Le vide joue un rôle essentiel dans les processus de revêtement de couches minces, tels que le dépôt physique en phase vapeur (PVD) et le dépôt par faisceau d'électrons (E-beam), en créant un environnement qui minimise la contamination, améliore le transport des matériaux et garantit la formation d'un film de haute qualité.Le vide réduit la densité des molécules de gaz, ce qui permet au matériau évaporé de parcourir de plus longues distances sans collision, ce qui améliore le dépôt directionnel et la pureté du film.En outre, il empêche les réactions chimiques indésirables et la contamination par les gaz ambiants, ce qui garantit une forte adhérence et des films minces de haute qualité.L'environnement sous vide est essentiel pour obtenir les propriétés souhaitées des films, telles que l'uniformité, la pureté et l'adhérence, ce qui le rend indispensable dans les processus de revêtement de films minces.
Explication des points clés :
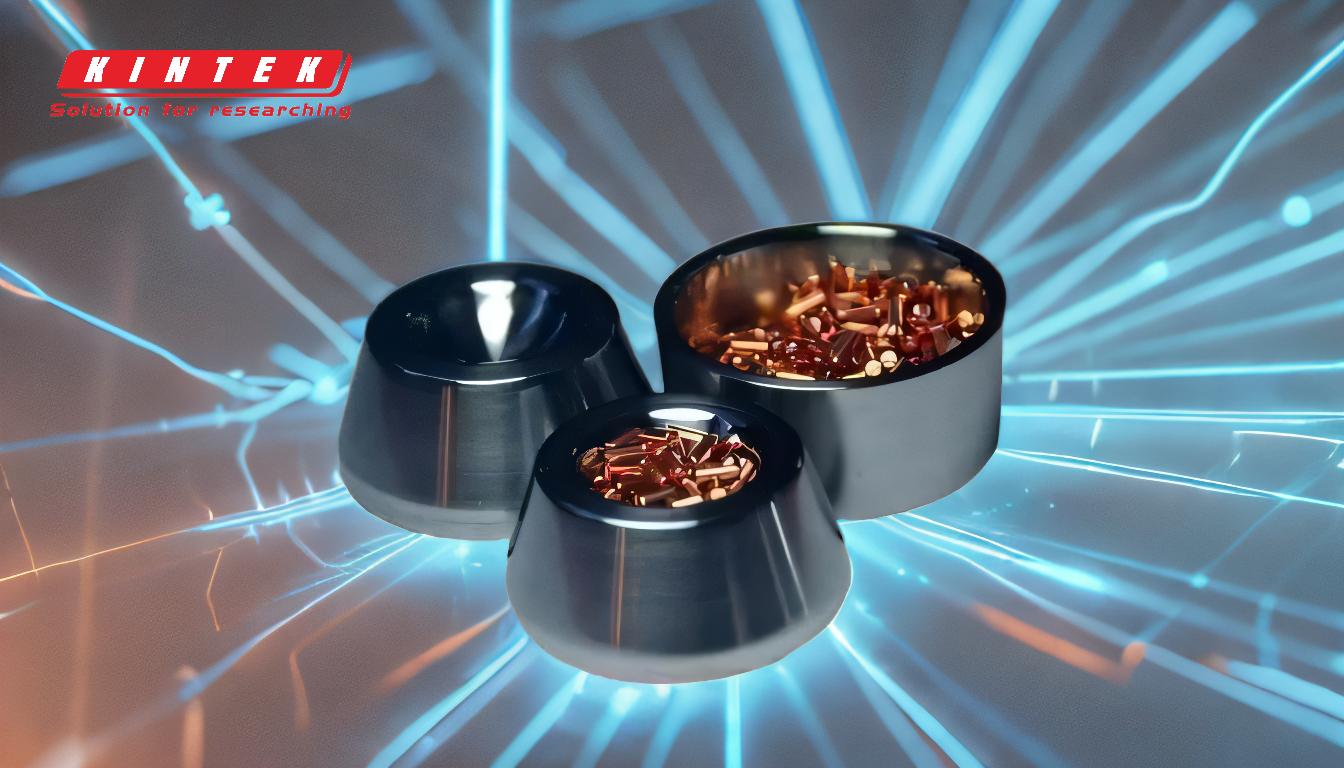
-
Minimiser la contamination:
- Un environnement sous vide réduit la présence de gaz indésirables tels que l'oxygène, l'azote et le dioxyde de carbone, qui peuvent réagir avec le matériau du film ou provoquer des défauts.
- En maintenant un vide poussé (généralement inférieur à 10^-5 Torr), le système minimise la contamination par les gaz de fond, ce qui garantit des films minces d'une grande pureté.
-
Augmentation du libre parcours moyen:
- Dans le vide, le libre parcours moyen des atomes ou molécules évaporés augmente considérablement.Par exemple, à 10^-5 Torr, le libre parcours moyen est d'environ 1 mètre.
- Cela permet au matériau évaporé de se déplacer en ligne droite vers le substrat sans entrer en collision avec les molécules de gaz, ce qui garantit un dépôt efficace et directionnel.
-
Amélioration de la qualité du film:
- Un environnement sous vide garantit que le matériau évaporé se condense uniformément sur le substrat, ce qui permet d'obtenir des films minces de haute qualité avec une adhérence et une uniformité excellentes.
- Il empêche la formation de défauts causés par les collisions entre molécules de gaz ou les réactions chimiques, qui peuvent affaiblir l'intégrité structurelle du film.
-
Contrôle de la composition des gaz et des vapeurs:
- Le vide permet un contrôle précis de la composition des gaz et des vapeurs dans la chambre de traitement, ce qui est essentiel pour obtenir des propriétés de film spécifiques.
- Ce contrôle est essentiel pour des procédés tels que la pulvérisation réactive, où l'introduction de gaz réactifs doit être gérée avec soin.
-
Réduire la densité des particules:
- En abaissant la densité des particules dans la chambre, le vide garantit que le matériau évaporé est l'espèce dominante, ce qui réduit la probabilité d'incorporation d'impuretés dans le film.
- Ceci est particulièrement important dans les applications nécessitant des films ultra-purs, telles que la fabrication de semi-conducteurs.
-
Prise en charge de taux d'évaporation thermique élevés:
- Un environnement sous vide facilite les taux d'évaporation thermique élevés en réduisant la perte d'énergie des atomes évaporés due aux collisions avec les molécules de gaz.
- Cette caractéristique est cruciale pour les procédés tels que l'évaporation résistive, où des taux d'évaporation élevés sont nécessaires pour un dépôt efficace.
-
Prévention des réactions chimiques:
- Le vide minimise la présence de gaz réactifs, empêchant les réactions chimiques indésirables entre le matériau du film et les gaz ambiants.
- C'est particulièrement important pour les matériaux très réactifs à l'oxygène ou à l'azote, car cela permet au film de conserver les propriétés souhaitées.
-
Atteindre l'ultravide pour des applications avancées:
- Pour les applications avancées, il est nécessaire d'atteindre des conditions d'ultravide (UHV) (10^-9 Torr ou moins) afin d'éliminer les gaz à l'état de traces qui peuvent causer des défauts.
- Les environnements UHV sont essentiels pour produire des couches minces sans défaut dans les industries de haute précision comme l'optique et la microélectronique.
En résumé, le vide est essentiel dans les processus de revêtement de couches minces car il garantit un environnement propre et contrôlé qui améliore le transport des matériaux, minimise la contamination et permet la formation de couches minces de haute qualité, uniformes et adhérentes.Ces avantages sont essentiels pour répondre aux exigences rigoureuses des applications modernes dans des secteurs tels que les semi-conducteurs, l'optique et l'aérospatiale.
Tableau récapitulatif :
Bénéfice principal | Explication |
---|---|
Minimiser la contamination | Réduit les gaz indésirables, garantissant des films minces d'une grande pureté. |
Augmentation du parcours libre moyen | Permet à la matière évaporée de parcourir de plus longues distances sans collision. |
Amélioration de la qualité des films | Assure une condensation uniforme et une forte adhérence des films minces. |
Contrôle de la composition des gaz | Permet un contrôle précis des gaz pour obtenir des propriétés de film spécifiques. |
Réduction de la densité des particules | Réduit l'incorporation d'impuretés, ce qui est essentiel pour les films ultra-purs. |
Favorise une évaporation élevée | Facilite les taux d'évaporation thermique élevés pour un dépôt efficace. |
Prévention des réactions chimiques | Minimise les gaz réactifs, préservant ainsi les propriétés du film. |
Atteindre l'ultravide | Élimine les traces de gaz pour des films sans défaut dans les applications avancées. |
Découvrez comment la technologie du vide peut améliorer vos processus de revêtement de couches minces. contactez nos experts dès aujourd'hui !