Les fours à induction et les fours à arc sont tous deux largement utilisés pour la fusion et l'affinage des métaux, mais ils diffèrent considérablement dans leurs principes de fonctionnement, leurs applications et leurs capacités. Les fours à induction utilisent l'induction électromagnétique pour générer de la chaleur, ce qui leur permet de fondre des métaux à faible teneur en carbone et de produire des alliages de haute qualité. Ils sont plus respectueux de l'environnement et plus efficaces, et les progrès réalisés permettent de produire des aciers de haute qualité. Les fours à arc, quant à eux, utilisent des arcs électriques pour générer de la chaleur, ce qui les rend plus adaptés à la production d'acier à grande échelle avec des exigences métallurgiques plus élevées. Cependant, ils produisent plus de gaz d'échappement, de résidus et de bruit. Le choix entre les deux dépend des exigences métallurgiques spécifiques, de l'échelle de production et des considérations environnementales.
Explication des points clés :
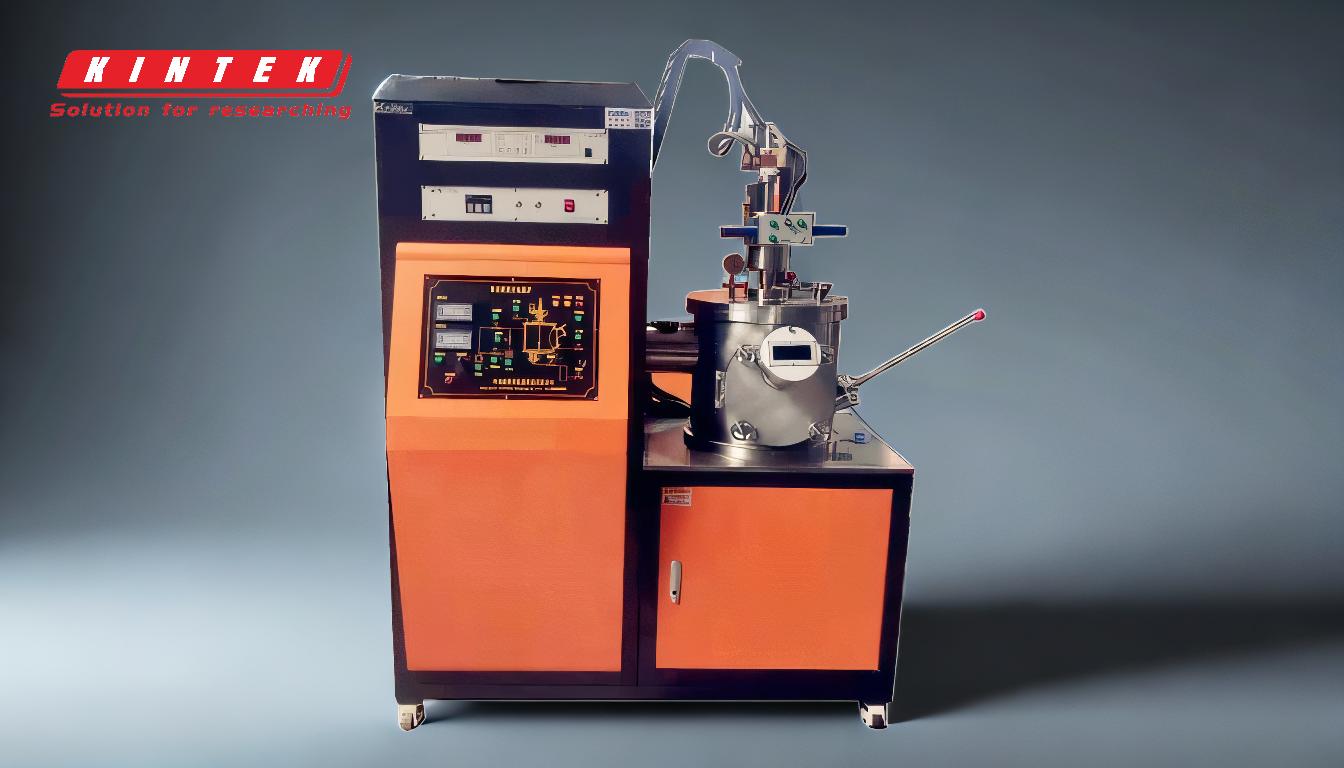
-
Principe de fonctionnement:
- Four à induction: Utilise l'induction électromagnétique pour générer de la chaleur. Un courant alternatif à haute fréquence passe dans une bobine, créant un champ magnétique qui induit des courants de Foucault dans le métal et le réchauffe. Cette méthode ne nécessite pas de contact direct entre la source de chaleur et le métal.
- Four à arc: Utilise un arc électrique pour générer de la chaleur. Un arc électrique est créé entre les électrodes et le métal, produisant une chaleur intense. Cette méthode implique un contact direct entre la source de chaleur (l'arc) et le métal.
-
Capacités métallurgiques:
- Four à induction: Historiquement, les fours à induction avaient des capacités métallurgiques limitées, mais les progrès réalisés depuis les années 1980 ont permis d'améliorer leur capacité à produire des aciers faiblement alliés, des aciers fortement alliés et même des aciers inoxydables à très faible teneur en carbone et des superalliages de haute qualité. Ils sont particulièrement efficaces pour fondre les métaux à faible teneur en carbone et produire des alliages dans des conditions spécifiques (environnements acides, neutres ou proches du vide).
- Four à arc: Il possède généralement des capacités métallurgiques supérieures à celles des fours à induction, ce qui lui permet d'affiner des qualités d'acier plus exigeantes. Il est couramment utilisé dans la production d'acier à grande échelle.
-
Applications:
- Four à induction: Il est généralement utilisé pour affiner les qualités d'acier répondant à des exigences générales de qualité métallurgique, en particulier pour les pièces moulées en acier de petite taille. Il est également utilisé pour produire des alliages de haute qualité et fondre des matériaux non magnétiques comme l'aluminium.
- Four à arc: Principalement utilisé dans la production d'acier à grande échelle, où une qualité métallurgique supérieure et des volumes plus importants sont requis. Il est moins adapté à la production d'alliages à petite échelle ou spécialisés.
-
Impact sur l'environnement:
- Four à induction: Plus respectueux de l'environnement, avec moins d'émissions, de résidus et de bruit. Il a également un meilleur rendement énergétique, ce qui permet de réduire les pertes de combustion et le temps de fusion du métal.
- Four à arc: Il produit une grande quantité de gaz d'échappement, de résidus et de bruit, et a une consommation d'énergie plus élevée. Il est moins respectueux de l'environnement que les fours à induction.
-
Efficacité et performance thermique:
- Four à induction: Plus efficace que les fours traditionnels à terre ouverte. Il utilise des bobines à haute tension pour produire des fréquences comprises entre 50 Hz et 10 000 Hz, ce qui permet un chauffage rapide et une efficacité thermique plus élevée. Il en résulte de meilleurs rendements avec moins de pertes par combustion et une production d'acier supérieure.
- Four à arc: Bien qu'efficace pour la production à grande échelle, il est moins performant en termes de consommation d'énergie et de rendement thermique que les fours à induction.
-
Adéquation des matériaux:
- Four à induction: Convient à la fusion de métaux à faible teneur en carbone et à la production d'alliages de haute qualité. Il est particulièrement efficace pour les matériaux non magnétiques tels que l'aluminium, pour lesquels une conception minutieuse du champ magnétique est nécessaire.
- Four à arc: Convient à une large gamme de métaux, mais est particulièrement efficace pour la production d'acier à grande échelle où une qualité métallurgique supérieure est requise.
-
Progrès technologiques:
- Four à induction: Depuis les années 1980, d'importants progrès en matière d'équipements et de réfractaires ont amélioré ses capacités métallurgiques, permettant la production d'aciers et d'alliages de haute qualité.
- Four à arc: Le secteur de l'acier reste le choix privilégié pour la production d'acier à grande échelle, avec des améliorations constantes en termes d'efficacité et d'impact sur l'environnement.
En résumé, le choix entre un four à induction et un four à arc dépend des exigences spécifiques du processus métallurgique, notamment de l'échelle de production, du type de métal à fondre et des considérations environnementales. Les fours à induction conviennent mieux à la production d'alliages de haute qualité à petite échelle et à faible impact sur l'environnement, tandis que les fours à arc sont plus adaptés à la production d'acier à grande échelle avec des exigences métallurgiques plus élevées.
Tableau récapitulatif :
Aspect | Four à induction | Four à arc |
---|---|---|
Principe de fonctionnement | Utilise l'induction électromagnétique ; pas de contact direct avec le métal. | Utilise des arcs électriques ; contact direct avec le métal. |
Capacités métallurgiques | Produit des alliages de haute qualité, des aciers à faible teneur en carbone et des superalliages. | Supérieure pour l'affinage des qualités d'acier de haute qualité. |
Applications | Production à petite échelle d'alliages de haute qualité ; fusion de matériaux non magnétiques comme l'aluminium. | Production d'acier à grande échelle ; exigences métallurgiques plus élevées. |
Impact sur l'environnement | Réduction des émissions, des déchets et du bruit ; meilleure efficacité énergétique. | Plus d'émissions, de déchets et de bruit ; moins respectueux de l'environnement. |
Efficacité | Chauffage rapide, efficacité thermique plus élevée, moins de perte de combustion. | Moins efficace en termes de consommation d'énergie et de performance thermique. |
Adéquation des matériaux | Idéal pour les métaux à faible teneur en carbone et les matériaux non magnétiques. | Convient à une large gamme de métaux, en particulier à la production d'acier à grande échelle. |
Progrès technologiques | Amélioration des capacités métallurgiques depuis les années 1980. | Amélioration continue de l'efficacité et de l'impact environnemental. |
Vous ne savez toujours pas quel four est le mieux adapté à vos besoins ? Contactez nos experts dès aujourd'hui pour des conseils personnalisés !