Le revêtement par dépôt physique en phase vapeur (PVD) est un procédé sophistiqué utilisé pour déposer des couches minces de matériaux sur un substrat, afin d'en améliorer les propriétés telles que la résistance à l'usure, la dureté et l'aspect esthétique.Le procédé consiste à chauffer un matériau cible jusqu'à ce qu'il se vaporise, puis à déposer la vapeur sur la surface du substrat.Les matériaux couramment utilisés dans les revêtements PVD sont des métaux tels que le titane, le chrome, le tungstène et l'aluminium, qui sont souvent combinés à des gaz réactifs tels que l'azote ou les hydrocarbures pour former des revêtements tels que les nitrures et les carbonitrures.Le procédé PVD est polyvalent, capable d'incorporer une large gamme de matériaux inorganiques et certains matériaux organiques, ce qui le rend adapté à diverses applications, depuis les revêtements décoratifs durables jusqu'aux composants aérospatiaux de haute performance.
Explication des points clés :
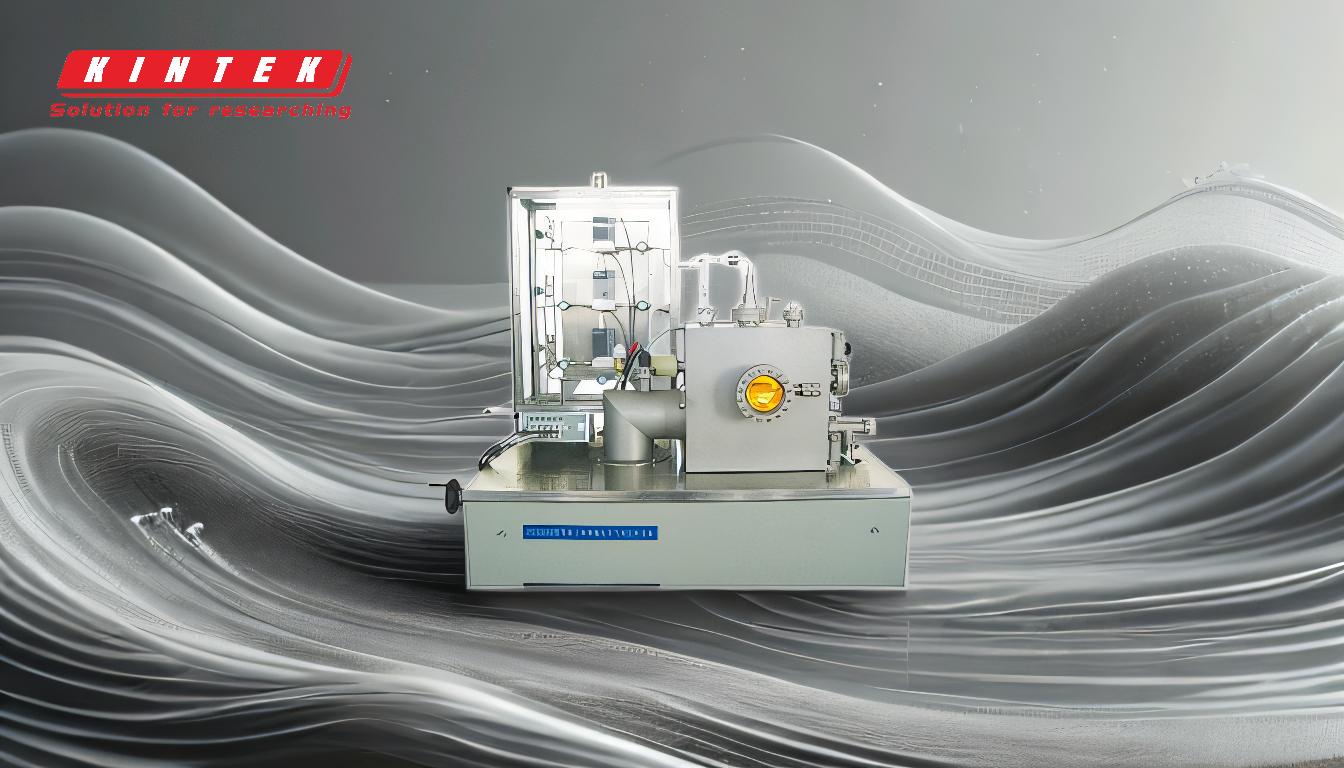
-
Matériaux cibles dans le revêtement PVD:
- Métaux et alliages:Les métaux couramment utilisés dans les revêtements PVD sont le titane, le chrome, le tungstène et l'aluminium.Ces métaux sont choisis pour leurs propriétés spécifiques, telles que la dureté, la résistance à l'usure et la capacité à former des liaisons fortes avec les gaz réactifs.
- Céramiques et composés:Le dépôt en phase vapeur peut également déposer des céramiques et des composés tels que des carbures, des nitrures, des siliciures et des borures.Ces matériaux sont souvent utilisés dans des applications spécialisées exigeant des performances élevées, telles que les composants aérospatiaux et automobiles.
- Tableau périodique des éléments:Le procédé peut utiliser une large gamme d'éléments du tableau périodique, ce qui permet de créer des revêtements uniques adaptés à des besoins spécifiques.
-
Gaz réactifs:
- Azote:Souvent utilisé pour former des revêtements de nitrure, connus pour leur dureté et leur résistance à l'usure.Par exemple, le nitrure de titane (TiN) est un revêtement PVD couramment utilisé dans les outils de coupe.
- Gaz à base d'hydrocarbures:Ces gaz sont utilisés pour créer des revêtements de carbonitrure, qui combinent les propriétés des carbures et des nitrures.Ils sont particulièrement utiles dans les applications nécessitant à la fois de la dureté et une faible friction.
-
Matériaux de support:
- Matériaux de base:Le substrat, ou matériau de base, peut être constitué de divers matériaux, notamment de métaux, de plastiques et de céramiques.Le choix du substrat dépend de l'application envisagée et des propriétés souhaitées pour le produit final.
- Préparation de la surface:Avant le processus PVD, le substrat subit souvent une préparation de surface telle que le nettoyage et le polissage afin d'assurer une bonne adhérence du revêtement.
-
Processus de revêtement PVD:
- Vaporisation:Le matériau cible est chauffé jusqu'à ce qu'il se vaporise.Cette opération peut être réalisée par des méthodes telles que la pulvérisation cathodique ou l'évaporation.
- Dépôt:Le matériau vaporisé est ensuite déposé sur la surface du substrat, formant un film mince.L'épaisseur du film peut varier de quelques nanomètres à quelques micromètres.
- Uniformité:Le procédé PVD est connu pour produire des revêtements uniformes, ce qui est essentiel pour obtenir des performances et un aspect cohérents.
-
Applications des revêtements PVD:
- Revêtements durables-décoratifs:Utilisé dans les produits où la durabilité et l'aspect esthétique sont importants, tels que les montres, les bijoux et l'électronique grand public.
- Performance Coatings:Appliqué aux composants qui nécessitent des propriétés mécaniques améliorées, tels que les outils de coupe, les moules et les pièces de moteur.
- Revêtements DLC (Diamond-Like Carbon):Ces revêtements offrent une dureté élevée et une faible friction, ce qui les rend idéaux pour les applications dans les industries automobile et aérospatiale.
- Alternatives au chrome PVD:Utilisé comme alternative écologique au chromage traditionnel, il offre des propriétés esthétiques et protectrices similaires.
-
Avantages du revêtement PVD:
- Propriétés améliorées:Les revêtements PVD améliorent la résistance à l'usure, la dureté et la résistance à la corrosion du substrat.
- Attrait esthétique:Le procédé permet de produire des revêtements aux couleurs et aux finitions variées, ce qui renforce l'attrait visuel du produit.
- Impact sur l'environnement:Le dépôt en phase vapeur (PVD) est considéré comme un procédé respectueux de l'environnement en raison du peu de déchets qu'il génère et de la faible consommation d'énergie qu'il entraîne par rapport aux méthodes de revêtement traditionnelles.
La compréhension de ces composants et processus clés permet d'apprécier la polyvalence et l'efficacité des revêtements PVD dans diverses applications industrielles.
Tableau récapitulatif :
Composant | Description |
---|---|
Matériaux cibles | Métaux (par exemple, titane, chrome), céramiques et éléments du tableau périodique. |
Gaz réactifs | Azote, hydrocarbures (par exemple, pour les revêtements de nitrure et de carbonitrure). |
Matériaux du support | Métaux, plastiques, céramiques ; nécessite une préparation de la surface pour l'adhérence. |
Procédé | Méthodes de vaporisation et de dépôt (par exemple, pulvérisation, évaporation). |
Applications | Revêtements décoratifs durables, revêtements performants, DLC, alternatives au chrome PVD. |
Avantages | Amélioration de la résistance à l'usure, de la dureté, de la résistance à la corrosion et de l'attrait esthétique. |
Exploitez le potentiel des revêtements PVD pour vos applications. contactez nos experts dès aujourd'hui !