Le processus de pulvérisation est une technique largement utilisée pour déposer des couches minces de matériaux sur des substrats.Il consiste à créer un vide dans une chambre de réaction, à introduire un gaz inerte comme l'argon et à ioniser le gaz pour former un plasma.Des ions à haute énergie provenant du plasma bombardent un matériau cible, provoquant l'éjection d'atomes qui se déposent sur un substrat pour former un film mince.Ce processus est hautement contrôlable et peut être utilisé pour déposer une large gamme de matériaux avec une épaisseur et une uniformité précises.Les étapes clés comprennent la création d'un vide, l'introduction et l'ionisation du gaz, la génération d'un plasma et l'accélération des ions pour pulvériser les atomes cibles sur le substrat.
Explication des points clés :
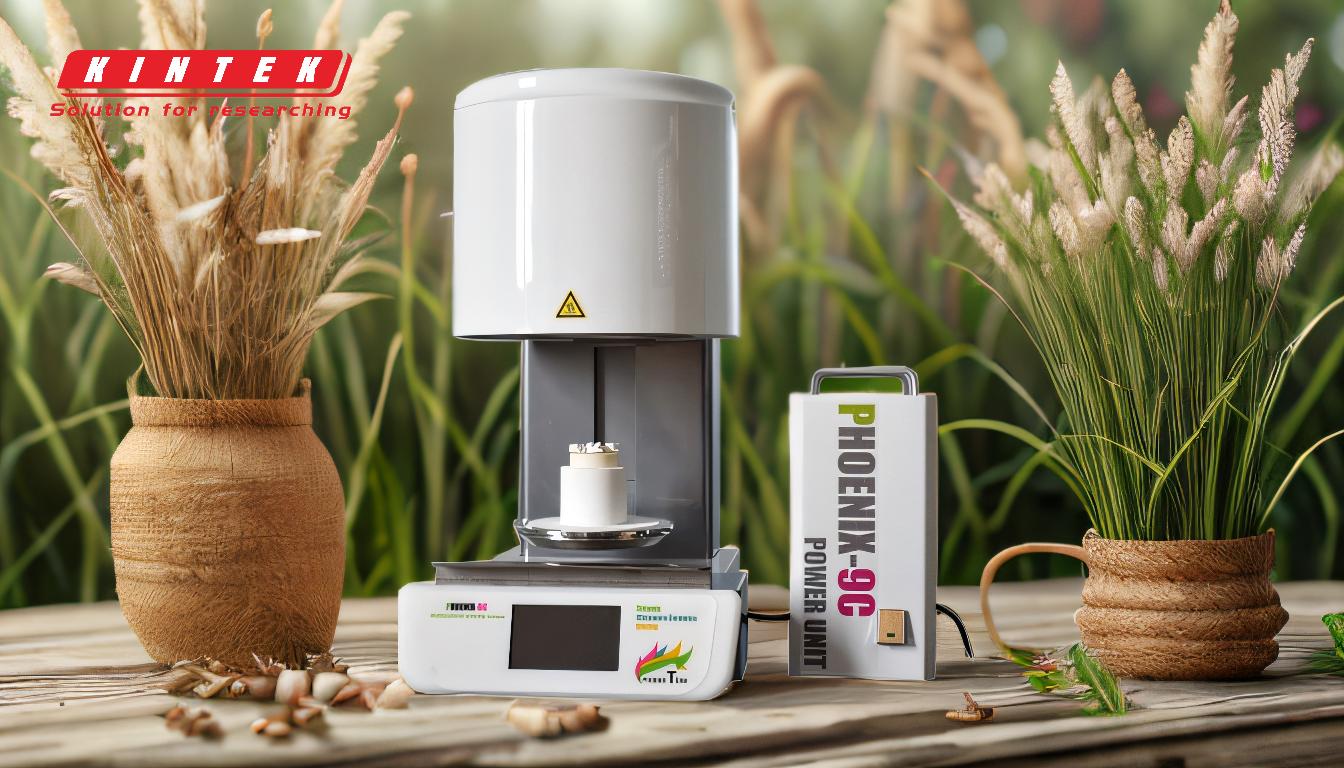
-
Création d'un vide dans la chambre:
- La première étape du processus de pulvérisation consiste à créer un vide dans la chambre de réaction.Il s'agit de réduire la pression interne à environ 1 Pa (0,0000145 psi) pour éliminer l'humidité et les impuretés.L'environnement sous vide est crucial car il empêche la contamination par des gaz résiduels et garantit une surface propre pour le dépôt.Le vide permet également de mieux contrôler le processus de pulvérisation en minimisant les réactions indésirables.
-
Introduction d'un gaz inerte:
- Une fois le vide établi, un gaz inerte, généralement de l'argon, est introduit dans la chambre.L'argon est choisi parce qu'il est chimiquement inerte, c'est-à-dire qu'il ne réagit pas avec le matériau cible ou le substrat.Le gaz est introduit à une pression contrôlée, généralement comprise entre 10-1 et 10-3 mbar.Cet environnement à basse pression est essentiel pour maintenir la stabilité du plasma qui sera généré dans les étapes suivantes.
-
Génération d'un plasma:
- Une haute tension (généralement de 3 à 5 kV) est appliquée à travers la chambre pour ioniser le gaz argon et créer un plasma.Le plasma est constitué d'ions argon chargés positivement et d'électrons libres.Le processus d'ionisation est souvent renforcé par la présence d'un champ magnétique, qui contribue à confiner le plasma et à augmenter la densité des ions.Cette étape est cruciale car le plasma est la source des ions à haute énergie qui seront utilisés pour pulvériser le matériau cible.
-
Accélération des ions vers la cible:
- Le matériau cible, qui est la source des atomes à déposer, est chargé négativement (cathode).Les ions argon chargés positivement dans le plasma sont attirés par la cible chargée négativement.Lorsque ces ions entrent en collision avec la cible, ils transfèrent leur énergie cinétique aux atomes de la cible.Ce transfert d'énergie est suffisant pour déloger les atomes de la surface de la cible, un processus connu sous le nom de pulvérisation.
-
Ejection et dépôt des atomes de la cible:
- Les atomes pulvérisés sont éjectés de la surface de la cible sous forme de particules neutres.Ces particules traversent la chambre à vide et sont transportées vers le substrat.Le substrat est généralement placé en face de la cible, et les atomes pulvérisés se condensent sur sa surface, formant un film mince.Le processus de dépôt est hautement contrôlé, ce qui permet d'obtenir une épaisseur et une uniformité précises du film.
-
Formation d'un film mince:
- Les atomes pulvérisés qui atteignent le substrat adhèrent à sa surface, formant un film mince.Les propriétés du film, telles que l'épaisseur, l'uniformité et l'adhérence, sont influencées par divers facteurs, notamment l'énergie des atomes pulvérisés, la température du substrat et la pression à l'intérieur de la chambre.Le substrat peut être chauffé à des températures allant de 150°C à 750°C, en fonction des propriétés souhaitées du revêtement.Ce chauffage permet d'améliorer l'adhérence et la qualité du film déposé.
-
Rôle des champs magnétiques:
- Dans certains systèmes de pulvérisation, un champ magnétique est utilisé pour renforcer le processus d'ionisation et confiner le plasma autour de la cible.C'est ce qu'on appelle la pulvérisation magnétron.Le champ magnétique augmente la densité du plasma, ce qui entraîne un taux plus élevé de bombardement ionique sur la cible.Il en résulte un processus de pulvérisation plus efficace et des taux de dépôt plus élevés.
-
Contrôle et optimisation:
- Le processus de pulvérisation est hautement contrôlable, avec différents paramètres qui peuvent être ajustés pour optimiser le dépôt.Ces paramètres comprennent la tension appliquée, la pression du gaz inerte, l'intensité du champ magnétique et la température du substrat.En contrôlant soigneusement ces variables, il est possible de déposer des couches minces ayant des propriétés spécifiques, telles que la conductivité électrique, la transparence optique ou la résistance mécanique.
-
Applications de la pulvérisation cathodique:
- La pulvérisation est utilisée dans un large éventail d'applications, notamment la fabrication de semi-conducteurs, de revêtements optiques et de cellules solaires en couches minces.Elle est également utilisée dans la production de revêtements durs pour les outils et de revêtements décoratifs pour les produits de consommation.La capacité de déposer une grande variété de matériaux avec un contrôle précis fait de la pulvérisation une technique polyvalente et précieuse dans la fabrication moderne et la recherche.
En résumé, le processus de pulvérisation est une méthode complexe mais hautement contrôlée pour déposer des couches minces de matériaux sur des substrats.Il s'agit de créer un vide, d'introduire un gaz inerte, de générer un plasma et d'utiliser des ions à haute énergie pour pulvériser des atomes d'un matériau cible sur un substrat.Le processus est influencé par divers paramètres, notamment la tension, la pression, les champs magnétiques et la température du substrat, qui peuvent être ajustés pour obtenir les propriétés souhaitées du film.La pulvérisation est largement utilisée dans des secteurs allant de l'électronique à l'optique, ce qui en fait une technologie essentielle dans la fabrication moderne.
Tableau récapitulatif :
Étape | Description de l'étape |
---|---|
1.Créer un vide | Réduire la pression de la chambre à ~1 Pa pour éliminer les impuretés et assurer un dépôt propre. |
2.Introduction du gaz inerte | Ajouter de l'argon à une concentration de 10-1 à 10-3 mbar pour maintenir la stabilité du plasma. |
3.Générer un plasma | Appliquer 3-5 kV pour ioniser le gaz argon, créant ainsi un plasma d'ions et d'électrons. |
4.Accélérer les ions | Des ions chargés positivement bombardent le matériau cible chargé négativement. |
5.Éjection des atomes cibles | Les atomes cibles sont pulvérisés et déposés sur le substrat. |
6.Formation d'un film mince | Les atomes pulvérisés se condensent sur le substrat, formant un film mince uniforme. |
7.Utiliser des champs magnétiques | Les champs magnétiques améliorent la densité du plasma et l'efficacité de la pulvérisation (pulvérisation magnétron). |
8.Optimisation des paramètres | Ajuster la tension, la pression, le champ magnétique et la température du substrat pour obtenir les propriétés souhaitées du film. |
9.Applications | Utilisé dans les semi-conducteurs, les revêtements optiques, les cellules solaires et les revêtements durs. |
Découvrez comment la pulvérisation cathodique peut révolutionner vos applications de couches minces. contactez nos experts dès aujourd'hui !