Le dépôt physique en phase vapeur (PVD) est une technique de revêtement polyvalente utilisée pour déposer des couches minces de divers matériaux sur des substrats.Le processus consiste à vaporiser un matériau solide dans le vide, puis à le condenser sur un substrat pour former un film mince.Le procédé PVD permet de déposer une large gamme de matériaux, notamment des métaux, des alliages, des céramiques et même certains matériaux organiques.Le choix du matériau dépend des propriétés souhaitées du revêtement, telles que la dureté, la résistance à la corrosion, la conductivité électrique ou les propriétés optiques.Les matériaux couramment utilisés en PVD sont le titane, le zirconium, l'aluminium, l'acier inoxydable, le cuivre, l'or et divers nitrures, carbures et oxydes.En outre, les substrats doivent être compatibles avec le vide et un prétraitement est souvent nécessaire pour garantir une bonne adhérence et une bonne qualité de film.
Explication des points clés :
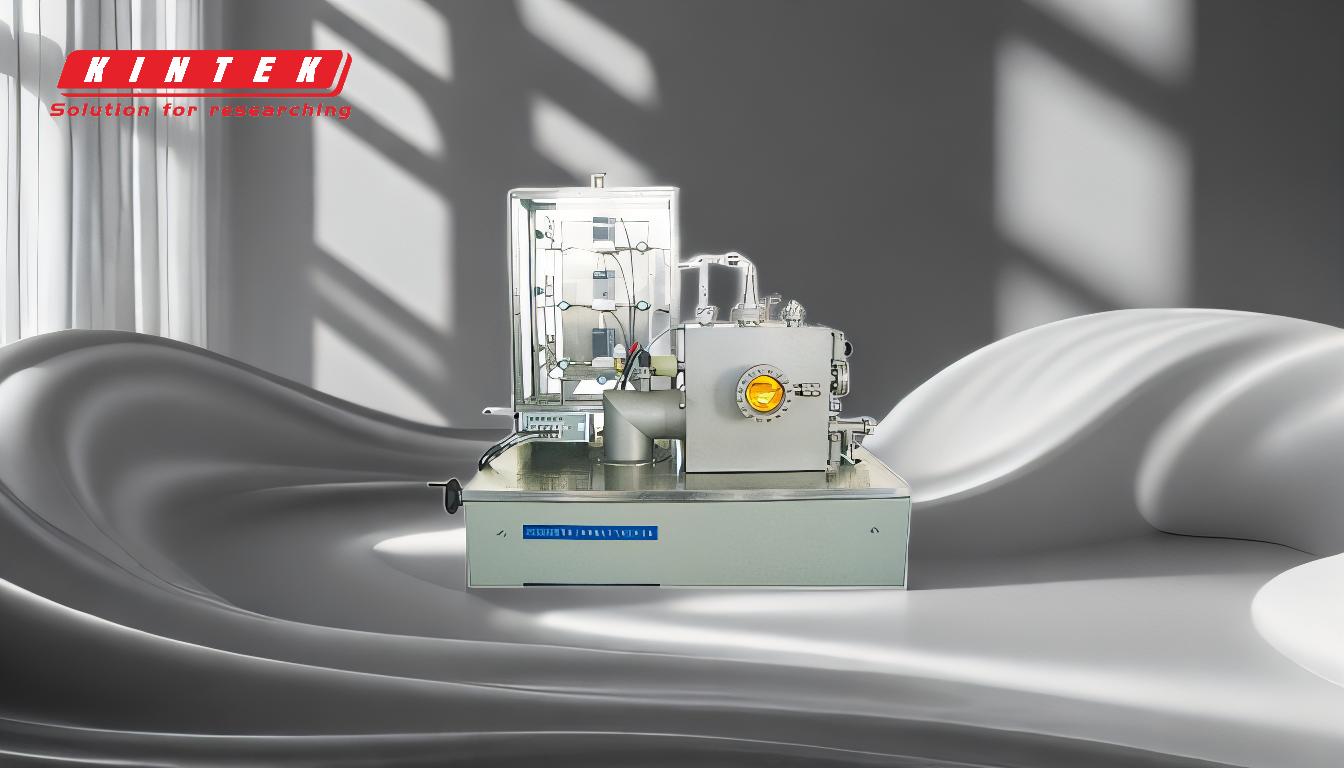
-
Types de matériaux utilisés pour le dépôt en phase vapeur (PVD):
- Métaux:Le dépôt en phase vapeur est couramment utilisé pour déposer des métaux tels que le titane, le zirconium, l'aluminium, l'acier inoxydable, le cuivre, l'or, le chrome, le nickel, l'étain, le platine, le palladium et le tantale.Ces métaux sont choisis pour leurs propriétés spécifiques, telles que la résistance à la corrosion, la conductivité électrique ou l'attrait esthétique.
- Alliages:Le dépôt en phase vapeur peut également déposer des alliages, qui sont des combinaisons de métaux conçues pour obtenir des propriétés spécifiques.Les alliages nickel-chrome et cuivre-nickel en sont des exemples.
- Les céramiques:Les matériaux céramiques, y compris les nitrures (par exemple, le nitrure de titane), les carbures (par exemple, le carbure de silicium) et les oxydes (par exemple, le dioxyde de silicium), sont souvent déposés par dépôt en phase vapeur (PVD).Ces matériaux sont appréciés pour leur dureté, leur résistance à l'usure et leur stabilité thermique.
- Semi-conducteurs et isolants:Le procédé PVD permet de déposer des matériaux semi-conducteurs tels que le dioxyde de silicium (SiO2) et l'oxyde d'indium et d'étain (ITO), qui sont utilisés dans des applications électroniques et optiques.Les isolants tels que le verre peuvent également être revêtus par PVD.
- Matériaux organiques:Bien que moins courants, certains matériaux organiques peuvent être déposés par PVD, bien que cela soit généralement plus difficile en raison de leur faible stabilité thermique.
-
Adéquation des matériaux au dépôt en phase vapeur (PVD):
- Exigences en matière de vaporisation:Les matériaux utilisés pour le dépôt en phase vapeur doivent pouvoir être vaporisés ou bombardés pour former une vapeur.Cela implique généralement de chauffer le matériau à des températures élevées ou d'utiliser des techniques telles que la pulvérisation cathodique.
- Compatibilité avec le vide:Le matériau doit être stable sous vide.Certains matériaux peuvent se décomposer ou réagir sous vide, ce qui les rend impropres au dépôt en phase vapeur.
- Adhésion et qualité du film:La qualité du film déposé, y compris son adhérence au substrat, est essentielle.Une mauvaise adhérence ou une mauvaise qualité du film peut entraîner une délamination ou d'autres défauts.
-
Considérations relatives au support:
- Compatibilité avec le vide:Les substrats doivent être compatibles avec le vide ou traités pour le devenir.Les substrats les plus courants sont les aciers à outils, le verre, le laiton, le zinc et le plastique ABS.
- Prétraitement:Les substrats sont souvent prétraités pour améliorer l'adhérence et la qualité du film.Il peut s'agir d'un nettoyage, d'un revêtement organique ou d'un dépôt électrolytique de matériaux tels que le nickel et le chrome.
-
Applications des matériaux revêtus par PVD:
- Aérospatiale et électronique:L'or est souvent utilisé dans l'électronique aérospatiale pour son excellente conductivité et sa résistance à la corrosion.
- Outillage et outils de coupe:Le nitrure de titane et d'autres revêtements durs sont utilisés pour prolonger la durée de vie des outils de coupe et des moules.
- Revêtements optiques et décoratifs:Le procédé PVD est utilisé pour appliquer des revêtements décoratifs et fonctionnels sur des articles tels que les montres, les bijoux et les pièces automobiles.
- Fabrication de semi-conducteurs:Le dépôt en phase vapeur est utilisé pour déposer des couches minces de matériaux tels que le dioxyde de silicium et l'oxyde d'indium et d'étain dans la production de semi-conducteurs et d'écrans.
-
Limites et défis:
- Limites matérielles:Tous les matériaux ne conviennent pas au dépôt en phase vapeur (PVD).Certains matériaux ne se vaporisent pas efficacement ou se dégradent sous les températures élevées ou les conditions de vide requises.
- Épaisseur du film:Le dépôt en phase vapeur (PVD) dépose généralement des films minces, dont l'épaisseur varie de quelques nanomètres à plusieurs centaines de nanomètres.L'obtention de revêtements plus épais peut nécessiter plusieurs cycles de dépôt.
- Coût et complexité:Les équipements et les procédés PVD peuvent être coûteux et complexes, en particulier pour les applications à grande échelle ou de haute précision.
En résumé, le dépôt en phase vapeur est une technique de revêtement très polyvalente, capable de déposer une large gamme de matériaux, notamment des métaux, des alliages, des céramiques et certains matériaux organiques.Le choix du matériau dépend des propriétés souhaitées du revêtement et de l'application spécifique.Les substrats doivent être compatibles avec le vide et nécessitent souvent un prétraitement pour garantir une bonne adhérence et une bonne qualité de film.Si le dépôt en phase vapeur offre de nombreux avantages, il présente également des limites, notamment en ce qui concerne l'adéquation des matériaux, l'épaisseur du film et le coût.
Tableau récapitulatif :
Catégorie | Matériaux | Propriétés principales |
---|---|---|
Métaux | Titane, zirconium, aluminium, acier inoxydable, cuivre, or, chrome, etc. | Résistance à la corrosion, conductivité électrique, attrait esthétique |
Alliages | Nickel-chrome, Cuivre-nickel | Propriétés sur mesure pour des applications spécifiques |
Céramiques | Nitrure de titane, carbure de silicium, dioxyde de silicium | Dureté, résistance à l'usure, stabilité thermique |
Semi-conducteurs | Dioxyde de silicium (SiO2), oxyde d'indium et d'étain (ITO) | Utilisé dans des applications électroniques et optiques |
Matériaux organiques | Utilisation limitée en raison des problèmes de stabilité thermique | Applications spécialisées nécessitant des revêtements organiques |
Prêt à explorer les revêtements PVD pour votre projet ? Contactez nos experts dès aujourd'hui pour commencer !