L'objectif des procédés de fabrication à base de poudre
Table des matières
- L'objectif des procédés de fabrication à base de poudre
- Le processus de pressage isostatique à froid (CIP)
- Le processus de pressage isostatique à chaud (HIP)
- L’opportunité d’un prétraitement en une seule étape des constructions via la fabrication additive multi-matériaux
- L'utilisation de la technologie de dépôt sélectif de Kintek dans le pressage isostatique
- Le potentiel d’une approche similaire pour les pièces traitées à l’aide de HIP
- Conclusion : le pont du dépôt sélectif de poudre entre la nouvelle fabrication additive et la fabrication traditionnelle
- Le potentiel du dépôt sélectif de poudre pour créer un pont entre la nouvelle technologie de fabrication additive et la fabrication traditionnelle de composants haut de gamme
- La possibilité d'apaiser l'anxiété de l'industrie concernant les articles produits via la fabrication additive grâce à cette approche
L'objectif de la plupart des procédés de fabrication à base de poudre
L'objectif de la plupart des procédés de fabrication à base de poudres , tels que la métallurgie des poudres (PM), est de produire des pièces denses avec moins de 1 % de porosité sans faire fondre la matière première. La poudre libre utilisée dans ces procédés a généralement une faible densité d'empilement, avec une densité maximale théorique de seulement 64 % pour des particules parfaitement sphériques empilées de manière aléatoire. Cependant, en utilisant des distributions granulométriques de poudre appropriées ou des poudres déformables, des densités de tassement supérieures à 90 % peuvent être obtenues.
Les limites du pressage uniaxial
Pour obtenir des résultats satisfaisants dans les procédés de fabrication à base de poudres, l’application d’une pression est cruciale. Le pressage uniaxial, où la pression est appliquée dans une direction, est couramment utilisé. Cependant, cette méthode présente des limites, notamment pour les pièces épaisses. Cela tend à entraîner des différences de densité dans le sens du pressage, ce qui peut affecter la qualité de la pièce finale.
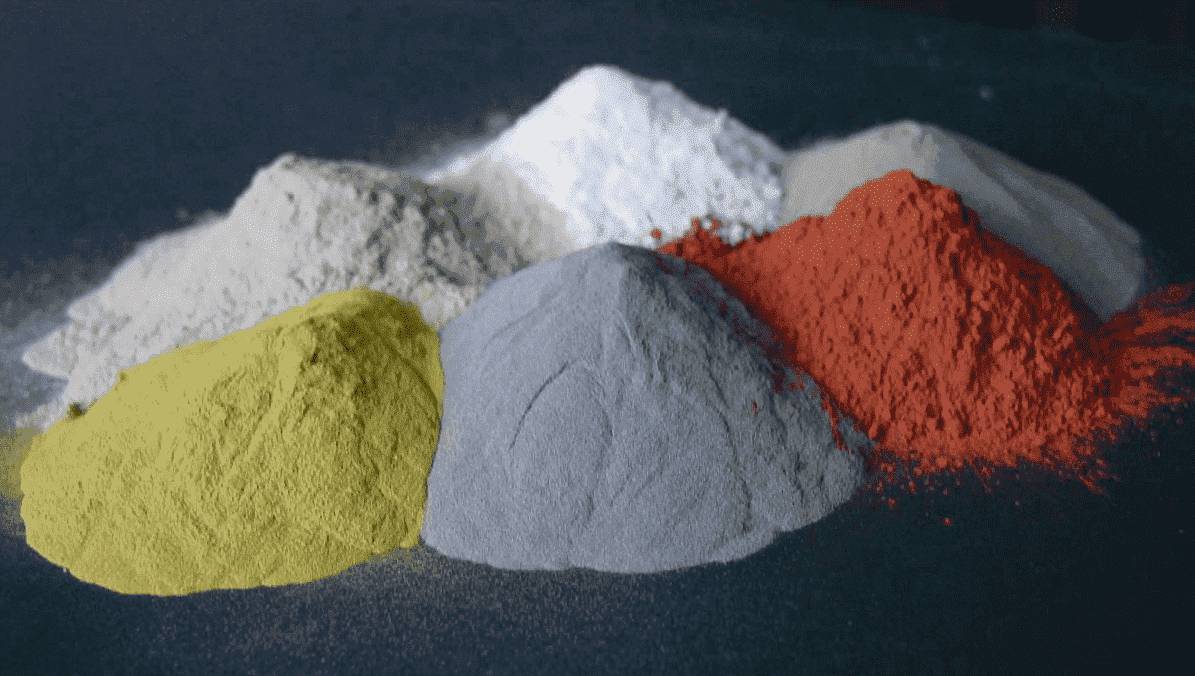
La solution : le pressage isostatique
Pour surmonter les limites du pressage uniaxial, le pressage isostatique est souvent utilisé pour les pièces en vrac. Le pressage isostatique est une technique de traitement des poudres qui utilise la pression d'un fluide pour compacter la pièce. Les poudres métalliques sont placées dans un récipient souple, qui sert de moule à la pièce. La pression du fluide est exercée sur toute la surface extérieure du récipient, ce qui l'amène à presser et à former la poudre selon la géométrie souhaitée. Contrairement au pressage uniaxial, le pressage isostatique applique une pression dans toutes les directions, ce qui entraîne une répartition plus uniforme de la densité.
Processus alternatifs
Pressage isostatique
Le pressage isostatique est un procédé de fabrication à base de poudre largement utilisé qui applique une pression uniforme pour consolider les poudres ou réparer les défauts des pièces moulées. Il peut être utilisé pour une gamme de matériaux, notamment la céramique, les métaux, les composites, les plastiques et le carbone. Le processus consiste à placer la poudre dans un moule flexible, à la sceller et à la soumettre à une pression provenant de toutes les directions. Le pressage isostatique offre des avantages uniques pour les applications céramiques et réfractaires, car il permet la formation de formes de produits avec des tolérances précises, réduisant ainsi le besoin d'usinage coûteux.
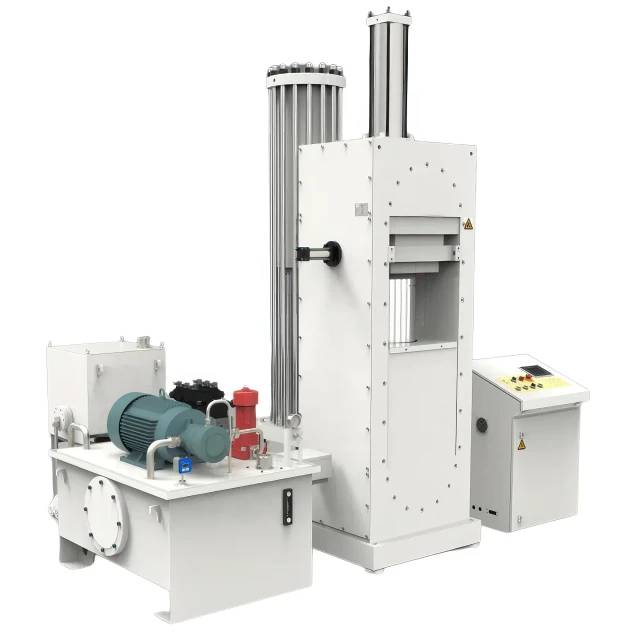
Traitement des métaux en poudre
Le traitement des métaux en poudre est une autre technique de fabrication à base de poudre qui permet de produire des produits dont les propriétés peuvent surpasser celles des matériaux alliés. Dans ce processus, des poudres métalliques ou céramiques, ainsi qu'un liant, sont mélangées pour former un mélange qui peut être pressé dans les formes souhaitées. Pour les pièces plus grandes, le mélange est versé dans des moules. Ce processus est couramment utilisé dans la production de produits tels que les forets en composite de diamant polycristallin (PDC) pour le forage de puits profonds, où le mélange est pressé et cuit pour donner des produits de forme proche de la valeur nette.
Progrès dans la métallurgie des poudres
Les procédés à base de poudre, tels que le compactage de poudre, le pressage isostatique à chaud de poudre (P-HIP), le moulage par injection de métal (MIM) et le frittage par plasma étincelant, sont de plus en plus utilisés pour fabriquer des produits en forme de filet (NS) et quasi-net. forme (NNS) des composants d’alliages hautes performances. Ces processus visent à fabriquer des pièces qui correspondent étroitement à la géométrie finale requise, réduisant ainsi les coûts, les délais et le gaspillage de matériaux en minimisant les étapes du processus telles que l'usinage et la finition. Les technologies à base de poudre ont la capacité de produire des pièces dont les propriétés de performance peuvent égaler, voire améliorer, celles des processus de fabrication traditionnels comme le moulage. Cela est dû à des facteurs tels que la microstructure uniforme associée aux matériaux particulaires et aux progrès de la métallurgie des poudres qui permettent de produire une large gamme d'alliages hautes performances sous forme de poudre.
En conclusion, l’objectif des procédés de fabrication à base de poudre est de produire des pièces denses avec des densités de tassement élevées et une porosité minimale. Le pressage isostatique est une technique précieuse utilisée pour surmonter les limites du pressage uniaxial, offrant une répartition plus uniforme de la densité dans les pièces épaisses. De plus, des procédés alternatifs tels que le traitement des poudres métalliques et les progrès de la métallurgie des poudres ont élargi les capacités de fabrication à base de poudres, permettant la production de formes complexes et d'alliages hautes performances.
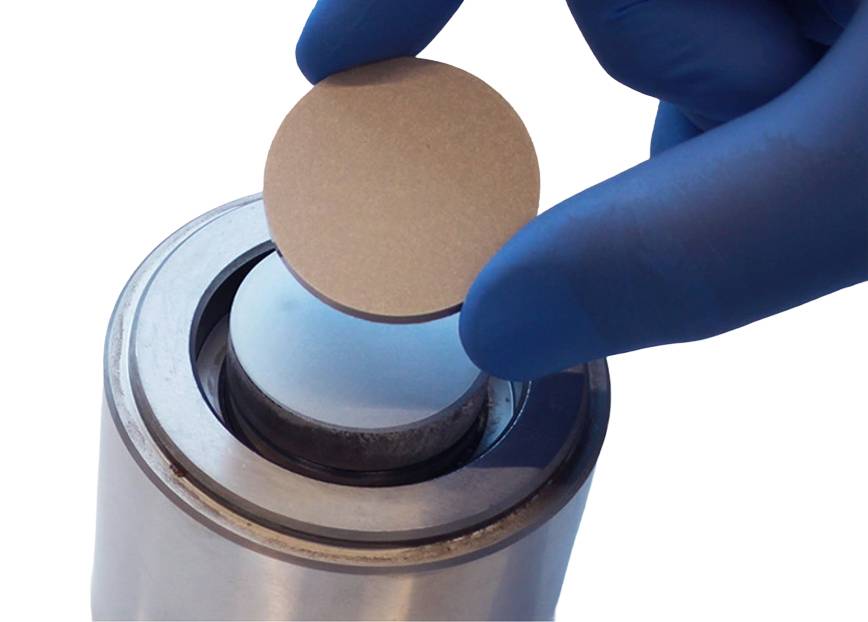
Le processus de pressage isostatique à froid (CIP)
Le processus de CIP
Le pressage isostatique à froid (CIP) est une méthode de traitement des matériaux utilisée pour façonner et compacter des poudres en composants de différentes tailles et formes. Il s’agit de placer la poudre ou une partie verte de faible densité dans un récipient flexible scellé et de la plonger dans un liquide à l’intérieur d’un récipient sous pression. Une pression de plusieurs milliers de bars est appliquée, comprimant le compact vert aussi près que possible de sa densité d'emballage maximale. Cette densité initiale plus élevée accélère la consolidation jusqu'à la densité finale dans le cycle thermique.
Le CIP utilise le principe proposé par le scientifique français Blaise Pascal, selon lequel un changement de pression dans un fluide incompressible enfermé est transmis sans diminution à chaque partie du fluide et à la surface de son récipient. Les matériaux en poudre sont scellés dans un moule de formage à faible résistance à la déformation, tel qu'un sac en caoutchouc, et une pression liquide est appliquée pour comprimer uniformément le corps moulé sur toute sa surface.
Le pressage de moules métalliques est une méthode de pressage similaire au CIP. Dans cette méthode, les matériaux en poudre sont remplis dans un espace délimité par un moule métallique et un poinçon inférieur. Ils sont ensuite compressés en réduisant la distance entre les poinçons supérieur et inférieur.
Les avantages d'une densité initiale élevée pour accélérer la consolidation jusqu'à la densité finale dans le cycle thermique
La densité initiale élevée obtenue grâce au procédé CIP offre plusieurs avantages dans la consolidation des poudres. Ces avantages comprennent :
Compression prévisible pendant le processus de frittage ultérieur : un compactage élevé et une densité uniforme assurent une compression prévisible pendant le processus de frittage, ce qui se traduit par une densité finale constante et fiable.
Capacité à traiter des formes grandes, complexes et parfaites : le CIP permet le traitement de formes grandes et complexes avec une grande précision. Cela permet d'économiser du temps et de l'argent lors des processus de post-traitement.
Génération de pièces au rapport hauteur/largeur supérieur à 2:1, en maintenant des densités uniformes dans tout le composant.
Résistance verte pour la manipulation et le traitement en cours de processus : Le compact vert formé par CIP a une résistance suffisante pour subir une manipulation et un traitement en cours de processus, réduisant ainsi les coûts de production.
Dans l'ensemble, le processus CIP offre une mise en forme et un compactage efficaces et efficients des poudres, ce qui donne lieu à des composants de haute qualité avec les densités souhaitées. Sa polyvalence et sa capacité à traiter divers matériaux en font une méthode précieuse dans des secteurs tels que la fabrication de précision, l'aérospatiale, la défense et l'automobile.
Selon un rapport de DataIntelo, le marché mondial des équipements de pressage isostatique à froid (CIP) devrait croître à un TCAC substantiel au cours de la période de prévision, 2020-2026. La demande croissante de produits traités par CIP dans des secteurs tels que la fabrication de précision, l'aérospatiale, la défense et l'automobile est à l'origine de cette croissance.
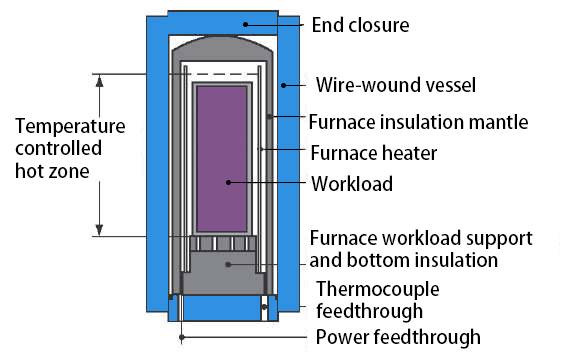
Le processus de pressage isostatique à chaud (HIP)
L’avantage du frittage uniaxial assisté par pression dans la HIP
Une pression peut également être appliquée pendant le cycle thermique. Dans le frittage uniaxial assisté par pression, seuls des produits en forme de plaque peuvent généralement être produits. Pour les pièces plus complexes, le pressage isostatique à chaud (HIP) est utilisé. Le HIP est réalisé dans une atmosphère gazeuse, la principale exigence est donc que la surface extérieure des pièces traitées soit au départ étanche aux gaz. En tant que tel, ce processus peut être utilisé pour produire des composants en scellant sous vide de la poudre de pièces dans une coque en acier doux. L'application uniforme d'une pression garantit que la forme est conservée à mesure que la pièce et la coque rétrécissent. Les poudres traitées à l'aide d'une stratégie HIP ne sont généralement pas compatibles avec les processus de fusion, soit nécessitant des températures excessives, soit produisant des microstructures défavorables. Néanmoins, les efforts supplémentaires déployés pour traiter ces matériaux indiquent leur utilisation dans des applications exigeantes où même un faible niveau de porosité n'est pas acceptable.
Les exigences et les résultats du processus HIP
Le pressage isostatique à chaud (HIP) est l'application simultanée d'une température et d'une pression élevées sur des métaux et d'autres matériaux pendant une durée spécifiée afin d'améliorer leurs propriétés mécaniques. Dans l'unité HIP, un four à haute température est enfermé dans un récipient sous pression. La température, la pression et la durée du processus sont toutes contrôlées avec précision pour obtenir les propriétés optimales du matériau. Les pièces sont chauffées dans un gaz inerte, généralement de l'argon, qui applique une pression « isostatique » uniformément dans toutes les directions. Cela fait que le matériau devient « plastique », permettant aux vides de s'effondrer sous la pression différentielle. Les surfaces des vides se lient par diffusion pour éliminer efficacement les défauts atteignant une densité proche de la théorie tout en améliorant les propriétés mécaniques des pièces telles que les pièces moulées à modèle perdu.
L'incompatibilité des poudres traitées selon une stratégie HIP avec les procédés de fusion
Le pressage isostatique à chaud (HIP) est un processus de traitement de matériaux qui implique l'utilisation de chaleur et de pression pour améliorer les propriétés physiques d'un matériau. Elle est généralement réalisée sur les métaux et la céramique. Lorsque l’un ou l’autre de ces types de matériaux est exposé à la chaleur et à la pression, leurs propriétés physiques changent. HIP est un processus efficace pour éliminer les défauts des pièces fabriquées de manière additive à base de poudre, générant un matériau 100 % dense avec des propriétés de fatigue et une ductilité améliorées.
Secteurs HIP s'est imposé depuis qu'il a atteint une échelle comparable à celle des pièces moulées et forgées et est devenu reconnu comme un concurrent économique du forgeage et de la fonderie dans des applications nécessitant des coûts de matières premières plus élevés. Il existe actuellement trois principaux secteurs HIP : le pétrole et le gaz, la production d'électricité et l'aérospatiale. La production d’un composant PM HIP est plus simple et plus courte que les processus métallurgiques conventionnels habituels. Le coût du HIP par rapport aux coûts de l’énergie et des matériaux a diminué de 65 % au cours des deux dernières décennies.
Introduction Le pressage isostatique à chaud (HIP) est un procédé permettant de densifier des poudres ou des pièces coulées et frittées dans un four à haute pression (100-200 MPa) et à des températures de 900 à 1250°C, par exemple pour les aciers et superalliages. La pression du gaz agit uniformément dans toutes les directions pour offrir des propriétés isotropes et une densification à 100 %. Il offre de nombreux avantages et est devenu une alternative viable et performante aux processus conventionnels tels que le forgeage, le moulage et l'usinage dans de nombreuses applications.
Frittage/Métallurgie des poudres : technologie de pressage isostatique à chaud (HIP)
Le pressage isostatique à chaud est passé du laboratoire de recherche à la production régulière à grande échelle au cours des 50 dernières années. L’avenir de cette technologie s’annonce prometteur alors que la demande de propriétés matérielles améliorées, l’utilisation de matériaux en poudre et le désir de produire des pièces de forme nette ou quasi nette s’accélèrent.
Source de température du four chauffée par résistance à l'intérieur de la cuve
Le procédé HIP, initialement connu sous le nom de liaison sous pression de gaz, a été développé au laboratoire du Battelle Memorial Institute à Columbus, Ohio, en 1955. L'application originale était la liaison par diffusion de gaines de zirconium sur des alliages zirconium-uranium pour les éléments combustibles nucléaires. À peu près à la même époque, ASEA-Suède utilisait l'application de pression isostatique pour compacter les premiers diamants synthétiques. Le pressage isostatique à chaud (HIP) est un procédé de fabrication utilisé pour réduire la porosité des métaux et augmenter la densité de nombreux matériaux céramiques. Cela améliore les propriétés mécaniques et la maniabilité du matériau.
Qu'est-ce que le pressage isostatique à chaud (HIP) ?
Le pressage isostatique à chaud (HIP), ou « Hipp'ing », est l'application simultanée de chaleur et de haute pression sur des matériaux. Ce procédé est idéal pour améliorer les caractéristiques de votre produit fabriqué additivement en supprimant la porosité jusqu'à 100%.
Aujourd’hui, ce procédé est déjà utilisé dans l’amélioration des produits fabriqués de manière additive. Après Hipp'ing, le résultat est l'élimination des vides internes (c'est-à-dire la porosité) et une microstructure améliorée, conduisant à des propriétés mécaniques considérablement améliorées. HIP peut être appliqué à une large gamme d’alliages, notamment le titane, les aciers, l’aluminium, le cuivre et le magnésium.
L’opportunité d’un prétraitement en une seule étape des constructions via la fabrication additive multi-matériaux
Les avantages potentiels de la fabrication additive multi-matériaux dans les processus CIP et HIP
La fabrication additive multi-matériaux offre une gamme d'avantages potentiels dans les processus de consolidation par pressage isostatique (CIP) et de pressage isostatique à chaud (HIP). En utilisant le dépôt sélectif de poudre, cette approche peut combler le fossé entre la nouvelle technologie de fabrication additive et les méthodes de fabrication traditionnelles de composants haut de gamme. En consolidant les pièces à l’aide d’une technologie établie, cela peut contribuer à atténuer les inquiétudes concernant la qualité et la fiabilité des articles produits par fabrication additive.
L’un des principaux avantages de la fabrication additive multi-matériaux est la diminution des coûts de fabrication. Avec une complexité accrue des pièces, moins d’étapes de traitement et des délais réduits, les fabricants peuvent réaliser des économies. Ceci est particulièrement avantageux pour la production de petites séries ou de prototypes, où l'efficacité et la rentabilité sont cruciales.
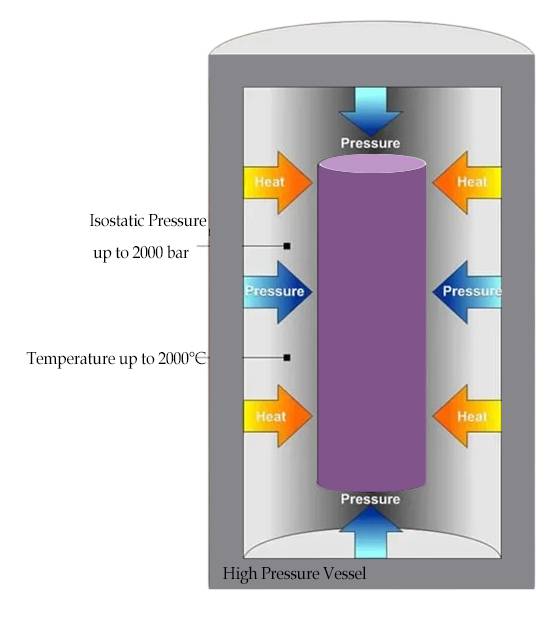
La diminution potentielle des coûts de fabrication avec une complexité accrue des pièces, moins d'étapes de traitement et du temps
Le recours à la fabrication additive multi-matériaux peut entraîner une diminution des coûts de fabrication. Les méthodes traditionnelles de fabrication soustractive ont des limites géométriques qui ne s’appliquent plus à la fabrication additive. Cela signifie que des formes et des conceptions complexes peuvent être créées sans augmenter considérablement les coûts de production. De plus, la possibilité de créer plusieurs versions du même produit sans faire varier le coût de production peut réduire davantage les coûts.
Un autre avantage non négligeable de la fabrication additive multi-matériaux
La transformation est la réduction drastique des déchets de transformation. En ajoutant du matériau étape par étape jusqu'à l'obtention de l'objet souhaité, le gaspillage est minime par rapport aux méthodes de fabrication soustractives traditionnelles. Cela réduit non seulement les coûts, mais contribue également à un processus de fabrication plus durable.
Le monde de la fabrication additive métallique connaît une augmentation notable de l'utilisation de méthodes telles que le moulage par injection de métal (MIM), le jet de liant (BJ) et la modélisation par dépôt fondu (FDM). Ces méthodes offrent des avantages uniques en termes de coût, de flexibilité de conception et de propriétés des matériaux.

Dans la fabrication additive métallique, le déliantage thermique est un processus crucial après l’impression. Il s’agit d’éliminer les liants et autres additifs pour obtenir une pièce métallique totalement dense. Le déliantage correct des pièces produites par fabrication additive métallique est essentiel pour obtenir les propriétés mécaniques et la précision dimensionnelle souhaitées.
Les processus CIP et HIP utilisent des constructions multi-matériaux. Le CIP implique l'utilisation de coques en polymère avec des poudres céramiques, tandis que le HIP utilise un boîtier en tôle d'acier doux soudé avec des alliages de métallurgie des poudres haut de gamme. Ces méthodes présentent une opportunité pour le prétraitement en une seule étape des constructions via la fabrication additive multi-matériaux.
Cette approche est particulièrement bénéfique pour la production de petites séries ou de prototypes, car elle permet d'augmenter la complexité des pièces avec moins d'étapes de traitement et moins de temps. En tirant parti des avantages de la fabrication additive multi-matériaux, les fabricants peuvent améliorer l’efficacité et la rentabilité de leurs processus de production.
La base industrielle du procédé HIP se développe rapidement en raison de la demande croissante de propriétés améliorées des matériaux et de l'utilisation de matériaux en poudre. De plus, les progrès de l'équipement HIP, les délais de traitement plus courts et l'amélioration de la rentabilité font du processus HIP un choix viable pour une large gamme de matériaux. Cela renforce encore le potentiel d’un prétraitement en une seule étape des constructions via la fabrication additive multi-matériaux.
En conclusion, la fabrication additive multi-matériaux offre des opportunités significatives pour améliorer l’efficacité, réduire les coûts et réaliser des conceptions complexes dans les processus CIP et HIP. En tirant parti des avantages de cette technologie, les fabricants peuvent rester à la pointe de l'innovation et répondre aux exigences du marché concurrentiel d'aujourd'hui.
L'utilisation de la technologie de dépôt sélectif de Kintek dans le pressage isostatique
Le dépôt simultané de différents matériaux
Le pressage isostatique est une méthode de compactage de poudre dans un récipient en élastomère immergé dans un fluide à haute pression. Traditionnellement, ce procédé était principalement utilisé pour les céramiques et les métaux. Cependant, les progrès récents dans la technologie de dépôt sélectif, tels que l'approche innovante de Kintek, ont ouvert de nouvelles possibilités pour le pressage isostatique.
La technologie de dépôt sélectif de KinTek permet le dépôt simultané de différents matériaux. Cela signifie qu’au lieu d’utiliser un seul matériau en poudre, plusieurs matériaux peuvent être déposés couche par couche. Cela ouvre une gamme de possibilités pour créer des pièces complexes multi-matériaux aux propriétés uniques.
Création d'une coque polymère façonnée et étanche aux liquides entourant la poudre céramique non compactée
L'un des principaux avantages de la technologie de dépôt sélectif de KinTek dans le pressage isostatique est la capacité de créer une coque polymère façonnée et étanche aux liquides entourant la poudre céramique non compactée. Cette coque agit comme une barrière empêchant la poudre céramique de se disperser lors du processus de pressage isostatique.
En utilisant le dépôt sélectif pour créer cette coque, il est possible d'obtenir une densité verte uniforme même pour les pièces à rapport hauteur/diamètre élevé. Ceci est particulièrement important pour les applications où le contrôle dimensionnel est crucial, comme dans les industries aérospatiale ou automobile.
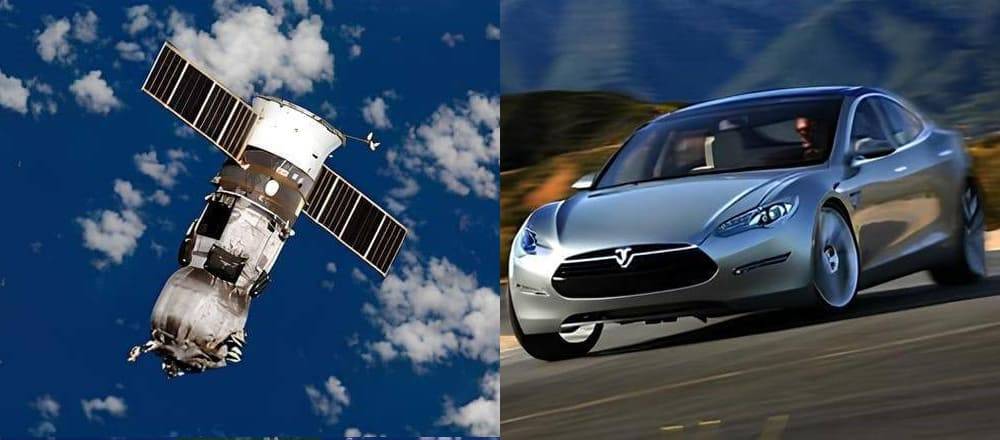
Le transport et le placement faciles de la construction à l'intérieur d'une machine CIP
Un autre avantage de la technologie de dépôt sélectif de est la facilité de transport et de placement de la construction à l'intérieur d'une machine de pressage isostatique à froid (CIP). La construction, constituée d'une coque polymère façonnée remplie de poudre céramique non compactée, peut être facilement manipulée et positionnée dans la machine CIP.
Cette facilité de transport et de placement augmente non seulement l'efficacité, mais réduit également le risque de dommages à la construction pendant le processus de chargement. Il permet un processus de pressage isostatique plus rationalisé et plus fiable, garantissant des résultats cohérents et des pièces de haute qualité.
En conclusion, la technologie de dépôt sélectif de offre des possibilités intéressantes pour le pressage isostatique. Le dépôt simultané de différents matériaux, la création d'une coque polymère façonnée et étanche aux liquides, ainsi que le transport et le placement faciles de la construction à l'intérieur d'une machine CIP contribuent tous à l'avancement de ce processus de fabrication. Avec un développement et un perfectionnement ultérieurs, la technologie de a le potentiel de révolutionner la façon dont nous produisons des pièces complexes et multi-matériaux avec un contrôle dimensionnel et des performances améliorés.
Le potentiel d’une approche similaire pour les pièces traitées à l’aide de HIP
Co-dépôt d'un acier à outils doux et d'un alliage spécifique PM à l'aide d'un système de dépôt sélectif de poudre
Pour les pièces qui doivent être traitées à l’aide de HIP, une approche similaire pourrait être utilisée. Un acier à outils doux et un alliage spécifique PM pourraient être co-déposés à l'aide d'un système de dépôt sélectif de poudre, et seul l'extérieur de l'acier à outils devrait être consolidé. Comme l'alliage PM n'a pas besoin d'être fondu, il est facile d'imaginer produire un boîtier prérempli avec une tuyauterie qui permettrait de sceller par soudure ce boîtier sous vide, tout comme dans les pièces produites par HIP en tôle soudée. Le reste du traitement HIP peut alors suivre la voie traditionnelle.
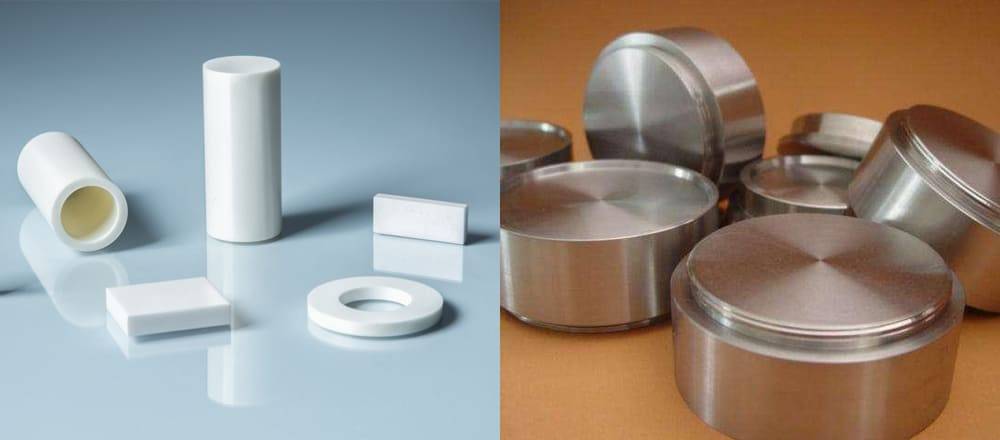
Réalisation d'un boîtier prérempli avec tuyauterie pour le scellement des soudures sous vide
Une approche similaire au traitement HIP peut être utilisée pour les pièces nécessitant un traitement HIP. En co-dépôt d'un acier à outils doux et d'un alliage spécifique PM à l'aide d'un système de dépôt sélectif de poudre, il est possible de produire un boîtier prérempli avec une tuyauterie pour le scellement des soudures sous vide. Cela permet de consolider l'extérieur de l'acier à outils tout en préservant l'intégrité de l'alliage PM. Le traitement HIP restant peut alors se dérouler comme d'habitude.
La voie traditionnelle du reste du traitement HIP
Après le co-dépôt d'un acier à outils doux et d'un alliage spécifique PM à l'aide d'un système de dépôt sélectif de poudre et la consolidation de l'extérieur de l'acier à outils, le reste du traitement HIP peut suivre la voie traditionnelle. Cela inclut l'utilisation d'une technologie de refroidissement avancée pour améliorer les coûts de traitement et les propriétés finales des matériaux. Grâce à la possibilité de refroidir plus rapidement grâce au gaz argon et aux systèmes de refroidissement internes, les cycles HIP peuvent être considérablement réduits, ce qui entraîne des économies et une meilleure qualité des pièces.
L’utilisation du HIP dans diverses industries s’est avérée très bénéfique. HIP peut être utilisé pour fabriquer une large gamme de composants, y compris des composants métalliques de grande taille et massifs en forme de filet, tels que des pièces pétrolières et gazières et des roues en forme de filet. Il convient également à la production de petits outils de coupe PM HSS et de petites pièces telles que des brackets dentaires. Le procédé a évolué au fil des années pour devenir une méthode performante, de haute qualité et rentable pour produire des composants métalliques et céramiques.
HIPing offre de nombreux avantages, notamment des propriétés mécaniques améliorées, une réduction des rebuts, un usinage minimisé et la capacité de rajeunir les anciennes pièces. Il peut être appliqué sur une variété de matériaux, notamment l’aluminium, l’acier, l’acier inoxydable, le superalliage, le titane et la céramique. Avec les progrès des équipements HIP et des délais de traitement, le processus HIP devient de plus en plus populaire pour une large gamme de matériaux et d'applications.
En conclusion, une approche similaire au traitement HIP peut être appliquée aux pièces nécessitant un traitement HIP. En co-dépôt d'un acier à outils doux et d'un alliage spécifique PM à l'aide d'un système de dépôt sélectif de poudre, il est possible de produire des boîtiers préremplis avec des tuyauteries pour le scellement des soudures sous vide. Cette approche offre de nombreux avantages, notamment une qualité améliorée des pièces, une réduction du temps de traitement et des économies de coûts. Avec les progrès continus de la technologie HIP, le potentiel d’utilisation de cette approche dans diverses industries continue de se développer.
Conclusion : le pont du dépôt sélectif de poudre entre la nouvelle fabrication additive et la fabrication traditionnelle
Le potentiel du dépôt sélectif de poudre pour créer un pont entre la nouvelle technologie de fabrication additive et la fabrication traditionnelle de composants haut de gamme
Le dépôt sélectif de poudre a le potentiel de combler le fossé entre la nouvelle technologie de fabrication additive (FA) et la fabrication traditionnelle de composants haut de gamme. Cette approche tire parti des processus bien compris de traitement sous pression et de cycle thermique déjà disponibles dans l’industrie. En utilisant ces méthodes établies pour consolider les pièces créées via la fabrication additive, cela peut contribuer à atténuer l’anxiété de l’industrie concernant les articles produits grâce à cette nouvelle technologie.
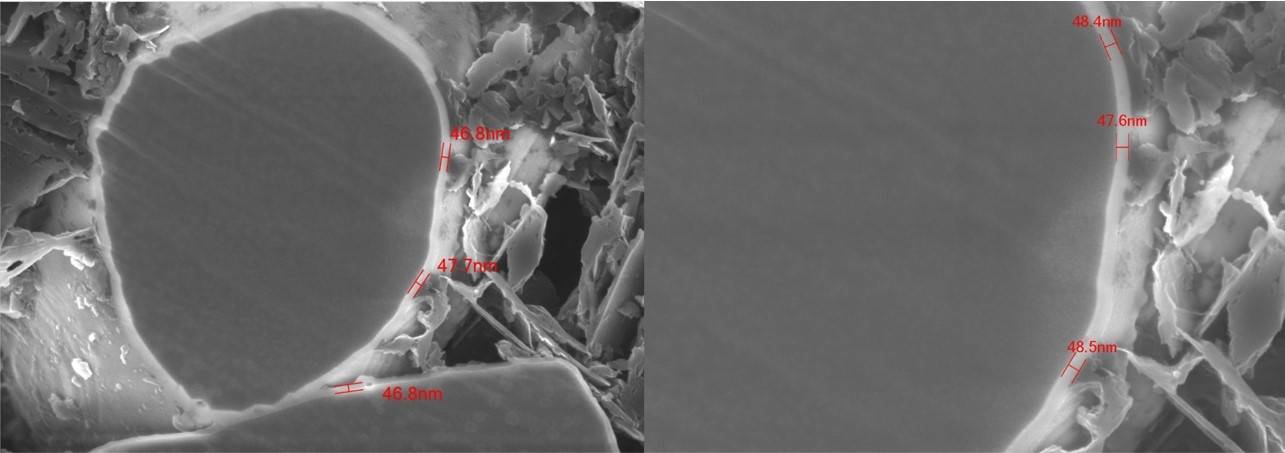
La possibilité d'apaiser l'anxiété de l'industrie concernant les articles produits via la fabrication additive grâce à cette approche
L’une des principales préoccupations de l’industrie en matière de fabrication additive est la qualité et la fiabilité des produits finaux. Les méthodes de fabrication traditionnelles ont été affinées au fil des décennies, et il existe un certain niveau de confiance dans les composants produits par ces processus.
En utilisant le dépôt sélectif de poudre, les pièces créées par FA peuvent être façonnées à l’aide de la nouvelle technologie mais consolidées à l’aide de méthodes établies de longue date. Cela peut contribuer à atténuer une partie de l’anxiété liée à l’utilisation de la fabrication additive pour les composants haut de gamme.
En conclusion, le dépôt sélectif de poudre offre une solution prometteuse pour combler le fossé entre les nouvelles technologies de fabrication additive et la fabrication traditionnelle. En tirant parti des processus et techniques établis dans la fabrication traditionnelle, cela peut contribuer à renforcer la confiance dans les composants produits par la fabrication additive.
CONTACTEZ-NOUS POUR UNE CONSULTATION GRATUITE
Les produits et services de KINTEK LAB SOLUTION ont été reconnus par des clients du monde entier. Notre personnel se fera un plaisir de répondre à toute demande que vous pourriez avoir. Contactez-nous pour une consultation gratuite et parlez à un spécialiste produit pour trouver la solution la plus adaptée aux besoins de votre application !