Introduction au dépôt en phase vapeur de silicium-carbone (VPD-SiC)
Avantages du VPD-SiC
Le VPD-SiC présente des améliorations substantielles par rapport aux matériaux conventionnels dans plusieurs domaines critiques, ce qui en fait un choix supérieur pour les applications de batteries avancées. Tout d'abord, l'efficacité duefficacité du premier tour du VPD-SiC est nettement plus élevée, ce qui se traduit par des cycles de charge-décharge initiaux plus efficaces et une perte d'énergie réduite. Cette amélioration est essentielle pour le déploiement rapide de batteries à haute performance dans diverses industries.
En outre, le VPD-SiC augmente considérablement lala densité énergétique. En intégrant des particules de silicium dans une matrice de carbone poreux, le matériau peut stocker plus d'énergie par unité de volume ou de masse, offrant ainsi des temps de fonctionnement plus longs et des fréquences de charge réduites. Ceci est particulièrement avantageux pour l'électronique portable, les véhicules électriques et les systèmes de stockage d'énergie renouvelable.
Lesperformance de cyclage du VPD-SiC est également supérieure, avec une stabilité accrue au cours de cycles de charge-décharge répétés. Cette durabilité est cruciale pour la longévité et la fiabilité des systèmes de batteries, car elle garantit des performances constantes sur de longues périodes sans dégradation.
En outre, le VPD-SiC atténue efficacement les effets suivantsl'expansion des cellules de la cellule, fréquents avec les anodes traditionnelles à base de silicium. Cette réduction de l'expansion du volume pendant les processus de charge et de décharge contribue à maintenir l'intégrité structurelle de la batterie, améliorant ainsi sa durée de vie et sa sécurité.
En termes deréduction des coûtsle VPD-SiC offre un potentiel d'industrialisation prometteur. Le processus de synthèse rationalisé, combiné à l'utilisation efficace des matières premières, peut conduire à des méthodes de production plus rentables. Cet avantage économique est essentiel pour augmenter la production et rendre les batteries à haute performance plus accessibles.
Dans l'ensemble, les avantages globaux du VPD-SiC en termes d'efficacité du premier tour, de densité énergétique, de performance de cyclage, d'expansion des cellules et de réduction des coûts en font un matériau transformateur pour la prochaine génération de technologies de batteries.
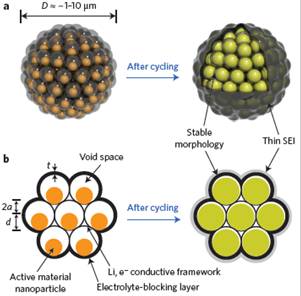
Principales étapes de la technologie VPD-SiC
Le processus de dépôt en phase vapeur (VPD) pour la création de matériaux d'anode en silicium-carbone (SiC) est une procédure en plusieurs étapes qui intègre plusieurs étapes critiques pour obtenir des solutions de stockage d'énergie à haute performance. La technologie peut être décomposée en trois phases principales : la préparation d'un squelette de carbone poreux, le dépôt de particules de silicium et l'application d'une couche de carbone.
-
Préparation du squelette de carbone poreux:
- Le fondement du processus VPD-SiC, le squelette de carbone poreux, est méticuleusement élaboré pour fournir un cadre robuste qui améliore les performances globales du matériau. Cette étape est essentielle pour créer une structure dotée d'une surface spécifique élevée et d'une excellente conductivité électrique, qui sont vitales pour améliorer la capacité de l'anode et la stabilité du cycle.
-
Dépôt de particules de silicium:
- Une fois le squelette de carbone poreux établi, l'étape suivante consiste à déposer des particules de silicium dans les pores. Cette étape est généralement réalisée grâce à l'utilisation de gaz silane, qui joue un rôle essentiel dans la formation de silicium dans la matrice de carbone. Le processus de dépôt est très sensible à des paramètres tels que la température et les débits de gaz, qui doivent être contrôlés avec précision pour garantir une distribution uniforme des particules et des propriétés optimales du matériau.
-
Couche de carbone:
- L'étape finale de la technologie VPD-SiC consiste à recouvrir le composite silicium-carbone d'une couche de carbone. Cette couche a plusieurs fonctions : elle protège les particules de silicium de la dégradation, améliore la conductivité électrique du matériau et apporte une stabilité mécanique supplémentaire. La couche de carbone est généralement appliquée par dépôt chimique en phase vapeur (CVD) ou par d'autres techniques similaires, ce qui permet d'obtenir une couche uniforme et continue qui encapsule efficacement les particules de silicium.
Chacune de ces étapes est interdépendante et leur intégration réussie est cruciale pour la production de matériaux d'anode silicium-carbone de haute qualité qui répondent aux exigences rigoureuses des applications modernes de stockage d'énergie.
Synthèse des matériaux en carbone poreux
Importance du carbone poreux
Les matériaux à base de carbone poreux jouent un rôle essentiel dans l'optimisation des anodes silicium-carbone, en améliorant de manière significative leurs performances globales. Cette amélioration est principalement attribuée à plusieurs propriétés clés inhérentes au carbone poreux.
Tout d'abord, la surface spécifique élevée du carbone poreux fournit une plateforme étendue pour le dépôt de particules de silicium. Cette grande surface garantit une répartition uniforme des particules de silicium, ce qui est essentiel pour maintenir l'intégrité structurelle et les performances de l'anode.
Deuxièmement, l'excellente conductivité électrique du carbone poreux facilite le transfert efficace d'électrons dans le matériau de l'anode. Cette propriété est vitale pour maintenir une efficacité énergétique élevée et réduire la résistance interne, ce qui est essentiel pour la performance à long terme et la durabilité de l'anode.
Enfin, la bonne stabilité mécanique du carbone poreux contribue à la résilience structurelle de l'anode. Cette stabilité est particulièrement importante lors des cycles répétés de charge et de décharge, car elle permet d'atténuer les changements de volume que subissent les particules de silicium, empêchant ainsi la dégradation et prolongeant la durée de vie de l'anode.
En résumé, la combinaison d'une surface spécifique élevée, d'une excellente conductivité électrique et d'une bonne stabilité mécanique rend les matériaux de carbone poreux indispensables à l'avancement des anodes silicium-carbone dans la technologie des batteries.
Considérations relatives à la synthèse
Lors de la synthèse de matériaux de carbone poreux pour les anodes silicium-carbone, plusieurs facteurs critiques doivent être méticuleusement pris en compte pour garantir des performances et une évolutivité optimales. La conception de la structure des pores est primordiale, car elle influence directement la capacité du matériau à s'adapter aux changements de volume pendant les cycles de lithiation et de délithiation. Une structure de pores bien conçue peut améliorer de manière significative la stabilité du cycle de l'anode et la conservation de sa capacité.
La sélection des précurseurs est un autre aspect essentiel. Le choix du matériau précurseur affecte non seulement les propriétés finales du carbone poreux, mais aussi la facilité de synthèse et le coût du matériau. Les précurseurs ayant un rendement élevé en carbone et une faible teneur en cendres sont généralement préférés, car ils facilitent la formation d'une matrice de carbone uniforme et conductrice. En outre, le précurseur doit être compatible avec des techniques de production évolutives afin de garantir la faisabilité de la fabrication à grande échelle.
L'évolutivité de la production à grande échelle est une considération non négociable. Le processus de synthèse doit pouvoir être adapté aux réacteurs industriels, afin de garantir une qualité et un rendement constants. Cela implique d'optimiser les conditions de réaction, telles que la température, la pression et les concentrations de réactifs, afin d'obtenir un dépôt uniforme de particules de silicium dans le carbone poreux. En outre, le processus doit minimiser la consommation d'énergie et la production de déchets, en s'alignant sur les pratiques de fabrication durable.
En résumé, la synthèse de matériaux de carbone poreux pour les anodes silicium-carbone nécessite une approche holistique, équilibrant la conception de la structure des pores, la sélection des précurseurs et l'extensibilité pour répondre aux exigences de performance et d'application industrielle.
Silane et processus de dépôt
Rôle du silane gazeux
Le gaz silane (SiH₄) joue un rôle essentiel dans le dépôt de particules de silicium dans la structure poreuse du carbone, une étape critique dans la fabrication de matériaux d'anode silicium-carbone. L'efficacité de ce processus dépend de la gestion minutieuse des propriétés du silane et de l'équilibre complexe des paramètres de dépôt.
L'un des principaux défis liés à l'utilisation du silane est sa sensibilité aux conditions environnementales. Par exemple, l'introduction d'oxygène dans la chambre de dépôt peut entraîner la formation de SiOH, ce qui nuit à la qualité du film de silicium. À l'inverse, en l'absence d'oxygène, on peut obtenir des films de silicium amorphes, qui sont à la fois purs et adaptés au dépôt. Cela souligne la nécessité d'un contrôle précis de l'environnement de dépôt afin d'éviter les réactions chimiques indésirables.
En outre, le coût et la disponibilité du silane sont des facteurs importants qui influencent la faisabilité d'une production à grande échelle. Le matériau doit être manipulé avec précaution en raison de sa nature réactive, ce qui nécessite un équipement spécialisé et des protocoles de sécurité pour atténuer les risques. En outre, le processus de dépôt nécessite un équilibre délicat entre le silane et d'autres gaz, tels que l'oxygène et le xénon, afin d'obtenir le composite silicium-carbone souhaité.
Pour optimiser le processus de dépôt, il est essentiel de maintenir des taux moyens d'introduction de silane. Un excès de silane peut entraîner la formation de SIH, tandis qu'un excès d'oxygène peut conduire à la formation de SiOH, deux phénomènes qui dégradent la qualité du produit final. Il est essentiel de trouver le bon équilibre pour obtenir des films de silicium à la fois amorphes et durs, ce qui améliore les caractéristiques de performance de l'anode.
En résumé, le rôle du gaz silane dans le processus de dépôt est multiple et nécessite une compréhension approfondie de ses propriétés chimiques et une gestion minutieuse des paramètres de dépôt pour garantir la production de matériaux d'anode silicium-carbone de haute qualité.
Paramètres du processus de dépôt
Les paramètres du processus de dépôt jouent un rôle essentiel dans la détermination de la qualité et des performances des matériaux d'anode silicium-carbone (Si-C). Les paramètres clés comprennent la température de dépôt, les conditions de réaction et les mesures de sécurité strictes, chacun d'entre eux influençant de manière significative les caractéristiques du produit final.
Influence de la température
La température de dépôt est un facteur critique qui affecte directement l'uniformité et la densité des particules de silicium dans la matrice de carbone poreux. Des températures plus élevées peuvent améliorer la diffusion du gaz silane dans les pores du carbone, ce qui conduit à un dépôt plus uniforme. Toutefois, des températures trop élevées peuvent également entraîner une dégradation thermique de la structure du carbone, réduisant ainsi sa stabilité mécanique et sa surface spécifique. Il est donc essentiel d'optimiser la température de dépôt pour équilibrer ces effets contradictoires.
Conditions de réaction
Les conditions de réaction, telles que les débits de gaz et la pression, sont tout aussi importantes. Elles déterminent le temps de séjour des réactifs dans la chambre de dépôt et la vitesse de formation des particules de silicium. Par exemple, un débit de gaz plus élevé peut entraîner des temps de séjour plus courts, ce qui risque de réduire l'uniformité du dépôt de silicium. Inversement, un débit plus faible peut améliorer le processus de dépôt, mais peut aussi augmenter le risque de colmatage ou d'autres problèmes opérationnels. Un contrôle précis de ces conditions est donc nécessaire pour obtenir des propriétés optimales du matériau silicium-carbone.
Mesures de sécurité
Étant donné la nature dangereuse du gaz silane, des mesures de sécurité strictes sont indispensables pendant le processus de dépôt. Ces mesures comprennent l'utilisation de systèmes avancés de détection des gaz, de protocoles d'arrêt d'urgence et de systèmes de ventilation robustes pour atténuer le risque de fuites ou d'explosions. Garantir un environnement de travail sûr permet non seulement de protéger le personnel, mais aussi d'assurer la fiabilité et la cohérence du processus de dépôt, ce qui est crucial pour la production à l'échelle industrielle.
En résumé, les paramètres du processus de dépôt - température, conditions de réaction et mesures de sécurité - sont étroitement liés aux performances et à la qualité des matériaux d'anode silicium-carbone. L'optimisation de ces paramètres est essentielle pour améliorer les propriétés électrochimiques du matériau et garantir sa viabilité pour des applications à grande échelle.
Équipement de dépôt
Types d'équipements de dépôt
Les fours rotatifs et les lits fluidisés sont les principaux types d'équipements utilisés dans le processus de dépôt des matériaux d'anode en silicium-carbone. Chaque type d'équipement offre des avantages et des défis distincts, qui sont des considérations cruciales pour obtenir des propriétés de matériaux et une évolutivité optimales.
Fours rotatifs
- Simplicité opérationnelle: Les fours rotatifs sont relativement simples à utiliser, ce qui en fait un choix privilégié pour les expériences initiales et la production à petite échelle.
- Rentabilité: Ils sont généralement plus rentables en termes d'investissement et de coûts d'exploitation, ce qui peut être avantageux pour les projets pilotes.
- Souplesse: Les fours rotatifs offrent une certaine souplesse dans le traitement de divers matériaux précurseurs et peuvent être adaptés à différentes conditions de dépôt.
Lits fluidisés
- Uniformité et efficacité: Les lits fluidisés sont réputés pour l'uniformité supérieure de la distribution des particules et les taux plus élevés d'utilisation du gaz silane. Il en résulte des propriétés de matériaux plus homogènes et des performances globales améliorées.
- Mesures de sécurité renforcées: L'utilisation de lits fluidisés nécessite des protocoles de sécurité rigoureux en raison de la réactivité élevée du gaz silane. Des systèmes de sécurité avancés et une surveillance continue sont essentiels pour atténuer les risques associés aux fuites de gaz et autres dangers.
- Complexité et fiabilité: Malgré leurs avantages, les lits fluidisés sont plus complexes et nécessitent une grande fiabilité pour assurer un fonctionnement continu et stable. Cette complexité peut poser des problèmes lors de la mise à l'échelle pour une production à l'échelle industrielle.
En résumé, si les fours rotatifs constituent une solution plus simple et plus rentable, les lits fluidisés offrent une uniformité et une efficacité accrues, mais avec une complexité et des exigences de sécurité accrues. Le choix de l'équipement dépend des besoins spécifiques et de l'échelle du processus de production.
Les défis de l'industrialisation
La production à grande échelle de matériaux d'anodes silicium-carbone à l'aide de lits fluidisés présente plusieurs défis importants. Il s'agit principalement d'assurer un fonctionnement continu, de maintenir l'uniformité du processus de dépôt et d'obtenir une utilisation élevée du gaz silane.
L'un des principaux obstacles est la nécessité del'optimisation de l'équipement et du processus. Les lits fluidisés, tout en offrant une uniformité et une utilisation du silane supérieures, nécessitent un contrôle méticuleux de divers paramètres tels que la température, les débits de gaz et la distribution de la taille des particules. Tout écart par rapport à ces conditions optimales peut entraîner une incohérence dans les propriétés des matériaux, ce qui est préjudiciable aux performances globales de l'anode.
En outre, lafiabilité et la sécurité du système de lit fluidisé sont essentielles. L'utilisation de gaz silane, hautement réactif et potentiellement explosif, nécessite des mesures de sécurité robustes et une surveillance continue. Cela ajoute une couche de complexité au processus d'industrialisation, exigeant des systèmes d'automatisation et de contrôle avancés pour garantir un fonctionnement sûr et efficace.
En outre, lévolutivité du processus de lit fluidisé est une préoccupation importante. Le passage d'expériences en laboratoire à une production industrielle à grande échelle nécessite une réflexion approfondie sur la manière de maintenir le même niveau de contrôle et d'uniformité sur des volumes plus importants. Cela implique souvent des investissements importants dans la modernisation des équipements et l'amélioration des procédés.
En résumé, si les lits fluidisés offrent des avantages prometteurs pour la production d'anodes en silicium-carbone, leur industrialisation nécessite de relever des défis techniques et opérationnels considérables. Il s'agit notamment d'optimiser les équipements et les procédés, de garantir la fiabilité et la sécurité et de résoudre les problèmes d'évolutivité pour parvenir à une production continue à grande échelle.
CONTACTEZ-NOUS POUR UNE CONSULTATION GRATUITE
Les produits et services de KINTEK LAB SOLUTION ont été reconnus par des clients du monde entier. Notre personnel se fera un plaisir de répondre à toute demande que vous pourriez avoir. Contactez-nous pour une consultation gratuite et parlez à un spécialiste produit pour trouver la solution la plus adaptée aux besoins de votre application !