Le dépôt en phase vapeur (DPV) englobe deux techniques principales :le dépôt chimique en phase vapeur (CVD) et le dépôt physique en phase vapeur (PVD).Les deux procédés impliquent le dépôt de films minces sur des substrats, mais diffèrent dans leurs mécanismes et leurs applications.Le dépôt en phase vapeur repose sur des réactions chimiques pour former les revêtements, tandis que le dépôt en phase vapeur utilise des processus physiques tels que l'évaporation ou la pulvérisation.Cette explication décompose les processus de dépôt en phase vapeur et de dépôt en phase vapeur, en mettant en évidence leurs principales étapes, méthodes et applications.
Explication des points clés :
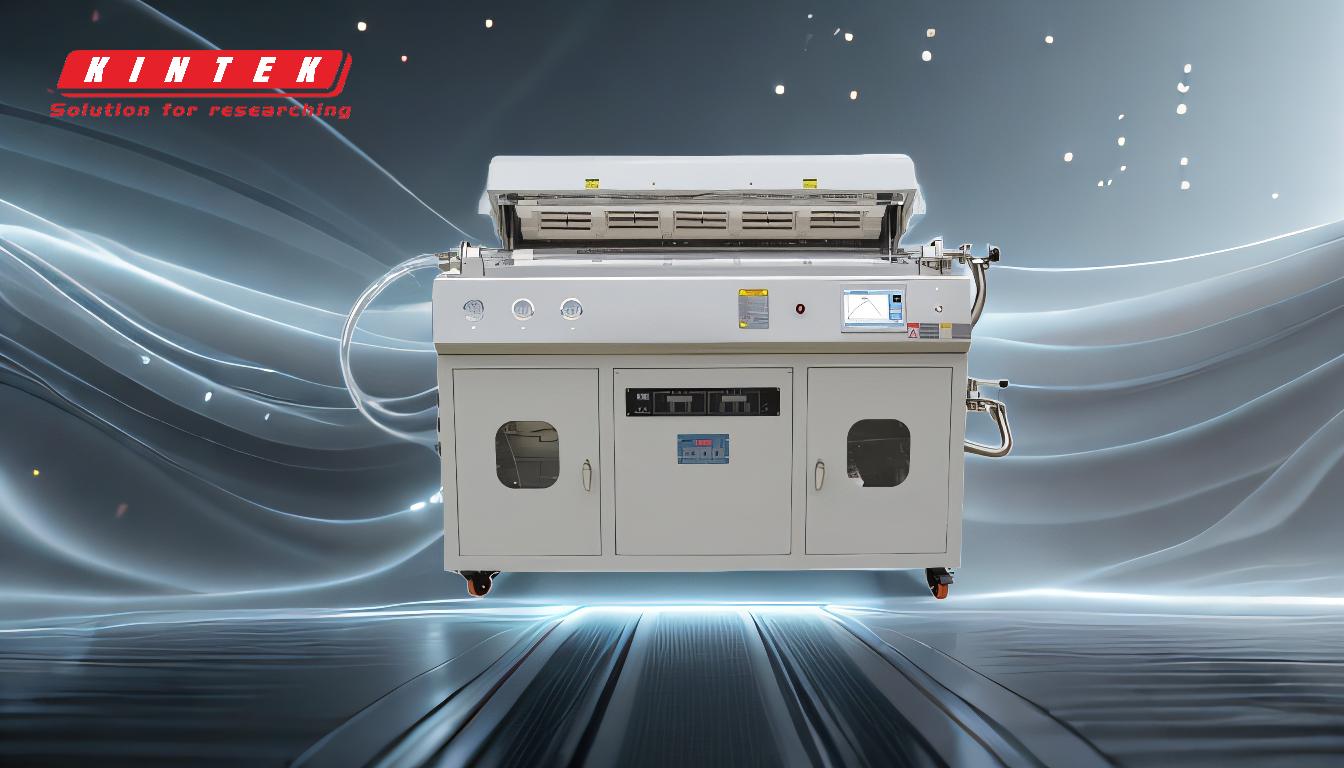
-
Processus de dépôt chimique en phase vapeur (CVD)
- Transport des espèces gazeuses en réaction:Dans le procédé CVD, les gaz précurseurs sont introduits dans une chambre de réaction et transportés jusqu'à la surface du substrat.Cette étape permet de s'assurer que les espèces réactives atteignent la surface de manière uniforme.
- Adsorption à la surface:Les espèces gazeuses s'adsorbent sur la surface du substrat, formant une fine couche de molécules réactives.
- Réactions catalysées par la surface:Des réactions chimiques se produisent à la surface du substrat, souvent catalysées par la chaleur ou le plasma, conduisant à la formation du film mince souhaité.
- Diffusion et croissance en surface:Les espèces réactives diffusent à travers la surface jusqu'aux sites de croissance, où se produisent la nucléation et la croissance du film.
- Désorption et élimination des sous-produits:Les produits de réaction gazeux se désorbent de la surface et sont évacués de la chambre de réaction, ce qui garantit un processus de dépôt propre.
- Les applications:Le dépôt en phase vapeur (CVD) est largement utilisé dans la fabrication de semi-conducteurs, les revêtements pour la résistance à l'usure et la création de films de haute pureté.
- L'équipement:A machine de dépôt chimique en phase vapeur est essentielle pour ce processus, car elle fournit des environnements contrôlés pour un dépôt de film précis.
-
Processus de dépôt physique en phase vapeur (PVD)
- Evaporation:Dans le procédé PVD, le matériau à déposer est vaporisé à l'aide de sources à haute énergie telles que des faisceaux d'électrons ou du plasma.Cette étape permet de déloger les atomes du matériau cible et de créer une vapeur.
- Transport:Les atomes vaporisés sont transportés dans un environnement sous vide ou à basse pression jusqu'au substrat.
- Réaction:Dans le cas du dépôt en phase vapeur réactif, les atomes vaporisés réagissent avec les gaz introduits (par exemple, l'oxygène ou l'azote) pour former des composés tels que des oxydes, des nitrures ou des carbures.
- Dépôt:Les atomes ou les composés se condensent à la surface du substrat, formant un film mince et uniforme.
- Méthodes:Les méthodes courantes de dépôt en phase vapeur comprennent le dépôt thermique en phase vapeur, l'épitaxie par faisceaux moléculaires et le dépôt par pulvérisation d'un faisceau d'ions.Ces techniques produisent des films très purs et très adhérents.
- Les applications:Le procédé PVD est utilisé pour les revêtements décoratifs, les films optiques et les revêtements résistants à l'usure dans des industries telles que l'aérospatiale et l'automobile.
-
Comparaison des procédés CVD et PVD
- Mécanisme:Le dépôt en phase vapeur (CVD) repose sur des réactions chimiques, tandis que le dépôt en phase vapeur (PVD) fait appel à des procédés physiques tels que l'évaporation ou la pulvérisation.
- Exigences en matière de température:Le dépôt en phase vapeur (CVD) nécessite généralement des températures plus élevées que le dépôt en phase vapeur (PVD).
- Qualité du film:Le procédé CVD produit des films d'une excellente conformité et d'une excellente couverture des étapes, tandis que les films PVD sont très purs et denses.
- Complexité de l'équipement:Les systèmes CVD sont souvent plus complexes en raison de la nécessité d'une alimentation précise en gaz et d'un contrôle de la réaction, tandis que les systèmes PVD sont plus simples mais nécessitent des conditions de vide élevé.
-
Choisir la bonne méthode
- Pour les films de haute pureté:Le procédé PVD est préféré en raison de sa capacité à produire des revêtements extrêmement purs et uniformes.
- Pour les géométries complexes:Le dépôt en phase vapeur est idéal pour revêtir des formes complexes et obtenir une épaisseur uniforme.
- Pour les applications à haute température:Le dépôt en phase vapeur (CVD) convient aux processus à haute température, tandis que le dépôt en phase vapeur (PVD) est plus adapté aux applications à basse température.
En comprenant les processus de dépôt en phase vapeur, y compris les rôles des machines de dépôt chimique en phase vapeur Grâce aux machines de dépôt chimique en phase vapeur, les fabricants peuvent choisir la méthode appropriée à leurs besoins spécifiques, garantissant ainsi des couches minces de haute qualité pour diverses applications.
Tableau récapitulatif :
Aspect | CVD | PVD |
---|---|---|
Mécanisme | Réactions chimiques | Processus physiques (évaporation, pulvérisation) |
la température | Températures élevées | Températures basses |
Qualité du film | Excellente conformité et couverture des étapes | Films très purs et denses |
Complexité de l'équipement | Complexe (apport précis de gaz, contrôle de la réaction) | Plus simple (nécessite des conditions de vide poussé) |
Applications | Semi-conducteurs, revêtements résistants à l'usure, films de haute pureté | Revêtements décoratifs, films optiques, revêtements résistants à l'usure |
Vous avez besoin d'aide pour choisir la bonne méthode de dépôt en phase vapeur ? Contactez nos experts dès aujourd'hui pour un accompagnement personnalisé !