Le processus de revêtement PVD (Physical Vapor Deposition) est une technique sophistiquée utilisée pour appliquer des revêtements fins et durables sur divers matériaux, principalement des métaux. La durée du processus peut varier considérablement, allant généralement de 30 minutes à 2 heures, en fonction de facteurs tels que l'épaisseur de revêtement souhaitée, la taille de la pièce et le type spécifique de processus PVD utilisé. L'épaisseur du revêtement est généralement comprise entre 0,25 microns et 5 microns, et le processus comporte plusieurs étapes clés : vaporisation, réaction et dépôt. Chaque étape joue un rôle crucial dans la détermination des propriétés finales du revêtement, telles que la dureté, la couleur et la résistance à la corrosion et à l'oxydation.
Points clés expliqués :
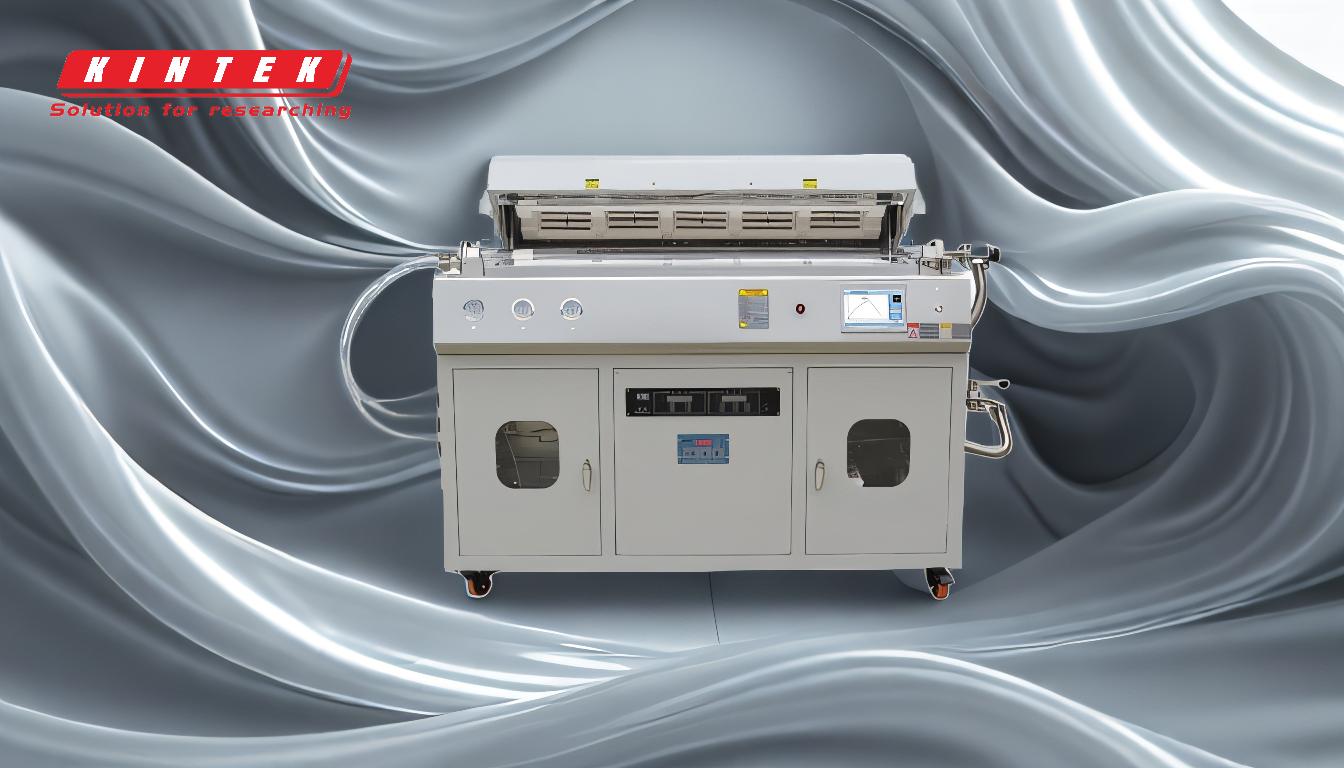
-
Durée du processus de revêtement PVD :
- Le processus de revêtement PVD prend généralement entre 30 minutes et 2 heures. Les pièces plus petites ou plus simples peuvent nécessiter moins de temps, tandis que les pièces plus grandes ou plus complexes peuvent prendre plus de temps.
- Le temps requis peut également dépendre de l’épaisseur de revêtement souhaitée, des revêtements plus épais nécessitant des temps de traitement plus longs.
-
Épaisseur du revêtement :
- Les revêtements PVD sont généralement très fins, allant de 0,25 microns à 5 microns. Cette fine couche est suffisante pour apporter des améliorations significatives des propriétés telles que la dureté, la résistance à la corrosion et l’aspect esthétique.
- L'épaisseur du revêtement est un facteur critique pour déterminer la durabilité et les performances globales du matériau revêtu.
-
Types de processus de revêtement PVD :
- Revêtement par pulvérisation : Implique le bombardement d’un matériau cible avec des ions à haute énergie pour éjecter des atomes, qui se déposent ensuite sur le substrat.
- Évaporation thermique : Utilise la chaleur pour vaporiser le matériau de revêtement, qui se condense ensuite sur le substrat.
- Évaporation par faisceau d'électrons : Utilise un faisceau d'électrons pour chauffer et vaporiser le matériau de revêtement.
- Placage ionique : Combine la vaporisation avec le bombardement ionique pour améliorer l’adhérence et la densité du revêtement.
- Chaque procédé présente des caractéristiques et des avantages uniques, ce qui les rend adaptés à différentes applications et matériaux.
-
Étapes du processus de revêtement PVD :
- Vaporisation: Le matériau cible est converti en vapeur par diverses méthodes telles que la pulvérisation ou l'évaporation.
- Réaction: Le matériau vaporisé réagit avec les gaz présents dans la chambre pour former des composés qui déterminent les propriétés du revêtement, telles que la dureté et la couleur.
- Déposition: Le matériau vaporisé et réagi se dépose sur le substrat, formant un revêtement mince et uniforme.
-
Propriétés et applications :
- Les revêtements PVD sont très résistants à la corrosion et à l’oxydation, ce qui les rend idéaux pour une utilisation dans des environnements difficiles.
- La dureté du revêtement est un facteur crucial dans sa durabilité, avec des matériaux comme le TiN (nitrure de titane) améliorant considérablement la limite de fatigue et l'endurance du substrat.
- Les revêtements PVD sont couramment appliqués sur l'acier inoxydable, offrant une variété de finitions telles que polie, brossée, satinée ou mate, selon la préparation de la surface.
-
Préparation des surfaces :
- L’état de surface du support est essentiel pour obtenir la finition souhaitée. Les surfaces polies ou miroir sont utilisées pour les finitions PVD polies, tandis que les surfaces brossées ou satinées sont utilisées pour les finitions satinées ou mates.
- Les revêtements PVD ne nivellent ni ne comblent les imperfections de la surface, le substrat doit donc être correctement préparé avant le processus de revêtement.
Comprendre ces points clés peut aider à sélectionner le processus et les paramètres de revêtement PVD appropriés pour des applications spécifiques, garantissant ainsi des performances et une longévité optimales des matériaux revêtus.
Tableau récapitulatif :
Aspect | Détails |
---|---|
Durée | 30 minutes à 2 heures, selon la taille de la pièce et l'épaisseur du revêtement. |
Épaisseur du revêtement | 0,25 microns à 5 microns, offrant dureté, résistance à la corrosion et bien plus encore. |
Types de processus | Revêtement par pulvérisation, évaporation thermique, évaporation par faisceau d'électrons, placage ionique. |
Étapes clés | Vaporisation, réaction, dépôt. |
Applications | Résistance à la corrosion, dureté améliorée et finitions esthétiques pour les métaux. |
Optimisez vos matériaux avec les revêtements PVD— contactez nos experts dès aujourd'hui pour des solutions sur mesure !