Les fours à induction, bien qu'ils soient très efficaces pour la fusion des métaux, présentent plusieurs limites qui peuvent avoir une incidence sur leur utilisation dans certaines applications industrielles.Le principal inconvénient est leur incapacité à affiner les matériaux, ce qui signifie que les matériaux de charge doivent déjà être exempts d'oxydes et avoir une composition connue.En outre, certains éléments d'alliage peuvent être perdus en raison de l'oxydation, ce qui nécessite de les ajouter à nouveau à la matière fondue.Ces facteurs peuvent accroître la complexité et les coûts des opérations, en particulier dans les procédés exigeant des compositions d'alliage précises.
Explication des points clés :
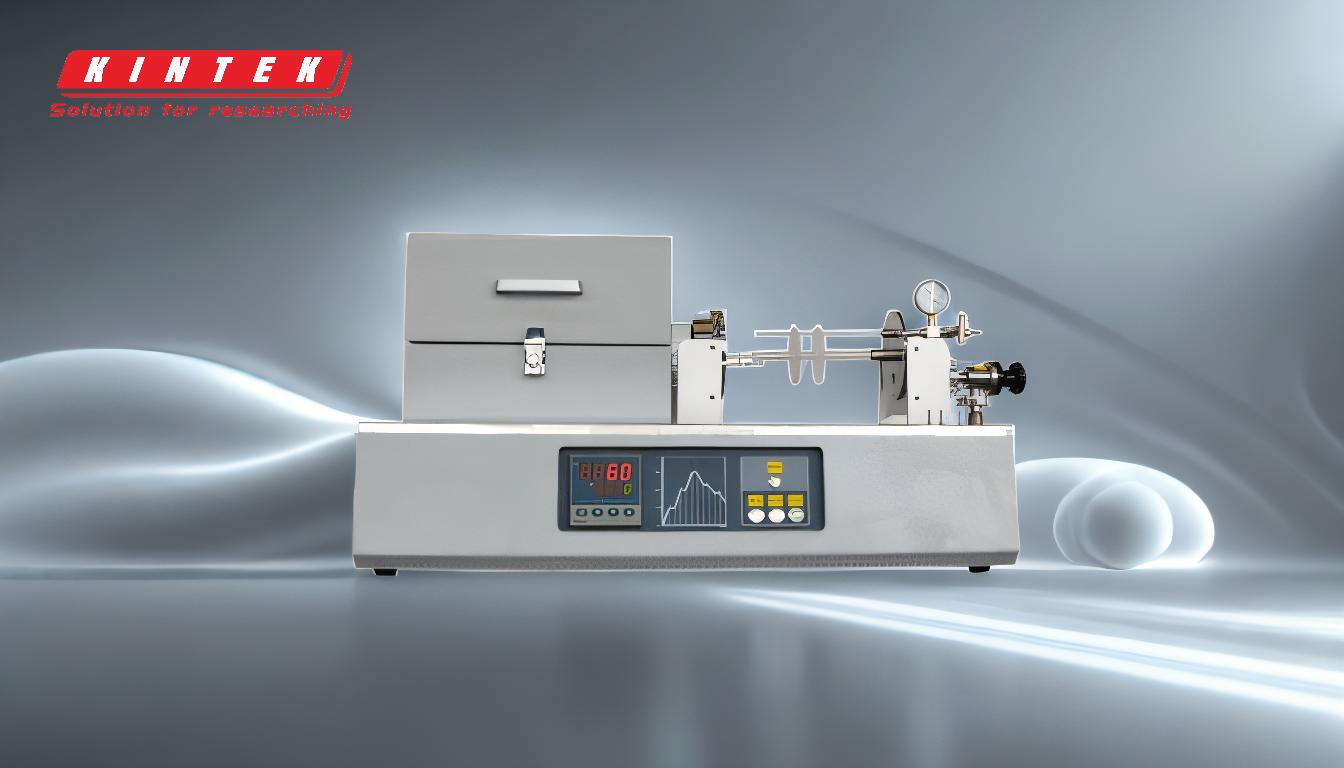
-
Manque de capacité de raffinage:
- Les fours à induction ne peuvent pas affiner le métal pendant le processus de fusion.Cela signifie que les matières premières utilisées doivent déjà être d'une grande pureté et exemptes d'oxydes.Toute impureté présente dans les matériaux de charge restera dans le produit final, ce qui peut constituer une limitation importante pour les applications nécessitant des métaux de haute pureté.
-
Exigence d'une composition connue:
- La composition des matériaux de charge doit être connue avec précision avant la fusion.En effet, le four à induction n'a pas la capacité d'ajuster la composition pendant le processus de fusion.Tout écart dans la composition peut entraîner des incohérences dans le produit final, ce qui peut être problématique pour les industries qui exigent un respect strict des spécifications des matériaux.
-
Perte d'éléments d'alliage:
- Au cours du processus de fusion, certains éléments d'alliage peuvent être perdus en raison de l'oxydation.C'est particulièrement vrai pour les éléments les plus réactifs et les plus enclins à l'oxydation.La perte de ces éléments peut altérer les propriétés souhaitées de l'alliage, ce qui nécessite de les ajouter à nouveau à la masse fondue.Cela accroît non seulement la complexité du processus, mais aussi le coût global.
-
Complexité et coûts opérationnels:
- Le besoin de matériaux de charge de haute pureté et la perte potentielle d'éléments d'alliage peuvent entraîner une complexité opérationnelle et des coûts accrus.Les industries peuvent être amenées à investir dans des processus ou des matériaux supplémentaires pour garantir la qualité et la cohérence du produit final.Cela peut rendre les fours à induction moins intéressants pour certaines applications où le coût et la simplicité sont des facteurs critiques.
-
Efficacité énergétique et considérations environnementales:
- Bien que les fours à induction soient généralement économes en énergie, la nécessité d'utiliser des matériaux de haute pureté et le risque de perte de matériaux peuvent compenser certains de ces avantages.En outre, la réaddition d'éléments d'alliage perdus peut avoir des répercussions sur l'environnement, en particulier si ces éléments sont dangereux ou difficiles à obtenir.
-
Comparaison avec d'autres types de fours:
- Par rapport à d'autres types de fours, tels que les fours à induction four à induction igbt Avec le temps, les limites des fours à induction deviennent plus évidentes.Par exemple, les fours à induction IGBT offrent un meilleur contrôle du processus de fusion et peuvent traiter une plus large gamme de matériaux, ce qui les rend plus polyvalents dans certaines applications industrielles.
En résumé, si les fours à induction offrent plusieurs avantages, tels que l'efficacité énergétique et le contrôle précis de la température, leurs limites en termes de capacité d'affinage, d'exigences en matière de composition des matériaux et de perte potentielle d'éléments d'alliage peuvent poser des problèmes importants.Ces facteurs doivent être soigneusement pris en compte lors de la sélection d'un type de four pour des applications industrielles spécifiques.
Tableau récapitulatif :
Limitation | Description |
---|---|
Manque de capacité d'affinage | Ne peut pas raffiner les métaux ; nécessite des matériaux de charge très purs et exempts d'oxyde. |
Exigence de composition connue | La composition du matériau de charge doit être connue avec précision avant la fusion. |
Perte d'éléments d'alliage | Les éléments réactifs peuvent s'oxyder et nécessiter un nouvel ajout, ce qui augmente les coûts. |
Complexité opérationnelle et coûts | Les matériaux de haute pureté et les processus de réaddition augmentent la complexité opérationnelle. |
Impact sur l'énergie et l'environnement | La perte et la réaddition de matériaux peuvent nuire à l'efficacité énergétique et augmenter les coûts. |
Vous avez besoin d'aide pour choisir le bon four pour vos besoins industriels ? Contactez nos experts dès aujourd'hui !