Les fours à induction et les fours à arc sont tous deux largement utilisés dans les processus métallurgiques, mais ils diffèrent considérablement dans leurs mécanismes de chauffage, leurs applications et leurs capacités.Les fours à induction utilisent l'induction électromagnétique pour générer de la chaleur à l'intérieur du métal lui-même, ce qui leur permet de fondre des métaux à faible teneur en carbone et de produire des alliages de haute qualité.Ils sont souvent utilisés pour les moulages d'acier de petite taille et ont vu leurs capacités métallurgiques s'améliorer au fil du temps.D'autre part, les fours à arc reposent sur un arc électrique entre les électrodes et le métal pour générer de la chaleur, ce qui les rend plus polyvalents pour les opérations à plus grande échelle et une gamme plus large de qualités d'acier.Les fours à arc ont généralement de meilleures fonctions métallurgiques, mais ils sont moins adaptés à la fusion d'alliages à faible teneur en carbone en raison du risque de contamination par le carbone des électrodes en graphite.
Explication des points clés :
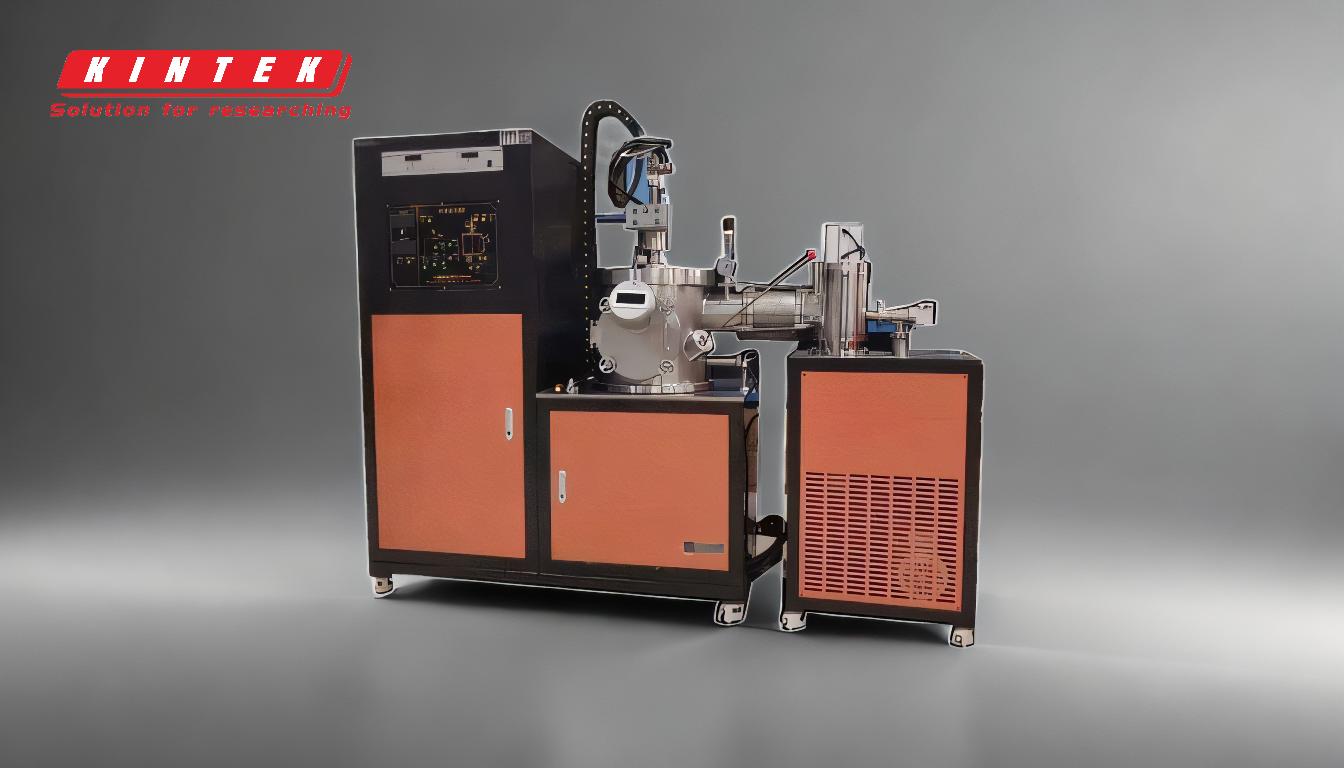
-
Mécanisme de chauffage:
- Four à induction:Cette méthode utilise l'induction électromagnétique pour générer de la chaleur directement à l'intérieur du métal.Cette méthode ne nécessite pas de contact avec le métal, ce qui réduit les risques de contamination.
- Four à arc:Utilise un arc électrique formé entre des électrodes en graphite et le métal pour générer de la chaleur.Cette méthode implique un contact direct avec le métal, ce qui peut entraîner une contamination par le carbone.
-
Les applications:
- Four à induction:Il est généralement utilisé pour affiner des qualités d'acier répondant à des exigences générales de qualité métallurgique, en particulier pour les pièces moulées en acier de petite taille.Il est également capable de produire des aciers faiblement alliés, des aciers fortement alliés et des aciers inoxydables à très faible teneur en carbone de haute qualité.
- Four à arc:Plus polyvalent, il est couramment utilisé pour les opérations à plus grande échelle.Il peut traiter une gamme plus large de nuances d'acier, mais il est moins adapté à la fusion d'alliages à faible teneur en carbone en raison du risque de contamination par le carbone.
-
Capacités métallurgiques:
- Four à induction:Historiquement, sa fonction métallurgique était considérée comme inférieure à celle des fours à arc.Toutefois, depuis les années 1980, les progrès réalisés en matière d'équipements et de réfractaires ont considérablement amélioré ses capacités, permettant la production d'alliages de haute qualité.
- Four à arc:Il a généralement de meilleures fonctions métallurgiques et est plus efficace pour l'affinage d'une gamme plus large de nuances d'acier.Cependant, elle est moins efficace pour la production d'alliages à faible teneur en carbone en raison du risque de contamination par le carbone des électrodes.
-
Contamination par le carbone:
- Four à induction:Ne nécessite pas d'électrodes en graphite, ce qui élimine le risque de contamination par le carbone.Il est donc idéal pour fondre l'acier et les alliages à très faible teneur en carbone.
- Four à arc:Utilise des électrodes en graphite, qui peuvent introduire du carbone dans la matière fondue, ce qui le rend moins adapté aux alliages à faible teneur en carbone.
-
Considérations relatives à la conception:
- Four à induction:Il faut concevoir avec soin la disposition du champ magnétique, en particulier pour les matériaux non magnétiques comme l'aluminium.La conception de l'inducteur doit tenir compte des fuites de flux magnétique et de la distance entre les spires pour garantir un chauffage efficace.
- Four à arc:La conception se concentre sur la configuration de l'électrode et la stabilité de l'arc pour assurer un chauffage et une fusion homogènes du métal.
-
Échelle opérationnelle:
- Four à induction:Plus adapté aux opérations à petite échelle et aux applications spécialisées nécessitant des alliages de haute pureté.
- Four à arc:Mieux adapté aux opérations industrielles à grande échelle où une large gamme de qualités d'acier est traitée.
En résumé, le choix entre un four à induction et un four à arc dépend des exigences métallurgiques spécifiques, de l'échelle de l'opération et de la nécessité de minimiser la contamination par le carbone.Les fours à induction sont idéaux pour les applications spécialisées à petite échelle nécessitant des alliages de haute pureté, tandis que les fours à arc sont plus polyvalents et conviennent à des opérations à plus grande échelle avec une gamme plus large de nuances d'acier.
Tableau récapitulatif :
Caractéristiques | Four à induction | Four à arc |
---|---|---|
Mécanisme de chauffage | L'induction électromagnétique chauffe directement le métal, ce qui réduit les risques de contamination. | Arc électrique entre les électrodes et le métal, qui peut introduire du carbone. |
Applications | Idéal pour les opérations à petite échelle, les alliages à faible teneur en carbone et les aciers de haute pureté. | Polyvalent pour les opérations à plus grande échelle et une large gamme de nuances d'acier. |
Capacités métallurgiques | Amélioration des capacités de production d'alliages de haute qualité depuis les années 1980. | Meilleur pour l'affinage d'une large gamme de nuances d'acier, mais moins efficace pour les alliages à faible teneur en carbone. |
Contamination par le carbone | Pas d'électrodes en graphite, ce qui élimine les risques de contamination par le carbone. | Les électrodes en graphite peuvent introduire du carbone, ce qui les rend moins adaptées aux alliages à faible teneur en carbone. |
Échelle opérationnelle | Idéal pour les applications spécialisées à petite échelle. | Convient aux opérations industrielles à grande échelle. |
Vous avez besoin d'aide pour choisir le four adapté à votre procédé métallurgique ? Contactez nos experts dès aujourd'hui pour des conseils personnalisés !