Le vide joue un rôle essentiel dans les fours de fusion par induction, notamment en améliorant la qualité et les propriétés des métaux fondus.En créant un environnement sous vide, le processus minimise la contamination par les gaz atmosphériques, empêche l'oxydation et élimine les gaz dissous nocifs et les impuretés du métal fondu.Il en résulte une amélioration des propriétés des matériaux, telles que la ténacité, la résistance à la fatigue, la résistance à la corrosion et les propriétés de fluage à haute température.La fusion par induction sous vide est particulièrement importante dans des secteurs tels que l'aérospatiale, le nucléaire et l'électronique, où les métaux et les alliages de haute pureté sont essentiels à la performance et à la sécurité.
Explication des points clés :
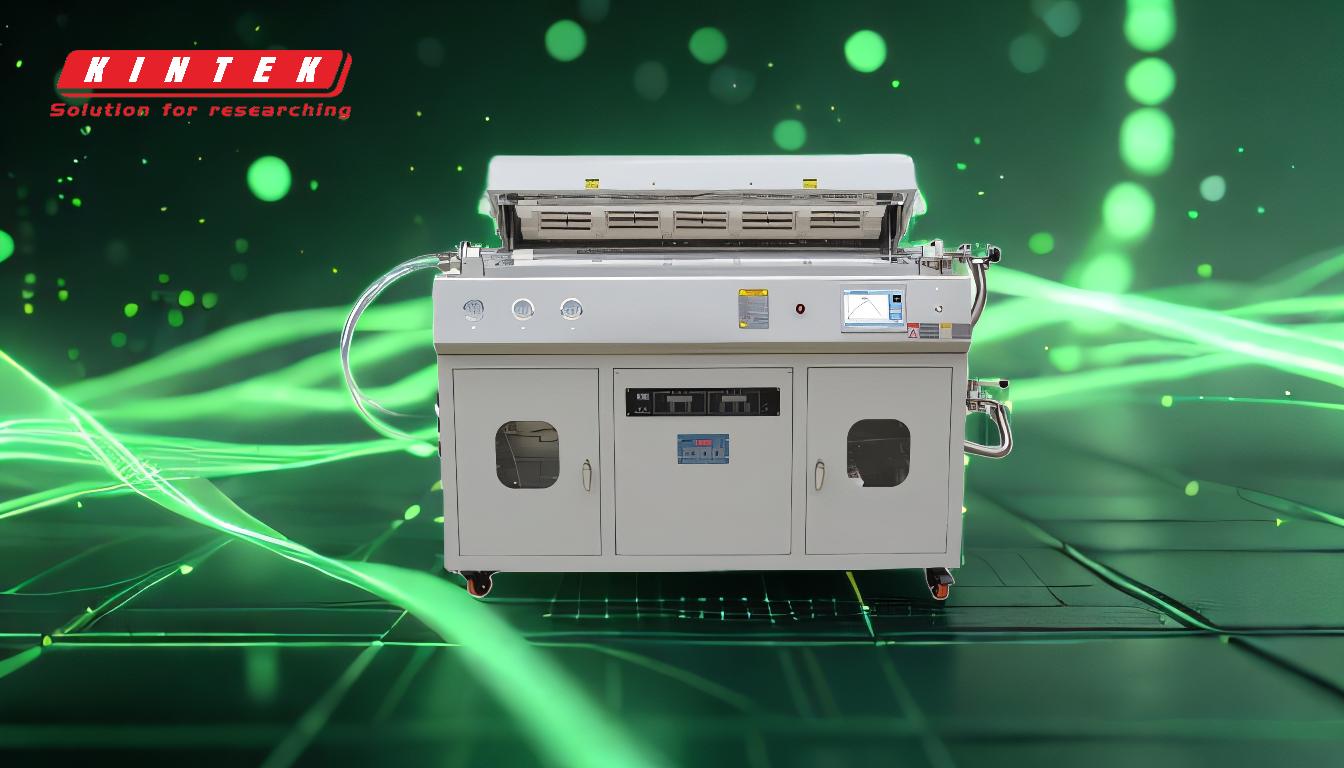
-
Prévention de l'oxydation et de la contamination:
- Dans un environnement sous vide, l'absence de gaz atmosphériques tels que l'oxygène et l'azote empêche l'oxydation et la contamination du métal en fusion.Cela est crucial pour les métaux très réactifs, comme le titane et l'uranium, qui peuvent former des oxydes ou des nitrures indésirables s'ils sont exposés à l'air.Le vide garantit que le métal reste pur et exempt d'inclusions non métalliques, qui peuvent affaiblir le matériau.
-
Élimination des gaz nocifs et des impuretés:
- La fusion par induction sous vide élimine efficacement les gaz dissous tels que l'hydrogène, l'oxygène et l'azote du métal en fusion.Ces gaz peuvent entraîner des défauts tels que la porosité, la fragilité et des propriétés mécaniques réduites dans le produit final.En dégazant le métal sous vide, le processus permet d'obtenir un matériau de meilleure qualité, aux propriétés mécaniques et thermiques améliorées.
-
Propriétés améliorées du matériau:
-
L'environnement sous vide améliore considérablement les propriétés matérielles des métaux fondus.Par exemple :
- Ténacité et résistance à la fatigue:L'élimination des impuretés et des gaz permet d'obtenir une microstructure plus homogène, ce qui améliore la capacité du matériau à résister aux contraintes et à la fatigue.
- Résistance à la corrosion:Les métaux plus purs avec moins d'inclusions sont moins sujets à la corrosion, ce qui les rend adaptés aux environnements difficiles tels que les applications aérospatiales et nucléaires.
- Propriétés de fluage à haute température:La fusion sous vide améliore la capacité du métal à résister à la déformation à des températures élevées, ce qui est essentiel pour les superalliages utilisés dans les moteurs à réaction et les turbines.
-
L'environnement sous vide améliore considérablement les propriétés matérielles des métaux fondus.Par exemple :
-
Applications dans les industries de haute performance:
-
La fusion par induction sous vide est largement utilisée dans les industries qui exigent des matériaux de haute performance, telles que :
- l'aérospatiale:Pour la production de superalliages à base de nickel, de cobalt et de fer utilisés dans les moteurs à réaction et les aubes de turbines.
- Industrie nucléaire:Pour la fusion et le moulage de l'uranium faiblement enrichi en barres de combustible, garantissant la pureté et l'intégrité du combustible nucléaire.
- Électronique:Pour créer des métaux et des alliages de haute pureté utilisés dans les composants électroniques, où même des impuretés mineures peuvent affecter les performances.
-
La fusion par induction sous vide est largement utilisée dans les industries qui exigent des matériaux de haute performance, telles que :
-
Types de fours de fusion à induction sous vide:
-
Les fours de fusion par induction sous vide se présentent sous deux formes principales :
- Type discontinu:Convient aux opérations à petite échelle ou au traitement d'alliages spécifiques nécessitant un contrôle précis de l'environnement de fusion.
- Type semi-continu:Idéal pour la production à grande échelle, permettant l'alimentation continue en matières premières et l'extraction du métal fondu sans rupture du vide.
-
Les fours de fusion par induction sous vide se présentent sous deux formes principales :
-
Polyvalence dans la fusion de divers métaux:
-
Les fours de fusion par induction sous vide peuvent fondre une large gamme de métaux, notamment :
- l'acier:Pour les applications à haute résistance.
- Aluminium et cuivre:Pour les matériaux légers et conducteurs.
- Métaux précieux:Pour les applications nécessitant une pureté et une valeur élevées.
- Alliages de titane:Pour les applications aérospatiales et médicales où la solidité et la résistance à la corrosion sont essentielles.
-
Les fours de fusion par induction sous vide peuvent fondre une large gamme de métaux, notamment :
-
Amélioration de l'ouvrabilité à chaud et des propriétés mécaniques:
- La fusion par induction sous vide améliore l'aptitude au travail à chaud des métaux, ce qui les rend plus faciles à forger, à laminer ou à extruder.Ceci est particulièrement important pour les superalliages, qui sont souvent soumis à des conditions extrêmes lors de leur fabrication et de leur utilisation.Le processus améliore également les propriétés mécaniques telles que la résistance à la traction, la ductilité et la résistance aux chocs, garantissant ainsi que le produit final répond aux normes strictes de l'industrie.
En tirant parti des avantages de la fusion par induction sous vide, les fabricants peuvent produire des métaux et des alliages de haute qualité qui répondent aux exigences des industries de pointe, en garantissant des performances, une fiabilité et une sécurité supérieures.
Tableau récapitulatif :
Principaux avantages de la fusion par induction sous vide | Détails |
---|---|
Prévient l'oxydation et la contamination | Élimine les gaz atmosphériques tels que l'oxygène et l'azote, garantissant ainsi la pureté du métal en fusion. |
Élimination des gaz nocifs et des impuretés | Dégaze l'hydrogène, l'oxygène et l'azote, réduisant ainsi les défauts tels que la porosité et la fragilité. |
Amélioration des propriétés des matériaux | Améliore la ténacité, la résistance à la fatigue, la résistance à la corrosion et les propriétés de fluage à haute température. |
Applications dans les industries de haute performance | Les industries aérospatiale, nucléaire et électronique font appel à la fusion sous vide pour obtenir des métaux de haute pureté. |
Types de fours | Type discontinu pour les opérations à petite échelle ; type semi-continu pour la production à grande échelle. |
Polyvalence dans la fusion des métaux | Capable de fondre l'acier, l'aluminium, le cuivre, les métaux précieux et les alliages de titane. |
Amélioration de l'ouvrabilité à chaud | Améliore les procédés de forgeage, de laminage et d'extrusion des superalliages. |
Exploitez le potentiel de la fusion par induction sous vide pour votre industrie. contactez-nous dès aujourd'hui pour en savoir plus !