La calcination est un processus de traitement thermique utilisé pour provoquer une décomposition thermique, une transition de phase ou l'élimination d'une fraction volatile dans les matériaux.L'équipement utilisé pour la calcination, connu sous le nom de calcinateur, se présente sous différentes configurations, chacune étant conçue pour répondre à des besoins industriels spécifiques.Les principaux types de calcinateurs sont les fours à moufle, les fours à réverbère et les fours à cuve.Ces types diffèrent en termes de conception, de fonctionnement et d'application, ce qui les rend adaptés à différents matériaux et processus.Ci-dessous, nous explorons ces types en détail, en nous concentrant sur leurs caractéristiques uniques, leurs avantages et leurs applications typiques.
Explication des points clés :
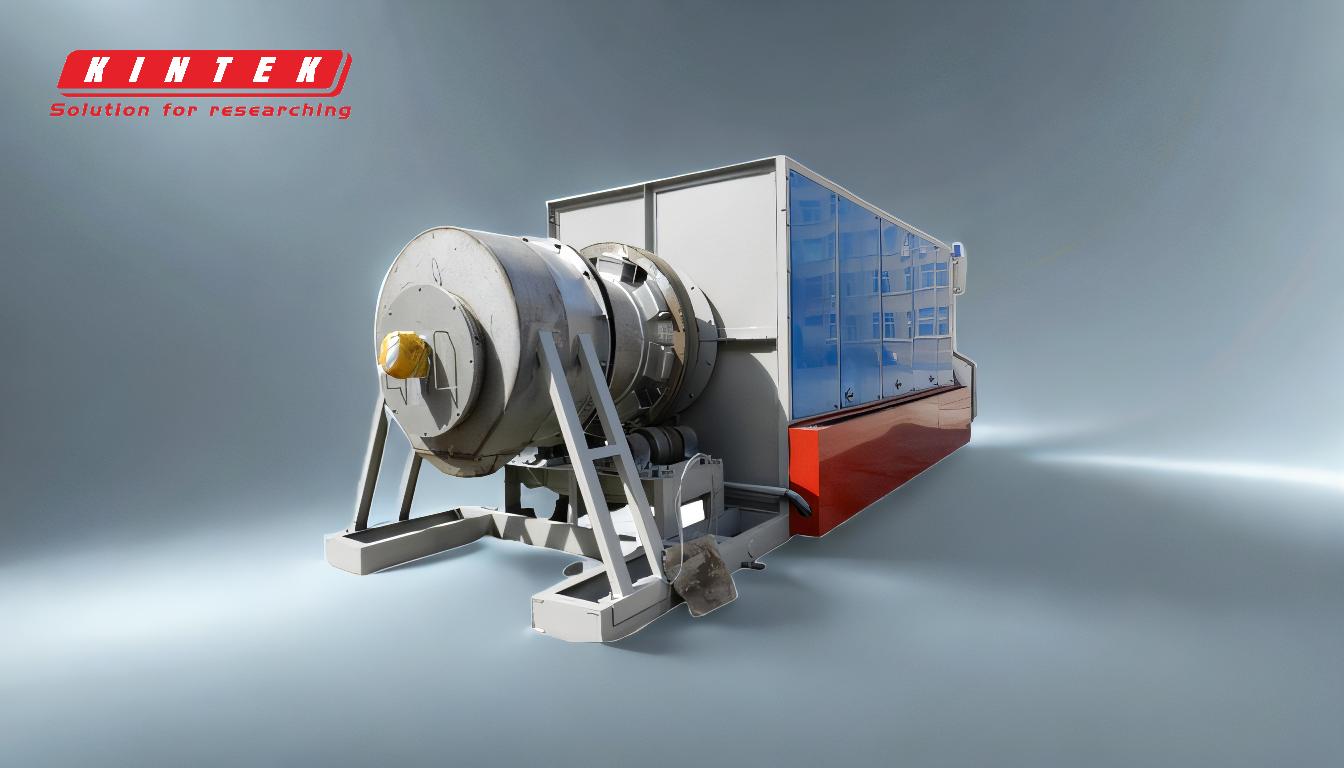
-
Fours à moufle
- Conception et fonctionnement:Les fours à moufle sont conçus avec une chambre séparée (le moufle) qui isole le matériau traité des gaz de combustion.Le matériau est ainsi chauffé indirectement, ce qui permet de maintenir un environnement propre et contrôlé.
-
Les avantages:
- Contrôle précis de la température.
- Protection des matériaux contre la contamination par les gaz de combustion.
- Convient aux applications à petite échelle ou en laboratoire.
-
Applications:
- Calcination de matériaux sensibles comme les céramiques, le verre et certains métaux.
- Recherche et développement en laboratoire.
-
Fours à réverbère
- Conception et fonctionnement:Les fours à réverbère se caractérisent par une grande chambre ouverte où la chaleur est réfléchie (réverbérée) par le toit et les murs sur le matériau.Le matériau est chauffé directement par les flammes et indirectement par la chaleur réfléchie.
-
Avantages:
- Débit élevé pour les processus industriels à grande échelle.
- Capacité à traiter des matériaux en vrac.
- Chauffage uniforme grâce à la réverbération de la chaleur.
-
Applications:
- Calcination de minerais, tels que la bauxite pour la production d'alumine.
- Traitement du clinker et d'autres minéraux industriels.
-
Fours à cuve
- Conception et fonctionnement:Les fours à cuve sont des structures verticales dans lesquelles le matériau est alimenté par le haut et se déplace vers le bas à travers une zone chauffée.La chaleur est généralement générée par la combustion d'un combustible à la base, et le matériau est calciné au fur et à mesure de sa descente.
-
Avantages:
- Utilisation efficace de la chaleur grâce au flux à contre-courant des matériaux et des gaz.
- Fonctionnement continu, ce qui le rend adapté à la production à grande échelle.
- Conception compacte par rapport aux fours horizontaux.
-
Applications:
- Calcination du calcaire pour produire de la chaux.
- Traitement des boulettes de minerai de fer et autres applications métallurgiques.
-
Comparaison des types de calcinateurs
- Échelle de fonctionnement:Les fours à moufle sont idéaux pour les applications à petite échelle ou précises, tandis que les fours à réverbère et les fours à cuve sont mieux adaptés aux processus industriels à grande échelle.
- Compatibilité des matériaux:Les fours à moufle sont préférés pour les matériaux sensibles, tandis que les fours à réverbère et les fours à cuve sont utilisés pour les matériaux en vrac tels que les minerais et les minéraux.
- Efficacité énergétique:Les fours à cuve sont généralement plus efficaces sur le plan énergétique en raison de leur conception, tandis que les fours à moufle nécessitent plus d'énergie pour le chauffage indirect.
-
Critères de sélection des calcinateurs
- Propriétés des matériaux:Le type de matériau traité (par exemple, sensibilité à la contamination, taille des particules) influence le choix du calcinateur.
- Échelle de production:Le débit requis détermine si un petit four à moufle ou un grand four à réverbère ou à cuve est nécessaire.
- Exigences en matière de température:Les différents calcinateurs ont des capacités de température variables, qui doivent s'aligner sur la température de calcination du matériau.
- Efficacité énergétique:Pour des opérations rentables, l'efficacité énergétique est un facteur essentiel, en particulier dans les installations industrielles à grande échelle.
En résumé, le choix du four de calcination dépend des exigences spécifiques du matériau et du procédé.Les fours à moufle sont idéaux pour les applications précises à petite échelle, les fours à réverbère excellent dans les processus industriels à grande échelle, et les fours à cuve offrent un fonctionnement continu économe en énergie pour les matériaux en vrac.Il est essentiel de comprendre ces différences pour sélectionner l'équipement adapté aux besoins de la calcination.
Tableau récapitulatif :
Type de four à calciner | Conception et fonctionnement | Avantages de l'application | Applications |
---|---|---|---|
Four à moufle | La chambre séparée isole le matériau des gaz de combustion ; chauffage indirect. | Contrôle précis de la température, absence de contamination, idéal pour une utilisation à petite échelle. | Calcination des céramiques, du verre, des métaux ; R&D en laboratoire. |
Four à réverbère | Chambre ouverte dont la chaleur est réfléchie par les parois ; chauffage direct et indirect. | Débit élevé, traitement des matériaux en vrac, chauffage uniforme. | Calcination de minerais (p. ex. bauxite), de clinker, de minéraux industriels. |
Four à cuve/fourneau | Structure verticale ; le matériau descend à travers la zone chauffée ; flux de chaleur à contre-courant. | Efficacité énergétique, fonctionnement continu, conception compacte. | Calcination du calcaire, boulettes de minerai de fer, applications métallurgiques. |
Vous avez besoin d'aide pour choisir le bon four de calcination pour votre procédé ? Contactez nos experts dès aujourd'hui !