Les revêtements PVD (Physical Vapor Deposition) sont composés d'une variété de matériaux, notamment des métaux, des alliages, des céramiques et des gaz réactifs, qui sont combinés pour créer des revêtements personnalisés aux propriétés spécifiques.Les principaux composants des revêtements PVD sont des métaux tels que le titane, le chrome, le tungstène, l'aluminium et le zirconium, qui sont souvent combinés à des gaz réactifs tels que l'azote, l'oxygène ou des gaz à base de carbone pour former des composés tels que les nitrures, les carbures et les carbonitrures.Ces revêtements sont appliqués sur des substrats tels que les métaux, les plastiques, le verre et les céramiques, et sont conçus pour répondre aux exigences de diverses industries, notamment l'aérospatiale, l'automobile, l'électronique et les applications décoratives.Le processus consiste à convertir des matériaux solides en vapeur, qui se condense ensuite sur le substrat, formant une liaison solide et durable.
Explication des points clés :
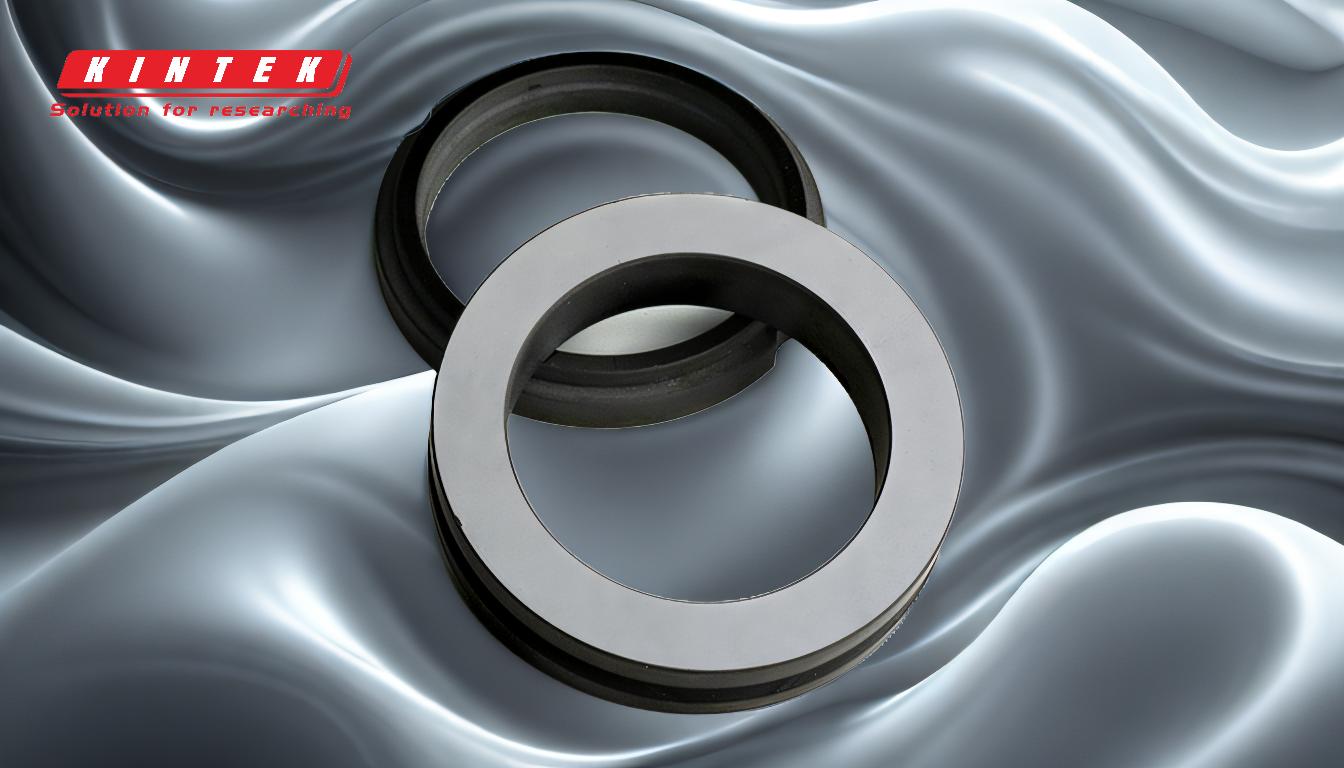
-
Métaux primaires utilisés dans les revêtements PVD:
- Titane (Ti):Couramment utilisé pour former le nitrure de titane (TiN), un revêtement dur et résistant à l'usure souvent utilisé dans les outils, les applications décoratives et les composants industriels.
- Chrome (Cr):Forme le nitrure de chrome (CrN), connu pour sa résistance à la corrosion et utilisé dans des applications telles que les revêtements de montres et les pièces de machines.
- Aluminium (Al):Souvent combiné au chrome pour former des revêtements en AlCr, utilisés pour prolonger la durée de vie des outils et des pièces de machines.
- Zirconium (Zr):Utilisé dans les revêtements spécialisés pour sa stabilité à haute température et sa résistance à l'usure.
- Tungstène (W):Généralement utilisé dans les applications à haute performance en raison de sa dureté et de sa stabilité thermique.
-
Gaz et composés réactifs:
- Azote (N₂):Réagit avec les métaux pour former des nitrures (par exemple TiN, CrN), qui sont durs, résistants à l'usure et souvent utilisés dans les outils de coupe et les revêtements décoratifs.
- Oxygène (O₂):Utilisé pour créer des oxydes (par exemple, SiO₂), qui sont souvent utilisés dans des applications optiques et électroniques.
- Gaz à base de carbone (par exemple, acétylène):Réagit avec les métaux pour former des carbures (par exemple TiC, WC) et des revêtements de carbone de type diamant (DLC), connus pour leur faible friction et leur grande dureté.
- Hydrocarbures:Utilisé pour créer des carbonitrures, qui combinent les propriétés des carbures et des nitrures pour améliorer les performances.
-
Matériaux de revêtement PVD courants:
- Nitrure de titane (TiN):Un revêtement de couleur or largement utilisé à des fins décoratives, pour les outils de coupe et les surfaces résistantes à l'usure.
- Nitrure de chrome (CrN):Un revêtement de couleur argentée connu pour sa résistance à la corrosion et utilisé dans les revêtements de montres et les pièces de machines.
- Oxyde de zinc et d'étain (ZnSn):Un revêtement optique utilisé dans les fenêtres et le verre à faible émissivité (low-e).
- Aluminium chrome (AlCr):Utilisé pour prolonger la durée de vie des outils et des pièces de machines.
- Oxyde d'indium et d'étain (ITO):Revêtement transparent et conducteur utilisé dans les écrans LCD, les écrans plasma et les panneaux tactiles.
-
Substrats pour les revêtements PVD:
-
Les revêtements PVD peuvent être appliqués sur une large gamme de substrats, notamment :
- les métaux:Acier inoxydable, aluminium et titane.
- Matières plastiques:Nylon et autres polymères.
- Céramiques:Utilisé dans des applications à haute température et résistant à l'usure.
- Verre:Utilisé dans les applications optiques et décoratives.
-
Les revêtements PVD peuvent être appliqués sur une large gamme de substrats, notamment :
-
Processus de revêtement PVD:
- Le procédé PVD consiste à convertir un matériau solide (la cible) en vapeur, qui se condense ensuite sur le substrat (la pièce).Cette opération s'effectue généralement dans une chambre à vide à des pressions comprises entre 10-² et 10-⁴ mbar.
-
Les techniques courantes de dépôt en phase vapeur comprennent
- l'évaporation:Utilisation d'un arc cathodique ou de sources de faisceaux d'électrons pour vaporiser le matériau cible.
- Pulvérisation:L'utilisation de magnétrons ou d'autres sources pour bombarder la cible avec des ions, provoquant l'éjection d'atomes qui se déposent ensuite sur le substrat.
- Des gaz réactifs tels que l'azote, l'oxygène ou l'acétylène peuvent être introduits au cours du processus pour créer des revêtements composés.
-
Applications des revêtements PVD:
- Revêtements décoratifs:TiN et CrN sont largement utilisés à des fins décoratives dans la bijouterie, l'horlogerie et l'électronique grand public.
- Outils industriels:Les revêtements PVD tels que TiN, AlCr et DLC sont utilisés pour améliorer la durabilité et les performances des outils de coupe, des moules et des pièces de machines.
- Aérospatiale et automobile:Les revêtements spécialisés tels que les carbures, les nitrures et les siliciures sont utilisés dans les composants qui nécessitent une résistance élevée à l'usure, une stabilité thermique et une résistance à la corrosion.
- L'électronique:Les revêtements ITO sont utilisés dans les écrans et les panneaux tactiles, tandis que d'autres revêtements sont utilisés dans les semi-conducteurs et les capteurs.
-
Personnalisation et polyvalence:
- Les revêtements PVD sont hautement personnalisables, ce qui permet de combiner différents métaux, gaz et éléments pour créer des revêtements aux propriétés spécifiques telles que la dureté, la résistance à l'usure, la résistance à la corrosion et les caractéristiques optiques.
- Grâce à cette polyvalence, les revêtements PVD conviennent à un large éventail d'industries, des biens de consommation aux applications de haute technologie.
En comprenant la composition et les propriétés des revêtements PVD, les acheteurs peuvent sélectionner les matériaux et les procédés les plus appropriés pour leurs applications spécifiques, garantissant ainsi des performances et une durabilité optimales.
Tableau récapitulatif :
Composant | Exemples d'application | Applications |
---|---|---|
Métaux primaires | Titane, chrome, aluminium, zirconium, tungstène | Outils, revêtements décoratifs, pièces de machines, applications à haute température |
Gaz réactifs | Azote, oxygène, gaz à base de carbone (par exemple, acétylène) | Revêtements de nitrures, d'oxydes, de carbures et de carbone de type diamant (DLC) |
Matériaux PVD courants | TiN, CrN, AlCr, ZnSn, ITO | Décoration, outils industriels, revêtements optiques, électronique |
Supports | Métaux, plastiques, céramiques, verre | Aérospatiale, automobile, électronique, applications décoratives |
Techniques PVD | Evaporation, pulvérisation cathodique | Revêtements personnalisés pour la résistance à l'usure, la résistance à la corrosion et les besoins optiques |
Vous êtes intéressé par des revêtements PVD personnalisés pour votre industrie ? Contactez nous dès aujourd'hui pour en savoir plus !