Un four rotatif, également connu sous le nom de four tournant, est un dispositif de chauffage spécialisé utilisé pour des processus tels que la fusion, la calcination et le traitement thermique des matériaux.Il fonctionne par rotation d'une chambre cylindrique autour de son axe central, ce qui permet de mélanger et de chauffer uniformément les matériaux au fur et à mesure de leur passage dans le four.La rotation assure une distribution uniforme de la chaleur et un traitement efficace, ce qui le rend idéal pour les applications dans la métallurgie, le traitement chimique et le traitement des déchets.Les principes de fonctionnement et les principaux composants d'un four rotatif sont décrits en détail ci-dessous.
Explication des points clés :
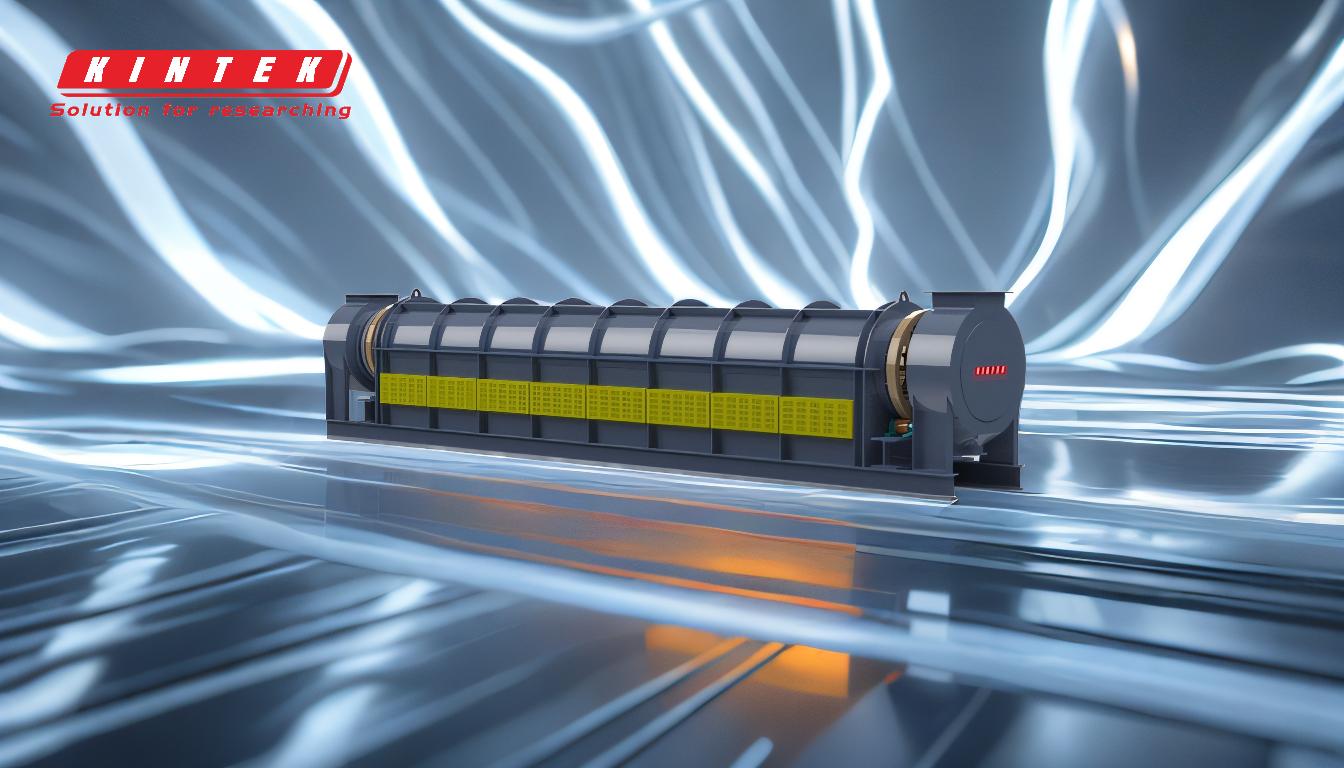
-
Structure et composants:
- Chambre cylindrique:Le corps principal du four rotatif est un tube cylindrique, généralement constitué de matériaux résistants à la chaleur tels que des briques réfractaires ou des métaux.Cette chambre tourne autour de son axe central.
- Système de chauffage:Le four est équipé de brûleurs ou d'éléments chauffants électriques qui fournissent la chaleur nécessaire au traitement des matériaux.La source de chaleur est placée stratégiquement pour assurer un chauffage uniforme.
- Mécanisme d'entraînement:Un système motorisé fait tourner la chambre à une vitesse contrôlée, assurant un mouvement régulier des matériaux à l'intérieur.
- Systèmes d'alimentation et de décharge:Les matériaux sont introduits à une extrémité du four et se déplacent progressivement vers l'extrémité de décharge au fur et à mesure de la rotation de la chambre.
-
Traitement des matériaux:
- La charge minérale ou le matériau est introduit dans la partie réacteur du four.Au fur et à mesure que la chambre tourne, le matériau est transporté le long du tube.
- La rotation assure un mélange complet et une exposition à la chaleur, ce qui est essentiel pour des processus tels que la fusion ou la calcination.Ce mouvement empêche également les matières de coller aux parois ou de former des amas.
-
Mécanisme de chauffage:
- Le système de chauffage porte la température à l'intérieur de la chambre au niveau requis, en fonction du matériau et du processus.La chaleur est répartie uniformément grâce à la rotation de la chambre.
- Dans certains cas, le four peut fonctionner sous atmosphère contrôlée ou sous vide afin d'obtenir des résultats de traitement spécifiques.
-
Les applications:
- Métallurgie:Utilisé pour la fusion des métaux et des alliages, où un chauffage et un mélange uniformes sont essentiels.
- Traitement chimique:Idéal pour la calcination, la pyrolyse et d'autres traitements thermiques de produits chimiques.
- Traitement des déchets:Efficace pour l'incinération des déchets dangereux ou la récupération de matériaux précieux à partir de sous-produits industriels.
-
Avantages:
- Chauffage uniforme:Le mouvement de rotation assure une distribution uniforme de la chaleur, réduisant ainsi le risque de points chauds ou de traitement inégal.
- Mélange efficace:L'action des matériaux en mouvement favorise un mélange complet, ce qui est crucial pour les réactions chimiques ou les transformations de phase.
- Polyvalence:Convient à une large gamme de matériaux et de procédés, ce qui en fait un outil polyvalent pour les applications industrielles.
-
Comparaison avec d'autres fours:
- Contrairement à un four à poussoir qui déplace les matériaux de manière linéaire, un four rotatif repose sur la rotation pour le transport et le mélange des matériaux.
- Contrairement à un four sous vide Un four rotatif fonctionne généralement à la pression atmosphérique, à moins qu'il ne soit spécifiquement conçu pour des conditions de vide.
En résumé, un four rotatif est un dispositif de chauffage très efficace et polyvalent qui s'appuie sur la rotation de sa chambre pour assurer un chauffage et un mélange uniformes des matériaux.Sa conception et son fonctionnement le rendent adapté à un large éventail d'applications industrielles, de la métallurgie au traitement des déchets.Pour plus de détails, voir la rubrique le four rotatif .
Tableau récapitulatif :
Aspect clé | Description de la structure |
---|---|
Structure de l'appareil | Chambre cylindrique en matériaux résistants à la chaleur, tournant autour de son axe. |
Système de chauffage | Brûleurs ou éléments électriques pour un chauffage uniforme. |
Mécanisme d'entraînement | Système motorisé pour une rotation contrôlée. |
Traitement des matériaux | Les matériaux sont mélangés et chauffés uniformément lors de leur passage dans le four. |
Applications | Métallurgie, traitement chimique et traitement des déchets. |
Avantages | Chauffage uniforme, mélange efficace et polyvalence. |
Découvrez comment un four rotatif peut optimiser vos processus industriels. contactez nos experts dès aujourd'hui !