La température de frittage des céramiques, en particulier dans les applications dentaires, se situe généralement entre 1 200 °C et 1 400 °C. Cette température élevée est essentielle pour faciliter la diffusion atomique à travers les frontières des particules, permettant ainsi aux particules de fusionner sans atteindre le point de fusion du matériau. Le processus comporte plusieurs étapes, notamment la préparation de la poudre, le chauffage, la fusion des particules et la solidification. Pour des matériaux comme la zircone, la température de frittage dépasse souvent 1 100 °C à 1 200 °C, certains fours fonctionnant plus près de 1 500 °C pour atteindre une densité maximale. La température précise dépend des propriétés du matériau et du résultat souhaité, garantissant une densité et une intégrité structurelle optimales.
Points clés expliqués :
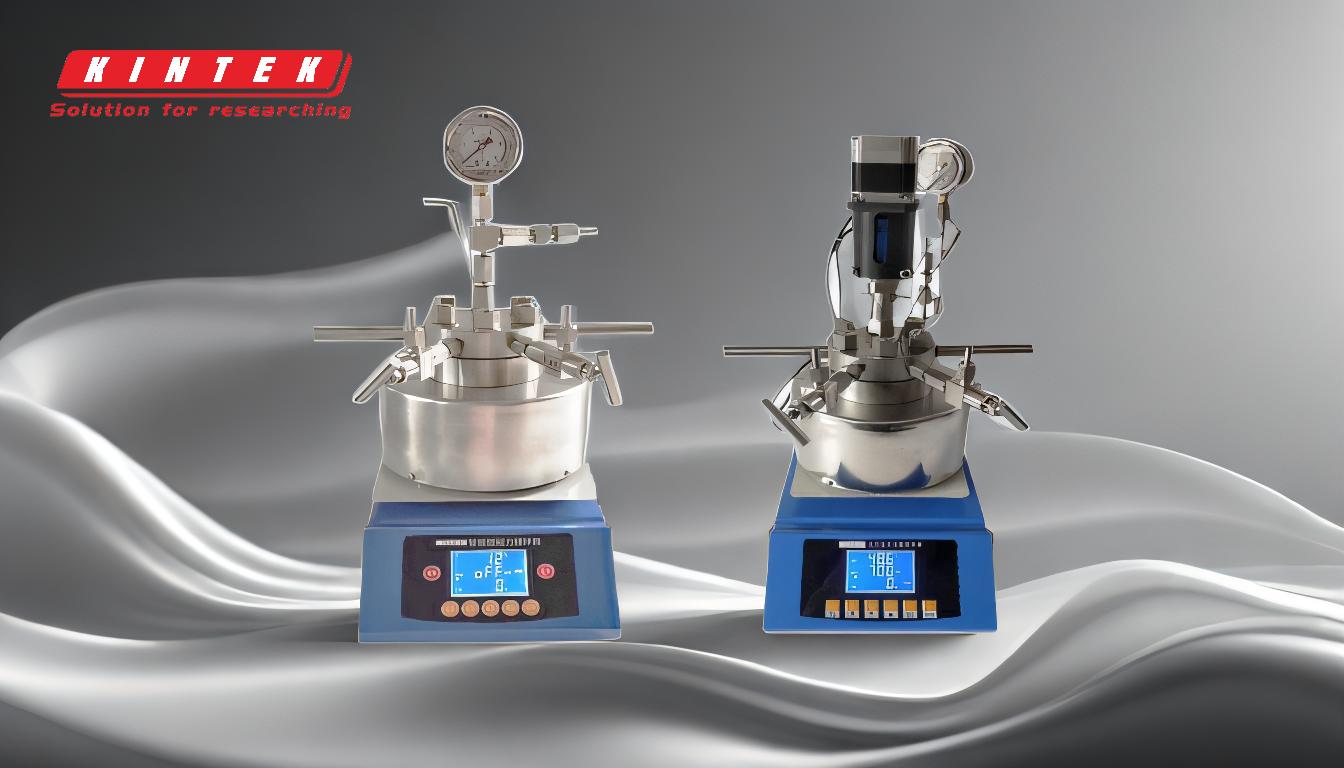
-
Plage de température pour les céramiques de frittage:
- Le processus de frittage nécessite généralement des températures comprises entre 1200°C et 1400°C pour la céramique, notamment dans les applications dentaires.
- Cette plage est critique car elle permet aux atomes de diffuser et aux particules de fusionner sans liquéfier le matériau.
- Pour la zircone, la transformation des états cristallins monocliniques en états cristallins polytétragonaux se produit autour de 1100°C à 1200°C , mais des températures plus élevées (jusqu'à 1500°C ) sont souvent utilisés pour atteindre une densité maximale quasi théorique.
-
Rôle de la température dans le frittage:
- La température est un facteur clé dans le frittage car elle doit être suffisamment élevée pour permettre la diffusion atomique et la liaison des particules, mais en dessous du point de fusion du matériau pour empêcher la liquéfaction.
- Le four de frittage doit maintenir un contrôle précis de la température pour garantir que le matériau atteigne la densité et les propriétés structurelles souhaitées.
-
Étapes du processus de frittage:
- Préparation de poudre: La matière première est préparée sous une forme compacte à l'aide de méthodes telles que le soudage à froid, l'impression 3D ou le pressage.
- Chauffage et consolidation: Le compact est chauffé juste en dessous de son point de fusion, activant les microstructures cristallines et initiant la liaison des particules.
- Fusion de particules: Les particules se densifient et fusionnent, un processus qui peut être accéléré grâce à des techniques comme le frittage en phase liquide (LPS).
- Solidification: Le matériau refroidit et se solidifie en une structure unifiée et dense.
-
Considérations spécifiques au matériau:
- Pour la zircone, la température de frittage est critique pour obtenir la transformation cristalline et la densité souhaitées.
- Les fours de frittage fonctionnent souvent à des températures plus élevées (par exemple 1 500 °C) pour garantir une densité maximale, qui peut atteindre jusqu'à 99% du maximum théorique .
-
Importance d’un contrôle précis de la température:
- Les fours de frittage doivent maintenir des températures inférieures au point de fusion du matériau pour éviter la liquéfaction tout en garantissant une chaleur suffisante pour la fusion des particules.
- Cette précision est cruciale pour obtenir les propriétés mécaniques et structurelles souhaitées dans le produit final.
-
Applications et implications:
- Dans les applications dentaires, le frittage est utilisé pour créer des restaurations en céramique à haute résistance telles que des couronnes et des ponts.
- La capacité de contrôler la température de frittage a un impact direct sur la qualité, la durabilité et les performances du produit final.
Pour plus d’informations sur les fours de frittage, vous pouvez vous référer à ce guide détaillé : four de frittage .
Tableau récapitulatif :
Aspect | Détails |
---|---|
Plage de température | 1 200°C–1 400°C (jusqu'à 1 500°C pour la zircone) |
Rôle clé de la température | Permet la diffusion atomique et la liaison des particules sans liquéfaction |
Étapes du frittage | Préparation de poudres, chauffage, fusion de particules, solidification |
Facteurs spécifiques au matériau | La zircone nécessite 1 100°C – 1 200°C pour la transformation cristalline |
Importance de la précision | Assure une densité, une intégrité structurelle et des propriétés mécaniques optimales |
Applications | Restaurations dentaires (couronnes, ponts) et composants céramiques à haute résistance |
Besoin de solutions de frittage précises pour vos céramiques ? Contactez nos experts dès aujourd'hui pour en savoir plus !