Le brasage par induction, bien qu'avantageux dans de nombreuses applications industrielles, présente plusieurs inconvénients notables. Ceux-ci incluent des coûts initiaux élevés, une complexité d’exploitation, des limitations matérielles et des défis liés au raffinage et au maintien de la composition des matériaux. Ci-dessous, nous explorons ces inconvénients en détail, fournissant une compréhension complète des limites associées au brasage par induction.
Points clés expliqués :
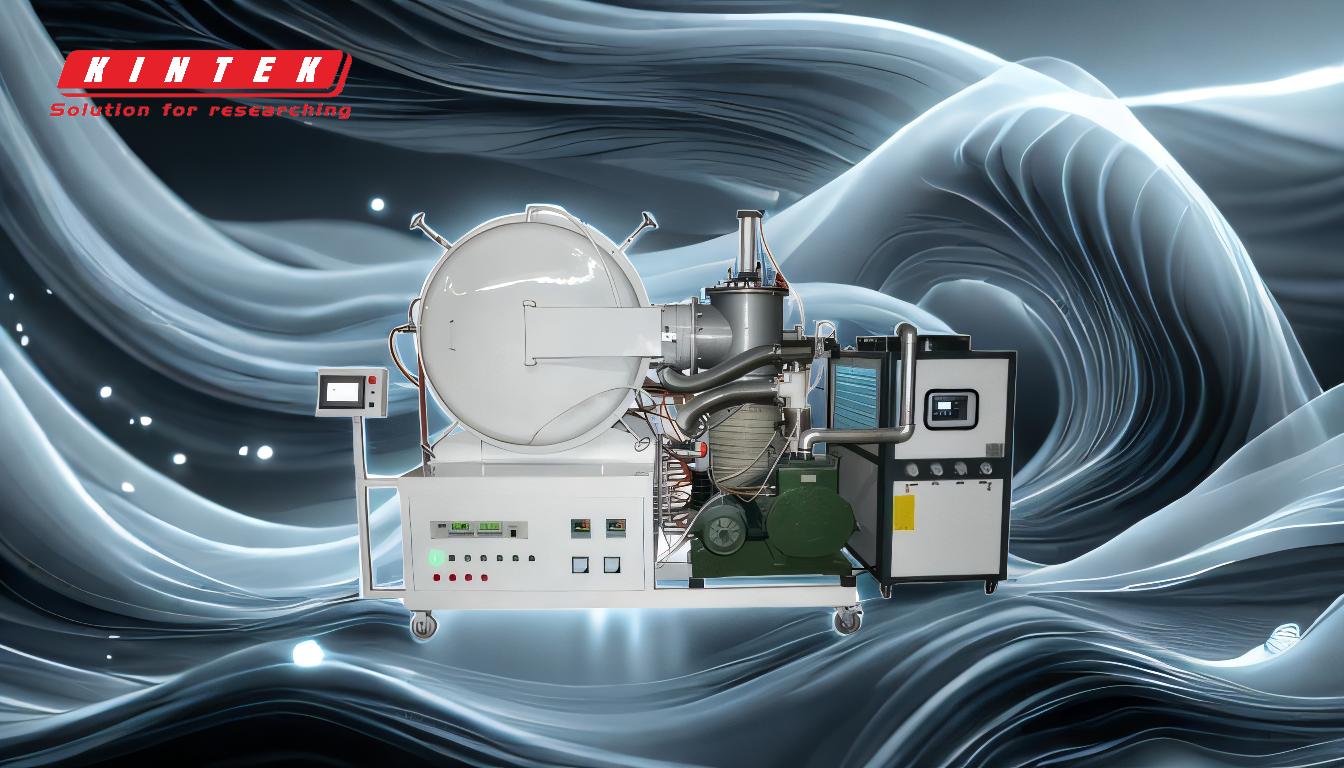
-
Coût initial élevé
- Les équipements de soudage par induction sont nettement plus chers que les méthodes de soudage traditionnelles.
- Le coût comprend non seulement la machine elle-même, mais également l'infrastructure associée, telle que les alimentations électriques et les systèmes de refroidissement.
- Pour les opérations à petite échelle ou les entreprises disposant de budgets limités, cet investissement initial élevé peut constituer un obstacle majeur à l’adoption.
-
Processus et fonctionnement complexes
- Le soudage par induction nécessite des connaissances et une formation spécialisées pour fonctionner efficacement.
- Le processus implique un contrôle précis de paramètres tels que la fréquence, la puissance et le temps de chauffage, ce qui peut s'avérer difficile pour les opérateurs inexpérimentés.
- La maintenance des équipements exige également une expertise technique, ce qui ajoute à la complexité opérationnelle.
-
Limites matérielles
- Le brasage par induction ne convient pas à tous les matériaux. Cela fonctionne mieux avec les métaux conducteurs comme le cuivre, le laiton et l’acier.
- Les matériaux non conducteurs ou ceux ayant une mauvaise conductivité thermique peuvent ne pas chauffer uniformément ou efficacement, conduisant à des résultats incohérents.
- Certains matériaux peuvent également se dégrader ou s'oxyder sous les températures élevées générées par le chauffage par induction.
-
Manque de capacité de raffinage
- Le brasage par induction n'a pas la capacité d'affiner ou de purifier les matériaux pendant le processus.
- Les matériaux utilisés doivent être préalablement exempts d'oxydes et de contaminants, car ceux-ci peuvent avoir un impact négatif sur la qualité du joint de soudure.
- Cette limitation nécessite des étapes de prétraitement supplémentaires, ce qui augmente le temps et les coûts.
-
Perte d'éléments d'oxydation et d'alliage
- Les températures élevées lors du brasage par induction peuvent provoquer l'oxydation de certains matériaux, en particulier ceux contenant des éléments d'alliage réactifs.
- L'oxydation peut entraîner la perte d'éléments d'alliage critiques, qu'il faudra peut-être rajouter pour conserver les propriétés souhaitées du matériau.
- Ce problème peut compromettre l'intégrité et les performances du produit final.
-
Consommation et efficacité énergétique
- Les systèmes de soudage par induction peuvent être gourmands en énergie, en particulier lorsqu'ils fonctionnent à des fréquences ou à des niveaux de puissance élevés.
- Bien que le chauffage par induction soit généralement efficace, la consommation globale d'énergie peut néanmoins être plus élevée que celle d'autres méthodes de brasage, en fonction de l'application.
-
Flexibilité limitée pour les pièces petites ou complexes
- Le brasage par induction est moins efficace pour les pièces petites, complexes ou de forme irrégulière en raison des difficultés à obtenir un chauffage uniforme.
- Des conceptions de bobines personnalisées peuvent être nécessaires pour des applications spécifiques, ce qui ajoute à la complexité et au coût.
-
Problèmes de sécurité
- Les températures élevées et les champs électromagnétiques générés lors du brasage par induction présentent des risques pour la sécurité des opérateurs.
- Des mesures de sécurité appropriées, telles que des équipements de protection et de protection, sont nécessaires pour atténuer ces risques.
En résumé, même si le brasage par induction offre des avantages tels que la vitesse, la précision et le chauffage localisé, ses inconvénients, notamment les coûts élevés, les limitations des matériaux et la complexité opérationnelle, doivent être soigneusement étudiés. Ces facteurs le rendent moins adapté à certaines applications ou entreprises aux ressources limitées. Comprendre ces limites est crucial pour prendre des décisions éclairées quant à savoir si le brasage par induction est le bon choix pour un cas d'utilisation spécifique.
Tableau récapitulatif :
Inconvénient | Détails |
---|---|
Coût initial élevé | Équipements et infrastructures coûteux ; barrière pour les opérations à petite échelle. |
Processus et fonctionnement complexes | Nécessite une formation spécialisée et un contrôle précis des paramètres. |
Limites matérielles | Idéal pour les métaux conducteurs ; défis avec les matériaux non conducteurs. |
Manque de capacité de raffinage | Aucune purification de matière pendant le processus ; prétraitement requis. |
Perte d'oxydation et d'alliage | Les températures élevées provoquent une oxydation et une perte d’éléments d’alliage critiques. |
Consommation d'énergie | Peut être gourmand en énergie, en particulier à hautes fréquences. |
Flexibilité limitée | Moins efficace pour les pièces petites ou complexes ; des bobines personnalisées peuvent être nécessaires. |
Problèmes de sécurité | Les températures élevées et les champs électromagnétiques présentent des risques pour les opérateurs. |
Besoin d'aide pour décider si le soudage par induction convient à votre application ? Contactez nos experts dès aujourd'hui pour des conseils personnalisés !