Le procédé d'évaporation par faisceau d'électrons est une technique sophistiquée de dépôt physique en phase vapeur (PVD) utilisée pour créer des revêtements minces et de haute pureté sur des substrats.Il s'agit d'utiliser un faisceau d'électrons à haute énergie pour chauffer et évaporer un matériau source, qui se condense ensuite sur un substrat dans une chambre à vide.Cette méthode est particulièrement efficace pour les matériaux ayant un point de fusion élevé, tels que les métaux et les alliages, et permet un contrôle précis de l'épaisseur du revêtement, qui varie généralement de 5 à 250 nanomètres.Ce procédé est largement utilisé dans les industries nécessitant des revêtements uniformes et de haute pureté, telles que les semi-conducteurs, l'optique et l'aérospatiale.
Explication des points clés :
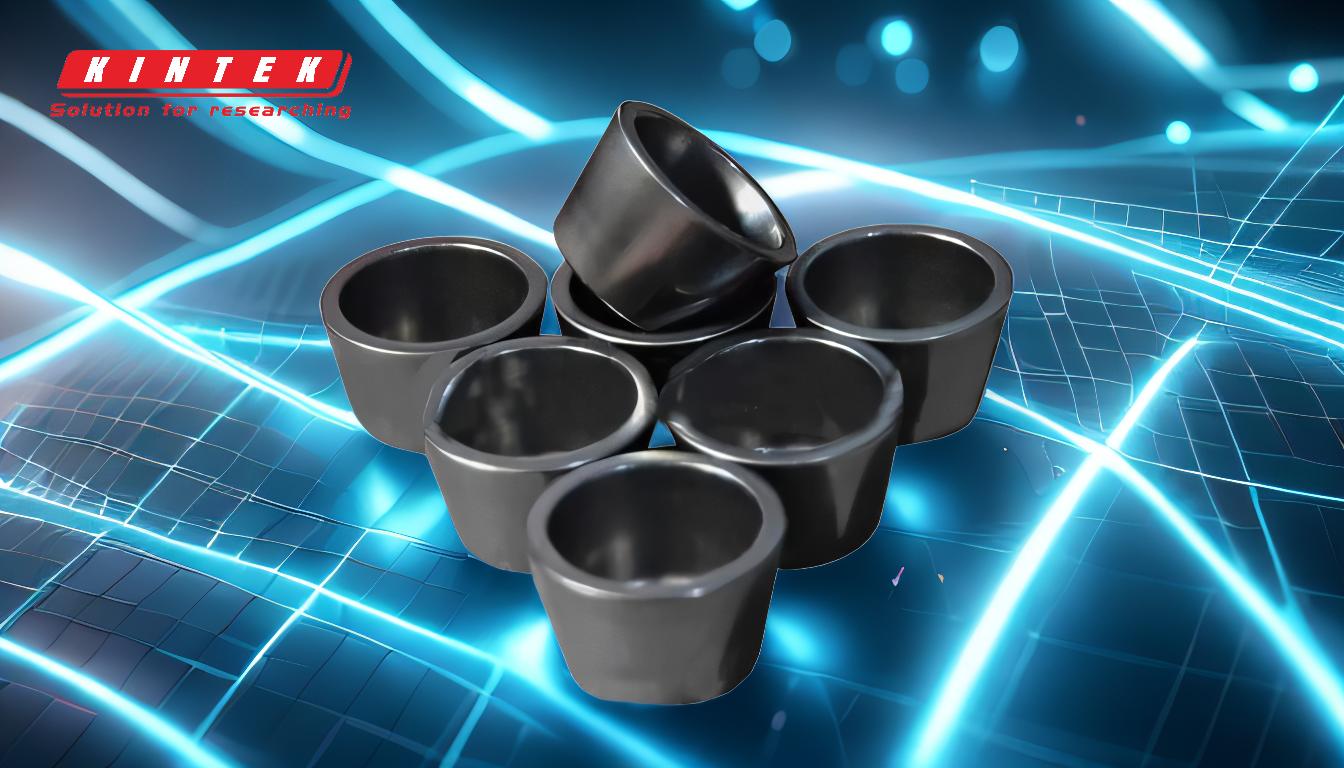
-
Génération et accélération de faisceaux d'électrons:
- Le processus commence par la production d'électrons à l'aide d'un filament de tungstène.Lorsque le filament est traversé par le courant, il s'échauffe et émet des électrons par émission thermionique.
- Ces électrons sont ensuite accélérés vers le matériau source à l'aide d'un champ électrique à haute tension, généralement de l'ordre de plusieurs kilovolts.La haute tension garantit que les électrons acquièrent suffisamment d'énergie pour chauffer efficacement le matériau source.
-
Focalisation du faisceau d'électrons:
- Un champ magnétique est utilisé pour concentrer les électrons accélérés en un faisceau étroit et concentré.Ce faisceau concentré est dirigé sur la surface du matériau source contenu dans un creuset ou un foyer en cuivre refroidi à l'eau.
- La focalisation du faisceau d'électrons est cruciale pour obtenir une densité d'énergie élevée, nécessaire à l'évaporation des matériaux ayant un point de fusion élevé.
-
Chauffage et évaporation du matériau source:
- Lorsque le faisceau d'électrons à haute énergie frappe le matériau source, il transfère une quantité importante d'énergie, ce qui provoque un échauffement rapide du matériau.Selon le matériau, ce transfert d'énergie peut conduire à l'évaporation ou à la sublimation.
- Le matériau source est généralement placé dans un creuset, qui peut être refroidi à l'eau pour éviter la contamination par des impuretés ou des réactions indésirables avec le matériau du creuset.
-
Environnement sous vide:
- L'ensemble du processus se déroule dans une chambre à vide afin de garantir que les particules évaporées se déplacent sans entrave jusqu'au substrat.L'environnement sous vide minimise les collisions entre les particules évaporées et les molécules de gaz résiduelles, qui pourraient autrement dégrader la qualité du revêtement.
- Le vide empêche également l'oxydation ou la contamination du matériau d'origine et du film mince obtenu.
-
Dépôt sur le substrat:
- Les particules évaporées remontent dans la chambre à vide et se déposent sur le substrat, qui est placé au-dessus du matériau source.Le substrat est généralement maintenu à une température contrôlée afin de garantir une bonne adhérence et une bonne qualité de film.
- Le processus de dépôt permet d'obtenir un revêtement fin et de haute pureté qui peut modifier les propriétés du substrat, telles que la conductivité électrique, la réflectivité ou la résistance à la corrosion, sans affecter sa précision dimensionnelle.
-
Contrôle de l'épaisseur du revêtement:
- L'épaisseur du film déposé est soigneusement contrôlée à l'aide de microbalances à cristal de quartz.Ces dispositifs surveillent la vitesse de dépôt en temps réel en mesurant le changement de masse au fur et à mesure que le film se développe sur le substrat.
- En ajustant des paramètres tels que le courant du faisceau d'électrons, la tension d'accélération et le temps de dépôt, il est possible d'obtenir avec une grande précision l'épaisseur de revêtement souhaitée, qui se situe généralement entre 5 et 250 nanomètres.
-
Avantages de l'évaporation par faisceau d'électrons:
- Haute pureté:Le processus produit des revêtements d'une très grande pureté, car l'environnement sous vide et le chauffage contrôlé minimisent la contamination.
- Matériaux à point de fusion élevé:L'évaporation par faisceau d'électrons est particulièrement adaptée aux matériaux ayant un point de fusion élevé, tels que l'or, le platine et les métaux réfractaires, qui sont difficiles à évaporer par les méthodes thermiques traditionnelles.
- Revêtements uniformes:Le faisceau d'électrons focalisé permet un chauffage et une évaporation uniformes, ce qui se traduit par une épaisseur et une qualité de film constantes sur l'ensemble du substrat.
- Revêtements multicouches:De nombreux systèmes à faisceau d'électrons sont équipés de plusieurs creusets, ce qui permet de déposer des revêtements multicouches ou de co-déposer différents matériaux sans rompre le vide.
-
Applications:
- Semi-conducteurs:L'évaporation par faisceau d'électrons est largement utilisée dans l'industrie des semi-conducteurs pour déposer des couches minces de métaux et d'alliages pour les interconnexions, les contacts et d'autres composants critiques.
- Optique:Le procédé est utilisé pour créer des revêtements à haute réflectivité pour les miroirs, les lentilles et d'autres composants optiques.
- Aérospatiale:L'évaporation par faisceau d'électrons est utilisée pour produire des revêtements protecteurs qui améliorent la durabilité et les performances des composants aérospatiaux.
- Recherche et développement:La technique est également utilisée en recherche et développement pour mettre au point de nouveaux matériaux et revêtements aux propriétés adaptées.
En résumé, le procédé d'évaporation par faisceau d'électrons est une méthode polyvalente et hautement contrôlée pour déposer des revêtements minces et de haute pureté sur des substrats.Sa capacité à traiter des matériaux à point de fusion élevé, à produire des revêtements uniformes et à fonctionner dans un environnement sous vide le rend indispensable dans diverses industries de haute technologie.
Tableau récapitulatif :
Aspect clé | Détails |
---|---|
Aperçu du procédé | Utilise un faisceau d'électrons à haute énergie pour évaporer et déposer des matériaux dans le vide. |
Composants clés | Filament de tungstène, champ magnétique, creuset, chambre à vide, substrat. |
Épaisseur du revêtement | 5 à 250 nanomètres, contrôlée par des microbalances à cristal de quartz. |
Avantages | Grande pureté, revêtements uniformes, traitement des matériaux à point de fusion élevé. |
Applications | Semi-conducteurs, optique, aérospatiale, R&D. |
Vous êtes intéressé par des revêtements de haute pureté pour votre industrie ? Contactez nous dès aujourd'hui pour en savoir plus sur les solutions d'évaporation par faisceaux d'électrons. pour en savoir plus sur les solutions d'évaporation par faisceau d'électrons !