Les fours à induction, en particulier les Four à induction IGBT , sont largement utilisés dans les industries métallurgiques et manufacturières en raison de leur efficacité et de leur précision. Cependant, ils présentent plusieurs inconvénients qui peuvent avoir un impact sur leur adéquation à certaines applications. Ceux-ci incluent des limitations en matière de capacité de raffinage, des coûts d’exploitation plus élevés, une efficacité énergétique moindre dans certaines conceptions et des défis liés à la maintenance et aux changements d’alliage. Ci-dessous, nous explorons ces inconvénients en détail pour fournir une compréhension complète des inconvénients associés aux fours à induction.
Points clés expliqués :
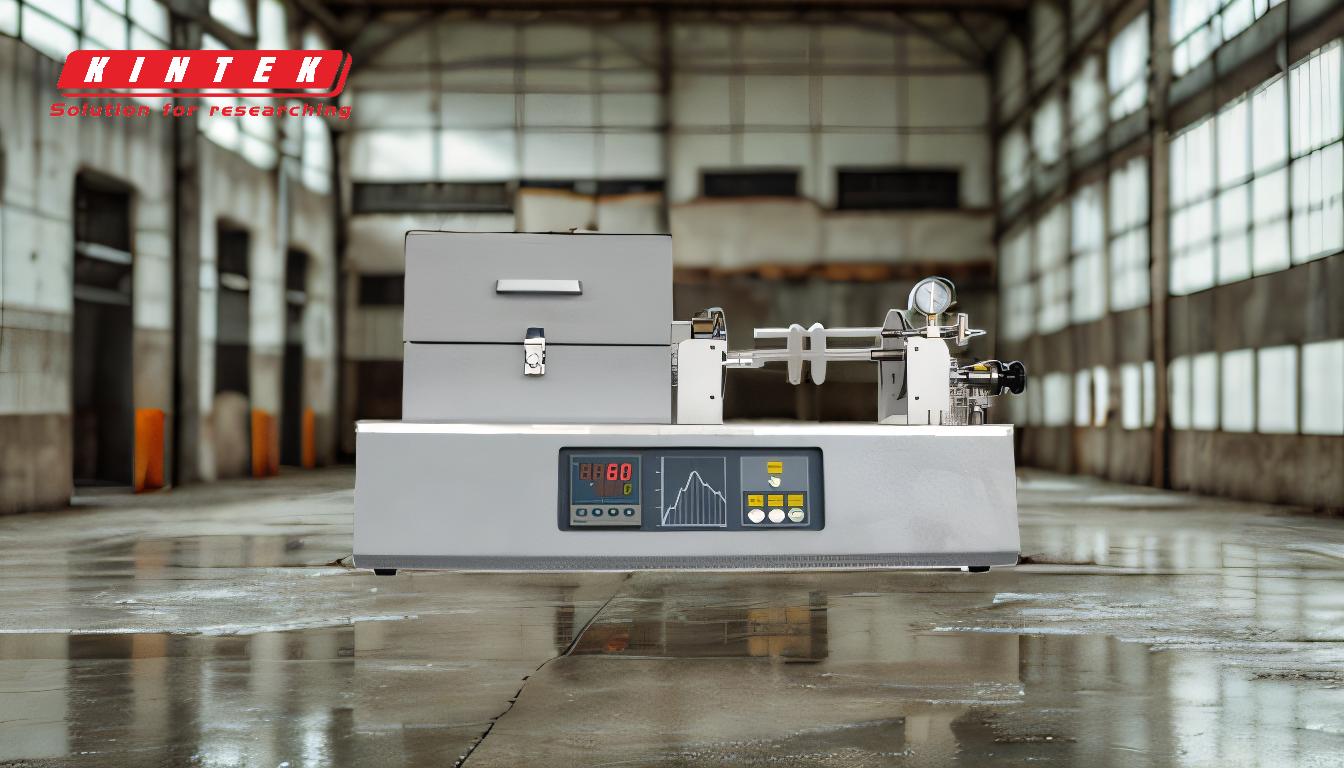
-
Manque de capacité de raffinage
- Les fours à induction, y compris les Four à induction IGBT , ne sont pas conçus pour les processus de raffinage.
- Les matériaux de charge doivent être exempts d'oxydes et avoir une composition connue pour éviter les problèmes lors de la fusion.
- Les éléments d'alliage peuvent être perdus en raison de l'oxydation, nécessitant une nouvelle addition, ce qui augmente les coûts des matériaux et la complexité opérationnelle.
-
Efficacité énergétique inférieure dans les fours à induction de type sans noyau
- Les fours à induction de type sans noyau, qui fonctionnent sur une large gamme de fréquences (50 Hz à 10 kHz), ont un rendement énergétique d'environ 75 %.
- C'est nettement inférieur à celui des fours à induction à noyau, qui peuvent atteindre un rendement énergétique allant jusqu'à 98 %.
- Les changements fréquents d’alliage dans les fours sans noyau peuvent également réduire la durée de vie du revêtement réfractaire, augmentant ainsi les coûts de maintenance.
-
Coûts d'exploitation élevés
- Les fours à induction dépendent de l’électricité, qui peut être plus chère que le gaz ou le mazout, ce qui entraîne des coûts d’exploitation plus élevés.
- Le coût de l’électricité peut varier considérablement selon l’emplacement, ce qui en fait une option moins économique dans les régions où les prix de l’énergie sont élevés.
-
Défis de maintenance et d’exploitation
- Les fours à induction à noyau nécessitent un entretien continu de la boucle métallique et sont rarement autorisés à refroidir, ce qui peut augmenter la complexité opérationnelle.
- Bien que les fournaises électriques soient généralement robustes, tout problème pouvant survenir peut nécessiter des réparations professionnelles, ce qui peut être coûteux et prendre du temps.
-
Limites des changements d'alliage
- Les fours à induction à noyau sont moins flexibles en ce qui concerne les changements d'alliage, car ils sont optimisés pour les opérations à haut débit avec peu de changements d'alliage.
- Les fours de type sans noyau, bien que plus flexibles, sont toujours confrontés à des problèmes d'usure du revêtement réfractaire en raison des changements fréquents d'alliage.
-
Contrôle de la température et perte de matière
- Bien que les fours à induction offrent un contrôle précis de la température, le manque de capacité de raffinage peut entraîner des pertes de matière, en particulier pour les éléments sujets à l'oxydation.
- Cela peut entraîner des coûts supplémentaires pour rajouter des éléments perdus et garantir que le produit final répond aux normes de qualité.
En résumé, bien que les fours à induction, y compris le Four à induction IGBT , offrent de nombreux avantages tels qu'un chauffage rapide, un rendement élevé et un contrôle précis de la température, mais ils présentent également des inconvénients importants. Ceux-ci incluent des limitations dans la capacité de raffinage, des coûts d’exploitation plus élevés, une efficacité énergétique moindre dans certaines conceptions et des défis liés à la maintenance et aux changements d’alliage. Comprendre ces inconvénients est crucial pour prendre des décisions éclairées lors de la sélection d’un four pour des applications industrielles spécifiques.
Tableau récapitulatif :
Inconvénient | Détails |
---|---|
Manque de capacité de raffinage | Non conçu pour le raffinage ; nécessite des matériaux pré-nettoyés. |
Efficacité énergétique inférieure | Les fours de type sans noyau ont une efficacité d'environ 75 % contre 98 % dans les conceptions à noyau. |
Coûts d'exploitation élevés | La dépendance à l’électricité entraîne des coûts plus élevés, en particulier dans les zones à forte énergie. |
Défis de maintenance | Nécessite un entretien continu ; les réparations peuvent être coûteuses et prendre du temps. |
Limites des changements d'alliage | Les fours à noyau sont moins flexibles ; usure réfractaire dans les conceptions sans noyau. |
Perte matérielle | Les éléments sujets à l'oxydation peuvent être perdus, augmentant ainsi les coûts des matériaux. |
Besoin d’aide pour choisir la fournaise adaptée à vos besoins ? Contactez nos experts dès aujourd'hui !