Le processus de pulvérisation PVD est une technique de dépôt de couches minces largement utilisée qui implique l'éjection d'atomes ou de molécules d'un matériau cible par bombardement d'ions à haute énergie, généralement des ions d'argon.Ces atomes éjectés traversent une chambre à vide et se condensent sur un substrat pour former un film mince et uniforme.Le processus commence par la génération de plasma, qui contient des ions argon et des électrons.Ces ions sont accélérés vers le matériau cible, ce qui provoque la pulvérisation d'atomes.Les atomes pulvérisés traversent ensuite la chambre et se déposent sur le substrat, créant ainsi un film mince.Cette méthode est hautement contrôlable et est utilisée dans diverses industries, notamment les semi-conducteurs, l'optique et les revêtements décoratifs.
Explication des points clés :
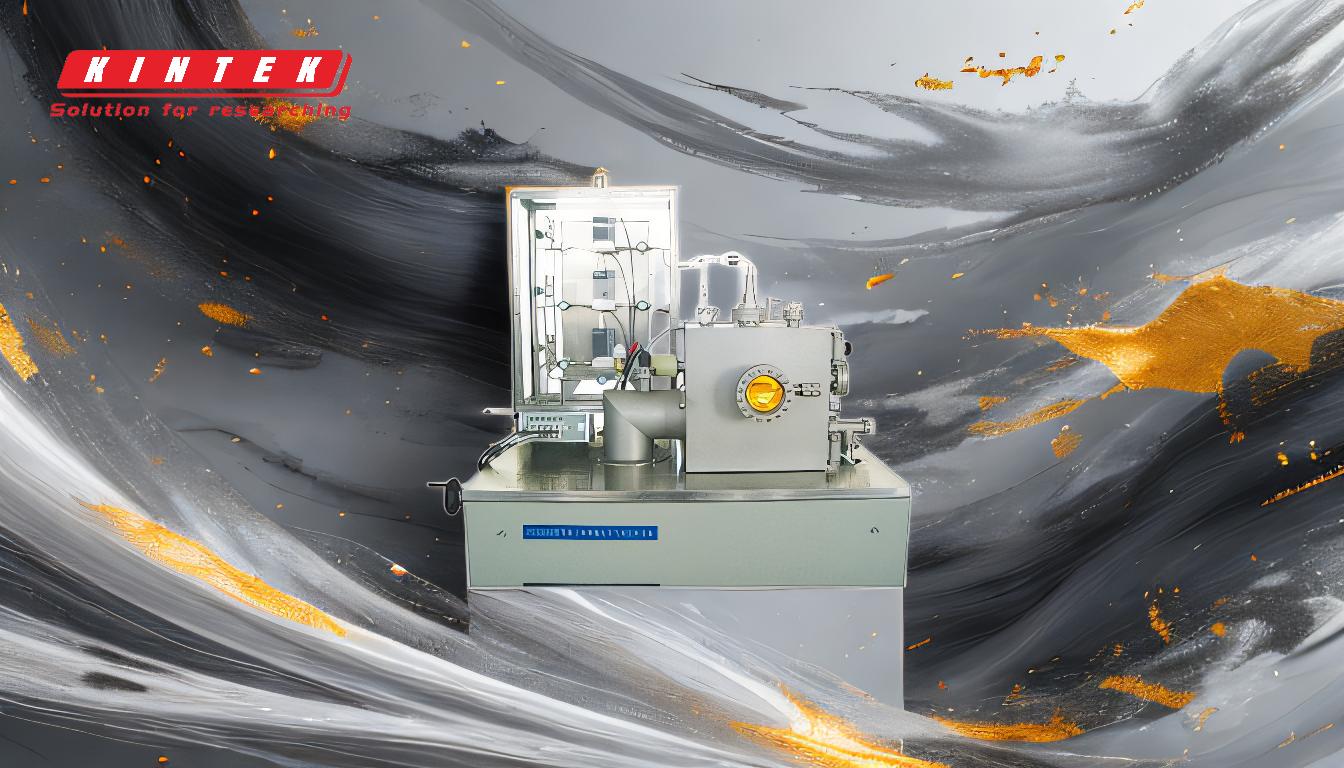
-
Introduction à la pulvérisation cathodique PVD:
- La pulvérisation PVD (Physical Vapor Deposition) est un procédé utilisé pour déposer des couches minces de matériaux sur un substrat.
- Il s'agit d'une technique sous vide dans laquelle des atomes ou des molécules sont éjectés d'un matériau cible et déposés sur un substrat.
-
Génération de plasma:
- Le processus commence par la génération d'un plasma à l'intérieur d'une chambre à vide.
- Le plasma est créé par l'ionisation d'un gaz, généralement de l'argon, qui produit un mélange d'ions argon et d'électrons.
- Ce plasma est essentiel pour le processus de pulvérisation car il fournit les ions à haute énergie nécessaires pour bombarder le matériau cible.
-
Bombardement du matériau cible:
- Des ions d'argon à haute énergie provenant du plasma sont accélérés vers le matériau cible.
- Lorsque ces ions atteignent la cible, ils transfèrent leur énergie aux atomes du matériau cible.
- Ce transfert d'énergie entraîne l'éjection d'atomes ou de molécules de la surface de la cible, un processus connu sous le nom de pulvérisation cathodique.
-
Transport des atomes pulvérisés:
- Les atomes ou molécules éjectés traversent la chambre à vide.
- L'environnement sous vide garantit que les atomes pulvérisés se déplacent en ligne droite sans entrer en collision avec des molécules de gaz, ce qui pourrait modifier leur trajectoire et réduire la qualité du film déposé.
-
Dépôt sur le substrat:
- Les atomes pulvérisés atteignent finalement le substrat, où ils se condensent et forment un film mince.
- Le substrat est généralement placé en face du matériau cible afin de garantir un dépôt uniforme.
- L'épaisseur et les propriétés du film peuvent être contrôlées en ajustant des paramètres tels que la puissance appliquée au plasma, la pression dans la chambre et la distance entre la cible et le substrat.
-
Avantages de la pulvérisation cathodique PVD:
- Précision:Le procédé permet un contrôle précis de l'épaisseur et de la composition du film déposé.
- Polyvalence:Il peut être utilisé pour déposer une large gamme de matériaux, y compris les métaux, les alliages et les céramiques.
- Uniformité:L'environnement sous vide et les paramètres contrôlés garantissent un dépôt de film uniforme et cohérent.
- Adhésion:Le processus à haute énergie permet une forte adhésion du film au substrat.
-
Applications de la pulvérisation PVD:
- Semi-conducteurs:Utilisé dans la fabrication de circuits intégrés et d'autres composants électroniques.
- Optique:Appliqué dans la production de revêtements antireflets, de miroirs et de filtres optiques.
- Revêtements décoratifs:Utilisés pour créer des finitions durables et esthétiques sur les produits de consommation.
- Revêtements durs:Appliqué aux outils et aux composants pour améliorer la résistance à l'usure et la durabilité.
-
Défis et considérations:
- Coût:L'équipement et l'environnement sous vide requis pour la pulvérisation cathodique en phase vapeur peuvent être coûteux.
- La complexité:Le processus nécessite un contrôle précis des différents paramètres, ce qui peut être complexe et requiert des opérateurs qualifiés.
- Limites des matériaux:Bien que polyvalents, tous les matériaux ne peuvent pas être facilement pulvérisés, et certains peuvent nécessiter des conditions ou des cibles spécialisées.
En résumé, la pulvérisation cathodique PVD est une technique de dépôt de couches minces très contrôlée et polyvalente qui implique l'éjection d'atomes d'un matériau cible par bombardement ionique à haute énergie.Ce procédé est largement utilisé dans diverses industries en raison de sa précision, de son uniformité et de sa capacité à déposer une large gamme de matériaux.Cependant, il présente également des difficultés telles que le coût et la complexité, qui doivent être prises en compte lors de la sélection de cette méthode pour des applications spécifiques.
Tableau récapitulatif :
Aspect | Détails |
---|---|
Aperçu du procédé | Éjection d'atomes d'un matériau cible par bombardement ionique à haute énergie. |
Étapes clés | Génération de plasma, bombardement de la cible, transport des atomes et dépôt d'un film. |
Avantages | Précision, polyvalence, uniformité et forte adhérence. |
Applications | Semi-conducteurs, optique, revêtements décoratifs et revêtements durs. |
Défis | Coût élevé, complexité du processus et limitation des matériaux. |
Découvrez comment la pulvérisation cathodique PVD peut améliorer votre processus de fabrication. contactez nos experts dès aujourd'hui !