Les fours à induction sont largement utilisés dans les milieux industriels et manufacturiers en raison de leur efficacité énergétique, de leur propreté et de leur précision. Ils sont particulièrement appréciés pour leur capacité à faire fondre les métaux rapidement et uniformément tout en minimisant la contamination et la consommation d'énergie. Les fours à induction sont polyvalents, capables de traiter des métaux ferreux et non ferreux, et conviennent à une variété d'applications, notamment la fabrication d'alliages, le moulage de précision et les processus de traitement thermique. Leur conception, qui utilise l’induction électromagnétique pour générer de la chaleur au sein même du métal, garantit un processus de fusion contrôlé et sans pollution. Cela en fait un choix écologique et rentable pour les fonderies et les opérations industrielles modernes.
Points clés expliqués :
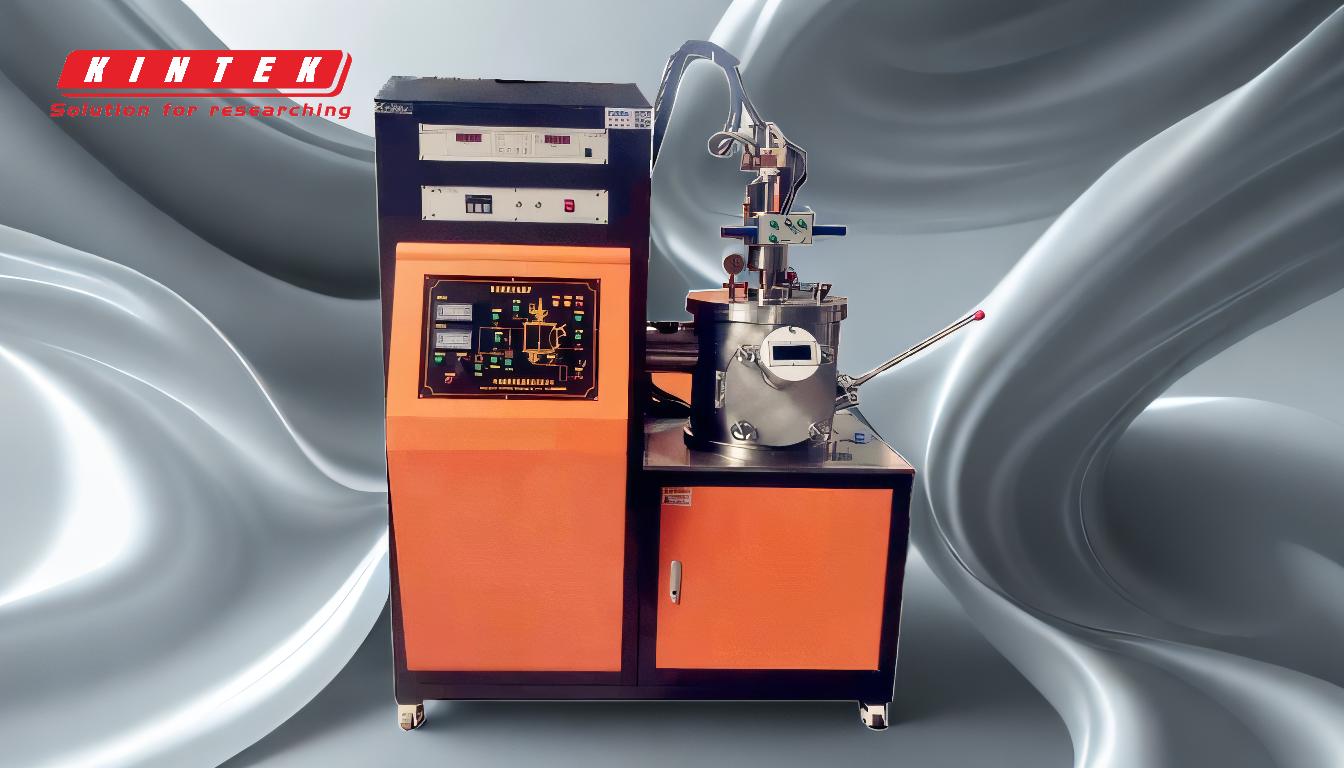
-
Efficacité énergétique et faible consommation d'énergie
- Les fours à induction sont très économes en énergie car ils génèrent de la chaleur directement dans la charge métallique par induction électromagnétique. Cela réduit les pertes d'énergie par rapport aux fours traditionnels qui dépendent de sources de chaleur externes comme la combustion ou les arcs.
- Le processus minimise la dissipation de chaleur, garantissant que la majeure partie de l'énergie est utilisée pour la fusion, ce qui se traduit par des coûts opérationnels inférieurs et une empreinte carbone réduite.
-
Fonctionnement propre et sans pollution
- Contrairement aux fours à combustion, les fours à induction ne produisent pas de poussière, de fumée ou d’autres polluants. Cela les rend respectueux de l’environnement et conformes aux réglementations environnementales strictes.
- L'absence de combustion ou de chauffage par arc élimine également le risque de contamination provenant de sources externes, garantissant la pureté du métal fondu.
-
Contrôle précis de la température
- Les fours à induction offrent un contrôle supérieur de la température, avec des différences de température minimales entre le noyau et la surface du métal. Cette précision est cruciale pour les processus qui nécessitent des conditions de fusion ou de chauffage spécifiques, tels que la fabrication d'alliages ou le traitement thermique.
- La capacité de réguler la chaleur avec précision aide à préserver les éléments d’alliage précieux, garantissant ainsi la qualité et la cohérence du produit final.
-
Vitesse de chauffage rapide et efficacité de production élevée
- Les fours à induction chauffent les métaux rapidement, réduisant considérablement les temps de fusion par rapport aux méthodes traditionnelles. Cela conduit à une efficacité de production et à un débit plus élevés.
- Le processus de chauffage rapide réduit également l’oxydation et la décarburation, qui peuvent dégrader la qualité du métal.
-
Polyvalence dans les applications
-
Les fours à induction conviennent à un large éventail d’applications, notamment :
- Faire fondre des métaux ferreux et non ferreux (par exemple, l'acier, l'aluminium, le cuivre).
- Fabrication d'alliages, où l'uniformité et la flexibilité sont essentielles.
- Moulage de précision, frettage, recuit et brasage.
- Processus de traitement thermique comme la trempe, le revenu et le préchauffage.
- Leur adaptabilité en fait un choix privilégié dans des secteurs allant de l’automobile à l’aérospatiale.
-
Les fours à induction conviennent à un large éventail d’applications, notamment :
-
Conditions de travail améliorées
- Le processus de fusion confiné et contrôlé des fours à induction crée un environnement de travail plus propre et plus sûr.
- Les travailleurs ne sont pas exposés à des polluants nocifs ou à une chaleur extrême, ce qui améliore les conditions générales de travail et réduit les risques pour la santé.
-
Économies de matériaux et de coûts
- Les fours à induction minimisent la perte de matière en réduisant l'oxydation et en préservant les éléments d'alliage. Cela conduit à des économies significatives sur les coûts des matières premières.
- Le contrôle précis du processus de fusion réduit également l’usure des matrices de forgeage et autres équipements, réduisant ainsi encore les coûts d’exploitation.
-
Faible encombrement et facilité de réglementation
- Les fours à induction sont compacts et nécessitent moins d’espace que les fours traditionnels.
- Le processus de fusion est facile à réguler, permettant d’obtenir des résultats cohérents et reproductibles, ce qui est essentiel pour une fabrication de haute qualité.
En résumé, les fours à induction sont choisis pour leur efficacité, leur propreté, leur précision et leur polyvalence. Ils offrent une solution durable et rentable pour les processus industriels modernes, ce qui les rend indispensables dans les fonderies et les installations de fabrication du monde entier.
Tableau récapitulatif :
Avantages clés | Détails |
---|---|
Efficacité énergétique | Génère de la chaleur directement dans le métal, réduisant ainsi les pertes d'énergie. |
Fonctionnement propre | Sans pollution, sans poussière ni fumée et conforme aux réglementations environnementales. |
Contrôle précis de la température | Différences de température minimales, préservant les éléments d’alliage. |
Vitesse de chauffage rapide | Réduit les temps de fusion, augmentant ainsi l’efficacité de la production. |
Versatilité | Convient aux métaux ferreux et non ferreux, à la fabrication d'alliages, etc. |
Conditions de travail améliorées | Un environnement plus propre et plus sûr avec des risques réduits pour la santé. |
Économies de coûts | Minimise les pertes de matériaux et réduit les coûts opérationnels. |
Conception compacte | Faible encombrement et régulation facile pour des résultats cohérents. |
Prêt à améliorer vos processus industriels avec des fours à induction ? Contactez-nous aujourd'hui pour en savoir plus !