Un four de calcination est un type spécialisé de four rotatif conçu pour effectuer la calcination, un processus thermique qui consiste à chauffer des matériaux à des températures élevées pour induire une dissociation chimique ou éliminer l'humidité liée. Ce processus est crucial dans des industries telles que la production de ciment, la métallurgie et la fabrication de produits chimiques. Les fours de calcination sont conçus pour assurer un contrôle précis de la température et un transfert de chaleur efficace, garantissant ainsi des réactions chimiques optimales. Ils sont généralement équipés de brûleurs avancés, de récupérateurs de chaleur et de conceptions personnalisables pour s'adapter à différents matériaux et sources de combustible. Ces fours jouent un rôle essentiel dans la production de matériaux inorganiques tels que l'oxyde de calcium et font partie intégrante des processus nécessitant un traitement thermique à haute température.
Explication des points clés :
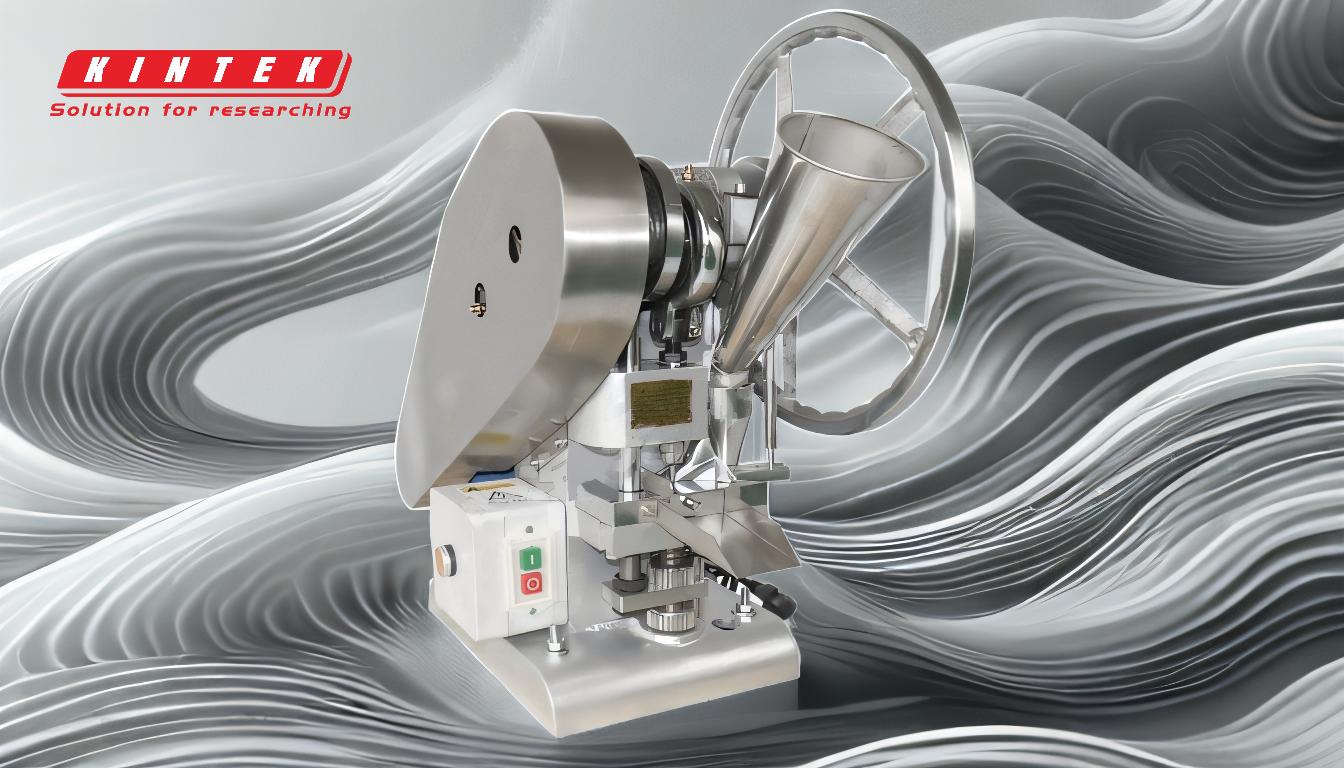
-
Définition et objectif de la calcination :
- La calcination est un processus thermique qui chauffe les matériaux à des températures élevées pour obtenir une dissociation chimique ou éliminer l'humidité liée.
- Il est couramment utilisé dans la production de matériaux inorganiques, comme la conversion du carbonate de calcium (CaCO₃) en oxyde de calcium (CaO) et en dioxyde de carbone (CO₂).
- Ce processus est essentiel dans des industries telles que la fabrication de ciment, la métallurgie et le traitement chimique.
-
Conception et structure des fours de calcination :
- Les fours de calcination sont généralement des fours rotatifs, c'est-à-dire de longs cylindres horizontaux inclinés sur leur axe pour faciliter le déplacement des matières.
- Ils sont conçus pour atteindre les températures élevées du lit nécessaires aux réactions chimiques, garantissant ainsi un traitement efficace.
- Les principales caractéristiques structurelles comprennent des brûleurs, des récupérateurs de chaleur et des systèmes de refroidissement pour optimiser l'efficacité thermique.
-
Systèmes de brûleurs :
- Les brûleurs des fours de calcination fournissent l'énergie nécessaire au processus de calcination.
- Ils sont souvent montés sur le carter de l'extrémité de décharge et peuvent être alimentés par différentes sources de combustible, notamment le gaz naturel, le propane, le diesel et le charbon pulvérisé.
- Le choix du bon brûleur est essentiel pour assurer un chauffage efficace et constant.
-
Efficacité thermique et récupération de la chaleur :
- Les fours de calcination sont conçus pour maximiser l'efficacité thermique en incorporant des récupérateurs de chaleur, tels que des préchauffeurs, qui récupèrent l'énergie des gaz d'échappement pour préchauffer le matériau d'alimentation.
- Les refroidisseurs sont utilisés pour abaisser la température du matériau traité afin de le manipuler en toute sécurité, tout en récupérant l'énergie pour d'autres usages, comme le préchauffage de l'air de combustion.
-
Contrôle de la température et personnalisation :
- Les fours de calcination offrent un contrôle précis de la température, souvent grâce à des systèmes de contrôle avancés tels que les écrans tactiles de contrôle TAP.
- Ils peuvent être personnalisés pour répondre aux exigences de processus spécifiques, y compris les schémas thermiques, les mécanismes de refroidissement de l'air et les mesures visant à empêcher la contamination des métaux ou les fuites de gaz.
- Les options de personnalisation garantissent que le four peut traiter une large gamme de matériaux et de processus.
-
Applications et utilisation dans l'industrie :
- Les fours de calcination sont largement utilisés dans les industries qui nécessitent un traitement à haute température, comme la production de ciment, où ils transforment le calcaire en chaux.
- Ils sont également utilisés en métallurgie pour le traitement des minerais et en chimie pour la production de matériaux tels que le borax et d'autres composés inorganiques.
-
Avantages environnementaux et opérationnels :
- Les fours de calcination modernes, tels que les fours rotatifs électriques, offrent des alternatives propres et efficaces aux procédés traditionnels à base de combustibles fossiles.
- Ils permettent aux industries de capturer et de réutiliser les émissions de CO₂, contribuant ainsi aux efforts de développement durable.
- La conception et l'exploitation de ces fours sont axées sur la réduction de la consommation d'énergie et de l'impact sur l'environnement.
En comprenant ces points clés, les acheteurs et les opérateurs de fours de calcination peuvent prendre des décisions éclairées sur la sélection, l'adaptation et l'exploitation de ces équipements critiques pour répondre à leurs besoins industriels spécifiques.
Tableau récapitulatif :
Caractéristiques principales | Description |
---|---|
Objectif | Chauffe les matériaux pour induire une dissociation chimique ou éliminer l'humidité. |
Conception | Fours rotatifs avec brûleurs, récupérateurs de chaleur et systèmes de refroidissement. |
Systèmes de brûleurs | Prend en charge plusieurs sources de combustible pour un chauffage efficace et constant. |
Efficacité thermique | Utilise des récupérateurs de chaleur et des refroidisseurs pour maximiser la récupération d'énergie. |
Contrôle de la température | Des systèmes avancés comme le contrôle TAP pour une gestion précise de la chaleur. |
Applications | Production de ciment, métallurgie et fabrication de produits chimiques. |
Avantages pour l'environnement | Réduit la consommation d'énergie et capture les émissions de CO₂ pour les réutiliser. |
Découvrez comment un four de calcination peut optimiser vos processus industriels contactez nos experts dès aujourd'hui !