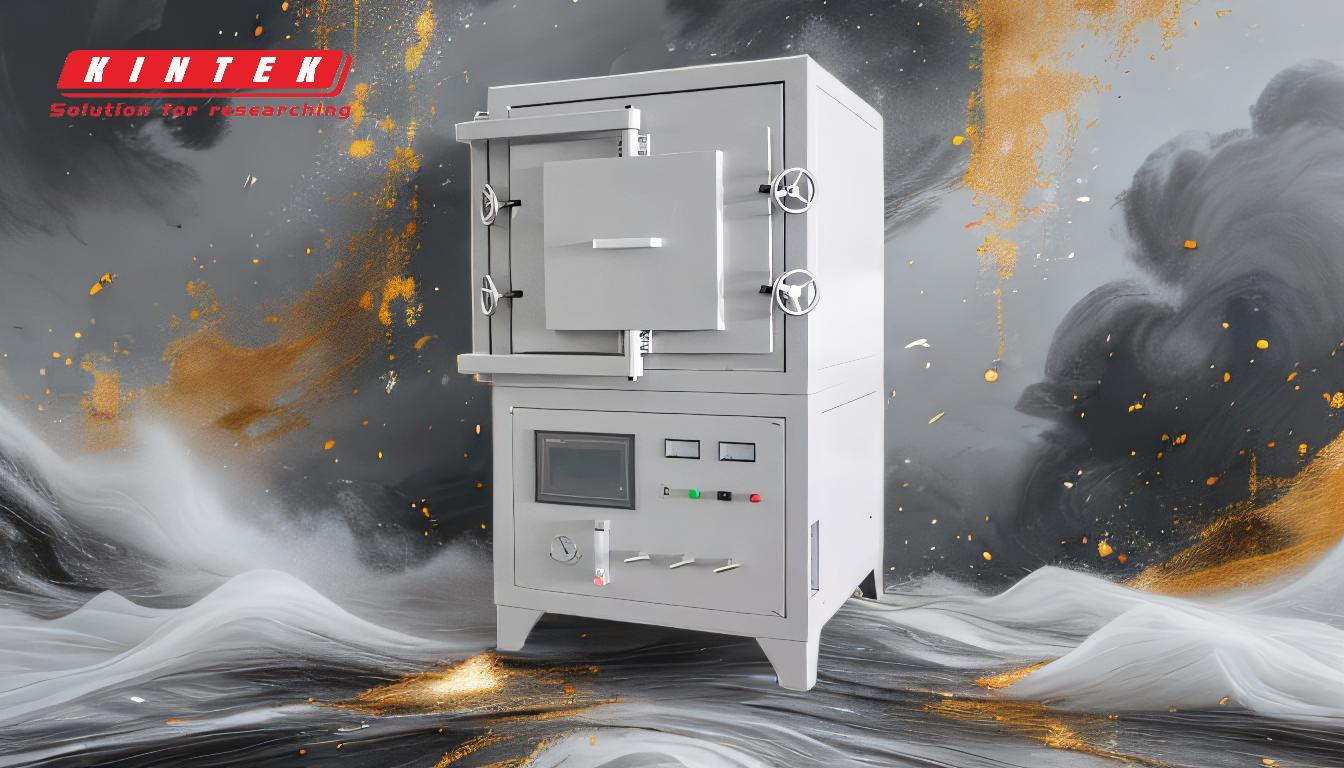
-
Définition et objectif du recuit à l'hydrogène:
- Le recuit à l'hydrogène est un processus de traitement thermique réalisé dans une atmosphère contenant 100 % d'hydrogène, généralement à des températures comprises entre 200 et 300 °C.
-
Ses principaux objectifs sont les suivants
- Prévenir l'oxydation et la décoloration des produits.
- Réduction des oxydes de surface grâce aux propriétés réductrices de l'hydrogène.
- Réduction des contraintes internes causées par les processus de fabrication tels que le moulage.
- Traitement de la fragilisation par l'hydrogène de certains matériaux.
-
Recuit brillant et nettoyage de surface:
- Le recuit à l'hydrogène est souvent appelé "recuit brillant" parce qu'il produit une surface propre et sans oxydation.
- L'hydrogène agit comme un gaz réducteur, éliminant les oxydes de la surface des pièces métalliques, ce qui est particulièrement utile pour les fils et autres composants nécessitant une finition impeccable.
-
Risques potentiels et précautions:
- L'hydrogène peut décarburer l'acier, ce qui entraîne une perte de carbone et peut affaiblir le matériau.
- Des précautions doivent être prises pour minimiser cet effet, en particulier lors du recuit d'aciers riches en carbone.
- Le processus est coûteux en raison du coût du maintien d'une atmosphère d'hydrogène pur, mais les mélanges d'azote et d'hydrogène offrent une alternative plus économique.
-
Recuit à faible teneur en hydrogène (cuisson):
- Le recuit à faible teneur en hydrogène, également appelé "cuisson", est un type spécifique de recuit à l'hydrogène visant à réduire ou à éliminer l'hydrogène dans les matériaux afin de prévenir la fragilisation par l'hydrogène.
- La fragilisation par l'hydrogène est un phénomène au cours duquel des atomes d'hydrogène se diffusent dans le réseau métallique, provoquant des fissures et dégradant les propriétés mécaniques telles que la plasticité, la ductilité et la résistance à la rupture.
- Ce processus est particulièrement important pour les matériaux tels que l'acier, qui sont susceptibles de se fissurer sous l'effet de l'hydrogène.
-
Impact sur les propriétés mécaniques:
-
Le recuit à faible teneur en hydrogène peut modifier de manière significative les propriétés mécaniques des matériaux. Par exemple :
- Dans l'acier à pipeline X80, le recuit à 200°C pendant 12 heures augmente la limite d'élasticité d'environ 10 % mais diminue l'allongement d'environ 20 %.
- Cela est dû à la formation d'une atmosphère de Cottrell, où les atomes de carbone diffusent dans les sites interstitiels des dislocations, les épinglant et réduisant la densité des dislocations mobiles.
- Bien qu'il soit efficace pour réduire la fragilisation interne par l'hydrogène, ce processus peut ne pas traiter la fragilisation par l'hydrogène causée par l'hydrogène absorbé en surface.
-
Le recuit à faible teneur en hydrogène peut modifier de manière significative les propriétés mécaniques des matériaux. Par exemple :
-
Applications et alternatives:
- Le recuit à l'hydrogène est largement utilisé dans les industries qui exigent des finitions de surface de haute qualité et une réduction des contraintes, telles que la fabrication de fils et le moulage.
- En raison du coût élevé de l'hydrogène pur, les mélanges azote-hydrogène sont souvent utilisés comme une alternative rentable, bien qu'ils n'offrent pas le même niveau de nettoyage des surfaces.
-
Paramètres du processus:
- Température : Elle est généralement comprise entre 200 et 300 °C, en fonction du matériau et des résultats souhaités.
- Atmosphère : 100 % d'hydrogène ou de mélanges azote-hydrogène.
- Durée : Elle varie en fonction de l'épaisseur du matériau et des exigences spécifiques, par exemple 12 heures pour le recuit à faible teneur en hydrogène de l'acier à pipeline X80.
-
Avantages et limites:
-
Avantages :
- Permet d'obtenir une surface propre et exempte d'oxydation.
- Soulage les contraintes internes et réduit la fragilisation par l'hydrogène.
-
Limites :
- Risque de décarburation de l'acier.
- Coût élevé du maintien d'une atmosphère d'hydrogène pur.
- Efficacité limitée contre la fragilisation par l'hydrogène absorbé en surface.
-
Avantages :
En comprenant ces points clés, les acheteurs d'équipements et de consommables peuvent décider en connaissance de cause quand et comment utiliser le recuit à l'hydrogène, en équilibrant ses avantages par rapport aux risques et aux coûts potentiels.
Tableau récapitulatif :
Aspect | Détails |
---|---|
Objectif | Prévient l'oxydation, réduit les oxydes de surface, soulage les tensions, lutte contre la fragilisation. |
Plage de température | 200-300°C |
Atmosphère | 100 % d'hydrogène ou de mélanges azote-hydrogène |
Principaux avantages | Surface propre, réduction des contraintes, réduction de la fragilisation par l'hydrogène. |
Risques | Décarburation de l'acier, coût élevé, efficacité limitée sur l'hydrogène absorbé en surface. |
Applications | Fabrication de fils, moulage et industries exigeant des finitions de haute qualité. |
Découvrez comment le recuit à l'hydrogène peut optimiser votre traitement des matériaux.. contactez nos experts dès aujourd'hui !