Le dépôt en phase vapeur est un procédé utilisé pour créer des films minces ou des revêtements sur un substrat en déposant un matériau vaporisé sur sa surface.Cette technique est largement utilisée dans des secteurs tels que les semi-conducteurs, l'optique et les revêtements de protection.Le processus consiste à convertir un matériau solide ou liquide en une vapeur, qui se condense ensuite sur un substrat pour former une couche mince et uniforme.Il existe deux principaux types de dépôt en phase vapeur : le dépôt physique en phase vapeur (PVD) et le dépôt chimique en phase vapeur (CVD).Le dépôt physique en phase vapeur consiste à vaporiser physiquement le matériau, tandis que le dépôt chimique en phase vapeur repose sur des réactions chimiques pour déposer le matériau.Les deux méthodes nécessitent des environnements contrôlés, impliquant souvent des chambres à vide, une régulation précise de la température et des pressions de gaz spécifiques.Le résultat est un revêtement très durable, résistant à la corrosion et tolérant à la température.
Explication des points clés :
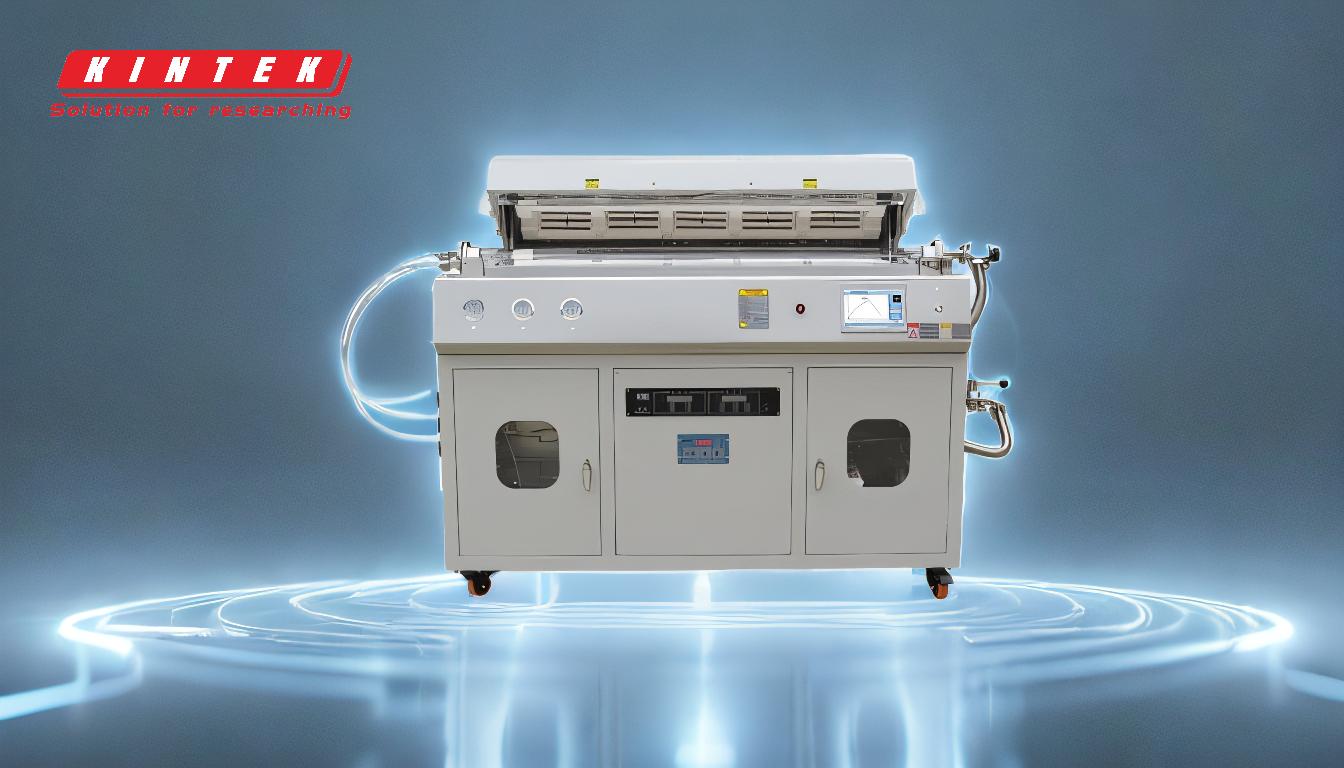
-
Vue d'ensemble du dépôt en phase vapeur:
- Le dépôt en phase vapeur est un processus par lequel des matériaux sont déposés sur un substrat sous la forme d'un film mince.
- Le matériau est d'abord vaporisé puis condensé sur le substrat, créant ainsi une couche uniforme.
- Cette technique est essentielle dans des secteurs tels que les semi-conducteurs, l'optique et les revêtements de protection.
-
Types de dépôt en phase vapeur:
-
Dépôt physique en phase vapeur (PVD):
- Il s'agit de vaporiser physiquement le matériau cible, souvent à l'aide de chaleur ou d'ions à haute énergie.
- Le matériau vaporisé est ensuite déposé sur le substrat.
- Les méthodes courantes de dépôt en phase vapeur comprennent la pulvérisation cathodique et l'évaporation thermique.
- Le dépôt en phase vapeur est connu pour créer des revêtements durables et résistants à la corrosion qui peuvent supporter des températures élevées.
-
Dépôt chimique en phase vapeur (CVD):
- Le dépôt du matériau sur le substrat s'effectue par le biais de réactions chimiques.
- Le substrat est placé dans une chambre de réaction remplie d'une forme gazeuse du matériau de revêtement.
- Le gaz réagit avec le substrat ou se décompose pour former un revêtement solide.
- Le dépôt en phase vapeur peut produire des revêtements très uniformes et conformes, ce qui le rend idéal pour les géométries complexes.
-
Dépôt physique en phase vapeur (PVD):
-
Principaux procédés de dépôt en phase vapeur:
-
Dépôt chimique en phase vapeur à basse pression (LPCVD):
- Un type de dépôt en phase vapeur qui fonctionne à des pressions réduites afin d'améliorer l'uniformité du film et de réduire les impuretés.
- Couramment utilisé dans la fabrication des semi-conducteurs.
-
Pulvérisation de plasma à basse pression (LPPS):
- Le plasma est utilisé pour activer les gaz réactifs et déposer des matériaux.
- Souvent utilisé pour créer des revêtements ayant des propriétés mécaniques ou électriques spécifiques.
-
Dépôt thermique en phase vapeur:
- Il s'agit de chauffer un matériau solide dans une chambre à vide poussé pour produire une pression de vapeur.
- Le matériau vaporisé se condense ensuite sur le substrat pour former un film mince.
- Il fonctionne généralement à des températures comprises entre 250 et 350 degrés Celsius.
-
Dépôt chimique en phase vapeur à basse pression (LPCVD):
-
Composants d'un système de dépôt en phase vapeur:
-
Source de chaleur:
- Utilisé pour vaporiser le matériau cible en PVD ou pour activer les réactions chimiques en CVD.
-
Chambre à vide:
- Fournit un environnement contrôlé avec une faible pression pour éviter la contamination et assurer un dépôt uniforme.
-
Matériau cible:
- Le matériau à déposer, qui peut être un métal, un semi-conducteur ou un autre solide.
-
Substrat:
- La surface sur laquelle le matériau est déposé, souvent faite de verre, de silicium ou d'autres matériaux.
-
Gaz d'alimentation:
- En CVD, des gaz réactifs sont introduits dans la chambre pour faciliter le processus de dépôt.
-
Contrôle de la température:
- La régulation précise de la température du substrat et de la chambre est cruciale pour obtenir les propriétés souhaitées du film.
-
Source de chaleur:
-
Applications du dépôt en phase vapeur:
-
Semi-conducteurs:
- Utilisé pour déposer des couches minces de matériaux tels que le silicium, le dioxyde de silicium et les métaux sur des tranches de semi-conducteurs.
-
Optique:
- Appliqué pour créer des revêtements antireflets, des miroirs et d'autres composants optiques.
-
Revêtements protecteurs:
- Fournit des revêtements résistants à l'usure, à la corrosion et des barrières thermiques pour les outils, les composants aérospatiaux et les appareils médicaux.
-
Revêtements décoratifs:
- Utilisé dans les secteurs de l'automobile et de la bijouterie pour créer des finitions esthétiques.
-
Semi-conducteurs:
-
Avantages du dépôt en phase vapeur:
-
Haute précision:
- Permet le dépôt de films extrêmement fins et uniformes, souvent à l'échelle nanométrique.
-
Polyvalence:
- Peut déposer une large gamme de matériaux, y compris des métaux, des céramiques et des polymères.
-
Durabilité:
- Produit des revêtements très résistants à l'usure, à la corrosion et aux températures élevées.
-
Évolutivité:
- Convient à la fois à la recherche en laboratoire à petite échelle et à la production industrielle à grande échelle.
-
Haute précision:
-
Défis et considérations:
-
Coût:
- Les coûts d'équipement et d'exploitation peuvent être élevés, en particulier pour les techniques avancées comme le dépôt en phase vapeur (CVD).
-
Complexité:
- Nécessite un contrôle précis des paramètres tels que la température, la pression et le débit de gaz.
-
Limites des matériaux:
- Tous les matériaux ne peuvent pas être facilement vaporisés ou déposés à l'aide de ces méthodes.
-
Préoccupations environnementales:
- Certains procédés impliquent des gaz dangereux ou une forte consommation d'énergie, ce qui nécessite une manipulation et une élimination soigneuses.
-
Coût:
En résumé, le dépôt en phase vapeur est une méthode polyvalente et précise qui permet de créer des couches minces et des revêtements dans un large éventail d'applications.En comprenant les différents types de dépôt en phase vapeur, les processus clés et les composants du système, on peut apprécier le rôle de la technologie dans la fabrication moderne et la science des matériaux.
Tableau récapitulatif :
Aspect | Détails |
---|---|
Types de produits | - Dépôt physique en phase vapeur (PVD) |
- Dépôt chimique en phase vapeur (CVD) | |
Principaux procédés | - Dépôt chimique en phase vapeur à basse pression (LPCVD) |
- Pulvérisation de plasma à basse pression (LPPS)
- Dépôt thermique en phase vapeur | Applications
- | Semi-conducteurs
- Optique
- Revêtements de protection Revêtements décoratifs |
- Avantages
- | Haute précision
- Polyvalence Durabilité Évolutivité
- |
- Défis
- | Coût élevé
Complexité Limites des matériaux Préoccupations environnementales