Un four rotatif est un équipement thermique spécialisé conçu pour chauffer, calciner, torréfier ou sécher des matériaux granuleux et pulvérulents.Il se compose d'un cylindre qui tourne autour de son axe longitudinal, souvent avec une légère inclinaison, afin d'assurer une distribution uniforme de la chaleur et un traitement cohérent des matériaux.Le four est chauffé de l'extérieur, généralement à l'aide d'un chauffage électrique, et est largement utilisé dans des applications industrielles telles que la production de matériaux, l'oxydation, la calcination et la récupération du plomb.Sa polyvalence et sa capacité à traiter une large gamme de matériaux en font un outil essentiel dans des secteurs tels que la métallurgie, l'optique et le traitement chimique.
Explication des points clés :
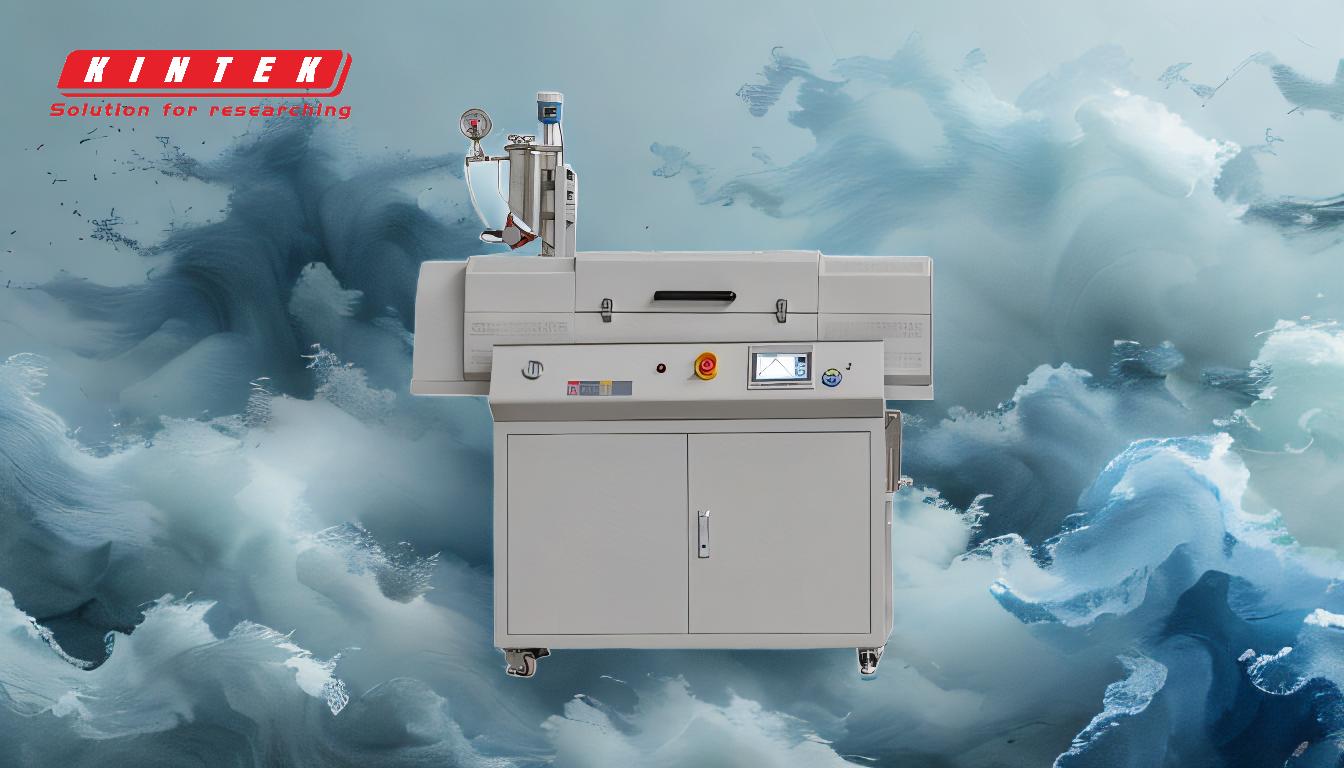
-
Définition et structure d'un four rotatif:
- Un four rotatif est un four industriel cylindrique qui tourne autour de son axe longitudinal.Il est conçu pour chauffer des matériaux en vrac en vue d'un traitement physico-chimique.
- Le four se compose d'un long tonneau légèrement incliné qui tourne lentement.Cette rotation garantit que les matériaux sont mélangés et chauffés uniformément lors de leur passage dans le four.
-
Mécanisme de chauffage:
- La chaleur nécessaire au traitement des matériaux dans un four rotatif est généralement générée par des éléments chauffants électriques situés à l'extérieur du tonneau.Cette méthode de chauffage externe garantit une distribution radiale cohérente de la température, ce qui est essentiel pour un traitement uniforme des matériaux.
-
Applications des fours rotatifs:
- Calcination et torréfaction:Les fours rotatifs sont couramment utilisés pour la calcination (décomposition thermique) et le grillage (oxydation ou réduction) de matériaux granuleux et pulvérulents.Ces procédés sont essentiels dans des industries telles que la métallurgie et la fabrication de produits chimiques.
- Séchage et vieillissement:Le four est également utilisé pour le séchage et le vieillissement des matériaux, qui sont des étapes critiques dans la production et le traitement des matériaux.
- Procédés d'oxydation:Les fours rotatifs sont utilisés dans les processus d'oxydation, qui consistent à réduire le nombre d'électrons dans un échantillon, souvent dans des applications chimiques et métallurgiques.
- Récupération du plomb:Une application importante des fours rotatifs est la récupération du plomb à partir des déchets de batteries plomb-acide, ainsi que la réduction des composés de plomb tels que le sulfate de plomb, les oxydes de plomb et les concentrés de plomb.
-
Manutention et traitement des matériaux:
- Les matériaux sont introduits dans la partie réacteur du four et transportés le long du tube rotatif.La rotation garantit que les matériaux sont continuellement mélangés et exposés à la chaleur, ce qui permet un traitement uniforme.
- La légère inclinaison de la cuve du four favorise le mouvement progressif des matériaux de l'extrémité d'alimentation à l'extrémité de décharge, ce qui garantit un traitement complet.
-
Polyvalence et importance industrielle:
- Les fours rotatifs sont des outils polyvalents utilisés dans un grand nombre d'industries, notamment la métallurgie, l'optique et le traitement chimique.Ils sont par exemple utilisés dans la production de lentilles et de miroirs primaires pour les télescopes optiques.
- Leur capacité à traiter différents matériaux et processus les rend indispensables dans les environnements industriels où un traitement thermique précis est nécessaire.
-
Avantages des fours rotatifs:
- Distribution uniforme de la chaleur:La conception assure une température radiale constante, ce qui est essentiel pour obtenir des propriétés de matériaux uniformes.
- Mélange efficace:Le mécanisme rotatif assure un mélange continu des matériaux, ce qui permet un traitement plus efficace.
- Polyvalence:La possibilité d'effectuer plusieurs processus (calcination, torréfaction, séchage, oxydation) dans un seul four en fait une solution rentable pour de nombreuses industries.
En résumé, un four rotatif est un équipement très efficace et polyvalent utilisé pour divers procédés thermiques dans des applications industrielles.Sa conception garantit une distribution uniforme de la chaleur et une manipulation efficace des matériaux, ce qui le rend essentiel pour des processus tels que la calcination, le grillage, le séchage et la récupération du plomb.
Tableau récapitulatif :
Caractéristique | Description de la structure |
---|---|
Structure de l'appareil | Tonneau cylindrique tournant autour de son axe, légèrement incliné pour faciliter l'écoulement du matériau. |
Mécanisme de chauffage | Chauffage électrique externe pour une distribution radiale cohérente de la température. |
Applications | Calcination, grillage, séchage, oxydation, récupération du plomb et vieillissement des matériaux. |
Manipulation des matériaux | Mélange continu et exposition uniforme à la chaleur pour un traitement complet. |
Secteurs d'activité | Métallurgie, optique, traitement chimique, etc. |
Avantages | Distribution uniforme de la chaleur, mélange efficace et capacités de traitement polyvalentes. |
Exploitez le potentiel des fours rotatifs pour répondre à vos besoins industriels. contactez nos experts dès aujourd'hui !