Le dépôt physique en phase vapeur (PVD) est un procédé de revêtement sous vide utilisé pour produire des films et des revêtements minces. Cela implique le transfert physique d'un matériau d'une source à un substrat, généralement par vaporisation, transport et condensation. Le procédé est largement utilisé dans des industries telles que l’électronique, l’optique et la fabrication d’outils en raison de sa capacité à produire des revêtements durables et de haute qualité. Ci-dessous, nous détaillons les étapes du PVD, en nous concentrant sur les étapes clés et leur importance.
Points clés expliqués :
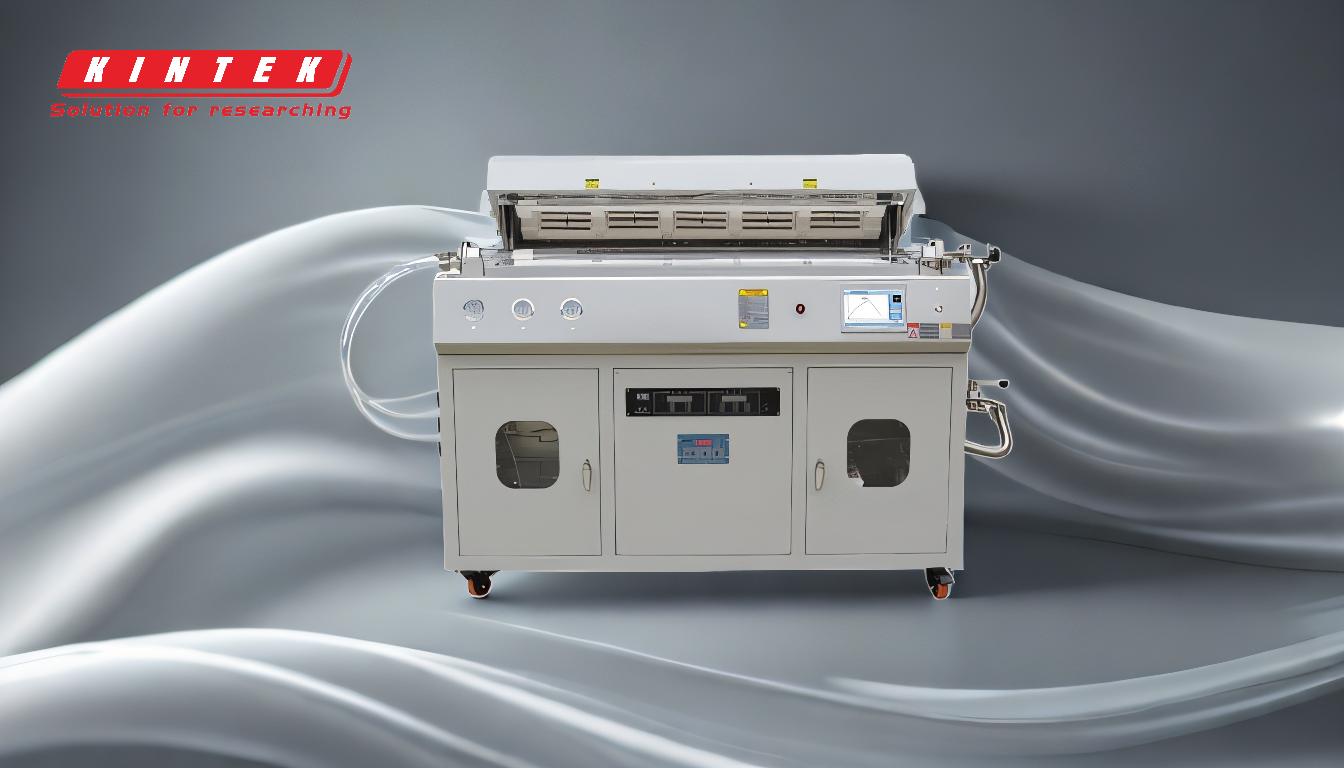
-
Vaporisation du matériau
- La première étape du PVD consiste à transformer le matériau à déposer en vapeur. Ceci est généralement réalisé grâce à des méthodes telles que la pulvérisation cathodique, l'évaporation ou la vaporisation à l'arc.
- Lors de la pulvérisation cathodique, des ions à haute énergie bombardent le matériau cible, délogeant les atomes et créant une vapeur. Lors de l'évaporation, le matériau est chauffé jusqu'à ce qu'il se vaporise.
- Cette étape est cruciale car elle détermine la composition et la qualité de la vapeur, ce qui impacte directement le revêtement final.
-
Transport de vapeur
- Le matériau vaporisé est transporté de la source au substrat dans un environnement sous vide ou basse pression.
- Le vide garantit une interférence minimale avec les autres gaz, permettant à la vapeur de circuler sans entrave et de maintenir sa pureté.
- Cette étape est essentielle pour réaliser un dépôt uniforme et contrôler l’épaisseur du revêtement.
-
Réaction avec des gaz réactifs (facultatif)
- Dans certains procédés PVD, un gaz réactif (par exemple de l'azote ou de l'oxygène) est introduit dans la chambre.
- Le gaz réactif interagit avec le matériau vaporisé pour former un composé, tel qu'un nitrure ou un oxyde, qui est ensuite déposé sur le substrat.
- Cette étape est particulièrement importante pour créer des revêtements durs et résistants à l'usure comme le nitrure de titane (TiN).
-
Condensation et formation de film
- La vapeur ou le composé se condense sur le substrat, formant un film mince et adhérent.
- Le substrat est souvent prétraité (par exemple nettoyé ou chauffé) pour améliorer l'adhérence et la qualité du film.
- Cette étape détermine les propriétés finales du revêtement, telles que sa dureté, sa durabilité et ses caractéristiques optiques.
-
Traitements post-dépôt (facultatif)
- Après dépôt, le substrat revêtu peut subir des traitements supplémentaires, tels qu'un recuit ou un polissage, pour améliorer les propriétés du film.
- Ces traitements peuvent améliorer l'adhérence, réduire les contraintes ou modifier la finition de la surface, selon l'application.
En suivant ces étapes, le PVD permet la création de revêtements hautes performances avec un contrôle précis de l'épaisseur, de la composition et des propriétés. Le processus est polyvalent et peut être adapté pour répondre aux exigences d’applications spécifiques, ce qui en fait la pierre angulaire de l’ingénierie de surface moderne.
Tableau récapitulatif :
Étape | Description | Importance |
---|---|---|
1. Vaporisation du matériau | Convertit le matériau en vapeur par pulvérisation, évaporation ou vaporisation à l'arc. | Détermine la composition et la qualité de la vapeur, ayant un impact sur le revêtement final. |
2. Transport de vapeur | La vapeur se déplace vers le substrat dans un environnement sous vide ou à basse pression. | Assure un dépôt uniforme et un contrôle précis de l’épaisseur du revêtement. |
3. réaction avec des gaz réactifs (facultatif) | Les gaz réactifs (par exemple l'azote) interagissent avec la vapeur pour former des composés. | Crée des revêtements durs et résistants à l'usure comme le nitrure de titane (TiN). |
4. Condensation et formation de film | La vapeur se condense sur le substrat, formant un film fin et adhérent. | Détermine les propriétés du revêtement telles que la dureté, la durabilité et les caractéristiques optiques. |
5. Traitements post-dépôt (facultatif) | Des traitements supplémentaires (par exemple, recuit) améliorent les propriétés du film. | Améliore l'adhérence, réduit les contraintes ou modifie la finition de surface pour les applications. |
Découvrez comment le PVD peut améliorer votre processus de revêtement : contactez nos experts dès aujourd'hui pour des solutions sur mesure !